In-Depth Analysis of Rubber Vulcanization Process
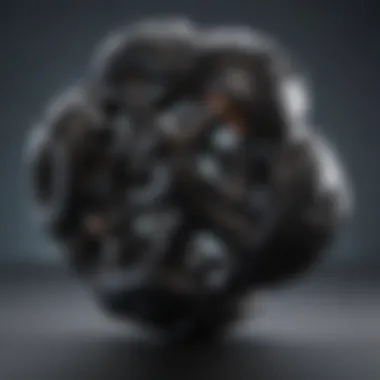

Intro
Vulcanization is one of those unsung heroes of material science, silently shaping the world around us. It’s a process that takes plain, flexible rubber and turns it into something far more robust and useful. This transformation is essential in industrial applications, from tires to seals, ensuring they endure extreme conditions and maintain performance. In this article, we will peel back the layers on rubber vulcanization, examining the mechanisms at play and how they apply to various sectors.
Understanding the significance of this process gives insights into its historical roots and its modern-day relevance. Each step of vulcanization involves an intricate dance of chemical reactions and heat application, leading to cross-linking in the rubber's molecular structure. These changes enhance resilience, elasticity, and longevity, so it’s no wonder that various industries rely on this process for producing high-quality rubber products.
Throughout the discussion, we will also touch on innovative advancements that are paving the way to more sustainable practices in rubber production and explore future pathways for research and development. By the end of this read, you’ll have a comprehensive grasp of rubber vulcanization—its chemistry, applications, and the impact it has on both everyday life and specialized fields of work.
Key Findings
Summary of the main results
The core findings of rubber vulcanization highlight several crucial aspects:
- Chemical Reactions: The process involves a series of reactions, primarily focusing on sulfur cross-linking which enhances the overall strength and elasticity of rubber.
- Material Durability: Vulcanized rubber exhibits astounding resilience against wear, heat, and various environmental stressors, making it ideal for demanding applications.
- Diverse Applications: From automotive tires to industrial pipes, the use-cases for vulcanized rubber are vast, illustrating its indispensability in modern manufacturing.
Significance of findings within the scientific community
The findings on rubber vulcanization are pivotal. The scientific community recognizes that advancements in this field can lead to improvements in material technology, bringing about solutions for ongoing challenges like environmental degradation and resource sustainability. Recent innovations showcase how modified vulcanization processes can reduce energy consumption and emissions, directly contributing to more eco-friendly manufacturing.
Implications of the Research
Applications of findings in real-world scenarios
The insights gleaned from understanding vulcanization have led to numerous practical applications:
- Automotive Industry: The production of tires that withstand higher pressures and temperatures, improving safety and performance.
- Medical Equipment: Creation of surgical apparatus that requires sterile and durable materials, ensuring safety and reliability.
- Consumer Products: Development of everyday items such as footwear and household goods that benefit from enhanced longevity and function.
Potential impact on future research directions
Future research avenues may focus on:
- Sustainability: Investigating bio-based alternatives to traditional rubber compounds to reduce ecological footprints.
- Smart Materials: Exploring how modern technology can integrate into vulcanization processes to produce responsive materials capable of adapting to varying conditions.
- Enhanced Performance: Continuous refinement of the vulcanization process to push the limits of rubber performance in extreme applications.
"Vulcanization is not merely about making rubber hard; it's about enhancing its life cycle and expanding its capabilities, thus opening doors to endless possibilities."
Preface to Rubber Vulcanization
Rubber vulcanization is a fundamental process that plays a vital role in transforming raw rubber into a highly durable material suitable for a multitude of applications. This section aims to shed light on the essence of vulcanization, delving into its significance and historical backdrop. Understanding this process is crucial not only for students and researchers but also for industry professionals engaged in material science and engineering.
Definition and Importance
At its core, vulcanization is a chemical process that involves the cross-linking of polymer chains in rubber. This transformation enhances the material's strength, elasticity, and heat resistance. The significance of vulcanization cannot be overstated as it ensures that rubber has the necessary properties to withstand wear, weather conditions, and various loads encountered in practical applications.
One might say that without vulcanization, rubber would be little more than an overly elastic material, unable to meet the demanding needs of industrial and consumer products. For instance, the tires on vehicles – which undergo intense friction and heat – rely heavily on the vulcanization process for optimal performance.
The benefits of vulcanization extend beyond mere durability. Properly vulcanized rubber can provide excellent aging resistance, meaning it does not deteriorate as quickly when exposed to environmental factors such as sunlight or ozone. This characteristic is key for products that are designed to have a longer service life, thus reducing waste and promoting sustainability in production.
Historical Overview
The history of vulcanization is quite fascinating, dating back to the early 19th century when it was simultaneously discovered by Charles Goodyear and Thomas Hancock. In 1839, Goodyear famously dropped a mixture of rubber and sulfur onto a hot stove, resulting in a remarkable transformation—a process that would drastically change the rubber industry.
Unlike the rudimentary methods of his time, Goodyear's vulcanization process laid a solid foundation for the industrial application of rubber. It took several years for this technique to gain traction, but by the late 1800s, the rise of industries such as automotive and manufacturing drove a demand for high-quality rubber products. This shift marks a pivotal moment wherein rubber went from being a novelty to an essential component in machinery, construction, and countless consumer products.
As we navigate through the realms of vulcanization in this article, it becomes apparent how historical developments inform current practices and innovations in the field.
"Vulcanization is not merely a chemical transformation; it's an evolution of material technology that continues to shape our modern world."
The successive advancements, especially in synthetic rubber, have broadened the applications of vulcanized rubber, making it indispensable in diverse sectors ranging from automotive to healthcare. The exploration of these aspects will continue to be a recurring theme throughout this article.
Fundamental Chemistry of Rubber
Understanding the fundamental chemistry of rubber is key to grasping the intricacies of vulcanization. Rubber, in its raw form, is a complex polymer composed of long chains of molecular units that confer both elasticity and resilience. The chemistry behind rubber determines its properties, behaviour under stress, and suitability for various applications. By delving into the chemistry, one can appreciate not only the versatility of rubber but also the pivotal role it plays in numerous industries.
Composition of Natural Rubber
Natural rubber is primarily derived from the latex of the rubber tree, Hevea brasiliensis. This milky fluid is rich in polyisoprene, a polymer that forms the backbone of natural rubber. Polyisoprene has a unique molecular structure—essentially repeating units that form long chains. This configuration is crucial as it accounts for the remarkable elasticity and strength of the rubber.
The composition of natural rubber is not just about polyisoprene. There are various non-rubber components present, including proteins, lipids, and carbohydrates. These constituents can significantly influence the performance of the rubber, impacting its adhesive qualities, aging resistance, and even how it interacts with other materials during the vulcanization process.
- Advantages of Natural Rubber:
- Superior tensile strength.
- Excellent resilience and flexibility.
- Biodegradable, making it an eco-friendly choice.
However, natural rubber does have its drawbacks. It can be prone to degradation due to heat, oxygen exposure, and certain chemicals. This is where vulcanization comes in—adding chemical agents to enhance its durability and resistance to such factors, thus broadening its application range.
Synthetic Rubber Variants
Synthetic rubber was developed as a response to the limitations of natural rubber. With the advent of petrochemical processes in the 20th century, various synthetic rubber variants emerged, each tailored for specific applications. The most common types include Styrene-Butadiene Rubber (SBR), Neoprene, and Butyl rubber.
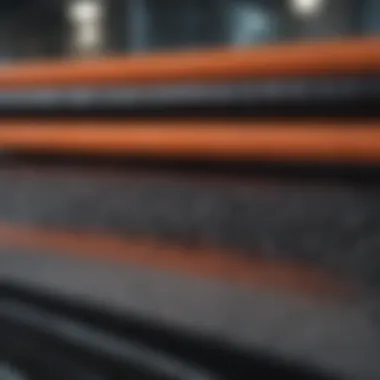
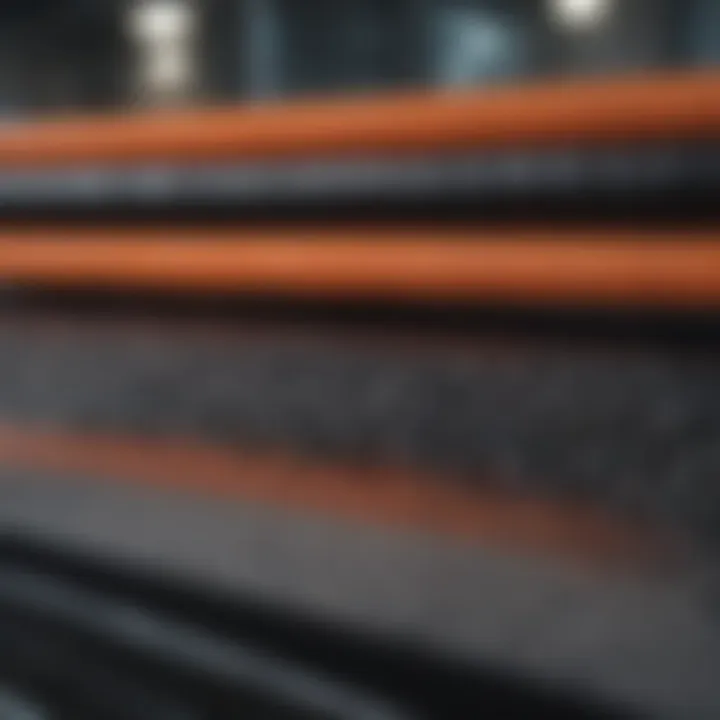
- Styrene-Butadiene Rubber (SBR):
- Neoprene:
- Butyl Rubber:
- Widely used in tires due to its excellent wear resistance.
- Composed of a copolymer of styrene and butadiene, offering a balance of durability and elasticity.
- Known for its chemical stability and weather resistance.
- Often utilized in automotive and construction applications.
- Renowned for its air retention properties, commonly found in inner tubes of tires.
- Less permeable to gases, making it ideal for applications requiring airtight seals.
The versatility of synthetic rubber is a game-changer, enabling the development of materials tailored to withstand specific environmental conditions or stresses. As industries evolve and demand increases for specialized rubber products, synthetic variants will likely continue to evolve in terms of chemistry and application.
Exploring the chemistry of both natural and synthetic rubber opens the door to understanding how different formulations can meet the safety, durability, and performance needs of modern industries.
In summary, the fundamental chemistry of rubber, encompassing both natural and synthetic variants, lays the groundwork for comprehending the vulcanization process and its broader implications in various sectors. Knowing the components and their unique characteristics illuminates the pathway toward innovation in rubber applications.
The Vulcanization Process Defined
The vulcanization process is a pivotal stage in the rubber industry, serving as the bridge transforming raw rubber into a material of remarkable durability and versatility. Understanding this process is essential as it uncovers the chemical and physical transformations that significantly enhance rubber's properties. As we delve deeper, the intricate interplay of temperature, chemicals, and time emerges as vital considerations that shape the outcome of the vulcanization process.
Raw Material Preparation
Before any rubber undergoes vulcanization, it is paramount to prepare the raw materials correctly. This preparation involves several steps, all ensuring that the raw rubber is suitable for the curing process. Typically, natural rubber sourced from latex trees undergoes extraction and purification. For synthetic alternatives, a polymerization process is needed, usually involving compounds like styrene and butadiene.
After the initial processing, additives come into play. Fillers such as carbon black are introduced. They improve strength and resilience, but the types and amounts used vary depending on the desired properties of the final product. Other chemicals, like accelerators and anti-aging agents, are also integrated at this stage to enhance the rubber's performance down the line.
Cross-Linking Mechanism
Once the raw materials are properly prepared, the cross-linking mechanism sets the stage for the actual transformation. This mechanism is fundamentally about creating bonds between polymer chains, effectively turning a sticky, malleable material into something strong and elastic.
The core of cross-linking often revolves around sulfur. When the rubber mix is heated with sulfur, a series of reactions occur that link the individual polymer chains together. This brings about a three-dimensional network structure, enhancing properties like heat resistance and tensile strength. Importantly, the degree of cross-linking can be adjusted. Too much can lead to brittleness, and too little may result in a lack of strength. Balancing this carefully is key to achieving the desired rubber properties.
Curing Agents and Their Roles
Curing agents play a crucial role in vulcanization, each serving specific purposes. The most well-known agent is sulfur, but the landscape includes many alternatives depending on application needs. For instance, peroxide curing agents provide benefits such as improved heat resistance and aging properties. Each agent interacts uniquely with the rubber matrix during the vulcanization process.
Here's a quick look at some common curing agents and their notable characteristics:
- Sulfur: Enhances elasticity but can lead to a slower cure time.
- Peroxides: Offer higher thermal stability but require higher curing temperatures.
- Resins: Can enhance the bonding between fillers and rubber, improving mechanical properties.
- Metal Oxides: Often used in conjunction with sulfur to act as a promoter in the curing process.
Using the right curing agent depends largely on the final application of the rubber. The interplay of these curing agents with the prepared raw materials determines the ultimate quality of the vulcanized rubber, impacting everything from performance in auto parts to medical devices.
"The vulcanization process is not just a step; it is the essence of rubber's transformation into a versatile material that meets the demands of various industries."
By understanding the intricacies of these processes, industry professionals can innovate and improve upon existing formulations and processing techniques, ultimately pushing the boundaries of what's possible in rubber technology.
Factors Influencing Vulcanization
Understanding the factors influencing vulcanization is pivotal in mastering the art of rubber processing. Several key elements come into play, each impacting the quality and characteristics of the final product. From temperature and time to pressure and atmosphere, these variables not only govern the efficiency of the curing process, but they also determine the robustness and longevity of the rubber. Grasping how these aspects work together can lead to significant advances in both industrial applications and product performance.
Temperature and Time
Temperature and time are perhaps the two most critical parameters during the vulcanization process. The relationship between heat and the curing duration directly affects the degree of cross-linking of polymer chains, which ultimately influences the rubber's properties.
- Optimal Temperature: Each rubber formulation has a specific optimal temperature for vulcanization. Exceeding this can lead to undesirable effects, like scorching—where the rubber becomes brittle, losing elasticity and strength. Conversely, insufficient heat may result in incomplete vulcanization, leaving the rubber soft and yielding poor mechanical properties.
- Curing Time: The time allotted for vulcanization is equally crucial. Insufficient time may lead to a weak cross-linked structure, while excessive time can decompose the rubber, affecting its integrity. Thus, finding the right balance is essential for achieving the desired material properties.
"A well-timed vulcanization process can mean the difference between a reliable product and a failure in performance."
Pressure and Atmosphere
The influence of pressure and atmosphere on the vulcanization process is often overlooked, yet these elements can significantly affect the outcome.
- Pressure Levels: Applying appropriate pressure ensures that the rubber compounds are compressed evenly, promoting a uniform curing process. This also aids in enhancing the density of the finished product. Too much pressure can restrict the expansion of the rubber, leading to defects, while too little may allow air pockets, which detract from the strength and integrity of the material.
- Atmospheric Conditions: The environment in which vulcanization occurs—namely, the atmosphere—also plays a role. Vulcanizing under inert conditions can prevent oxidation, which can degrade the rubber. Understanding how various gases interact at elevated temperatures is essential for optimizing formulations, especially when dealing with sensitive additives.
In essence, optimizing temperature, time, pressure, and atmospheric conditions is vital for producing high-quality vulcanized rubber. These factors not only refine the chemical processes during vulcanization but also ultimately shape the applications of rubber in our daily lives, from automotive parts to medical devices.
Types of Vulcanization
Understanding the types of vulcanization is pivotal in the realm of rubber processing. This section digs into the various methods used in the vulcanization industry, highlighting their importance, benefits, and considerations. Each type caters to specific requirements in terms of performance, efficiency, and the intended application of the final product. The right choice of vulcanization process can directly influence the material properties, lifecycle, and overall functionality of the end product. Therefore, it’s crucial for professionals in this field to have a solid grasp of these distinctions.
Accelerated Vulcanization
Accelerated vulcanization is a game-changer. It involves the use of heat, pressure, and added chemicals to speed up the curing process. This not only saves valuable production time but also improves efficiency. Techniques such as steam curing or the incorporation of accelerators like mercaptobenzothiazole (MBT) can be crucial in this method.
Here are some advantages to consider:
- Time Efficiency: Accelerating the curing phase significantly reduces the time required for production.
- Improved Productivity: Shorter curing times enable manufacturers to increase throughput, which is a critical factor in high-demand scenarios.
- Better Material Properties: When done correctly, this method can actually enhance the elasticity and durability of the vulcanized rubber.
However, not all that glitters is gold; there are foibles too. For instance, excessive heat might lead to scorching, adversely affecting the rubber’s quality. Thus, careful monitoring of conditions is imperative to strike a balance.
Sulfur vs. Peroxide Curing
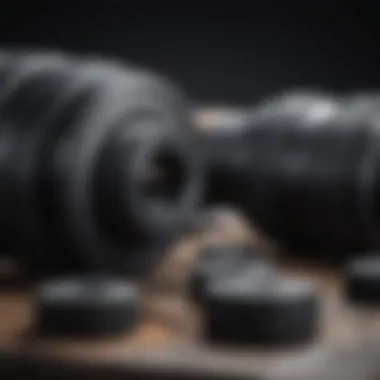
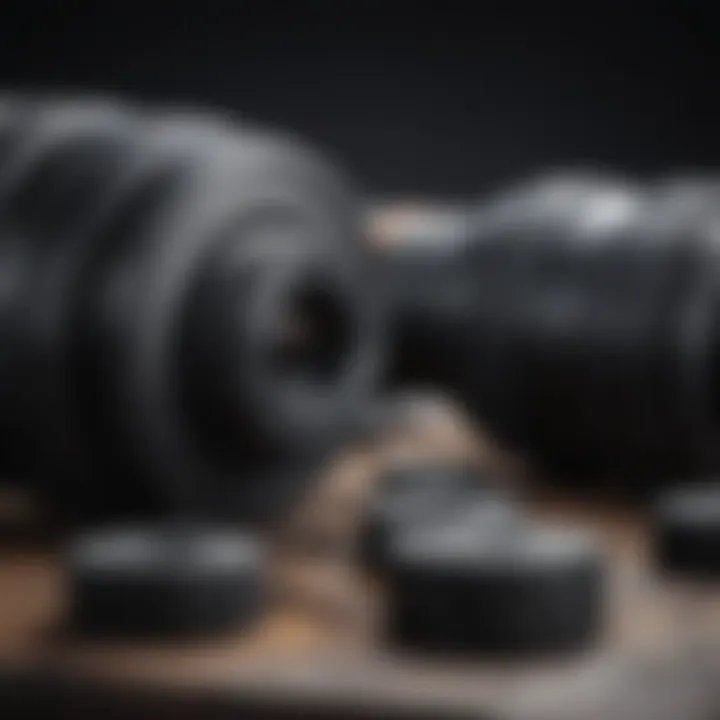
When we delve into vulcanization techniques, the debate between sulfur and peroxide curing takes the stage. Each method has its own set of merits and potential drawbacks, influencing application suitability and performance characteristics in distinct ways.
Sulfur Curing: This is perhaps the most traditional and widely used method. It involves the cross-linking of rubber molecules using sulfur, which offers several benefits:
- Flexibility: Produces rubber with significant elasticity, allowing for its use in a variety of applications.
- Cost-Effectiveness: Sulfur curing is generally more affordable compared to other methods, making it attractive for mass production.
On the flip side, sulfur-cured rubber may degrade faster under extreme conditions, losing its mechanical properties over time.
Peroxide Curing: This newer approach involves the use of peroxides as curing agents, which leads to a different cross-linking structure. Here are some points to consider:
- Heat Resistance: Peroxide-cured rubber tends to have better thermal stability, making it well-suited for high-temperature applications.
- Enhanced Durability: This process can create rubber that withstands environmental factors like ozone and UV exposure better than its sulfur-cured counterpart.
The right type of vulcanization can define not just the performance efficiencies but also the sustainability quotient of rubber products in diverse industries.
Applications of Vulcanized Rubber
The applications of vulcanized rubber represent a fundamental cornerstone in numerous industries, owing to its unique properties that emerge from the vulcanization process. When rubber is subjected to this thermochemical treatment, it gains enhanced durability, heat resistance, elasticity, and overall lifespan. This makes it an indispensable material in various sectors, each capitalizing on its unique characteristics to meet specific needs. In this section, we will delve into three primary fields where vulcanized rubber is especially crucial: the automotive industry, medical and pharmaceutical sectors, and consumer products.
Automotive Industry
The automotive industry stands as one of the largest consumers of vulcanized rubber. Vehicle manufacturers rely on this material to produce a multitude of components that ensure safety, comfort, and efficiency.
- Tires: Probably the most recognizable use of vulcanized rubber, tires are engineered for maximum performance. From resisting various weather conditions to minimizing road noise, the vulcanization process transforms raw rubber into a robust product capable of handling extreme loads. The intricate tread designs found in tires are not just aesthetic; they are meticulously crafted to enhance grip, fuel economy, and handling stability on different terrains.
- Seals and Gaskets: In a vehicle, preventing leaks is critical. Vulcanized rubber is employed to create seals and gaskets that maintain integrity in various systems including the engine, transmission, and cooling systems. They act as thin barriers to prevent fluid leakage, thereby enhancing operational efficiency and prolonging vehicle life.
- Suspension Parts: Rubber bushings in the suspension system are vital for absorbing shocks and maintaining ride comfort. The elasticity derived from vulcanization ensures that these components can withstand constant movement without losing their shape or efficiency.
This extensive reliance on vulcanized rubber not only enhances vehicle durability but also contributes to sustainability. Durable automotive components reduce the need for frequent replacements, curbing waste and promoting environmental responsibility.
Medical and Pharmaceutical Uses
In the medical realm, the unique properties of vulcanized rubber translate into critical applications that directly impact health and safety. Its ability to resist degradation, along with its hypoallergenic nature, makes it a prime candidate for various medical applications.
- Medical Devices: Devices such as syringes, stoppers for vials, and tubing are often made from vulcanized rubber. The rubber products must maintain sterility and withstand multiple uses while being flexible enough to serve their purpose. Their resilience and adaptability ensure that they can endure various sterilization processes without compromising integrity.
- Prosthetics and Orthotics: Vulcanized rubber is used in the production of prosthetic limbs and orthopedic devices. The material's elasticity and supportiveness provide comfort for users, which is essential for improving their quality of life. The ability of vulcanized rubber to mold effectively ensures a better fit, which is critical for functional prosthetics.
- Biocompatibility: Many formulations of vulcanized rubber can be tailored to meet specific biocompatibility standards. This expands its use in innovative medical applications that require close contact with human tissues, without triggering undesirable reactions.
Through these applications, vulcanized rubber has proven itself as a vital resource that not only contributes significantly to medical technology but also plays a crucial role in advancing healthcare.
Consumer Products
In the realm of consumer goods, vulcanized rubber is pervasive. It is utilized in a variety of products we often take for granted, yet these items significantly enhance our daily lives.
- Footwear: From casual sneakers to high-performance sports shoes, vulcanized rubber is a common ingredient in shoe manufacturing. This rubber provides traction, durability, and comfort, meeting the diverse needs of different wearers. The flexibility and resilience delivered via the vulcanization process ensure that footwear can withstand wear and tear from daily activities.
- Household Items: Many household goods incorporate vulcanized rubber. For instance, kitchen mats, rubber gloves, door mats, and even balloons rely on this material. Its non-slip and water-resistant characteristics make it ideal for such applications.
- Toys: The production of children's toys—including soft balls, bouncy castles, and various other playthings—often uses vulcanized rubber. The material's safety and durability ensure that toys can endure rough handling while being safe for children to use.
The versatility of vulcanized rubber in consumer products highlights the material’s extensive role in everyday life, making it a key player in enhancing both functionality and safety.
In essence, the applications of vulcanized rubber are vast and varied, underscoring its significance across multiple sectors. The evolution of this material, due to continuous research and development, promises to further augment its relevance in both existing and new applications.
Innovations in Vulcanization Technologies
The realm of rubber vulcanization is undergoing a significant transformation, driven by the need for more efficient and sustainable practices. Innovations in vulcanization technologies not only enhance the overall quality of rubber products but also address pressing environmental concerns. It is crucial for students, researchers, and industry professionals to grasp these advancements, as they lay the groundwork for a more sustainable future in rubber manufacturing.
The focus on energy-efficient processing and environmentally friendly approaches has become imperative. These aspects are reshaping how vulcanization is viewed, making the process not just about creating durable products but doing so with minimal impact on our planet.
Energy-Efficient Processing
Harnessing energy efficiency in vulcanization processes is akin to hitting two birds with one stone. The production cost drops significantly while simultaneously reducing the carbon footprint associated with rubber manufacture. New technologies, like microwave heating and infrared radiation, are increasingly being integrated into vulcanization systems. These methods facilitate a more uniform heat application, leading to:
- Reduced Energy Consumption: By optimizing heat distribution, manufacturers are seeing energy savings up to 30% compared to traditional steam processing.
- Shortened Curing Times: Faster processing not only speeds up production cycles but also lowers operational costs. This means products can reach the market quicker, a critical factor in today's fast-paced consumer environment.
- Enhanced Material Properties: Advanced processing techniques can lead to improved end-of-life properties such as tear resistance and elongation at break.
As the industry evolves, embracing energy-efficient practices is not merely a trend; it's becoming a necessity. Manufacturers positioning themselves as leaders in this respect can expect to see better market opportunities and improved customer loyalty.
Environmentally Friendly Approaches
The spotlight is now turning towards environmentally friendly approaches in the vulcanization process. The rubber industry is notorious for its reliance on petroleum-based products and harmful chemicals. As public awareness surrounding ecological impacts rises, companies are keen to explore sustainable alternatives that uphold performance without jeopardizing the environment. Some notable developments include:
- Use of Bio-Based Curing Agents: Shifting to natural additives drawn from plant sources reduces reliance on traditional petrochemical materials. For instance, using soy-based or sugar-derived curing agents is gaining traction.
- Recycled Rubber Content: Integrating recycled rubber not only lessens waste but also reduces the overall material costs. Scrap rubber is processed back into usable materials, exemplifying a circular economy in action.
- Water-Based Processing Techniques: Alternatives to solvent-based processes are becoming popular. These water-based methods minimize volatile organic compounds (VOCs), significantly lowering environmental impact during production.
"Sustainable rubber processing isn't just about reducing, but about innovating to create products that are responsible and durable."
Quality Control and Testing Methods
In the realm of rubber vulcanization, quality control is not just an afterthought; it serves as the backbone for ensuring the integrity and performance of the final product. The rubber industry is subject to rigorous standards due to the diverse applications of vulcanized rubber, from automotive to medical devices. By implementing strict quality control measures and testing methods, manufacturers can identify potential issues early on, thereby preventing costly failures and enhancing product reliability. The spotlight on quality assurance is essential not only for compliance purposes but also for maintaining customer satisfaction and trust.
Mechanical Property Assessments
Mechanical property assessments are fundamental in evaluating the performance characteristics of vulcanized rubber. These assessments focus on various physical properties such as tensile strength, elongation at break, hardness, and resilience. Using standardized tests, for instance, the ASTM D412 for tensile properties, industry professionals can determine how well rubber can withstand stress and deformation during its lifespan. Such tests are critical as they help predict how rubber will behave under specific conditions, ensuring that the material is suitable for its intended application.
A few important metrics examined during mechanical assessments:
- Tensile Strength: Indicates the maximum amount of stress that rubber can withstand while being stretched.
- Elongation at Break: Represents how much a rubber material can be stretched before it breaks, revealing its ductility.
- Hardness: Often measured using the Shore durometer, this property denotes the resistance of rubber to indentation and affects its wear resistance and overall longevity.
Regular mechanical property assessments not only assure quality but also aid in research and development, leading to innovations in rubber formulations.
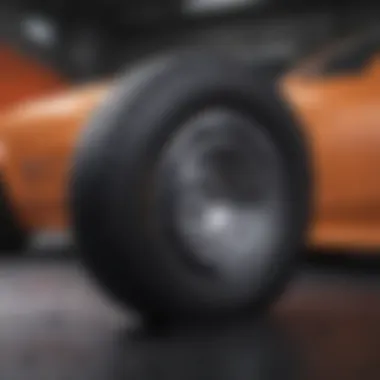
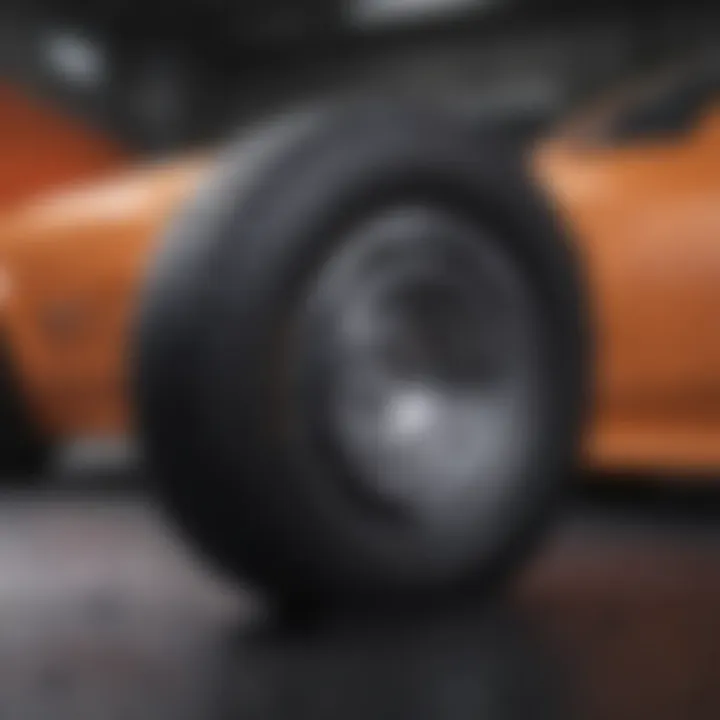
Chemical Resistance Evaluations
The chemical resilience of vulcanized rubber cannot be overstated. As rubber products often face exposure to various chemicals and environmental factors, chemical resistance evaluations play a pivotal role in determining the longevity and safety of these materials. Tests conducted to analyze how rubber reacts to specific chemicals help predict performance in real-world applications.
One common method used for these evaluations is the immersion test, where rubber samples are submerged in specific chemicals for set periods. Afterward, properties such as weight change, tensile strength, and elongation are measured to establish the rubber's resistance to degradation. Factors that are typically assessed include:
- Swelling: The degree to which a rubber material expands when in contact with chemicals.
- Hardness change: A comparison of the hardness before and after exposure, which indicates any softening or hardening due to chemical reactions.
- Loss of mass: A significant drop in mass signals detrimental effects from the exposure.
By ensuring that rubber can endure the stress of its chemical environment, manufacturers can deliver products that are not only durable but also reliable for both industrial and consumer applications.
Testing methodologies and standards are essential for achieving quality in vulcanized rubber, ultimately affecting everything from production efficiency to customer safety.
Challenges in the Rubber Industry
The rubber industry, while undeniably pivotal in various sectors such as automotive, healthcare, and consumer goods, faces a myriad of challenges that could impact its growth and sustainability. One of the most pressing issues is material degradation, which poses significant threats to the quality and longevity of rubber products. Furthermore, the complexity of global supply chains adds another layer of difficulty that manufacturers must navigate.
Material Degradation
Material degradation in rubber is a multifaceted issue that can arise due to several environmental and physical factors. Over time, exposure to sunlight, heat, ozone, and chemical agents can lead to a breakdown of the rubber's molecular structure. Such degradation often results in a loss of elasticity and strength, rendering the rubber unusable for its intended applications.
For instance, tires exposed to prolonged UV light can develop cracks that compromise their integrity. Similarly, in the medical sector, rubber components in devices like syringes or gloves can become brittle, posing severe risks during medical procedures. This highlights not only the importance of selecting appropriate materials for specific environments but also the need for ongoing research into more resilient compounds.
- Preventive measures: To counteract degradation, industry players often employ protective additives, which absorb harmful rays or enhance the material's resistance to wear and tear.
- Innovative materials: Recent developments have led to the exploration of alternative materials that can offer better stability under harsh conditions.
Supply Chain Issues
The rubber industry is also grappling with complex supply chain challenges that can disrupt production and increase costs. From sourcing raw materials like natural rubber from rubber trees to obtaining synthetic compounds, the entire process can be fraught with uncertainties. Global events, such as political instability in rubber-producing regions or natural disasters affecting plantations, can lead to sudden supply shortages.
Moreover, logistics play a crucial role in the rubber supply chain. Transporting raw materials across long distances can be inefficient and expensive. This often results in extended lead times, adversely affecting manufacturing schedules and, ultimately, market supply.
"The complexities of the rubber supply chain require manufacturers to be adaptable and forward-thinking to mitigate risks and ensure consistent quality."
To address these challenges, companies are increasingly looking to strengthen relationships with local suppliers and invest in technology that enhances supply chain transparency. Additionally, increasing stockpiles during favorable conditions can help buffer against unforeseen disruptions.
In summary, navigating the challenges of material degradation and supply chain issues in the rubber industry is critical for maintaining product quality and ensuring a reliable supply of goods to meet market demand. Continuous improvement and innovation are essential in establishing a resilient future for this crucial industry.
Future Directions in Vulcanization Research
The realm of rubber vulcanization is evolving rapidly, drawing attention towards innovative approaches that recalibrate how we perceive and utilize rubber materials. Researching future directions in vulcanization is not just an academic exercise; it holds immense potential for reshaping industries and addressing environmental challenges. As we navigate into this future, two significant avenues warrant our attention: biodegradable rubber materials and advanced computational modeling.
Biodegradable Rubber Materials
Biodegradable rubber materials provide a breakthrough in the quest for sustainability in the rubber industry. Traditional rubber products, while durable, can take decades to decompose, resulting in significant environmental burden. As awareness grows about the imperative of sustainable products, scientists and engineers are now investigating ways to create rubber that breaks down naturally without leaving harmful residues behind.
- Advantages of Biodegradable Rubber
- Environmental Impact: By using natural or less harmful materials, we can significantly reduce landfill contributions.
- Public Demand: Consumers are increasingly leaning towards eco-friendly products, making this avenue commercially viable.
- Innovation in Raw Materials: Exploring the use of natural fibers and biopolymers opens up new possibilities for product design.
Research focuses on specific techniques such as blending traditional synthetic rubbers with new biopolymers. These materials are engineered to maintain necessary performance standards while strategically introducing characteristics that facilitate their decomposition. Good examples are the development of polylactic acid (PLA) incorporated in rubber formulations, enhancing degradability.
"Innovation isn't just about new ideas; it's about rethinking what we already know and transforming it into something sustainable."
Advanced Computational Modeling
Advanced computational modeling stands as another beacon in vulcanization research, providing powerful tools to predict and simulate the behavior of rubber compounds before physical experimentation. This approach can drive down costs and accelerate development timelines, pushing the industry toward groundbreaking advancements.
- Key Features of Computational Modeling:
- Simulation Capabilities: Ability to predict how different formulations behave under various curing conditions.
- Material Optimization: Offers a controlled avenue to test and refine compositional mixtures efficiently.
- Data Handling: Large datasets from previous experiments can be utilized to enhance accuracy in new simulations.
Using advanced algorithms and machine learning, researchers can analyze complex interactions within rubber compounds, shedding light on optimal vulcanization parameters. Imagine a lab where physical experiments are minimized – the resultant data from computational analyses can forge pathways to better materials faster and more cost-effectively.
In summary, the future of vulcanization research appears promising, intertwining sustainability with cutting-edge technology. By embracing these future directions, we can not only cater to the industry's needs but also contribute positively to our environment, paving the way for a greener future in rubber manufacturing. We must remain curious and invested in these innovations if we are to harness their potential fully.
Culmination: The Impacts of Vulcanization on Society
Rubber vulcanization has profound implications for both industry and society at large. By enhancing the durability, elasticity, and heat resistance of rubber, vulcanization lays the groundwork for numerous applications, ranging from tires to medical devices. With the transformations it brings to raw rubber, vulcanization not only improves material performance but also paves the way for safer and more reliable products in everyday life.
Summary of Key Insights
At its core, the vulcanization process epitomizes the blend of chemistry and practicality. It ensures that materials used in critical sectors exhibit superior properties. Here’s a quick rundown of the key benefits and insights regarding vulcanization:
- Enhanced Durability: Vulcanized rubber withstands wear and tear, leading to longer-lasting products.
- Improved Safety: The applications in tires and other automotive components directly correlate to safer transport.
- Versatility: From industrial machinery to household products, vulcanized rubber plays a critical role in diverse sectors.
"The power of vulcanization lies not just in its chemical processes but in the lives it touches and the standards it sets."
By understanding these insights, both professionals and students in the field can appreciate how vulcanization integrates into broader technological advancements.
The Importance of Continued Research
While vulcanization has evolved significantly since its inception, the need for ongoing research remains vital. Here are some reasons why:
- Sustainability: With environmental concerns on the rise, research into sustainable materials and methods for vulcanization becomes crucial. Biodegradable and eco-friendly options can help reduce the rubber industry's carbon footprint.
- Innovation: Advances in computational modeling allow scientists to better predict the outcomes of different vulcanization methods, leading to finely-tuned processes that enhance product quality and performance.
- Market Demand: As industries evolve, so do their demands. Ongoing research ensures that new applications and material requirements are met efficiently.
In summary, understanding and investing in the future of rubber vulcanization can yield societal benefits while addressing pressing environmental and technological challenges. As the industry adapts to changing demands, continued research is indispensable to achieve progress.