Photolithography Steppers: Innovations & Applications
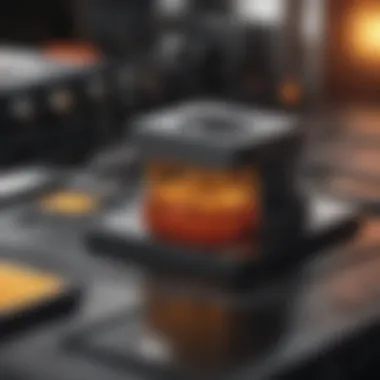
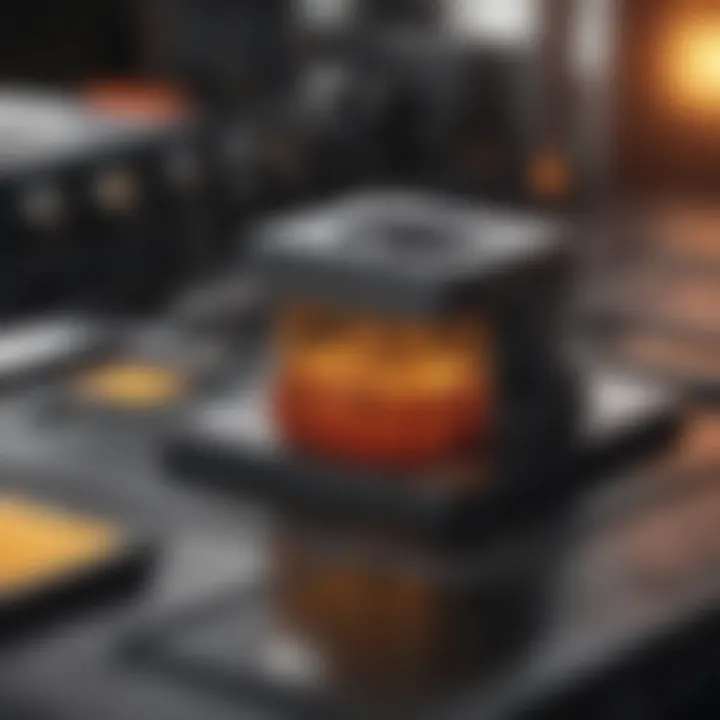
Intro
Photolithography is foundational in the semiconductor industry, and specifically, photolithography steppers play a pivotal role in this process. These machines are integral to the manufacturing of microchips, enabling precise patterning on silicon wafers. As such, understanding their principles, innovations, and applications offers insights into the evolution of electronic devices.
Photolithography steppers utilize light to transfer geometric patterns from a photomask to a substrate. The operational complexity behind these devices is impressive, intertwined with many innovations that have emerged over the years. A focus on the mechanisms of light projection, the advancements in resolution capabilities, and the implications of technologies like extreme ultraviolet lithography reveals the dynamism within this field.
In modern semiconductor fabrication, these steppers not only enhance production efficiency but also improve the processing capabilities of various electronic components. As electronic devices become increasingly sophisticated, understanding the advancements in photolithography steppers can help illuminate the future of manufacturing and technology as a whole.
With this framework in mind, we will delve into the key findings that reveal the significance of photolithography steppers in today's technological landscape.
Prolusion to Photolithography
Photolithography is a foundational technology critical to the manufacturing of semiconductor devices. As the demand for smaller, faster, and more efficient electronics increases, understanding the principles of photolithography becomes essential. This section provides insights into its definition, context, and historical development, giving the reader a solid foundation for more advanced topics discussed later in the article.
Definition and Context
Photolithography refers to a process used to transfer geometric patterns onto a substrate, primarily in semiconductor fabrication. This technique involves applying a photosensitive material, known as photoresist, onto the surface of a wafer. When exposed to light, the photoresist undergoes a chemical change, allowing specific areas to be either etched away or retained based on a designed pattern. The end result shapes the microscopic features that make up integrated circuits. This process is vital because it determines device performance and yields in semiconductor manufacturing, directly impacting electronic devices we rely on every day.
In today's world, photolithography is not only essential for chip fabrication but also for various applications like microelectromechanical systems (MEMS) and optoelectronics. As traditional optical lithography faces challenges from resolution limits, innovative developments like extreme ultraviolet lithography are emerging, expanding its applicability and relevance.
Historical Development
The journey of photolithography began in the mid-twentieth century, coinciding with the dawn of semiconductor technology. Early methods utilized simple masks and ultraviolet light to project patterns onto wafers. These initial techniques laid the groundwork for more complex approaches.
In the 1970s, advancements in optical systems and exposure techniques enabled the production of smaller features on chips. This marked the transition from 5-micron to sub-micron feature sizes, allowing integrated circuits to exponentially increase in complexity and capability.
"The evolution of photolithography is a testament to human innovation, driving the semiconductor industry forward with each new technique and approach."
As the industry progressed into the 1990s, techniques like 193-nanometer wavelength lithography became mainstream. These advancements allowed for further miniaturization and boosted the performance of semiconductor devices.
Despite rapid advancements, challenges remain, such as resolution limits and increasing costs. Future innovations will still be focused on pushing the boundaries of what's possible, aiming for higher precision and efficiency in the manufacturing of the next generation of electronic components.
Key Components of Photolithography Steppers
Photolithography steppers are sophisticated tools essential for the manufacture of semiconductor devices. They utilize light to transfer patterns from photomasks to semiconductor wafers. The efficiency and accuracy of these steppers are highly dependent on several critical components. Understanding these components is essential not only for grasping the operational principles but also for exploring innovations and applications in the semiconductor sector.
Light Sources
Light sources are fundamental in photolithography steppers. The type of light used influences the process significantly. Traditionally, Mercury vapor lamps and Xenon lamps served as common light sources. However, advancements led to the development of lasers like ArF excimer lasers. These sources emit short wavelengths, allowing for finer resolutions in patterns on the wafer surface. Shorter wavelengths provide better detail, enabling manufacturers to produce smaller and more efficient electronic components.
The transition from older light sources to modern excimer lasers marks a pivotal point in achieving higher precision. Each light source used must be thoroughly calibrated to ensure optimal exposure, as the intensity and stability of the light directly contribute to the quality of the imprint on the wafer.
Optical Systems
Optical systems in photolithography steppers play a crucial role in focusing light onto the wafer. These systems consist of lenses that manipulate light to create the desired image on a microscopic scale. The design of these optical systems is highly complex, involving various elements arranged to minimize aberrations and optimize focus.
Advanced systems often employ a combination of refractive and reflective components. For example, catadioptric lenses utilize both mirrors and refractive optics for effective light management. The performance of optical systems directly affects resolution and depth of focus, making them key players in determining the overall capability of a photolithography stepper. Ensuring these systems are aligned and free from defects is vital for maintaining high throughput and yield in manufacturing.
Photoresists
Photoresists are light-sensitive materials applied to the wafer that react to exposure from the light source. They undergo a chemical change when exposed to light, which subsequently allows for the selective development of the patterns. There are two types of photoresists: positive and negative.
Positive photoresists become soluble in the developer solution when exposed, revealing the pattern below. Negative photoresists, on the other hand, harden where they are exposed and remain intact when developed. The choice of photoresist affects resolution, contrast, and overall efficiency of the photolithography process. Recent advancements in photoresist formulations have led to improved performance, catering to the requirements of cutting-edge semiconductor applications.
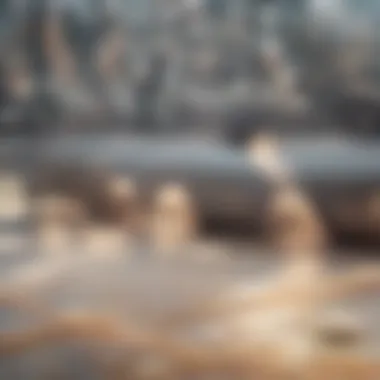
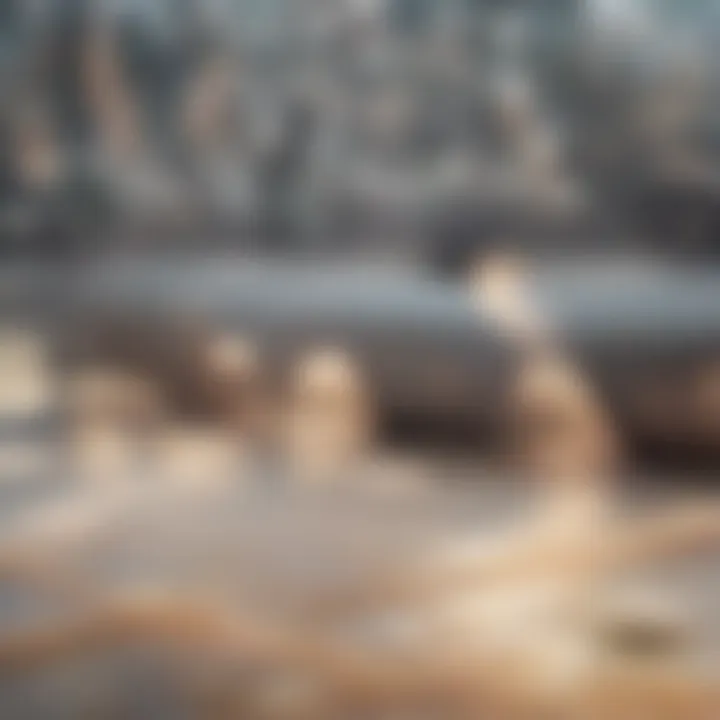
Wafer Stages
Wafer stages are the support structures that hold and position the wafers during exposure. These stages must achieve high precision in alignment, as even minute misalignments can lead to defects in the manufacturing process. Modern systems often utilize motorized stages that provide fine movement controls, ensuring accurate alignment with the photomask.
Furthermore, the integration of feedback mechanisms enhances the stability and accuracy during the exposure phase. These systems are designed to withstand environmental factors, such as vibration, and ensure consistency across multiple layers of photoresist. The success of the lithography process is heavily tied to the effectiveness of wafer staging techniques, directly influencing yield rates and production efficiency.
In summary, the key components of photolithography steppers—light sources, optical systems, photoresists, and wafer stages—each have critical roles that determine the success of semiconductor manufacturing processes. Understanding these elements is vital as the industry continues to evolve and innovate.
Operational Mechanism of Photolithography Steppers
Understanding the operational mechanism of photolithography steppers is fundamental to grasping how they contribute to semiconductor manufacturing. This section delves into the intricate processes that make photolithography steppers a vital component in the production of integrated circuits. The mechanism not only facilitates the transfer of intricate circuit designs onto silicon wafers but also influences the overall efficiency and precision of chip fabrication.
Process Overview
The operational workflow begins with the preparation of the silicon wafer. A photoresist layer is coated uniformly on the wafer's surface. This layer is sensitive to light, distinguishing between exposed and unexposed regions. Once the photoresist is applied, the wafer is loaded into the photolithography stepper. The stepper uses a series of high-precision optics to project the desired pattern from a photomask onto the wafer's surface. This step is critical as it defines the features of the integrated circuits.
The exposure utilizes intense light sources, such as argon fluoride lasers, to illuminate the photoresist-coated wafer through the photomask. The features on the photomask dictate where light can penetrate, creating an image on the photoresist. After the exposure phase, the wafer undergoes a development process. In this stage, the wafer is treated with a developer solution that removes either the exposed or unexposed regions of the photoresist, depending on whether a positive or negative resist is used. This results in a precise pattern that mirrors the photomask.
Alignment Techniques
Alignment is crucial in photolithography, ensuring that subsequent layers of patterns are accurately positioned. The alignment system of a stepper compensates for any inaccuracies that might occur during the wafer handling. Generally, there are two primary methods used — edge alignment and mark alignment.
- Edge Alignment: Utilizes the edges of previously defined features on the wafer for registration. The system measures the position of these edges and aligns the wafer accordingly.
- Mark Alignment: Involves specially designed alignment marks that are deeply etched into the wafer. The optical system of the stepper detects these marks and adjusts the exposure accurately.
Both techniques are vital to maintain the alignment accuracy, which directly impacts the performance and yield of the fabricated chips. A misalignment can lead to reduced device performance and increased defects in the final product.
Exposure and Development
Following the alignment, the exposure process activates the photoresist. The exposure time must be carefully calibrated to achieve the right level of sensitivity and pattern transfer. Overexposure or underexposure can lead to undesirable outcomes, affecting the final structure's integrity.
After exposure, the development phase is initiated. This phase entails submerging or spraying the wafer with a specific developer solution. The solution selectively dissolves either the exposed or unexposed areas of the photoresist, leaving behind the desired pattern. This pattern becomes the template for subsequent processes, such as etching or doping, integral to semiconductor fabrication.
In summary, the operational mechanism of photolithography steppers is defined by a series of systematic steps that combine art with precision. From coating photoresists to alignment techniques and exposure, each element contributes to the production of high-quality semiconductor devices. Understanding these mechanisms is essential for evaluating the efficiency and effectiveness of modern chip manufacturing.
Advancements in Photolithography Technology
Advancements in photolithography technology are vital as they directly affect the efficiency and capability of semiconductor manufacturing. This section explores various innovations that enhance photolithography steppers, highlighting specific elements that contribute to better performance in the industry. Keeping pace with the ever-increasing demand for smaller, faster, and more powerful electronic devices necessitates continual evolution in the tools and processes employed in fabrication. The development of new technologies not only improves the resolution and accuracy of lithographic techniques but also addresses challenges related to cost and sustainability.
Wet vs. Dry Lithography
Wet and dry lithography represent two approaches in the photolithography process. The primary difference lies in the environment used during the exposure of photoresists and the rinsing process afterward.
- Wet lithography involves using a liquid medium, typically a solvent, during the exposure phase. This method allows for enhanced imaging quality and reduces defects, which can be crucial for advanced chip designs. However, it usually requires more intricate handling and has longer processing times due to additional steps such as rinsing and drying.
- Dry lithography, on the other hand, utilizes gaseous or vapor-phase chemistries. This approach tends to offer quicker processing times and simpler handling, which can be beneficial in high-volume production scenarios. Despite the operational advantages, dry lithography might not achieve the same resolution as its wet counterpart, thus presenting a trade-off between speed and image fidelity.
Each method has unique strengths and shortcomings, making them suitable for specific applications within semiconductor manufacturing. The choice between wet and dry lithography often depends on the specific requirements of the production line and the desired characteristics of the final product.
Extreme Ultraviolet Lithography
Extreme ultraviolet lithography (EUV) is a groundbreaking technology that has transformed the landscape of chip manufacturing. EUV uses very short wavelengths of light, specifically 13.5 nanometers, allowing for the printing of extremely fine features on semiconductor wafers. This advancement enables manufacturers to create more compact circuits, leading to improved performance and energy efficiency in devices.
The transition to EUV lithography presents various advantages:
- Higher Resolution: The short wavelength allows for finer patterning, crucial as manufacturers aim for smaller chip features.
- Simplified Process: EUV reduces the need for multi-patterning techniques, which can complicate fabrication and increase costs.
- Lower Defect Rates: Improved optical systems in EUV tools lead to better image fidelity, resulting in fewer defects and more reliable performance.
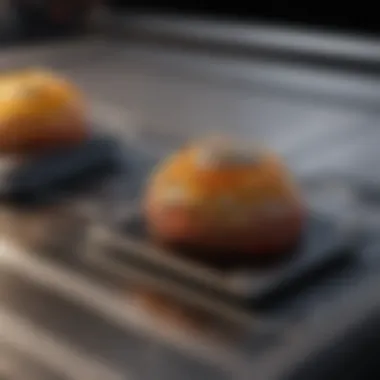
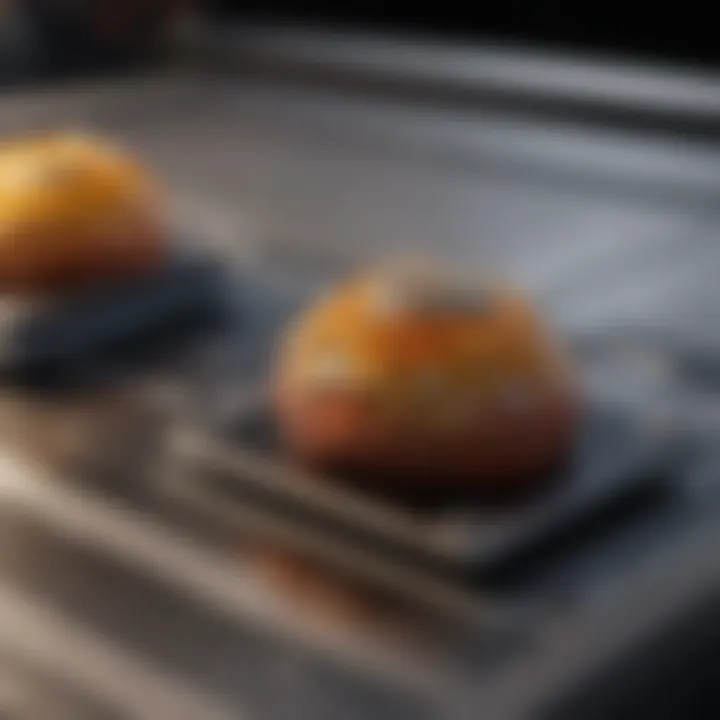
Nevertheless, transitioning to EUV lithography comes with challenges, such as the need for advanced infrastructure and significant capital investments. As EUV becomes more prevalent, it will likely continue to evolve, addressing these issues and making it a cornerstone of future semiconductor applications.
Multi-Patterning Techniques
With the limitations of traditional lithography methods becoming apparent, multi-patterning techniques have emerged as a valuable solution in semiconductor manufacturing. These techniques allow for the creation of smaller features by using multiple lithographic exposures to achieve a single layer pattern. This is particularly helpful given the physical limitations of photolithographic resolution.
Some key points about multi-patterning include:
- Enhanced Feature Size Reduction: By creating patterns in several steps, manufacturers can effectively produce smaller and more intricate designs. This plays a crucial role in maintaining performance within advanced nodes.
- Increased Complexity: Multi-patterning adds layers of complexity to the manufacturing process, leading to longer cycle times and increased potential for defects.
- Cost Implications: While multi-patterning can enhance the resolution, it often involves more materials and process steps, potentially driving up costs.
Applications of Photolithography Steppers
Photolithography steppers serve a crucial role in various industries, particularly in semiconductor manufacturing, microelectromechanical systems (MEMS), and optoelectronics. Understanding these applications illustrates how essential photolithography is to modern technology. The precision of photolithography is key in defining features at the nanoscale, shaping the future of electronic devices.
Semiconductor Manufacturing
The semiconductor industry is the primary user of photolithography steppers. These machines allow for the intricate patterning of wafers used in the production of integrated circuits. Steppers project images of circuit designs onto silicon wafers coated with photoresist material. As technology advances, the ability to fit more transistors onto a chip while maintaining or improving performance is paramount. For example, the switch to extreme ultraviolet lithography has allowed manufacturers to create smaller and more powerful chips.
"The use of photolithography is central to achieving the high integration density required in modern electronics, facilitating the continuous scaling of device dimensions."
In semiconductor manufacturing, process efficiency and accuracy are critical. Steppers not only enhance the resolution but also improve the speed of production. With tighter tolerances, they contribute to the increased yield—an important consideration when operating on thin profit margins. The economic impact of efficient photolithography translates directly into competitive advantages in this fast-paced sector.
Microelectromechanical Systems (MEMS)
MEMS technology benefits significantly from photolithography steppers. These systems combine mechanical and electrical components on a single chip to perform functions such as sensing and actuation. Photolithography provides the necessary precision to fabricate the tiny features involved in MEMS devices accurately. It allows for the layering of different materials, enabling complex structures to enhance device performance.
The applications of MEMS can be found in a range of industries, from automotive sensor systems to consumer electronics. For instance, micro sensors in airbag systems rely on MEMS technology to detect sudden changes in speed. The role of photolithography in MEMS is, therefore, not only vital for their creation but also contributes to the overall reliability and functionality of these innovative systems.
Optoelectronics
In the field of optoelectronics, photolithography steppers still play a fundamental role. Devices such as light-emitting diodes (LEDs) and lasers require precise design and layering to function effectively. The process facilitates the development of optoelectronic components by enabling the creation of intricate patterns and structures essential for electronic and photonic integration.
Photolithography enables high-volume production of optoelectronic devices, which is critical to meeting market demands. As applications expand to include advanced displays, telecommunications, and various lighting technologies, the efficiency and effectiveness of photolithography in these areas can drive innovation and improvements in performance.
The evolution of these technologies highlights the continuous need for enhancing photolithographic techniques, ensuring that industries can keep pace with rapid technological advancements and consumer expectations.
Challenges in Photolithography
Photolithography is essential for the production of semiconductors. However, several challenges arise within this complex field. Understanding these issues is crucial for students, researchers, and professionals to navigate the evolving landscape of semiconductor technology. Among these challenges, resolution limits, cost considerations, and material compatibility are foundational aspects that impact the effectiveness and efficiency of photolithography steppers.
Resolution Limits
Resolution limits refer to the smallest feature size that can be accurately replicated on a wafer. As technology advances, the demand for smaller and more complex integrated circuits increases. Traditional optical lithography techniques face physical limitations due to diffraction. The Rayleigh criterion defines the minimum resolvable feature size as a function of wavelength and numerical aperture. As engineers push the boundaries, they often grapple with challenges in achieving features smaller than 5 nm.
Advancements like extreme ultraviolet lithography (EUV) aim to overcome these limits. However, the transition from established methods to extreme ultraviolet poses risks and technical hurdles. Addressing these requires innovative optical designs and advanced photoresist materials that can withstand the new parameters.
"Progress in resolution can define the next era of semiconductor technology, affecting performance and miniaturization efforts."
Cost Considerations
The financial implications of photolithography processes are significant. The costs associated with photolithography steppers are influenced by several factors, including equipment price, operational expenses, and maintenance. As steppers become more advanced, the initial investments soar. For instance, an EUV lithography machine can cost upwards of $120 million, which remains prohibitive for many manufacturers.
Moreover, the cost of consumables, such as photomasks and photoresists, adds to the overall expense. Manufacturers must balance performance and financial viability to remain competitive. Continuous innovation in cost-effective materials and processes will be essential to reduce financial burdens and keep up with growing demands.
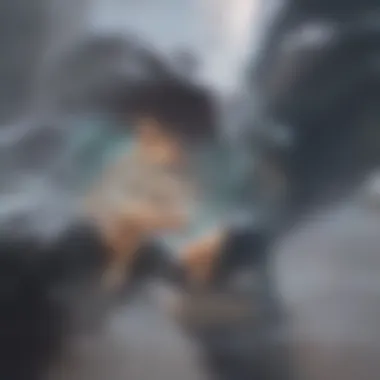
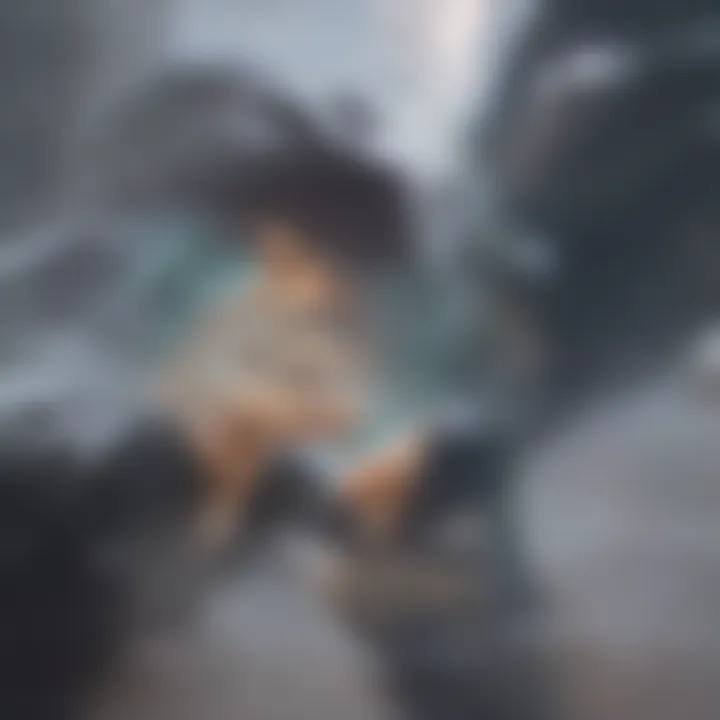
Material Compatibility
Material compatibility is another critical challenge in photolithography. The extensive range of materials utilized in semiconductor manufacturing presents distinct compatibility issues. For examples, photoresists must align well with substrate materials to ensure optimal adhesion and performance. Variations in thermal properties and expansion rates can lead to defects, affecting yield.
Moreover, the trend toward adopting new materials, such as graphene and advanced dielectrics, necessitates revisiting standard processes and workflows. Ongoing research is essential to address these compatibility issues while ensuring that innovations can be incorporated without abrupt disruptions.
Future Trends in Photolithography
The future of photolithography is poised for significant evolution, driven by ongoing technological advancements and growing industry demands. As newer applications emerge and existing practices are refined, understanding these trends is crucial for staying relevant in semiconductor manufacturing. This section investigates some prominent elements shaping the future of photolithography, focusing on emerging technologies and sustainability efforts.
Emerging Technologies
Emerging technologies in photolithography are directly related to the requirement for finer resolutions and greater efficiency.
- Extreme Ultraviolet Lithography (EUV): EUV offers a substantial resolution improvement over traditional methods. Utilizing shorter wavelengths, it enables the fabrication of smaller features essential for modern chips. Companies like ASML are leading the charge in developing EUV machines, making it vital for leading-edge semiconductor processes.
- Nanoimprint Lithography: This technology enables the creation of nanoscale patterns on substrates. Unlike conventional photolithography, it uses mechanical pressure instead of light, potentially simplifying the manufacturing process. Its ability to produce high-density patterns can lead to substantial cost reductions.
- 3D Lithography: As the industry shifts towards more complex tridimensional structures, 3D lithography techniques are being explored to meet these demands. These methods provide new avenues for device configuration and miniaturization.
- Hybrid Techniques: Combining different lithographic methods may enhance flexibility. Integrating traditional photolithography with emerging techniques could yield improved capabilities while maintaining cost efficiency.
These technologies focus on addressing the practical challenges faced in semiconductor fabrication and enhancing the overall performance of photolithography systems.
Sustainability Efforts
As global attention shifts toward sustainable practices, the photolithography sector is also seeking methods to reduce its environmental impact.
- Reduced Material Use: The development of new photoresist materials aims to minimize waste and improve compatibility with eco-friendly solvents. This shift is crucial in lowering the environmental footprint associated with chemical usage.
- Energy Efficiency Improvements: Innovations in light sources and optical systems are enhancing energy efficiency in lithography machines. Reducing power consumption not only lowers costs but also adheres to increasing regulatory demands for sustainability.
- Circular Economy Initiatives: The semiconductor industry is beginning to embrace circular economy principles, focusing on recyclability and reusability of materials used in photolithography. This strategy promotes a more sustainable lifecycle for products.
"Adopting sustainability measures in photolithography is essential, not just for compliance but for long-term viability in a changing market."
- Research in Green Chemistry: The adoption of green chemistry in developing photolithography materials is gaining traction. This research may lead to safer alternatives that can replace harmful substances currently used in the process and ultimately contribute to a healthier ecosystem.
In summary, the future trends in photolithography reflect an industry steadily moving towards greater integration of advanced technologies and sustainable practices, ushering in an era of innovation that is crucial for continued progress.
End
The conclusion of this article emphasizes the complexity and significance of photolithography steppers in modern semiconductor manufacturing. This technology serves as the backbone for producing integrated circuits, which are pivotal for the functionality of nearly all electronic devices today. By synthesizing various facets discussed throughout the article, one can appreciate not only the intricate equipment and methodologies involved but also the broader implications arising from advancement in this field.
Summary of Key Points
In summary, photolithography steppers are critical to the semiconductor industry. They employ light to transfer patterns onto a substrate, facilitating the creation of circuitry in silicon wafers. Major points include:
- Fundamental Mechanisms: The basic operational framework includes exposure, alignment, and development processes.
- Technological Improvements: Emerging technologies like Extreme Ultraviolet lithography and multi-patterning techniques are enhancing resolution and efficiency, addressing the traditional limitations present in photolithography.
- Diverse Applications: Photolithography is not limited to semiconductors; it extends to MEMS and optoelectronics, highlighting its versatility across various sectors.
- Challenges Addressed: Cost-effectiveness and material compatibility remain vital for future innovations in photolithography systems.
Implications for the Future
The implications of advancements in photolithography technology remain profound. As the demand for smaller, faster, and more efficient electronic devices surges, innovation in this area becomes increasingly essential. Key implications include:
- Scaling Challenges: As chip features continue to shrink, the need for innovative approaches to maintain resolution and pattern fidelity will become more pressing.
- Sustainability Advancements: With an increasing focus on sustainable manufacturing practices, developing eco-friendly materials and processes will likely shape the future landscape of photolithography.
- Global Competitiveness: Countries focusing on enhancing their semiconductor manufacturing capabilities through photolithography advancements will play a pivotal role in economic and technological leadership.
Hence, through continuous exploration and development, photolithography steppers will not only shape the evolution of electronic devices but also influence broader technological trends and sustainability initiatives across the industry.
Importance of References
- Credibility: A well-researched article enhances its credibility through references. By citing recognized sources, such as academic journals and reputable industry publications, the content gains legitimacy.
- Knowledge Base: The development of photolithography is grounded in decades of research. Through references, readers can trace advancements in the technology, understand historical milestones, and gain insights that could prompt further exploration.
- Contextual Understanding: Each reference provides context. For example, references related to extreme ultraviolet lithography offer a background on how this technology evolved and its significance compared to conventional methods. Readers need to grasp not just the current state but also the trajectory of developments.
"References are the footprints that guide you through the vast landscape of knowledge," a sentiment echoed by many academic scholars.
Specific Elements to Consider
- Diversity of Sources: A comprehensive list of references should encompass a variety of materials, including research papers, review articles, and reputable web resources. This diversity enriches the discussion, ensuring that multiple perspectives on photolithography are represented.
- Recent Publications: In a rapidly advancing field like semiconductor manufacturing, the relevance of information is time-sensitive. References should include recent publications to ensure that the insights presented reflect the latest technological advancements.
- Referencing Best Practices: When compiling references, it is crucial to follow standardized citation formats. This not only facilitates easy navigation but also enhances professionalism. Formats like APA or IEEE are commonly employed in scientific writing.
Benefits of Well-Chosen References
- Enhanced Learning Experience: For students, detailed references create an opportunity for deep learning. They can explore cited works to gain a more robust understanding of complex concepts.
- Networking and Community Building: Researchers and professionals who engage with cited works may find networking opportunities, fostering collaboration in future research endeavors.
- Continued Relevance: As technologies evolve, maintaining an up-to-date reference list helps in keeping discussions relevant. It forms a living document that can be referenced in future studies as a point of comparison.