Electroactive Polymer Actuators: Principles and Future
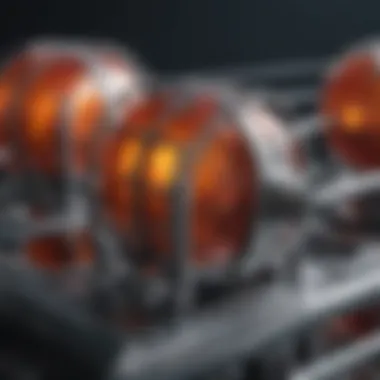
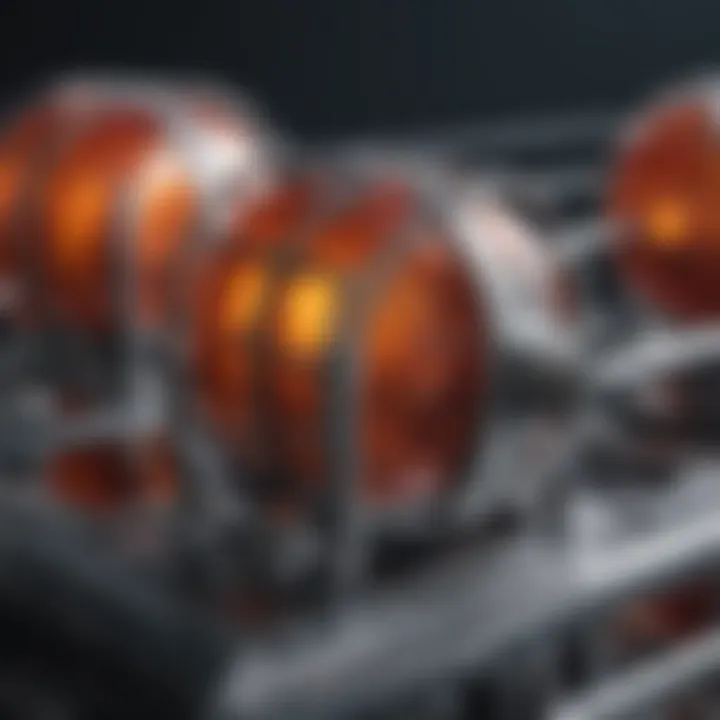
Intro
Electroactive polymers (EAPs) are specialized materials that change their shape or size when subjected to an electric field. These unique properties make them valuable in a variety of applications, particularly in fields such as robotics, biotechnology, and electronics. The significant advancement of EAPs has been fueled by research into their operational principles and material compositions. These materials can mimic natural muscle movements, making them ideal for integrating into devices that require actuation.
As the demand for versatile actuators rises, EAPs emerge as a favorable solution, offering flexibility, lightweight characteristics, and a capacity for large deformations. Their soft nature allows them to operate safely in contact with biological systems, leading to numerous innovations in medical devices. Understanding the principles and capabilities of EAPs helps researchers and engineers to think beyond traditional approaches to actuation, encouraging creative applications across various industries.
In this article, we will explore the key findings related to electroactive polymer actuators, evaluate their implications, and discuss future developments that may arise from ongoing research and technological improvements.
Foreword to Electroactive Polymers
Electroactive polymers (EAPs) are a class of materials that can change shape or size when stimulated by an electric field. Their unique characteristics make them highly relevant in today's technological landscape. The significance of studying electroactive polymers lies in their versatile applications across diverse fields such as robotics, biotechnology, and electronics.
EAPs are of great interest because they enable the development of smart actuators and sensors. These devices possess the ability to mimic natural movements, which allows for more effective and efficient operations in various applications. For instance, in soft robotics, EAPs can be utilized to create flexible actuators that enable complex movements without the rigidity of traditional materials.
Moreover, understanding EAPs helps researchers to unlock their potential for innovation. Continuous advancements in material science lead to improved performance characteristics, expanding the possible applications. Addressing the challenges associated with EAPs can enhance their performance and durability, making them more viable for industrial use.
In summary, the exploration of electroactive polymers is crucial for both academic research and practical applications. As we delve deeper into their definitions and historical context, we will uncover how EAPs evolved and their role in shaping modern technology.
Defining Electroactive Polymers
Electroactive polymers are materials that exhibit a mechanical response to an applied electric field. This response can manifest in several ways, such as elongation, contraction, or bending. Their general behavior under electrical stimulation distinguishes them from traditional polymers. EAPs typically fall into two main categories: intrinsic and extrinsic polymers.
- Intrinsic EAPs: These materials generate an electric field due to their innate characteristics, often seen in conductive polymers. They fully exploit electrode interactions.
- Extrinsic EAPs: This category involves composites that exhibit electroactive behavior due to interactions between various components, including ionic polymer-metal composites and dielectric elastomers.
The defining trait of these polymers is their ability to convert electrical energy into mechanical work, making them suitable for developing advanced actuators and sensors. Their versatility allows for application in a range of environments, enabling innovations in multiple domains.
Historical Context and Development
The history of electroactive polymers dates back several decades, with significant advancements shaping their current state. The initial research began in the 1960s, focusing on conductive polymers. However, real momentum was gained in the 1990s when researchers started exploring the actuation capabilities of these materials.
Some key milestones in the development of EAPs include:
- 1960s: Discovery of polyaniline and polypyrrole, which paved the way for conductive polymers.
- 1990s: The introduction of ionic polymer-metal composites, which demonstrated impressive actuation capabilities.
- 2000s: Research expanded into dielectric elastomers, highlighting their potential for practical applications in soft robotics and wearable devices.
The evolution of electroactive polymers reflects the increasing interest in adaptable materials. Their growth is closely linked to the advancement of nanotechnology and material sciences, leading to innovative applications in various sectors. As we move forward, these historical insights provide a backdrop for understanding the contemporary relevance of EAPs.
Mechanisms of Action
Understanding the mechanisms of action of electroactive polymers is vital for their application across different fields. These mechanisms dictate how these materials respond to electrical stimuli and how they can be utilized in practical applications. Electroactive polymers operate through electromechanical coupling, enabling conversion between electrical energy and mechanical motion. This section explores the nuances of electromechanical coupling and the various types of electroactive polymers, each with unique properties and functions.
Electromechanical Coupling
Electromechanical coupling is the underlying principle for the operation of electroactive polymers. It involves the interaction between electrical fields and mechanical properties, enabling these materials to deform when subjected to electrical stimuli. Such deformation can be tiny or significant, depending on the material's properties and the intensity of the applied electric field.
This coupling effect is crucial as it provides the responsive behavior that is essential for various applications. For instance, in soft robotics, actuators made from electroactive polymers can mimic biological movement, making machines more adaptable to different environments. The effectiveness of this coupling can be influenced by multiple factors such as the polymerโs thickness, the applied voltage, or the frequency of the electrical signal.
Types of Electroactive Polymers
Electroactive polymers can be categorized into several types based on their composition and functional mechanisms. Each type has distinct characteristics, influencing their performance in applications.
Conductive Polymers
Conductive polymers have gained attention for their ability to conduct electricity while maintaining flexibility. They can be synthesized to exhibit different levels of conductivity, granting designers control over the material properties. A significant advantage of conductive polymers lies in their lightweight nature, which makes them particularly useful for applications where weight is a critical factor, such as in portable devices.
The unique feature that sets conductive polymers apart is their inherent conductivity due to the delocalization of pi electrons across their backbone structure. This property allows them to function effectively in sensors and actuators. However, a potential disadvantage is their degradation in air and moisture, leading to reduced performance in long-term applications.
Ionic Polymer-Metal Composites
Ionic polymer-metal composites (IPMCs) are another category of electroactive polymers. These materials consist of an ionic polymer membrane covered by thin layers of metal on either side. When an electric field is applied, ions in the polymer move toward the metal interface, causing bending and deformation.
The key feature of IPMCs is their ability to produce precise motion with minimal power. This characteristic makes them attractive for applications in micro-robots and flexible actuators. However, their reliance on ionic conductivity can be a limitation, as their performance can be sensitive to environmental conditions, including temperature and humidity.
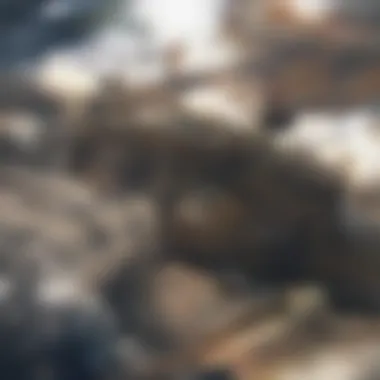
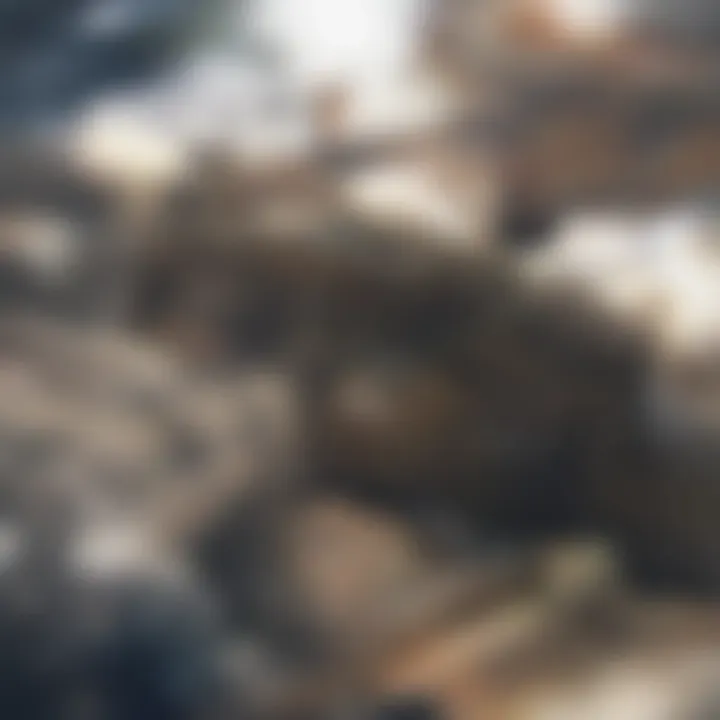
Dielectric Elastomers
Dielectric elastomers are characterized by their large actuation strains. These materials operate by distorting under an electric field, enabling them to expand or contract significantly. This high strain ability marks them as a promising choice for applications requiring considerable motion, such as soft robotics and mimicry of human muscles.
A major benefit of dielectric elastomers is their ability to generate substantial force while maintaining lightweight characteristics. Their unique feature of experiencing very high actuation strains without requiring complex mechanisms sets them apart from other types of electroactive polymers. However, they can suffer from issues related to breakdown voltage and loss of performance over time, making durability a concern in design.
"Understanding the mechanisms of action is crucial for optimizing the design and application of electroactive polymer actuators."
In summary, the mechanisms of action, particularly electromechanical coupling, are central to the functionality of electroactive polymers. By categorizing these polymers into conductive types, ionic polymer-metal composites, and dielectric elastomers, we gain insights into the advantages and limitations of each. This knowledge is essential for advancing research and applications.
Material Properties and Selection
The selection of materials used in electroactive polymer actuators is a crucial factor influencing their functionality and application. Material properties dictate not only the performance characteristics of these actuators but also their suitability for specific applications in robotics, biotechnology, and electronics. Understanding the balance between different material properties allows engineers and researchers to innovate and improve the efficiency of electroactive polymer actuators.
Physical Attributes
Flexibility and Stretchability
Flexibility and stretchability are paramount for electroactive polymers. These attributes allow the materials to easily deform and recover their shape. The key characteristic of flexibility is that it enables adaptive movements in actuators which is essential for robotic applications. When a polymer is both flexible and stretchable, it can undergo significant deformations without rupturing. This makes it a popular choice in applications like soft robotics where gentle movements are required.
A unique feature of flexible actuators is their capacity to mimic natural movements, such as those of muscle. This attribute benefits designs that require precise motion control. However, flexibility can come with a trade-off in terms of structural support. While a polymer may be highly flexible, it may not provide sufficient rigidity in specific applications that demand firm support.
Thermal Stability
Thermal stability is another critical material property. It refers to a material's ability to retain performance characteristics when subjected to varying temperatures. This property is significant in ensuring that electroactive polymers perform consistently over a range of operating conditions. A highly thermally stable polymer can be relied upon to deliver effective actuation without performance degradation, which is especially crucial in applications that involve fluctuating environmental conditions or operational extremes.
The key characteristic of thermal stability is its impact on longevity. A material that can resist thermal degradation will generally have an extended operational life. Unique features of thermally stable materials include the ability to withstand high-temperature cycles without losing their mechanical integrity. However, while enhanced thermal stability means increased operational reliability, it can sometimes lead to complexities in the manufacturing process, requiring sophisticated techniques for material processing.
Electrical Conductivity and Performance
Electrical conductivity is vital for the performance of electroactive polymer actuators. These materials must effectively convert electrical energy into mechanical energy. The diversity in the types of electroactive polymers means that their electrical conductivity can vary significantly. High conductivity leads to improved response times and efficient power usage, allowing for rapid actuation.
In applications where speed and precision are critical, such as in robotic grippers or medical devices, enhancing conductivity ensures these polymrs perform optimally. On the other hand, materials with lower electrical conductivity may require additional modifications or hybrid techniques that could complicate designs and increase costs.
Significant attention must also be paid to the balance between conductivity and other properties such as mechanical strength and thermal stability. Optimizing these properties is essential for creating effective and durable electroactive polymer actuators suited for diverse applications.
Fabrication Techniques
Understanding the fabrication techniques of electroactive polymers is crucial for advancing their application across multiple fields. The methods of production significantly impact the material properties and performance of these actuators. Achieving the desired flexibility, conductivity, and actuation response requires meticulous attention to both the techniques employed and the materials selected. Such considerations also influence the scalability of manufacturing, which is vital for commercial viability.
The fabrication process serves not only to optimize performance but also to address specific application requirements. As these techniques evolve, they allow for novel designs and functionalities, leveraging the unique properties of electroactive polymers. This discussion will encompass common manufacturing processes and the challenges faced during production.
Common Manufacturing Processes
Fabrication of electroactive polymers entails different manufacturing processes, each tailored to specific polymer types and application requirements. Common techniques include:
- Casting and Coating: This method involves spreading a polymer solution onto a substrate, allowing for the creation of thin films that can be subsequently processed to yield actuator properties. It is suitable for various polymer types, particularly conductive and dielectric materials.
- 3D Printing: Additive manufacturing plays a substantial role in creating complex geometries and structures not achievable through traditional methods. 3D printing can produce electroactive components with precise control over material distribution, leading to enhanced actuator performance.
- Electrospinning: This technique generates fine fibers from polymer solutions using high voltage. The resulting nanofibers possess a large surface area, improving the actuator's responsiveness and functionality. Electrospun mats are often used in applications needing lightweight and flexible actuators.
- Inkjet Printing: Similar to traditional printing, this method deposits conductive inks onto surfaces. This technology enables cost-effective production, especially for devices requiring intricate electronic circuits integrated with electroactive materials.
These processes are important for producing high-quality electroactive polymers tailored for specific applications, whether in robotics, biotech, or electronics.
Challenges in Production
Despite the advances in fabrication techniques, challenges arise in the production of electroactive polymers. These issues must be comprehensively understood to improve manufacturing and ensure the reliability of the finished products. Key challenges include:
- Uniformity and Quality Control: Achieving consistent material properties across batches can be difficult, especially when using new or experimental materials. Variability can directly affect performance, making stringent quality control essential.
- Scalability: Many advanced fabrication techniques, such as 3D printing and electrospinning, show advantages at smaller scales but can present difficulties when transitioning to mass production. The challenge is to maintain efficiency while ensuring product quality and performance remain high.
- Material Compatibility: Different electroactive polymers may not be compatible with each other, leading to complications during multi-material fabrication. Ensuring that the materials can work together without compromising performance is a critical consideration.
- Long-Term Stability: Electroactive materials can exhibit performance degradation over time due to environmental factors such as humidity, temperature, and mechanical stress. Developing production methods that enhance the longevity of these polymers is crucial for applications where durability is essential.
Identifying and addressing these challenges enhances the reliability and applicability of electroactive polymer actuators. As research progresses, solutions to these production obstacles will advance the integration of these materials into modern technology.
Applications in Robotics
Electroactive polymer actuators have become critical in the field of robotics, particularly due to their unique properties and capabilities. The primary benefit these actuators provide is their ability to facilitate movement in a lightweight and efficient manner. Robots often require flexibility, adaptability, and efficiency, which these polymers can deliver.
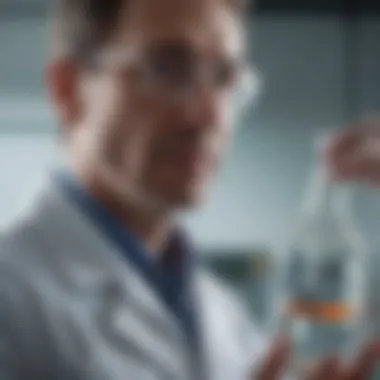
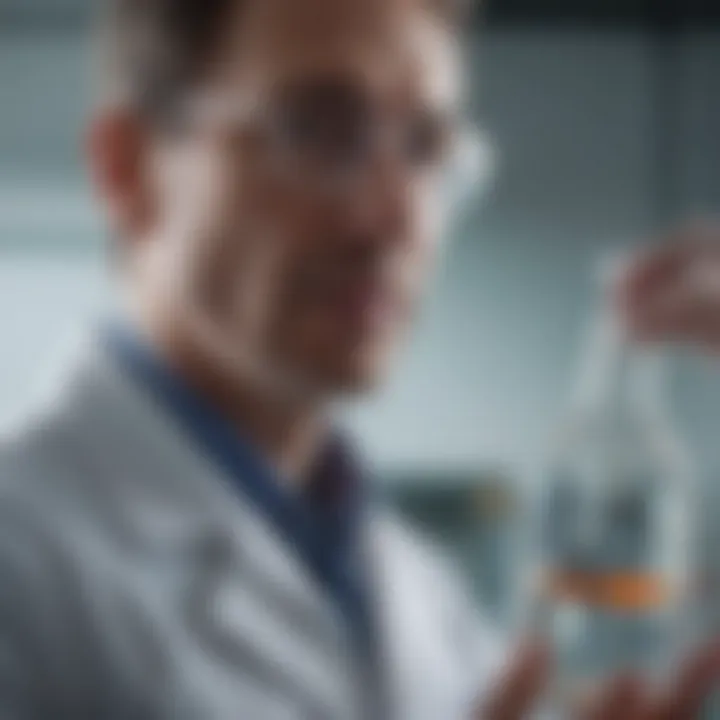
Moreover, with their capacity for significant deformation and responsiveness to electric stimuli, electroactive polymer actuators can mimic movements found in living organisms. This biomimetic approach enhances robot design, allowing for softer and more compliant robotic systems. These systems are especially useful in environments where gentle interaction is crucial, such as in healthcare or personal assistance. The capacity for nuanced movement also opens pathways to advanced applications, like rehabilitation robots or exoskeletons.
Considerations must be made regarding the actuatorโs performance in real-world scenarios. For instance, control strategies must be developed to handle the nonlinearities associated with electroactive polymers. Additionally, integrating these actuators into existing robotic platforms can be challenging, requiring thoughtful engineering solutions.
"The integration of electroactive polymers into robotics marks a significant transition in design philosophy, emphasizing adaptability and interaction."
Soft Robotics
Soft robotics is a prominent area that benefits greatly from electroactive polymer actuators. Unlike traditional rigid robots, soft robots utilize flexible materials, enabling them to navigate complex environments more effectively. Electroactive polymers allow these soft robots to alter their shapes and configurations when stimulated, providing a form of actuation that traditional motors cannot match.
The applications for soft robots span multiple sectors. In the medical field, soft robots can assist in delicate surgical procedures, adapting their form to fit various anatomical structures. In agricultural settings, they can gently harvest fruits without damaging them. The inherent design of robots utilizing electroactive polymers allows them to perform daily tasks while remaining safe and non-intrusive.
Furthermore, the scalability and design flexibility offered by electroactive polymers simplify the development of multifunctional soft robotic systems. Combining these materials with sensors and control algorithms can lead to responsive systems able to interact dynamically with their surroundings.
Actuation and Control Mechanisms
Actuation and control mechanisms are at the core of how electroactive polymers function within robotic systems. The actuation process involves converting electrical energy into mechanical movement, which is pivotal in efficient robotic operations. Understanding the control mechanisms is crucial for optimizing performance and ensuring reliability in applications.
Actuators using electroactive polymers need precise control strategies due to their unique response characteristics. Techniques such as feedback control loops are essential for managing the actuator's performance. Sensors embedded in the actuators can provide real-time feedback, allowing for adjustments on the fly.
Key points to consider include:
- The importance of designing control systems tailored to the specific characteristics of the electroactive polymers.
- The integration of machine learning to improve the adaptability of robotic systems over time.
- The necessity for simulation and modeling to predict actuator behavior under varying conditions.
Biotechnology Applications
The intersection of electroactive polymers and biotechnology presents a range of transformative possibilities that can significantly impact health care and medical technology. Electroactive polymers have unique properties that allow them to respond to electrical stimulation, providing versatile tools for various applications in this sector. Understanding these applications is essential for advancing medical devices and improving patient outcomes.
Biomedical Devices
Electroactive polymers have started to play an increasingly vital role in the development of biomedical devices. Their ability to change shape or size in response to electric signals makes them suitable for various medical applications, including prosthetics and implants. These polymers can mimic natural tissues, offering better integration within the human body.
Some key benefits of using electroactive polymers in biomedical devices include:
- Biocompatibility: Many electroactive polymers can be engineered to be biocompatible, meaning they can coexist with biological tissues without causing adverse reactions.
- Adaptive Functionality: These materials can adjust their mechanical properties based on electric signals or environmental conditions, offering a level of adaptability that traditional materials cannot match.
- Energy Efficiency: Electroactive polymer devices require less energy compared to conventional actuators, making them suitable for long-term applications like implantable devices.
However, designers must consider challenges such as the mechanical stability and lifetime of these devices. Proper material selection and optimization are crucial in ensuring that the devices perform reliably over time.
Tissue Engineering
Tissue engineering is another significant frontier for electroactive polymers. The aim is to repair or replace damaged tissues and organs using biological substitutes. Electroactive polymers can contribute to this field by acting as scaffolds that provide both mechanical support and electrical stimulation needed for cell growth.
They can promote cell alignment and proliferation due to their unique mechanical and electrical properties. This is particularly relevant when engineering cardiac or skeletal muscle tissues, where alignment of cells is paramount for effective functioning. Key points include:
- Enhanced Cell Growth: The stimuli-responsive nature encourages preferable cell behavior. This can expedite the healing process and improve the integration of grafts.
- Controlled Release of Pharmaceuticals: Electroactive polymers can be designed to release growth factors or drugs on demand, offering controlled delivery that can be tailored to specific needs.
- Monitoring and Feedback: These polymers can be embedded with sensors, allowing continuous monitoring of tissue status and automated adjustments to therapies as needed.
Electronics Integration
The integration of electroactive polymers (EAPs) into electronic devices represents a significant leap in functionality and versatility. Electroactive polymers can fundamentally change how electronic components interact with their environment. By enabling actuation, sensing, and responsive behaviors in devices, EAPs provide an avenue for creating smarter, more adaptive technologies.
One of the primary benefits of electronics integration is the fluid combination of functionality. Devices can become lighter and more efficient. Traditional electromechanical systems may rely on several separate components, increasing complexity and weight. EAPs can reduce the number of required parts by combining sensing and actuation in one material. This can lead to more compact designs crucial for portable and wearables.
Another significant consideration in this integration is the compatibility of these polymers with existing electronic systems. EAPs must be able to communicate effectively with standard electronic control systems. This can include anything from microcontrollers to larger processing chips. Developing compatible interfaces is essential to ensure reliable performance and seamless operation.
Smart Textiles
Smart textiles are one of the most promising applications for integrating electroactive polymers. These textiles can adjust their characteristics in response to external stimuli, making them suitable for various applications, including fashion, healthcare, and sports.
The potential for EAPs in smart textiles lies in their ability to respond to electrical signals. For example, fabric embedded with EAPs can change shape or stiffness when an electric current passes through it. This capability can be used in adaptive clothing that adjusts to temperature, improves comfort, or even helps monitor health conditions.
Some innovative designs are already in development. The integration of sensors can provide real-time data about a person's movement or posture. This information can be crucial for injury prevention in athletes or for monitoring patients in rehabilitation scenarios. Smart textiles can also enhance user experiences in fashion, allowing garments to change patterns or colors based on the wearer's mood.
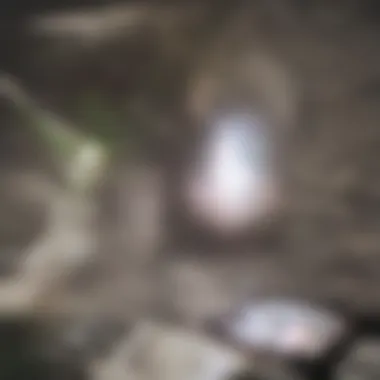

Microdevices and Sensors
Microdevices and sensors are another critical area where the integration of electroactive polymers shows great promise. As the demand for miniaturization continues, EAPs provide unique solutions for creating smaller, more efficient electronic devices.
Microdevices utilizing EAPs can achieve intricate functionalities that are unattainable with traditional materials. For instance, EAPs can serve as both actuators and sensors, enabling more sophisticated feedback mechanisms within devices. This dual functionality can lead to better performance in applications like robotics where precision and responsiveness are vital.
The focus on sensors is particularly relevant. EAP-based sensors can detect changes in pressure, acceleration, or deformation. These sensors can be applied in numerous fields, including environmental monitoring, healthcare, and even consumer electronics. A common example is the deployment of EAP sensors in soft robots, allowing them to interact more delicately with their surroundings.
"The integration of EAPs into electronics offers not just improvement but transformation in how devices operate and interact with the world."
Current Challenges and Limitations
The exploration of electroactive polymer actuators unveils various challenges and limitations that hinder their widespread application and performance. Understanding these aspects is crucial for researchers and professionals involved in the development of these materials. Addressing these limitations can lead to innovative solutions, which may catalyze future advancements in the field.
Performance Issues
Performance issues stand as a significant barrier to the effective deployment of electroactive polymers. One of the prominent concerns is the inconsistency in actuation response. Many electroactive polymers exhibit varying degrees of performance based on environmental conditions, such as temperature and humidity. For instance, dielectric elastomers may lose their efficiency when exposed to extreme temperatures, significantly affecting their usability in areas requiring precise and reliable actuation.
This inconsistency can be problematic in practical applications, where reliability is crucial. For robotics, precision in movement is necessary, while in biomedical devices, accurate dosages and responses can determine patient safety. To overcome this, rigorous testing under different environmental conditions is essential. Further research is needed to develop protocols that standardize performance measurements, giving insights into real-world behavior.
Additionally, the electrical field required for actuation can lead to dielectric breakdown, limiting the maximum operational voltage. This phenomenon not only restricts performance but can also pose safety risks. Potential strategies to enhance performance include tailoring the polymer compositions and refining fabrication techniques.
Durability and Longevity
Durability and longevity of electroactive polymers is another major concern. Many of these materials, while innovative, tend to experience degradation over time, affecting their long-term functionality. For example, repeated deformation can cause fatigue, leading to the material losing its elasticity and actuation capability. This issue is prominently seen in ionic polymer-metal composites, where metal electrode detachment can significantly degrade performance after extensive use.
Moreover, exposure to environmental factors like moisture and UV radiation can further accelerate degradation. Understanding the environmental resilience of these materials is vital. Research into improving the weather resistance and fatigue life of electroactive polymers will be critical for enhancing their applicability in outdoor environments.
Evaluating durability should also encompass the life cycle costs of employing these materials in devices. Professionals need to assess not only initial costs but also maintenance and replacement costs over the device's expected lifetime. This holistic approach could impact the decision-making process regarding material selection for specific applications.
Future Perspectives
Electroactive polymers (EAPs) represent a promising frontier not only in material science but in various applied fields. The importance of discussing future perspectives lies in understanding how these materials will evolve and influence new technologies. As research progresses, the role of EAPs can expand significantly, leading to enhanced actuation capabilities, improved performance metrics, and application versatility. This section delves into the advances in materials science and emerging applications that are poised to reshape industries.
Advances in Materials Science
Recent years have seen impressive developments in materials science related to electroactive polymers. Researchers are focused on improving the fundamental material properties, which directly impact performance.
Some of the key areas of advancement include:
- Composite Materials: Integration of different materials enhances the properties of EAPs. For example, combining conductive polymers with nanomaterials can produce actuators that show better performance and enhanced durability.
- Enhanced Conductivity: Traditional limitations in electrical conductivity are addressed through the use of novel additives. Materials like graphene and carbon nanotubes are frequently explored to push the conductivity envelope.
- Self-healing Capabilities: This aspect is crucial for increasing the lifespan and durability of actuators. Self-healing polymers can repair themselves after damage, significantly reducing maintenance and replacement costs.
- Tailored Response Mechanisms: In the future, scientists aim to design polymers that respond dynamically to specific stimuli, offering tailored actuation for precise applications.
The convergence of these advancements could also lead to the development of hybrid actuators, merging the benefits of electroactive polymers with other actuation technologies. Such synergies could provoke a revolution in how and where EAPs are utilized.
Emerging Applications
The potential applications for EAPs are vast and varied, spanning multiple sectors and markets. Emerging trends indicate not only the deepening of established applications but also the exploration of wholly new avenues for implementation.
- Wearable Technology: As wearables become more sophisticated, EAPs may provide adaptive features. Their lightweight nature and flexibility can enable devices that conform better to the human body.
- Artificial Muscles: EAPs are actively being researched as alternatives to traditional actuators in robotics. Their ability to mimic biological muscles can offer softer and safer interaction in robotic systems designed to work alongside humans.
- Smart architectures: Buildings and structures designed with EAPs could incorporate capabilities for self-adjustment based on environmental conditions. This innovation could lead to improved energy efficiency and sustainability.
"The integration of electroactive polymers into various technologies heralds a new era of innovation and adaptation across multiple sectors."
- Healthcare Innovations: In the medical field, electroactive polymer actuators may emerge in advanced prosthetics or assistive devices, aiding individuals with disabilities for more natural movement.
- Environmental Monitoring Devices: EAPs could be used to create responsive sensors for environmental applications, enabling more accurate and dynamic responses to changing conditions.
Ending
The conclusion of this article serves as a pivotal point in understanding the larger narrative surrounding electroactive polymer actuators. It synthesizes the many elements discussed throughout the article, helping to highlight both the significance of the topic and its implications for future advancements.
Summary of Findings
In summary, we explored the principles that underlie the operation of electroactive polymers. Their unique properties allow for significant movement when an electrical field is applied. We reviewed several types, including conductive polymers, ionic polymer-metal composites, and dielectric elastomers. These materials have diverse applications, especially in soft robotics and biomedical devices, where their flexibility and responsiveness provide distinct advantages. Key challenges remain regarding durability and long-term performance, which need further research and development for practical deployment.
Significance for Future Technology
Looking forward, the potential of electroactive polymers in technology appears broad and transformative. As materials science progresses, we can expect the emergence of newer formulations that may overcome current limitations. Applications could expand further into smart devices and autonomous systems, enhancing efficiency and functionality. By continuing to research and innovate in this field, we can unlock new possibilities in various sectors, including healthcare, robotics, and consumer electronics. The integration of these actuators into everyday technology could mark a significant advancement in how we interact with devices and make them more adaptable to human needs.
The development of electroactive polymers could lead to highly responsive systems that significantly change our understanding of material behavior in technology.