The Role of Cobalt in Advancing 3D Printing
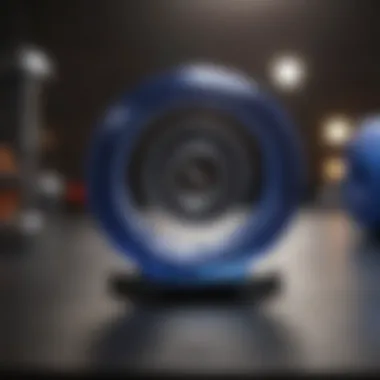
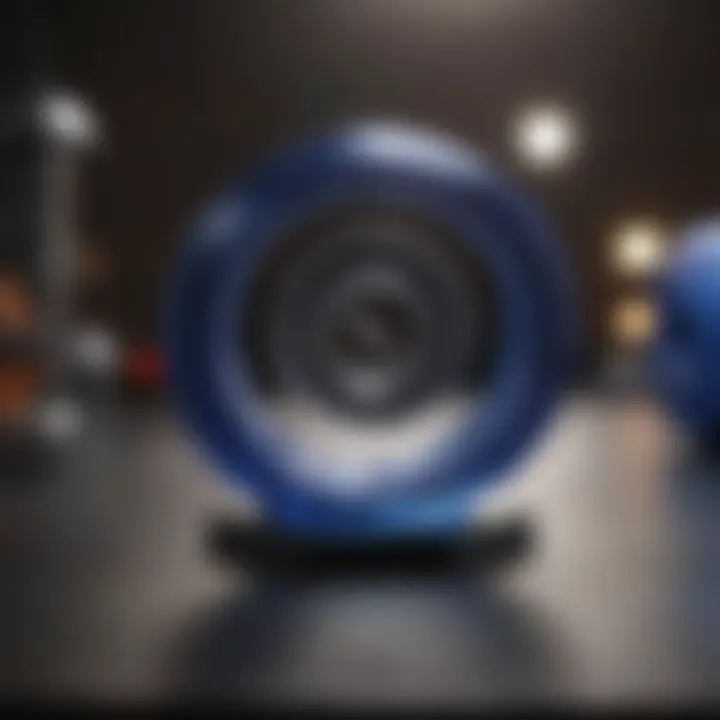
Intro
In recent years, 3D printing technology has gained significant traction in various industries, reshaping how products are designed and manufactured. Among the materials that have catalyzed this shift, cobalt stands out due to its unique properties and versatile applications. Cobalt is not just a shiny metal; it has unique characteristics that make it an essential player in the realm of additive manufacturing. Its incorporation into different alloys affords enhancements in mechanical strength, thermal resilience, and corrosion resistance. As we navigate through this topic, we'll delve into how cobalt is influencing the world of 3D printing, the advances in technology that allow for its utilization, and what the future might hold.
Key Findings
Summary of the Main Results
Cobalt's role in 3D printing is manifold. Through its use in various alloys, it enhances overall material performance, contributes to better structural integrity, and promotes better heat resistance. Many studies indicate that when cobalt is included in a metal alloy for additive manufacturing, it can improve the fatigue life of parts, making them more reliable under stress. Moreover, cobalt's magnetic properties open up avenues for applications in electronics and medical devices.
Significance of Findings Within the Scientific Community
The findings regarding cobalt's role are not just academic; they carry weight in practical applications across industries such as aerospace, automotive, and even medical technology. Scientists and engineers are particularly interested in how cobalt-based alloys can lead to ground-breaking advancements in various fields. The ability to manipulate cobalt’s properties to attain desired characteristics could lead to innovative solutions in enhancing product lifespan and performance.
"Cobalt is the unsung hero of 3D printing, quietly bolstering material properties and expanding the horizons of what's possible in manufacturing."
Implications of the Research
Applications of Findings in Real-World Scenarios
From the aerospace sector, where materials need to withstand extreme conditions, to the medical field where precision and reliability are imperative, cobalt's attributes are invaluable. For instance, the use of cobalt-chromium alloys in prosthetics is revolutionizing how implants are developed, providing durability and biocompatibility.
The automotive industry is also leveraging cobalt-infused materials to develop more robust parts, aiming for vehicles that last longer and perform better under varying conditions. These real-world applications highlight the versatility and emerging significance of cobalt in modern manufacturing.
Potential Impact on Future Research Directions
As researchers continue to explore the characteristics of cobalt in alloys, there is no telling how this might influence future innovations in 3D printing technology. New studies could lead to better understanding and perhaps the development of even more efficient materials. Given cobalt's unique properties, the potential to discover new applications and techniques is vast. This research may not only advance the science behind materials but also usher in a new wave of manufacturing possibilities that were not previously imaginable.
In summary, the role of cobalt in 3D printing technology is crucial. Its robust properties, extensive applications, and potential for future advancements make it a focal point for ongoing research and development. As we continue to uncover its capabilities, the dialogue surrounding environmental considerations and market trends will also be essential in shaping how cobalt is used sustainably.
Preface to Cobalt in 3D Printing
In recent years, the landscape of manufacturing has dramatically shifted with the rapid advancement of 3D printing technologies. What’s crucial to understand here is that cobalt plays a significant role in this transformation, especially within the realm of additive manufacturing. Cobalt’s unique characteristics elevate its standing as a material of choice for engineers and researchers alike, prompting a deeper investigation into its applications and benefits.
Cobalt isn’t just any metal; it exhibits remarkable strength, corrosion resistance, and excellent thermal stability. These properties make it a perfect candidate for high-performance parts, particularly in industries where durability and precision are non-negotiable. When we talk about 3D printing, these characteristics become even more pertinent, as the technology demands materials that can perform exceptionally under various conditions.
Another important consideration is the ability of cobalt to enhance the properties of alloys. When combined with metals like chromium and nickel, cobalt can create superalloys that withstand extreme heat and stress. This melting pot of characteristics opens doors to innovative applications across diverse sectors, from aerospace to medical devices.
Moreover, the adaptability of cobalt in different printing processes—from powder bed fusion to binder jetting—highlights its versatility. This adaptability is crucial in today's fast-paced tech landscape where materials need to keep up with evolving demands.
Additionally, as industries focus on sustainability and ethical sourcing, there is an increasing scrutiny on cobalt extraction. It is essential to also consider these factors in our exploration of cobalt’s role in 3D printing. The intricacies of sourcing and using cobalt responsibly underscore the complexity of integrating this material into production processes.
In essence, this section serves as a launching pad for a comprehensive analysis of cobalt's contributions to 3D printing technology. By diving deeper into its properties, interplay with various alloys, and its importance in different manufacturing methods, we aim to provide valuable insights that resonate with professionals and researchers alike.
Understanding cobalt's role is foundational to grasping the broader implications it has within the rapidly evolving field of additive manufacturing.
Properties of Cobalt
Cobalt possesses distinct properties that make it a vital component in the realm of 3D printing. Its unique characteristics lend themselves well to various applications, particularly in advanced manufacturing processes where precision and durability are paramount. Understanding cobalt’s properties is crucial, as these features directly influence its performance in additive manufacturing technologies. The effectiveness of cobalt ultimately hinges on how well these properties are leveraged in the development of new alloys and materials.
Physical Properties
When we talk about cobalt, it’s hard not to mention its physical properties, which are pretty remarkable. For starters, cobalt boasts a relatively high melting point of around 1,495 °C (2,723 °F). This high thermal resistance is a huge plus in 3D printing, where the material needs to withstand significant heat during the processing phase.
Cobalt presents good toughness, which is particularly valuable when manufacturing parts that require a higher level of durability, like those used in aerospace and medical devices. Its shining, metallic appearance is not just an aesthetic quality; this hardness also translates to wear resistance, making cobalt an excellent choice for functional parts that experience heavy use.
Another noteworthy aspect is cobalt’s density. It sits comfortably between aluminum and iron, providing a balanced weight-to-strength ratio. This property allows for the creation of parts that are not overly heavy yet maintain structural integrity in demanding conditions. Because many of these parts are designed for applications in spaces where every gram counts, cobalt’s density plays a critical role in the design phase.
Chemical Properties

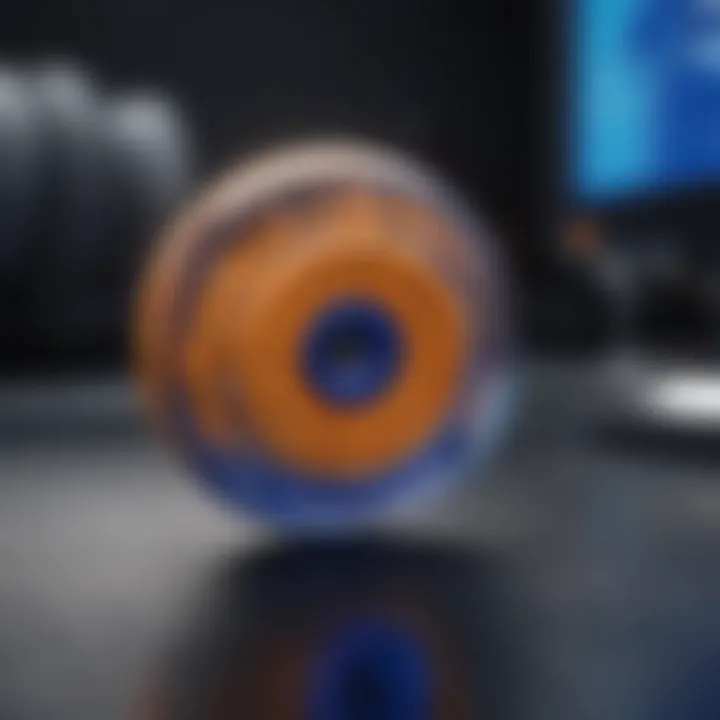
On the chemical front, cobalt is quite intriguing. One of its standout features is that it’s relatively inert, meaning it doesn't react with oxygen at room temperature. This stability makes cobalt a favored choice for applications where oxidation and degradation could present problems over time.
Cobalt readily reacts with nonmetals like sulfur and phosphorus, creating compounds that can enhance its properties when alloyed with other metals. For instance, cobalt can be combined with nickel to produce superalloys that shine in high-temperature environments. These superalloys have applications ranging from turbo engines to components in space vehicles, emphasizing cobalt's importance in high-performance contexts.
Furthermore, cobalt can exhibit a variety of oxidation states, typically +2 and +3, enabling its functionality in diverse chemical environments. Cobalt’s ability to form complex compounds not only enriches its utility but allows it to play a critical role in electrochemical processes, hence its application in batteries as well.
"Cobalt serves as a bridge, connecting diverse applications through its unique physical and chemical properties, enabling innovation in 3D printing and beyond."
In summary, cobalt’s properties—both physical and chemical—provide a sturdy foundation for its utilization in 3D printing technology. From its high melting point and toughness to its resistance to oxidation and versatility in forming alloys, cobalt is a powerhouse of characteristics that advance manufacturing and technological innovation. Understanding these properties allows researchers and industry practitioners to harness cobalt effectively in the pursuit of creating cutting-edge 3D-printed materials.
The Role of Cobalt in Alloy Formulations
The integration of cobalt into alloy formulations is a cornerstone of modern metallurgy, especially in the realm of 3D printing. This is not just about mixing metals; it’s about elevating their properties to meet specific demands across industries. Cobalt's role in alloying brings forth a suite of advantages, impacting everything from durability to thermal stability.
Cobalt-based Alloys
Cobalt-based alloys are known for their exceptional wear resistance and ability to maintain strength at high temperatures. These alloys often find their place in demanding environments, such as aerospace and medical sectors. For instance, cobalt-chromium alloys have been particularly beneficial in producing high-performance implants due to their excellent biocompatibility and corrosion resistance. The strength of cobalt allows for the production of lighter components without compromising integrity, which is vital in fields where every gram matters.
Furthermore, alloys like Inconel and Stellite, which incorporate cobalt, have become staples in various manufacturing processes. The utility of cobalt-based alloys extends beyond just strength; they can also enhance electrical and thermal conductivity, making them suitable for electronic devices and cutting-edge applications in additive manufacturing.
Performance Characteristics
Cobalt's unique properties in alloy formulations result in performance characteristics that are hard to overlook. When cobalt is alloyed with other metals, it imparts:
- High Hardness: This makes cobalt-based alloys ideally suited for wear-resistant applications. They excel in conditions where other materials might falter under stress.
- Thermal Stability: Cobalt-containing alloys maintain structural integrity at elevated temperatures, which is critical in applications like turbine engines.
- Corrosion Resistance: The addition of cobalt enhances resistance to oxidative and corrosive environments, making these alloys long-lasting.
Such characteristics mean that components made from cobalt-based alloys can withstand harsh conditions for extended periods, reducing maintenance costs and increasing operational efficiency. For sectors like marine and oil exploration, where reliability is paramount, this becomes a significant advantage.
Cobalt plays a critical role not just in enhancing material properties, but also in driving innovation in manufacturing technologies, paving the way for next-gen applications.
As we move closer to fully realized additive manufacturing capabilities, the relevance of cobalt in alloy formulations stands to grow. By continuously evolving these alloys, researchers and engineers can meet the increasingly complex demands of modern technology, ensuring that cobalt remains a key player in the landscape of 3D printing.
Cobalt and Additive Manufacturing Processes
Cobalt plays a crucial role in the landscape of additive manufacturing, particularly due to its versatile properties that enhance the performance of various materials. The significance of cobalt in processes like powdered metals and binders cannot be overstated. It not only improves the strength and durability of 3D printed items but also opens doors for innovative applications across industries such as aerospace, medical, and automotive. Understanding the methods of embedding cobalt within additive manufacturing is paramount for researchers and practitioners in the field.
Powder Bed Fusion Techniques
One of the most notable processes that integrates cobalt is the powder bed fusion technique. This method involves using a laser to selectively melt a powder bed, which can include cobalt-based powders. The temperature and precision of the laser allow for fine control over the structure and properties of the final product.
This approach benefits from cobalt’s high melting point and excellent load-bearing capabilities, making it suitable for applications where strength and reliability are non-negotiable. Moreover, cobalt-rich alloys provide improved oxidation resistance, which is critical in environments exposed to high temperatures or corrosive substances. The ability to manipulate cobalt's properties during the additive process further enhances material performance characteristics, leading to innovations in design and functionality.
Benefits of Powder Bed Fusion with Cobalt
- Strength and Durability: Parts printed with cobalt alloys tend to be more robust, which is vital in critical applications, like in aerospace components.
- Reducing Material Waste: Powder bed fusion generates less waste compared to traditional machining, a significant factor in optimizing material usage.
- Enhanced Surface Finish: Utilizing cobalt can lead to superior surface finishes, which can be important for aesthetic as well as functional reasons.
Binder Jetting Methods
Binder jetting offers another avenue for incorporating cobalt into additive manufacturing. This technique employs a binding agent to join cobalt particles into a solid object. While more traditional forms of forming may impede the use of cobalt due to its specific material properties, binder jetting thrives on adaptability.
In this process, cobalt powder is deposited layer by layer, and an adhesive binds the individual particles together. After printing, the piece is typically cured in a sintering step, which helps to detoxify the binder and improve the structure's integrity. This makes binder jetting especially appealing for producing large items with complex geometries that would be difficult or impossible to achieve using other methods.
Considerations in Binder Jetting with Cobalt
- Cost Efficiency: Compared to traditional casts or molds, binder jetting can reduce costs significantly, especially for low-volume production runs.
- Customizable Properties: Tailoring the amount and type of binder used can impact the final material properties – a critical advantage for specialized applications.
- Environmentally Friendly: The binder jetting process generally leads to less energy consumption as it operates at lower temperatures than methods like laser sintering.
Cobalt's unique characteristics allow manufacturers to innovate beyond traditional limits, ensuring that the future of 3D printing embraces strength with versatility.
Applications of Cobalt in Various Industries
Cobalt is not just a fascinating metal; it is a cornerstone in various sectors of industry, and understanding its applications is vital to appreciating its role in 3D printing technology. Its characteristics, such as high melting point and excellent resistance to oxidation, make it particularly useful in demanding environments. In this section, we explore how cobalt is applied across different fields, examining the unique benefits it brings to each.
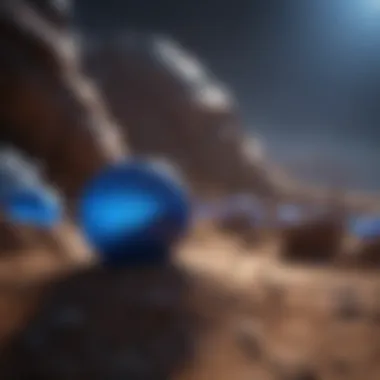
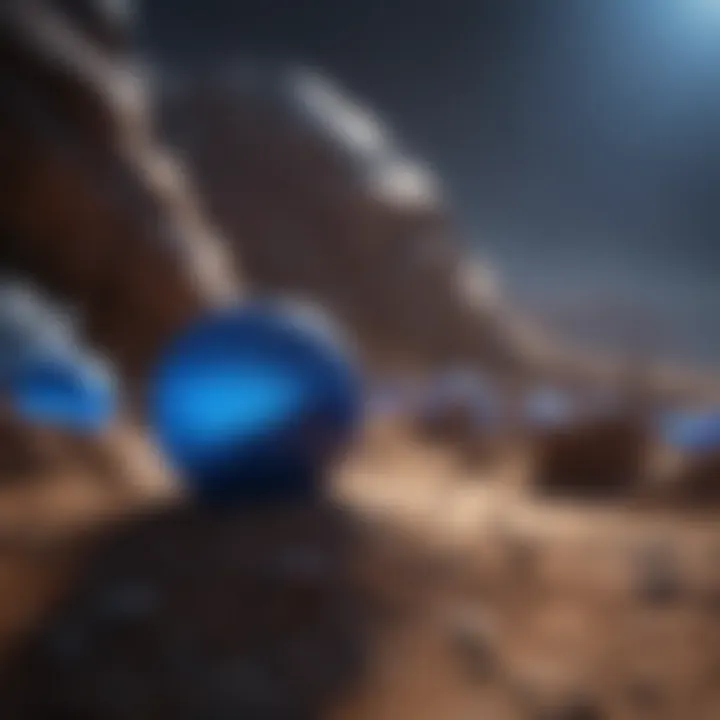
Aerospace Sector
In aerospace manufacturing, the performance and reliability of materials are paramount. Components must withstand extreme temperatures and pressures while maintaining structural integrity. Cobalt plays a significant role here, particularly in superalloys that are often employed in turbine engines.
- Heat Resistance: Cobalt-based alloys can endure high thermal stresses, making them suitable for engine components that operate at high temperatures.
- Durability: These alloys exhibit excellent wear resistance, essential for reducing friction and prolonging the life of engine parts.
- Impact Strength: Cobalt contributes to high impact strength, which is crucial during rapid changes in pressure and temperature conditions encountered in flight.
"In the aerospace industry, the said metals like cobalt are not just materials; they are the backbone of reliability in flight."
Medical Devices
The medical field demands great precision and safety, especially when it comes to implants and devices that interact directly with the human body. Cobalt’s biocompatibility makes it a suitable candidate for several medical applications, especially in orthodontics and prosthetic devices.
- Stainless Steel Alloys: Cobalt is often included in stainless steel alloys used in surgical instruments and implants, providing necessary strength and corrosion resistance.
- Magnetic Resonance Imaging (MRI): Certain cobalt compounds are essential in the production of MRI components, enhancing imaging clarity and resolution.
- Orthopedic Applications: Cobalt-chromium alloys are frequently utilized in joint replacements, offering both durability and a lower rejection rate by the body compared to other materials.
Automotive Innovations
In the automotive sector, the pursuit of innovation often leads to the adoption of advanced materials that improve performance, safety, and efficiency. Cobalt contributes to this drive, especially in the context of batteries and specialty coatings.
- Batteries: Cobalt is a critical component in lithium-ion batteries, enhancing the energy density and lifespan of electric vehicles. Given the rise of electric vehicles, cobalt’s role in this context is becoming increasingly crucial.
- High-Performance Coatings: Cobalt-based coatings are applied to engine parts to improve wear resistance and corrosion protection, ultimately extending the service life of components.
- Lightweight Structures: Cobalt’s strength-to-weight ratio aids in the development of lightweight automotive structures that improve fuel efficiency and performance.
In closing, cobalt's applications across these different sectors highlight its versatility and importance in modern manufacturing and technology. As industries evolve, the material will undoubtedly continue to adapt, playing an ever more significant role in the future of 3D printing and beyond.
Challenges in Using Cobalt for 3D Printing
When diving into the intricate realm of 3D printing, the role of materials cannot be understated. Cobalt, despite its unique properties and applications, brings along a few challenges that are worth discussing. In the case of this technology, the hurdles surrounding cobalt largely revolve around its costs and supply chain issues, which can significantly influence both the feasibility and sustainability of its usage in various settings. This section primarily tackles these elements, providing insights that are essential for professionals and researchers in the field.
Material Costs
The cost of cobalt is a considerable factor in its widespread application within 3D printing. Market fluctuations and geopolitical concerns often lead to unpredictable pricing, making it crucial for manufacturers to establish reliable budgeting strategies. In recent years, cobalt prices have seen a rollercoaster of fluctuations, driven largely by high demand from various industries, notably the electronics and automotive sectors.
Here are some key points regarding material costs for cobalt in 3D printing:
- Raw Material Pricing: Due to its reputation for strength and resistance to high temperatures, cobalt can be more expensive than other common metals like aluminum or steel. This higher cost presents a barrier, particularly for startups or smaller manufacturers who may not afford high-risk investments.
- Processing Expenses: Bringing cobalt into 3D printing involves additional processing, which can further inflate the overall costs. Factors such as powder production techniques and the need for specialized equipment for fusion processes can add to the initial material costs.
- Vendor Pricing Disparities: Differences in vendor pricing can complicate procurement. Some suppliers may charge premium rates for cobalt powders perceived as higher quality, creating a dilemma for purchasers on whether to sacrifice quality for cost-efficiency or vice versa.
In dealing with these costs, companies may explore alternative alloys or substitutes, but this requires careful evaluation. Striking a balance between performance and proficiency without compromising product quality is vital.
Supply Chain Concerns
Supply chain issues are the other side of the coin when considering cobalt for 3D printing applications. The sourcing of cobalt largely depends on geopolitical stability in the regions where it is mined, primarily in the Democratic Republic of the Congo. Here are notable aspects surrounding supply chain concerns:
- Geopolitical Factors: With cobalt being predominantly mined in specific areas, any political instability in these regions can lead to dramatic supply shortages. Such disruptions can halt production or drive prices up even further, impacting overall manufacturing timelines.
- Ethical Sourcing: There has been growing concern over the ethical implications of cobalt mining, including labor practices and environmental effects. Companies face pressure from consumers and watchdog organizations to ensure that their supply chains are ethical and sustainable. Some manufacturers may need to invest considerably in certifications or audits to prove the integrity of their cobalt sources.
- Logistical Challenges: Getting cobalt from the mines to manufacturing facilities often involves complex logistics. From shipping to customs clearance, every step in the movement of materials can introduce delays or additional costs. A smooth supply chain fosters timely delivery, which is essential in maintaining production schedules in 3D printing.
"The future of cobalt in 3D printing hinges on its competitiveness, not just in material costs but also in sustainability and ethical procurement."
Environmental and Ethical Considerations
As we navigate through the growing landscape of 3D printing technology, the implications of using cobalt cannot be overlooked. While its unique properties offer numerous advantages in improving material performance, we must address environmental and ethical challenges that come hand-in-hand with its utilization. Companies and researchers are increasingly pressed to evaluate the long-term effects of cobalt extraction and production, making these considerations pivotal in modern additive manufacturing discussions.
Sustainability of Cobalt Extraction
Cobalt is primarily mined for its vital use in batteries, but when we look specifically at 3D printing, the sustainability of its extraction raises significant concerns. The majority of cobalt comes from the Democratic Republic of the Congo, a nation riddled with issues, including environmental degradation and labor practices that can be less than savory. The mining processes often lead to habitat destruction and water pollution, which can have dire consequences on local ecosystems.
- Environmental Impact: Harvesting cobalt not only disrupts the land but also requires substantial energy, contributing to carbon emissions.
- Resource Scarcity: As demands for cobalt rise due to its applications, there’s growing fear that extracting methods will unsustainably deplete resources over time.
- Recycling and Recovery: Some companies explore avenues for recycling cobalt-based materials, which alleviates some pressure from primary extraction. Implementing recycling processes into production can enhance the sustainability factor greatly.
Corporate Responsibility
With the increasing scrutiny on equitable practices, corporations stand at a crossroads in maintaining their reputations while sourcing cobalt responsibly. Many organizations now strive to align with ethical sourcing policies that promote transparency and environmental stewardship.
"A responsible approach believes that success is predicated not only on profit but also on the well-being of the planet and its people."
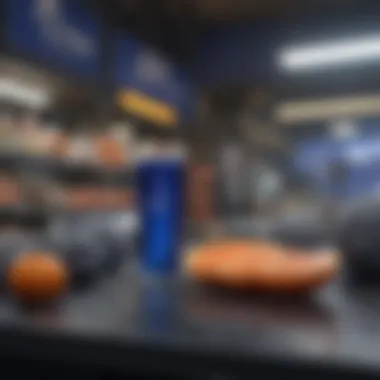
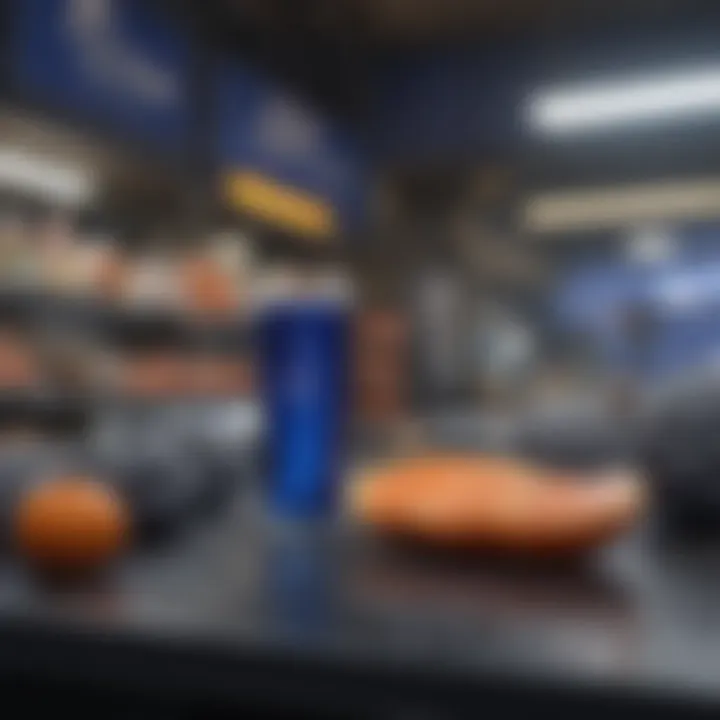
- Transparency in Supply Chains: Companies must focus on being forthright about where and how they source cobalt. Higher standards of disclosure can mitigate concerns about unethical mining practices.
- Certifications: Some firms are pursuing certifications that verify cobalt comes from ethical sources. This assurance is crucial for attracting consumers who question the integrity of products they use.
- Investment in Communities: Engaging with local communities and providing support through education and improved living conditions can foster goodwill, and showcase a commitment beyond profit margins.
By embracing these environmental and ethical considerations, the hope is to not only enhance the position of cobalt within the 3D printing industry but to do so responsibly and sustainably. This balance is essential to ensure that such advancements do not come at a price to the planet or its inhabitants, shaping a future where innovation coexists with ethical imperatives.
Future Directions for Cobalt in 3D Printing
Considering the significant role cobalt plays in 3D printing technologies, it’s essential to explore its future directions. As industries increasingly rely on additive manufacturing, understanding cobalt's evolving application can shed light on innovation pathways.
The exploration of cobalt's potential is not just a theoretical exercise; it has tangible benefits. For instance, enhancing material properties like strength and durability through cobalt-based alloys can lead to advancements in sectors such as aerospace and medical technology.
Innovative Research Areas
As we look ahead, several promising research areas will likely shape cobalt’s future in additive manufacturing:
- New Alloys and Composites: Researchers are examining cobalt's compatibility with other metals to create novel alloys. This can lead to better performance outputs in high-stress environments, like those encountered in aerospace applications.
- Surface Modification Techniques: There’s growing interest in using cobalt coatings to improve resistance to wear and corrosion. These surfaces can significantly extend the lifespan of 3D printed components, making them more viable for real-world applications.
- Cobalt Recycling Technologies: Sustainability concerns are driving research into efficient recycling methods for cobalt. Developing techniques to reclaim cobalt from used materials can alleviate supply chain issues while minimizing environmental impact.
Innovation in these areas not only enhances the material properties but also aligns with industry demands for more sustainable practices.
Market Trends and Predictions
Looking at the market trends, several predictions emerge regarding cobalt's involvement in 3D printing:
- Increased Demand Across Sectors: The automotive and aerospace industries are expected to witness a surge in the demand for cobalt-based materials due to their superior performance characteristics.
- Price Volatility: As economies look to enhance production efficiency, cobalt prices may fluctuate. Monitoring these trends will be crucial for manufacturers aiming to plan their resource allocation effectively.
- Emerging Markets: Regions such as Asia and Africa are anticipated to become significant players in cobalt production, thus influencing global market dynamics.
"The role of cobalt in 3D printing is set to evolve, with research and market forces playing pivotal roles in shaping its future."
In this context, a thorough understanding of these trends can empower professionals and students alike to anticipate market needs, driving innovation in 3D printing technologies.
The End
The examination of cobalt within the realm of 3D printing cannot be overstated. Recognizing its pivotal role in this technology provides immense insight for those actively engaged in the fields of engineering, manufacturing, and materials sciences. Cobalt is not merely another metal; it's a cornerstone for creating materials that can withstand extreme environments, particularly in industries such as aerospace and medical devices.
One significant element discussed in this article is the adaptability of cobalt-based alloys. They exhibit remarkable strength and durability, which allows them to excel in tackling the demands of modern applications. For instance, in aerospace, the lightweight yet resilient nature of cobalt alloys contributes to advancements in fuel efficiency and safety, marking substantial progress in an industry that thrives on innovation. This versatility extends to the burgeoning medical sector where cobalt is utilized in implants and surgical instruments — demonstrating its biocompatibility and durability in crucial applications.
Moreover, the discussion surrounding environmental and ethical considerations further enriches our understanding of cobalt's role in 3D printing. As industries continue to focus on sustainability, it becomes imperative to navigate the challenges associated with cobalt extraction and its broader impact on the environment. Acknowledging corporate responsibility within this sphere underscores the importance of ethical sourcing, a notion that resonates with consumers and industry leaders alike.
In light of future directions for cobalt in this technology, it is clear that we stand on the brink of innovations that could redefine how we perceive and utilize materials. The ongoing research into new alloy formulations, coupled with market trends that reflect a shift towards responsible production, indicates a promising horizon.
"Cobalt's integration into 3D printing technology not only enhances performance but also calls upon industries to act ethically and sustainably."
In summary, the conclusion encapsulates the importance of cobalt in additive manufacturing. The benefits and considerations explored highlight that cobalt isn't merely a choice of material; it's a strategic partner in the quest for stronger, safer, and more efficient technologies. As we move forward, the insights gathered here will undoubtedly assist students, researchers, and professionals to navigate the complexities and potentials of cobalt in their respective pursuits.
References and Further Reading
When venturing into the subject of cobalt's application in 3D printing, having robust references and further reading material is invaluable. This is not just about throwing together a list of sources; it's a crucial element that enriches understanding and insight for those diving deep into the topic.
Importance of References
The inclusion of references serves multiple purposes:
- Credibility: A well-cited piece showcases the depth and authenticity of research, letting readers know that the information is rooted in established studies and expert opinions. This is vital for students and professionals alike, who depend on accurate data to make informed decisions in their fields.
- Comprehensive Understanding: 3D printing is a multifaceted field, and cobalt's role spans various industries. Reference materials provide context, expand upon topics introduced, and introduce readers to new concepts and technologies that relate to cobalt and its properties. This holistic view can drive innovation and foster a richer understanding.
- Continued Learning: For researchers and educators, references are gateways to further study. They can lead to discovering new methods, innovative applications, and emerging research trends related to cobalt in additive manufacturing. One small reference can often open up an expansive web of knowledge.
Suggested Readings
To assist those interested in digging deeper, here are a few recommended sources:
- Wikipedia: A great starting point for an overview. It provides basic facts and essential concepts about cobalt's properties and its integration into 3D printing. Visit Wikipedia for a broader understanding.
- Encyclopedia Britannica: Known for its thorough articles, this platform covers historical and modern perspectives on cobalt, illustrating its significance in various fields. Accessible at Britannica.
- Reddit: For contemporary discussions and community insights, Reddit is an invaluable resource. Engaging directly with experts and enthusiasts can spark new ideas and understanding. Check out relevant subreddits for ongoing conversations about 3D printing and cobalt applications at Reddit.
- Facebook Groups: Some niche Facebook groups focus on 3D printing technology and materials. These can be great for networking, sharing experiences, and learning about the latest advancements directly from practitioners in the field.
"The best tool you can have is knowledge—equipping yourself with information is the first step to mastering any technology."
Culmination
In summary, references and further reading are not just appendices; they are integral to the development of both knowledge and expertise. By utilizing these resources, individuals can clarify concepts, support their research, and remain agile in a rapidly changing technological landscape. Good scholarship doesn't just stop at understanding a topic; it seeks to expand upon and evolve the discourse.
Engagement with high-quality references ultimately elevates the caliber of any research. With cobalt's innovative role in 3D printing, comprehending this subject thoroughly is essential for realizing its potential.
As the landscape of additive manufacturing continues to shift, staying informed through credible sources ensures that one's footing in this intricate field remains grounded.