Understanding Sintered Plastic: Applications and Benefits
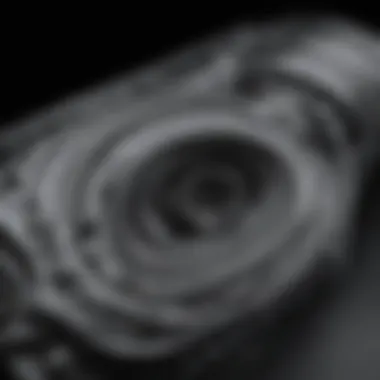
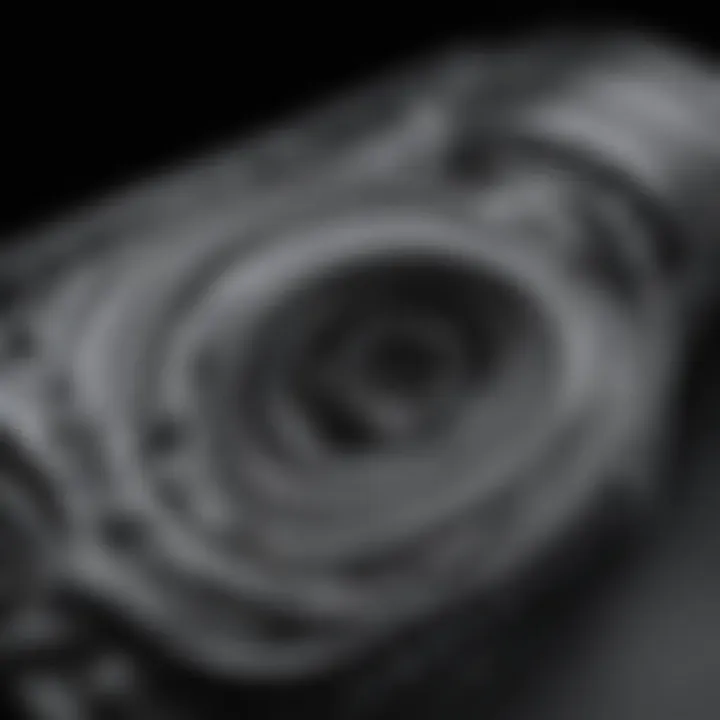
Intro
Sintered plastic has emerged as a significant material in various industries due to its unique properties and versatile applications. The process involves fusing polymer powders through heat and pressure, enabling the creation of complex shapes with high precision. This technique has garnered attention as manufacturers seek innovative ways to optimize production efficiency and reduce waste. Understanding sintered plastic requires an exploration of the material's core attributes, its manufacturing methods, and the landscape of current uses.
This article dives into these facets, offering insights into the advantages that sintered plastic holds over traditional manufacturing methods. The interplay of technology and material science will be a central focus, highlighting the potential future pathways for this unique approach. We will also analyze the broader implications of these advancements in the context of contemporary manufacturing requirements and sustainability goals.
Key Findings
Summary of the main results
Sintered plastic demonstrates numerous qualities, such as:
- Durability: Sintered plastics exhibit high resistance to wear and impact, making them ideal for applications requiring robust materials.
- Customizability: The manufacturing process allows for customized shapes and sizes, which can cater to specific industry needs.
- Lightweight: Compared to metals and ceramics, sintered plastics are significantly lighter, offering advantages in transport and overall application.
These findings reveal the material's potential to replace traditional materials in many sectors, especially where weight and efficiency play crucial roles.
Significance of findings within the scientific community
The exploration of sintered plastic is noteworthy for researchers and manufacturers alike. These findings contribute to the scientific discourse on:
- Advancements in additive manufacturing technologies.
- The potential for reduced environmental impact through less material waste.
- Enhanced performance characteristics that can lead to innovative applications.
The ongoing investigation into sintered plastic's properties and uses underscores the material's relevance in modern manufacturing contexts.
Implications of the Research
Applications of findings in real-world scenarios
Sintered plastic is making strides in various fields such as:
- Aerospace: Lightweight and durable components can improve fuel efficiency.
- Automotive: Custom parts can reduce production costs and assembly time.
- Consumer Electronics: Bespoke casings and components enhance both function and aesthetics.
These examples illustrate how sintered plastic enables industries to achieve greater efficiency and performance while meeting consumer demands.
Potential impact on future research directions
As the understanding of sintered plastic deepens, several potential research avenues emerge:
- Exploring new composite materials to enhance mechanical properties.
- Investigating the long-term sustainability of sintered plastic in relation to recyclability.
- Assessing the scalability of production methods to meet growing market demands.
Future advancements may further solidify sintered plastic's presence in manufacturing, providing new solutions that address contemporary challenges in various sectors.
Prologue to Sintered Plastic
Understanding sintered plastic is essential as it plays a significant role in modern manufacturing processes. This domain marries traditional plastic qualities with advanced material science, resulting in unique attributes that serve various industrial and consumer needs. By examining this topic, we can appreciate new dimensions of material properties and applications that arise from sintering techniques. Notably, the relevance of sintered plastic extends beyond mere functionality; it addresses environmental concerns and contributes to cost-effective production.
Defining Sintered Plastic
Sintered plastic refers to a method where powdered polymer is heated to a point where particles bond without becoming liquid. It stands out for its ability to create intricate shapes and designs that might be difficult to achieve with conventional processes. The characteristics of sintered plastic make it beneficial in areas like precision engineering, where exact specifications are not just preferred but required. This process allows for enhanced optimization in material usage, decreasing waste significantly when compared to traditional machining methods.
The term "sintering" itself denotes how fine particles adhere to one another during heating. The melting point of the base material is not reached, which preserves key properties of the polymer, such as flexibility, strength, and resistance to certain environmental factors. Thus, sintered plastic emerges as a valuable material in contexts where performance is paramount.
Historical Background
The development of sintered plastics can be traced to advancements in materials science during the mid to late 20th century. Initially, the focus was largely on metals and ceramics, but as the demand for lightweight and versatile materials increased, attention shifted towards plastics. Early applications adopted basic sintering methods primarily for industrial needs.
Research around the late 20th century brought significant innovations. Scientists began to recognize the potential of various polymer compositions to create sintered products. This realization led to broader industrial applications, particularly in the automotive and aerospace industries, where sintered plastics provided durable yet lightweight components. Today, sintered plastics find application beyond industrial uses, such as in consumer products and medical devices.
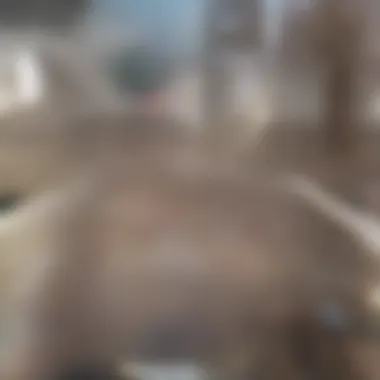
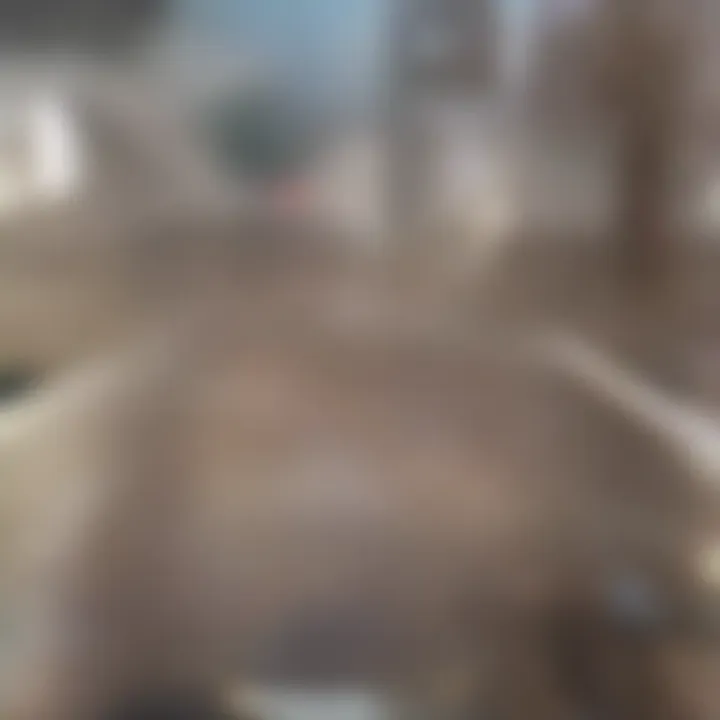
Overall, a grasp of sintered plastics’ origins helps to contextualize its current significance and future potential. As sustainability becomes increasingly fundamental, understanding how sintered plastic fits in a circular economy is crucial for researchers, technologists, and manufacturers.
Manufacturing Processes of Sintered Plastic
The manufacturing processes of sintered plastic hold great significance in this field. Understanding these processes helps to appreciate how sintered plastics achieve their unique properties and applications. The ability to manipulate material characteristics through specific manufacturing techniques opens new avenues for innovation.
Powder Preparation Techniques
Powder preparation is a crucial phase in the manufacturing of sintered plastics. It involves the production of fine powder from plastic materials that can be sintered effectively. The quality of this powder directly impacts the final product’s properties.
The process starts with the selection of the polymer raw materials. These can include polyamide, polypropylene, and other thermoplastics. The chosen materials undergo grinding to produce a consistent powder size. This uniformity is critical for ensuring even sintering, as variations can lead to weaknesses in the final product.
An important aspect of powder preparation is achieving the right particle size distribution. A well-defined range enhances packing density, which contributes to better mechanical properties and strength in the final sintered product. Additionally, additives such as lubricants may be included to improve flow characteristics and reduce friction during compaction.
Sintering Methods
Sintering methods define how the prepared powder is transformed into solid forms. Various techniques can be applied, each with its unique benefits and applications. Three significant sintering methods are Conventional Sintering, Laser Sintering, and Injection Molding.
Conventional Sintering
Conventional sintering is a widely used method that involves applying heat to the powder at a temperature below its melting point. This approach promotes particle bonding, resulting in solid forms. The key characteristic of conventional sintering is its simplicity and cost-effectiveness. Because it allows for the use of various materials, this method is a popular choice among manufacturers.
One unique feature of conventional sintering is the ability to produce complex geometries with good dimensional stability. However, it does face limitations in terms of product speed and uniformity in large scale production. The risk of defects due to uneven heating or insufficient temperature control can affect product quality.
Laser Sintering
Laser sintering represents an advanced technique that uses laser beams to fuse powdered material layer by layer. This method excels in creating highly detailed models and prototypes. The key characteristic of laser sintering is precision; it can produce intricate shapes that conventional methods may struggle with.
Laser sintering's unique feature lies in its capability to use a broad range of materials, including specialized polymers that traditional methods cannot process. However, the disadvantages include higher costs and slower production rates compared to conventional methods, which may be a concern for large-volume manufacturing.
Injection Molding
Injection molding is another significant method in manufacturing sintered plastics. This process involves injecting heated plastic powder into a mold and then applying heat and pressure to create a solid part. The key characteristic of injection molding is its ability to produce large quantities quickly and efficiently. It is beneficial for creating uniform products with consistent quality.
A unique feature of injection molding is its versatility; it can accommodate various shapes and sizes. Its advantages include rapid production and minimized waste. However, the initial setup costs can be high, and this method may not be suitable for low-volume projects.
Cooling and Post-Processing
The cooling and post-processing stages follow the sintering process. Cooling is critical as it influences the final material structure and properties. Proper cooling helps to reduce residual stresses that can lead to deformation. After cooling, additional post-processing steps may be necessary to refine the product. These can include machining, surface treatment, and quality inspection to ensure that the final part meets the required specifications.
Material Properties of Sintered Plastics
The study of sintered plastics is incomplete without an investigation of their material properties. Understanding these properties is essential because they dictate how these materials perform in various applications. These properties can differentiate sintered plastic from traditional materials and provide significant advantages in specific scenarios. Hence, the focus on material properties is crucial for students, researchers, and professionals working with advanced materials.
Physical Properties
The physical properties of sintered plastics include parameters like density, porosity, and surface texture. Density can vary significantly based on the resin and additives used during sintering. Generally, sintered plastics have a lower density when compared to metals. This factor makes them lighter and sometimes a better choice in applications where weight savings are critical, such as in automotive and aerospace sectors.
Porosity is another defining characteristic. Sintered plastics typically exhibit a degree of porosity. This may enhance insulation properties, making them suitable for electrical applications. However, excessive porosity can negatively impact mechanical integrity, so careful control during manufacturing is necessary. Surface texture can also vary and plays a role in the performance. A smoother surface can reduce friction in specific applications, while a rougher texture may enhance adhesion of paints or coatings.
Mechanical Properties
Mechanical properties are vital for evaluating the performance of sintered plastics under stress. Key aspects include tensile strength, compressive strength, and flexibility. Tensile strength refers to the resistance of the plastic to being pulled apart. Higher tensile strength can be particularly useful in structural applications where load-bearing is a concern.
Compressive strength comes into play in scenarios where the material is subjected to pressing forces. It is crucial in applications where shapes are retained under load, such as in support structures. Additionally, flexibility is another significant mechanical property. Some sintered plastics, such as polyamide, show considerable resilience and can return to their original shape after being deformed.
"Understanding the mechanical properties of sintered plastics helps industries select the appropriate material for specific applications."
Thermal Properties
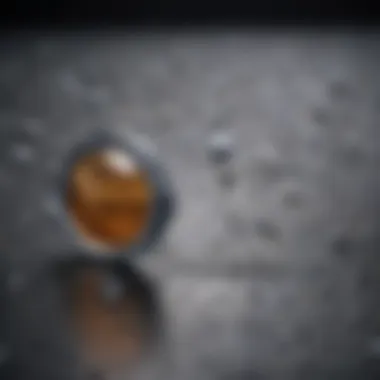
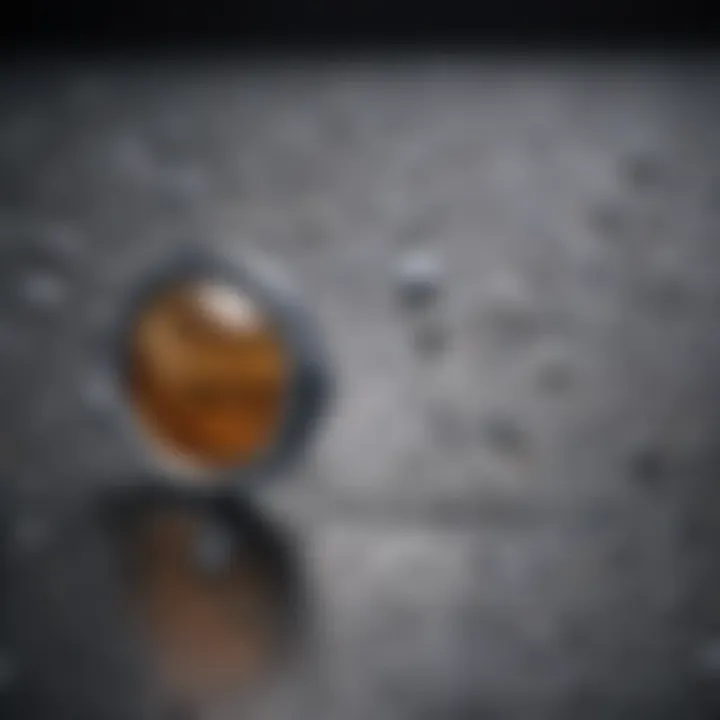
Thermal properties encompass thermal conductivity, heat resistance, and thermal expansion. Thermal conductivity is a measure of how well a material conducts heat. Sintered plastics usually have lower thermal conductivity compared to metals, making them good insulators in electronic applications. This is particularly advantageous for preventing overheating in sensitive components.
Heat resistance refers to how well a material can maintain its integrity at elevated temperatures. Certain sintered plastics can withstand high temperatures, making them suitable for use in engine compartments or other heat-intensive environments. Last, thermal expansion is important as it indicates how much a material will expand or contract with temperature changes. Knowing the thermal expansion characteristics is vital to avoid material failure in applications exposed to temperature fluctuations.
Applications of Sintered Plastic
Sintered plastic finds itself in a diverse array of applications across different sectors. This multitude of applications showcases both the versatility and efficiency of this material, which has become integral to modern manufacturing processes. With unique properties, sintered plastics provide solutions that traditional materials often cannot. This section highlights key areas where sintered plastics are utilized, along with discussing benefits and considerations.
Industrial Uses
In industrial settings, sintered plastics are recognized for their high-performance characteristics. They are used in various machinery parts, such as gears and bearings, due to their excellent wear resistance and low friction properties. Their lightweight nature reduces energy consumption in machines, making them a preferred choice for engineers seeking to optimize performance and efficiency.
Some specific examples include:
- Conveyor rollers: Sintered plastics are often employed in the manufacturing of conveyor systems. They withstand heavy loads while minimizing noise levels.
- Valves and fittings: Their ability to resist corrosion contributes to longer life spans in fluid handling applications.
Consumer Products
In the consumer sector, sintered plastics have revolutionized product design. The ability to create complex geometries has led to innovative applications in everyday items. For instance, sintered plastics can be found in products like electronics housings and household appliances. The combination of aesthetic design and functional performance allows manufacturers to meet both consumer demands and industry standards.
Sintered plastic applications in consumer products include:
- Mobile phones: Parts such as cases and internal components benefit from the lightweight and durable nature of these materials.
- Sporting goods: Items like custom fit eyewear frames are produced using sintered plastics to meet specific individual requirements.
Medical Applications
The medical field has increasingly turned to sintered plastics for its unique biocompatibility and sterilization properties. Applications range from surgical instruments to prosthetic devices. The ability to customize these materials for specific medical needs offers significant improvements in patient care.
Notable applications in this sector include:
- Implants: Custom orthopedic implants that match the patient's anatomy enhance recovery outcomes.
- Diagnostic equipment: Sintered plastic components are often used in devices that require precision and reliability, such as MRI machines.
Automotive Industry
Sintered plastics have carved out a substantial niche within the automotive industry. They are employed in applications that require high durability and resistance to harsh environments. This includes components such as battery cases, electrical connectors, and interior panels.
The automotive sector benefits from sintered plastics in several ways:
- Lightweighting: Using sintered plastics helps reduce the overall weight of vehicles, thereby improving fuel efficiency and performance.
- Environmental resistance: Sintered plastics are resistant to extreme temperatures and chemicals, making them suitable for under-the-hood applications.
The applications of sintered plastic are numerous and varied. Across industries, they provide functional advantages that enhance product performance and longevity. As industries continue to explore new uses, the role of sintered plastics is destined to expand further.
Advantages of Sintered Plastic
The advantages of sintered plastic are multifaceted, allowing it to stand out in various industries where performance and cost are critical factors. This section will detail specific benefits such as cost-effectiveness, design flexibility, and durability. Understanding these advantages helps industries make informed decisions when selecting materials for their projects and products.
Cost-Effectiveness
Sintered plastic offers notable cost advantages, especially in large-scale production. The manufacturing process involves shaping powdered materials through heat and pressure without requiring significant amounts of raw materials. This can lead to substantial savings. The lower material waste, compared to traditional methods, translates to reduced costs.
Moreover, sintered plastic parts usually require less machining or finishing. Therefore, this means lower labor costs. These aspects contribute to lowering the total production costs significantly. Companies applying sintered plastic in their manufacturing processes can yield products that balance performance and pricing better than some alternatives.
Design Flexibility
Another valuable advantage of sintered plastic is its design flexibility. The sintering process enables the creation of complex geometries that challenge conventional manufacturing methods. Designers often find that sintered plastic allows for the production of intricate shapes without substantial limitations, as there is no requirement for additional tooling.
This flexibility also supports rapid prototyping and customization. Companies can respond quickly to changes in market demands or target specific applications with tailored designs. Sintered plastic not only supports innovative designs but also encourages creative approaches in product development.
Durability and Longevity
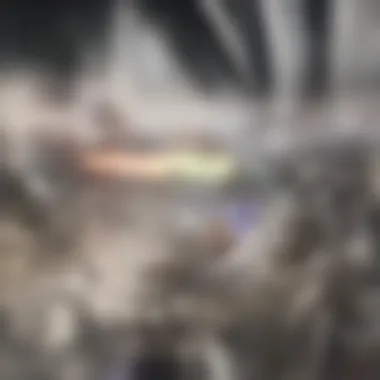
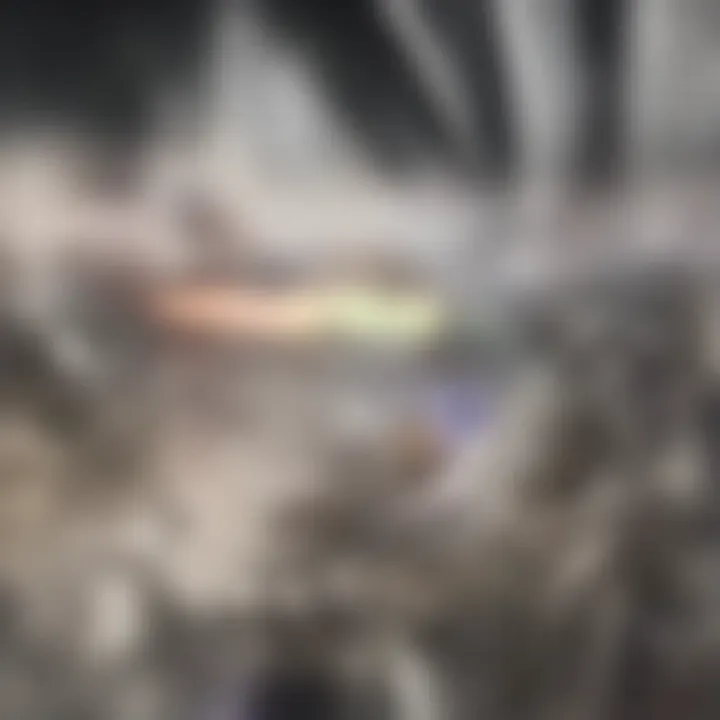
Durability is crucial in material selection. Sintered plastics often exhibit superior resilience when compared to their plastic counterparts. After sintering, these materials achieve high density and strength, which enhances their performance under stress. They can withstand harsh conditions, including temperature variations and chemical exposure, making them suitable for demanding applications.
The longevity of sintered plastic also makes it a compelling choice. Many products developed from sintered plastics can maintain their integrity over extended periods, reducing the need for frequent replacements. This reliability fosters customer satisfaction and loyalty while simultaneously cutting down on maintenance costs for companies.
"The combined advantages of cost, flexibility, and durability establish sintered plastic as a vital material in modern manufacturing.”
Challenges in the Sintered Plastic Sector
The use of sintered plastic is expanding its presence in various industries, but it is not without its challenges. Understanding these hurdles is essential for anyone involved in manufacturing or considering adopting sintered plastic for applications. This section dives into two major challenge areas: material limitations and environmental concerns.
Material Limitations
Sintered plastic has some unique material properties, but these also come with limitations. One important aspect is the strength of sintered parts compared to those made from traditional materials like metals. While sintered plastics can perform well under certain conditions, they may not always withstand the same stress.
Another element to consider is fabrication difficulties. Sintered plastics often require specific temperatures and pressures for sintering, which can limit the types of materials that can be effectively used. This means that manufacturers may have to compromise on the material choices, potentially affecting the overall performance of the final product.
Additionally, the surface finish of sintered parts can sometimes be rougher than desired. This can create challenges in specific applications where aesthetics or tight tolerances are crucial. To mitigate these issues, downstream processes may be needed. However, these add time and costs to production, which could affect overall competitiveness.
The challenges of material limitations in sintered plastics urge manufacturers to innovate continuously.
Environmental Concerns
The environmental impact of sintered plastic production raises significant concerns. Many of the raw materials used in sintered plastic processes come from petroleum-based resources. Their extraction and processing contribute to environmental degradation and resource depletion. Moreover, the life cycle of sintered plastic often does not favor sustainability. They can be difficult to recycle and resolve the extent of waste generated during production.
Another point of discussion is the carbon footprint associated with sintering processes. Although they can be less resource-intensive than some traditional manufacturing techniques, energy consumption remains a concern. As industries move towards cleaner and greener practices, this is an ongoing consideration that must be addressed.
Adoption of sustainable practices, such as utilizing bio-based materials or improving recycling methods, is essential for the future of sintered plastics. Stakeholders in the sector are increasingly emphasizing the importance of these environmental issues. Organizations and researchers are actively exploring solutions that might alleviate these concerns, ensuring that the benefits of sintered plastic do not come at too great an environmental cost.
Future Trends in Sintered Plastic Development
The landscape of sintered plastic is rapidly evolving. This section examines the future trends that are reshaping the industry. Understanding these trends is crucial for students, researchers, educators, and professionals who work in or study material science.
Innovations in Materials
Advancements in material science play a pivotal role in the progression of sintered plastics. New materials are being developed that enhance performance characteristics. For example, bio-based polymers are gaining traction as sustainable alternatives. These materials provide an eco-friendly option that still meets the rigorous demands of various applications. Their biodegradability offers a clear advantage in reducing environmental impact.
Additionally, composites that blend traditional plastics with advanced fibers are emerging. These composites exhibit superior strength and durability, expanding the potential applications in industries such as aerospace and automotive. By leveraging the unique properties of these materials, manufacturers can create components that are not only lightweight but also robust.
Moreover, the incorporation of additives and fillers can modify the behavior of sintered plastics. This allows for fine-tuning of thermal, mechanical, and chemical properties. Such innovations ensure that sintered plastic remains a competitive choice in various high-performance settings.
Advancements in Technology
Alongside material innovation, technological advancements are propelling the future of sintered plastic. The emergence of advanced manufacturing techniques significantly enhances production efficiency. One notable example is the development of digital fabrication technologies. Techniques such as additive manufacturing and 3D printing enable the creation of complex geometries that were previously difficult to achieve.
Additionally, the continuous improvement in sintering methods, especially laser sintering, shows promise. This technique allows for finer control over the sintering process, resulting in improved part quality and reduced waste. Such advancements not only optimize resource use but also enhance the overall cost-effectiveness of production.
Furthermore, automation and smart technologies are playing a larger role in manufacturing processes. The adoption of Industry 4.0 principles facilitates real-time monitoring and data analytics, leading to smarter decision-making in production. This means that sintered plastics can be produced with greater precision and less human intervention, ultimately reducing errors.
"The integration of advanced materials and cutting-edge technology will drive the next generation of sintered plastics, showcasing their versatility and relevance in modern manufacturing."
The End
The concluding section serves as a critical synthesis of the discussions in this article. It encapsulates the fundamental aspects of sintered plastic, emphasizing its significance in modern manufacturing processes. Sintered plastic offers distinct advantages that stand apart from traditional materials.
Summary of Key Points
- Definition and Historical Context: Sintered plastic is a specific form of material processing that utilizes heat and pressure to meld powdered plastic into a solid structure. Its historical development underscores its growth and application within various industries.
- Manufacturing Processes: The article delves into the manufacturing methods of sintered plastic which includes powder preparation, different sintering techniques, and post-processing steps that are pivotal to create robust end products.
- Material Properties: Highlighting the physical, mechanical, and thermal properties reveals the versatility of sintered plastic. These properties make it suitable for numerous applications, ranging from industrial equipment to consumer goods.
- Applications: Industries such as automotive, medical, and consumer products utilize sintered plastic due to its flexibility, cost-effectiveness, and durability.
- Advantages and Challenges: The benefits of sintered plastic, including cost and design flexibility, are balanced by material limitations and environmental considerations that must be addressed in future developments.
- Future Trends: Current innovations hint at a promising future for sintered plastic, driven by advancements in materials and technology that can enhance its performance and expand its utility.
Future Outlook for Sintered Plastic
As industries evolve, the relevance of sintered plastic continues to grow. The demand for sustainable materials and processes is shaping the future of manufacturing. Innovations in biodegradable plastics and eco-friendly sintering techniques are likely to emerge, addressing environmental concerns while maintaining performance standards.
Moreover, advancements in technology, particularly in digital design and manufacturing, may streamline production methods. Techniques such as 3D printing can be integrated with sintering processes to create complex geometries at lower costs, pushing the boundaries of design flexibility even further.
Thus, the future of sintered plastic looks not only bright but also crucial for various sectors aiming for efficiency and sustainability. It remains an area of significant research and development, promising to yield even more versatile and practical applications in the years to come.