Understanding Copper Foil Thickness and Its Impact
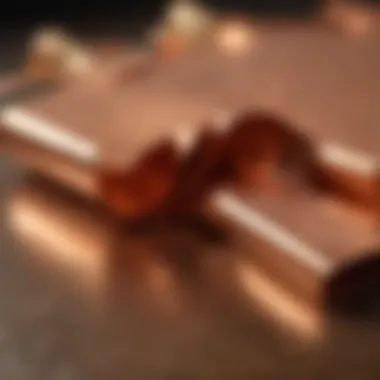
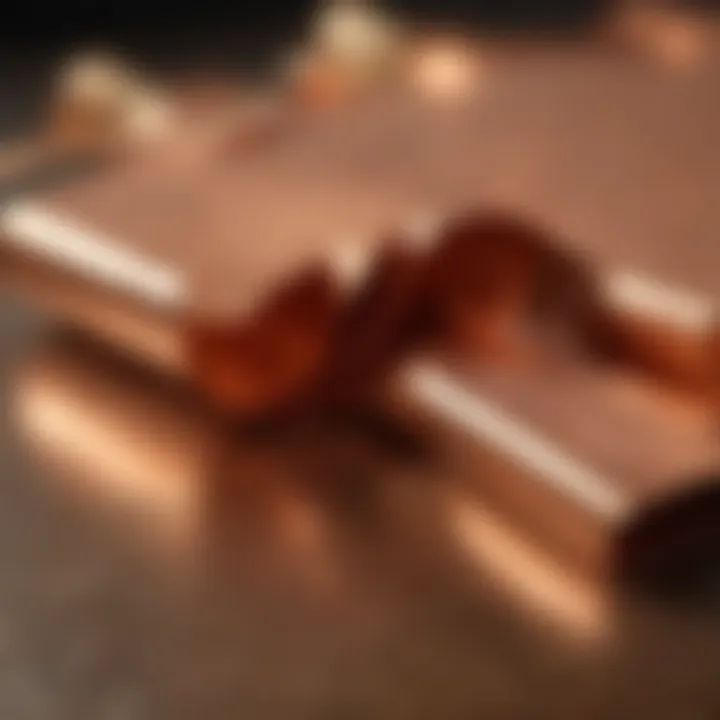
Intro
Copper foil thickness plays a vital role in many fields, particularly in electronics and material science. The thickness of copper foil can influence various properties, including electrical conductivity, thermal properties, and mechanical strength. As technology progresses, understanding these aspects becomes increasingly important, not only for researchers but also for industrial applications and product development.
Copper has long been a preferred material in many technological applications due to its excellent conductivity. However, the effective use of copper foil requires careful consideration of its thickness. In this discussion, we will investigate the implications of copper foil thickness, explore measurement techniques, and discuss industry standards. By gathering insights from current research, this article aims to shed light on why thickness is critical in todayโs technological landscape.
Prelude to Copper Foil Thickness
Understanding copper foil thickness is essential in various technological domains, especially in electronics and materials science. This aspect significantly influences the performance, reliability, and efficiency of devices. Copper foil thickness determines the conductivity and structural properties which directly impact applications such as circuit boards, batteries, and electromagnetic shielding.
The need for precise control over copper foil thickness arises from the increasing demand for miniaturization in electronic devices. Innovations in technology, such as smartphones and electric vehicles, have intensified the focus on optimizing materials, making copper foil a cornerstone of modern engineering.
Definition of Copper Foil Thickness
Copper foil thickness refers to the measurement of the thin layer of copper, often used as a conductive element in various applications, particularly in electronics. It is typically measured in micrometers (ยตm) or mils, with common thicknesses ranging from 1 to 500 ยตm. This thickness influences both electrical and mechanical properties, determining the efficiency with which copper can conduct electricity and its ability to withstand physical stress.
The accuracy in measuring this thickness is crucial for achieving desired conductive characteristics. For example, thicker copper foils may provide better current carrying capacity but can also add unnecessary weight and cost in certain applications.
Historical Context
The use of copper foil dates back to ancient civilizations, where it was recognized for its conductive properties. However, its application in modern electronics began in the mid-20th century with the rise of printed circuit boards (PCBs). The increasing complexity of electronic devices drove the need for more refined manufacturing techniques.
Historically, the thickness of copper foil was standardized for specific industries. In the 1980s, the introduction of automated manufacturing processes allowed for more consistent thickness, enhancing performance and reliability in applications such as telecommunications and computing.
Today, significant advancements in manufacturing technology have led to the development of specialized processes for producing copper foil with exact thickness specifications tailored to evolving technological demands.
Copper foil thickness plays a vital role in shaping the future of electronic designs, influencing everything from energy efficiency to device miniaturization.
Measurement Techniques for Copper Foil Thickness
Understanding the measurement techniques for copper foil thickness is essential in various industrial applications. Precise thickness measurements affect the material's performance, particularly in sectors like electronics, automotive, and renewable energy. Various methods exist, each with unique advantages and considerations, making it crucial to select the appropriate technique. The right measurement can lead to improved product quality, enhanced reliability, and rigorous compliance with industry standards.
Standard Measurement Methods
Standard methods for measuring copper foil thickness remain foundational in ensuring quality control. Common techniques include micrometers, calipers, and optical devices.
- Micrometers offer highly accurate measurements, typically used in workshops. They can measure small thicknesses down to one-hundredth of a millimeter.
- Calipers, both digital and mechanical, are versatile and easy to use, making them suitable for various thickness ranges.
- Optical devices use light reflection to determine thickness, offering non-contact measurements. These are especially helpful when working with sensitive materials or thin foils.
Each method emphasizes different aspects; thus, depending on factors such as the precision required or the material's characteristics, some may be preferable over others. Overall, combining these methods can provide a comprehensive understanding of the foil's qualities.
Advanced Techniques
Advanced techniques go beyond standard methods, allowing for more detailed analysis or specific requirements.
X-ray fluorescence
X-ray fluorescence (XRF) is a powerful method for determining material composition, including copper foil thickness. XRF measures the radiation emitted by a material when exposed to X-rays. This technique enables precise elemental analysis without damaging the sample.
Key characteristics of X-ray fluorescence include:
- Non-destructive: XRF does not alter the material, preserving it for further use.
- Rapid analysis: Results can be obtained quickly, facilitating fast decision-making.
However, the unique feature of XRF is its ability to provide insights into not just thickness but also the elemental composition of the foil.
Advantages of using XRF in this context include:
- High sensitivity to detect trace elements, essential for quality control.
- Capability to analyze multiple elements simultaneously, saving time and resources.
On the downside, the initial cost of XRF equipment can be significant, which may deter smaller operations from adopting this technology.
Ultrasonic testing
Ultrasonic testing employs sound waves to measure foil thickness and is another advanced technique utilized in various industries. By sending high-frequency sound waves through the material and measuring the time taken for the echoes to return, this method can accurately determine thickness without direct contact.
Key characteristics of ultrasonic testing are:
- High accuracy: It can detect minor variations in thickness, which is critical for electronic applications.
- Versatile: Suitable for various materials, including metals and composites.
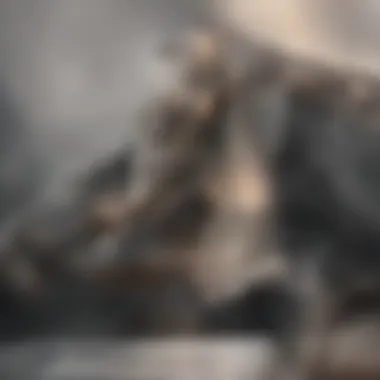
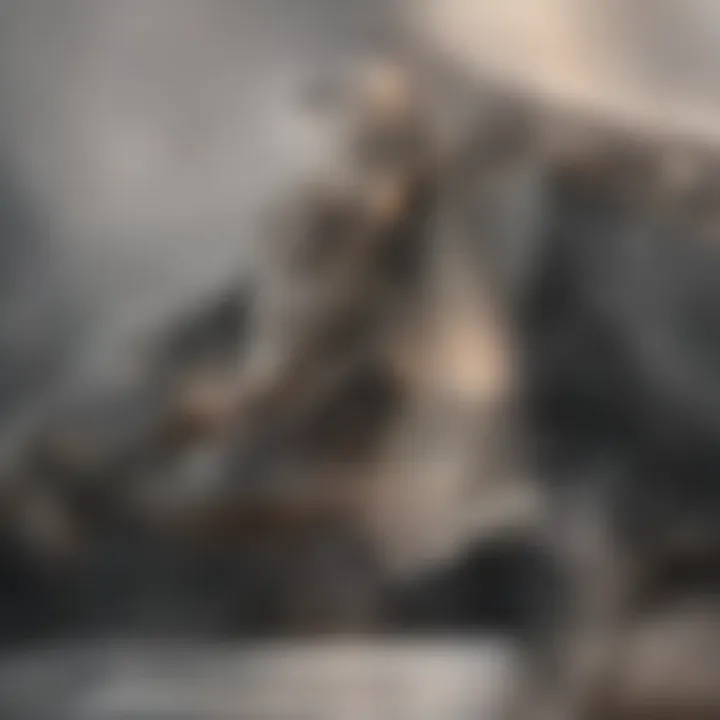
The unique feature of ultrasonic testing is its effectiveness in assessing thickness at inaccessible or hard-to-reach areas.
Advantages include:
- Non-destructive testing ensures that the material remains intact.
- It allows for in-field testing, making it convenient in real-world applications.
A potential disadvantage is that ultrasonic testing can require more training to operate and interpret results accurately.
Factors Influencing Copper Foil Thickness
Understanding the factors that influence copper foil thickness is critical for developers and engineers in the field. Copper foil thickness can significantly affect the performance and application of the material in various technologies. For example, thinner foils may improve flexibility but can compromise strength. Conversely, thicker foils can enhance electrical conductivity but may be less suitable for high-density applications.
Material Properties
Material properties of copper greatly impact its foil thickness. The purity of copper plays a vital role; higher purity levels generally yield better performance in terms of electrical conductivity and ductility. The addition of alloying elements can enhance specific properties but may also influence the foil's overall thickness. Moreover, grain structure affects how copper behaves during manufacturing. Fine-grained copper can result in thinner but stronger foils, improving functionality in applications such as circuit boards.
Manufacturing Process Variations
Variations in manufacturing processes have a notable effect on the thickness of copper foil. Different techniques, such as rolling, electroforming, and casting, offer distinct outcomes in terms of foil attributes. Rolling processes can be adjusted to achieve desired thicknesses, but care must be taken to avoid defects. Electroforming allows for exceptional control over thickness at the micro-level, but this process can be time-consuming and require specialized equipment. Each process leaves a unique fingerprint on the final product, affecting its performance in various applications.
Environmental Considerations
Environmental conditions during the manufacturing and usage of copper foil can also influence its thickness. Temperature and humidity variations can lead to expansion or contraction of the material. This physical state change can alter thickness, potentially leading to performance issues in sensitive applications. Additionally, exposure to corrosive elements might cause degradation, impacting the foil's actual thickness and strength over time. Evaluating these factors is essential for ensuring reliability and longevity in the final applications of copper foil products.
"The intricate balance of material properties, manufacturing processes, and environmental factors shapes the effectiveness of copper foil in technological applications."
Thus, recognizing these elements is essential when designing applications that rely heavily on copper foil to function optimally. Not only are the physical characteristics of the copper itself important, but the methods used to create the foil and the environments in which they are used also play pivotal roles.
Impact of Copper Foil Thickness on Electrical Conductivity
The electrical conductivity of copper foil is highly dependent on its thickness. As technology advances, the demand for more efficient electrical components increases. Thus, understanding how thickness influences conductivity is essential. Thinner foils can lead to reduced electrical resistance, enhancing performance in various applications. Conversely, excessively thin foils might compromise durability and mechanical stability.
Theoretical Foundations
At a fundamental level, electrical conductivity in metals, including copper, is influenced by the availability of free electrons to carry electric current. Copper is known for its excellent conductivity, attributed to its atomic structure. As foil thickness varies, several factors come into play. For example, when the thickness of a copper foil decreases, surface scattering becomes more significant. This means that the travel path for electrons can be disrupted more readily, potentially increasing resistance.
Furthermore, the Hall effect can change with varying thicknesses. When a magnetic field is applied to a current-carrying conductor, the voltage generated perpendicular to both the current and the magnetic field is influenced by the material properties, including thickness. Researchers emphasize that optimizing copper foil thickness is critical in applications that require precise electrical performance.
Practical Applications in Electronics
In the realm of electronics, the thickness of copper foil plays a pivotal role in circuit board design and performance. For instance, in printed circuit boards (PCBs), different thicknesses are chosen based on the specific requirements of the device. Thinner foils might be used in high-frequency applications, where lower resistance translates to improved performance. However, these foils must also withstand mechanical stresses during assembly and operation.
In power electronics, thick copper foils are often essential. They provide low thermal resistance, allowing for improved heat dissipation. This is crucial in applications like power converters and electric vehicle components, where heat buildup can be detrimental to functionality and lifespan.
Key Consideration: The balance between electrical conductivity and mechanical integrity must be maintained, ensuring reliable performance without sacrificing durability.
The automotive industry also benefits from varying copper foil thicknesses. Certain components require thicker foils to handle the high current loads efficiently, while others may utilize thinner foils in sensor applications where flexibility and weight are important. Continuous innovation in copper foil technology enables manufacturers to meet the evolving demands of electronic devices, promoting efficiency and sustainability.
In summary, the impact of copper foil thickness on electrical conductivity is significant. Understanding the theoretical principles and their practical applications allows engineers and designers to make informed choices that enhance functionality while addressing operational requirements.
Mechanical Properties Related to Thickness
Understanding mechanical properties related to copper foil thickness is vital for various applications. These properties influence not just the performance of the foil itself, but also the overall efficiency and durability of the devices in which it is integrated. Factors such as tensile strength and ductility are critical in determining how copper foil will behave under stress, while fatigue resistance speaks to its long-term performance in dynamic environments.
The characteristics of copper foil are largely determined by its thickness. Thicker foils typically exhibit greater tensile strength, which is essential for applications where mechanical stress is prevalent. Conversely, thinner foils may provide enhanced flexibility and ductility, enabling them to fit into more complex designs without sacrificing performance. Understanding these properties allows manufacturers and engineers to select the appropriate foil based on the specific requirements of their projects.
Tensile Strength and Ductility
Tensile strength refers to the maximum amount of stress that a material can withstand while being stretched or pulled before failing. In the context of copper foil, this property is essential, especially in applications where the foil may be subjected to forces such as bending or stretching. Thicker copper foils tend to possess higher tensile strength, making them suitable for demanding applications like circuit boards in rugged environments.
Ductility, on the other hand, measures a material's ability to deform under tensile stress. It is an important characteristic for copper foils as it dictates how well the material can be manipulated without breaking. Thinner foils, which may sacrifice some tensile strength, can often better endure stress without fracturing. This balance between tensile strength and ductility is crucial for performance in different environments.
"The optimal balance of tensile strength and ductility in copper foil ensures its reliability and functionality across applications."
In practice, selecting the appropriate copper foil thickness is a matter of analyzing the requirements of the end application. Engineers must weigh the need for strength against the need for flexibility, considering the operational conditions that the copper foil will face.
Fatigue Resistance
Fatigue resistance encompasses a materialโs ability to resist failure under repeated loading conditions. For copper foil, this characteristic is paramount in applications involving cyclic loads, such as in automotive and aerospace industries. Copper foil that is too thin might succumb to fatigue failure after a relatively short period, while adequately thick foil will withstand repeated stress without degrading.
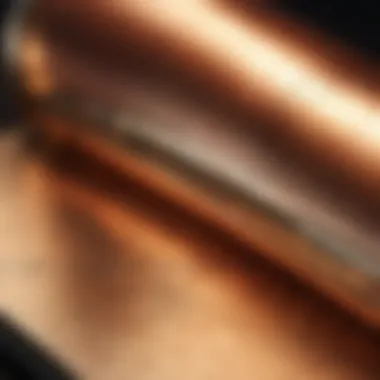
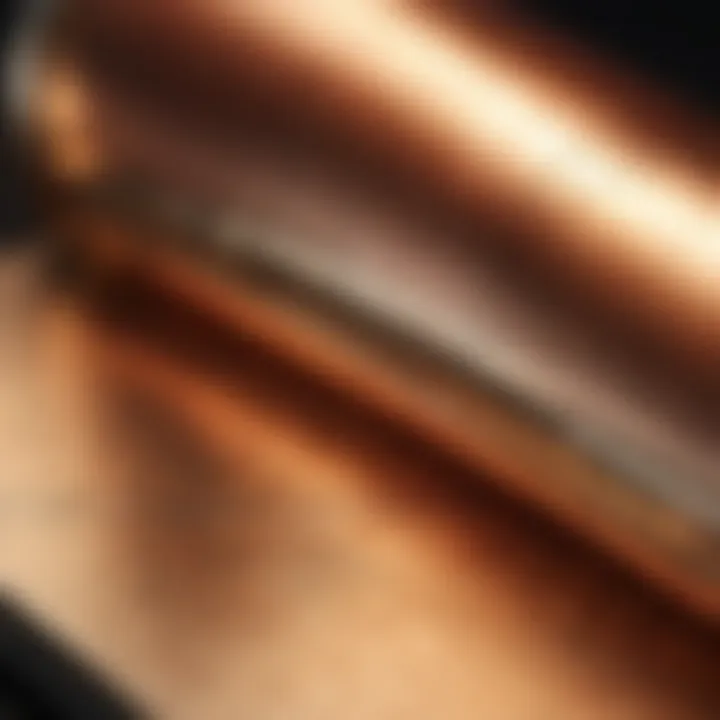
The impact of thickness on fatigue resistance is influenced by grain structure and how the material is processed. Thicker foils often show improved fatigue life due to their ability to better distribute stress. However, factors such as the manufacturing process, including techniques like rolling and annealing, also significantly affect fatigue performance.
In summary, mechanical properties related to copper foil thickness guide decisions regarding material usage in various applications. Awareness of tensile strength, ductility, and fatigue resistance informs best practices in material selection, leading to enhanced performance and durability. For those engaged in production, engineering, or research, a comprehensive understanding of these properties is vital.
Industry Standards for Copper Foil Thickness
Understanding industry standards for copper foil thickness is crucial in the context of production and application. These standards not only dictate the quality and performance of copper foil but also ensure consistency across various manufacturing processes. The importance is underscored by the necessity for reliable and efficient materials in high-tech applications, where even minute variations in thickness can lead to performance issues or failures in components.
The industry adopts certain guidelines to streamline production and design, enhancing overall product reliability. Such standards typically encompass aspects such as minimal thickness tolerances, maximum allowed defects, and essential physical properties like tensile strength. The adherence to these standards is paramount for manufacturers to meet customer expectations and regulatory demands, thus instilling confidence in end-users.
Furthermore, aligning with industry standards helps in minimizing waste during production. By clearly defining specifications, companies can optimize their material usage, thereby recognizing both economic and environmental benefits. Given the escalating demands within sectors such as electronics and renewable energy, mastering these standards is not merely advantageous but necessary in maintaining competitiveness.
International Standards Organizations
International Standards Organizations play a pivotal role in standardizing copper foil thickness. Institutions such as the International Organization for Standardization (ISO) and American National Standards Institute (ANSI) establish guidelines that manufacturers must follow. These organizations evaluate scientific data, consult with industry experts, and incorporate feedback from global markets to create relevant standards.
Particularly for copper foils, standards like ISO 2086 outline specifications that encompass both mechanical and electrical characteristics. The relevance of these guidelines cannot be overstated. They guarantee that products are produced within acceptable tolerances, furthering the reliability of various applications they support, from printed circuit boards to automotive connectors.
The participation in these organizations allows manufacturers to stay up-to-date with emerging technologies and practices, fostering innovation while preserving quality.
Key Responsibilities of International Organizations:
- Development of thickness specifications
- Assessment of production methods for compliance
- Facilitation of collaboration between stakeholders
- Promotion of best practices globally
Regulatory Compliance
Regulatory compliance in relation to copper foil thickness encompasses various legal and safety standards that manufacturers must adhere to. These are typically established by governmental bodies focusing on consumer safety and environmental protection.
Regulatory measures often include stipulations on material purity, thickness tolerances, and production practices that minimize adverse environmental impacts. Compliance ensures that products meet not just safety benchmarks but also performance standards necessary for operational excellence in sensitive fields like aerospace and medical devices.
Failure to comply can lead to dire consequences, such as product recalls, legal repercussions, and significant financial losses. Therefore, manufacturers are encouraged to integrate quality control systems that regularly assess adherence to these regulations.
Importance of Compliance:
- Ensures product safety and reliability
- Protects manufacturers from legal liabilities
- Enhances brand reputation among customers
- Encourages sustainable practices in production
In summary, industry standards for copper foil thickness are integral to ensuring quality and reliability in numerous applications. Organizations that maintain stringent compliance with international standards and regulatory frameworks position themselves favorably in the competitive landscape, paving the way for innovation and improved product offerings.
Innovations in Copper Foil Manufacturing
The manufacturing of copper foil has seen significant advancements in recent years. These innovations are not only about improving the efficiency and cost-effectiveness of production but also addressing the growing demand for high-quality copper foil in various applications. Understanding these innovations is critical for professionals and researchers who aim to stay competitive in this rapidly evolving industry.
Emerging Technologies
Emerging technologies have transformed copper foil manufacturing. Techniques like electroforming and rolling have evolved to produce thinner and more precise foil. Electroforming, for instance, allows for the creation of extremely thin copper foil while maintaining high conductivity and strength. This process involves electrodepositing copper onto a substrate, resulting in a smooth, uniform thickness.
Additionally, advancements in laser technology have introduced new ways to cut and shape copper foil with high precision. Systems that utilize lasers can minimize waste and reduce the time needed for production.
Some technologies enhance the performance of copper foils in demanding applications. For example, the introduction of alloying methods creates foils with unique properties, resulting in better thermal conductivity and resistance to corrosion. These foils are essential for industries requiring reliable performance under challenging conditions.
"Innovation in manufacturing processes is key to unlocking the full potential of materials and enhancing their applications across various fields."
Sustainable Manufacturing Practices
Sustainability is becoming increasingly important in the manufacturing sector, including copper foil production. As the environmental awareness among consumers and companies grows, the focus on sustainable practices in copper foil manufacturing intensifies.
One prominent approach is the recycling of scrap copper foil. By reusing materials, manufacturers reduce resource consumption and waste. Additionally, companies are exploring cleaner production techniques, aiming to lower energy use and emissions during production.
Water management practices are also being refined. Minimizing water usage and ensuring that wastewater is treated before disposal benefits not only the environment but also aids compliance with strict regulations.
It's essential that manufacturers adopt these sustainable practices to meet not just market demands but also regulatory obligations. The interconnected benefits of sustainability include cost reductions, improved public perception, and long-term viability in the industry.
Applications of Copper Foil Across Industries
Copper foil plays a vital role across a variety of industries. Its unique properties, such as excellent electrical conductivity, ductility, and thermal properties, make it an essential material. This section dives into how copper foil is integrated into different sectors, emphasizing specific benefits and considerations that arise from its utilization.
Consumer Electronics
The consumer electronics sector is one of the leading users of copper foil. Devices like smartphones, tablets, and laptops rely on printed circuit boards, where copper foil is a fundamental component. Thin copper foil allows for the creation of densely packed circuits, enabling smaller and more efficient devices.
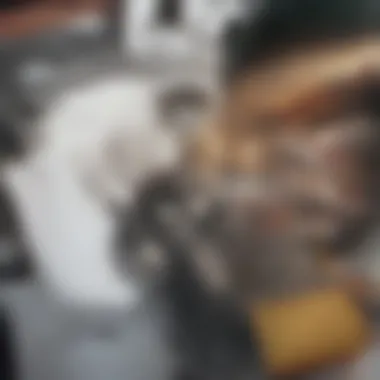
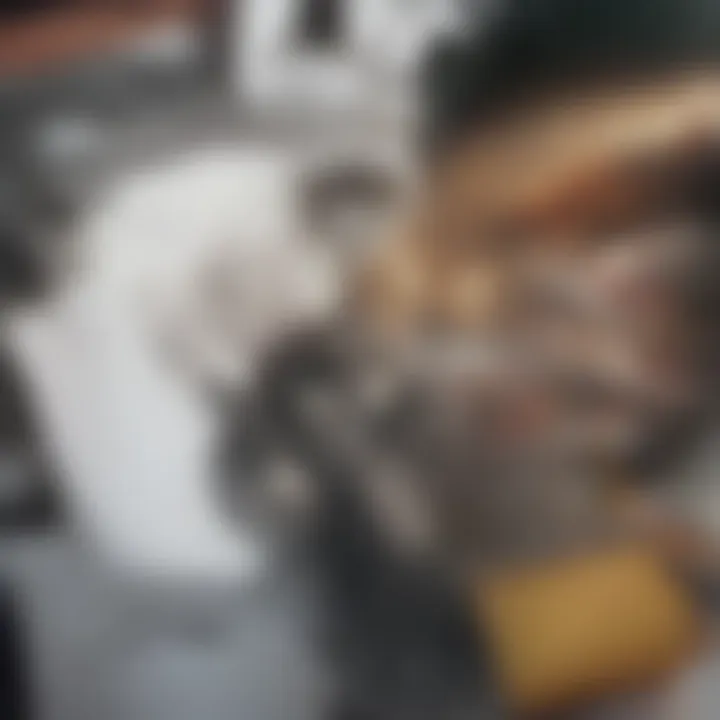
In these applications, the thickness of the copper foil is crucial. Thicker foils provide higher conductivity and better performance, while thinner options offer flexibility and weight savings. Manufacturers often seek a balance that meets performance needs without compromising size constraints.
Benefits of copper foil in consumer electronics include:
- Improved conductivity: Higher efficiency leads to enhanced battery life.
- Space-saving designs: Allows for compact circuit layouts.
- Thermal management: Efficient heat dissipation prevents overheating in devices.
However, challenges exist. As devices become smaller, the demand for ultra-thin foils increases, pushing production techniques and material properties to their limits.
Automotive Industry
The automotive industry is experiencing a transformative shift towards electric vehicles (EVs) and sophisticated embedded electronics. Copper foil is integral in the manufacturing of electric motor components as well as wiring harnesses. Its properties are essential for efficient energy transfer and overall vehicle performance.
In the context of EVs, the demand for lightweight materials leads to increased use of thinner copper foils, which help enhance energy efficiency without adding weight. Additionally, thicker copper foils are employed in critical components to ensure high current conductivity for battery connections and motor drives.
Key considerations for copper foil in automotive applications include:
- Weight reduction: Thinner materials support lighter vehicle designs.
- Safety regulations: Compliance with automotive standards is vital.
- Heat resistance: Components must endure varying temperatures and conditions.
This industry must address challenges related to durability and cost-effectiveness while adapting to rapid technological changes in vehicle designs.
Renewable Energy Solutions
As the world moves towards sustainable energy sources, copper foil's role in renewable energy solutions is increasingly significant. Solar panels utilize copper foil as a conductive layer in photovoltaic cells. The demand for efficient energy conversion places a premium on the material's conductivity and reliability.
In wind energy applications, copper foil also plays a role in generator components and power electronics. Reliable connections and robust insulation properties are essential to ensure long-term performance under tough environmental conditions.
Advantages of copper foil in renewable energy include:
- Efficiency improvement: Better conductivity translates to more effective energy harnessing.
- Durability: Resistance to environmental degradation extends the lifecycle of components.
- Cost-effectiveness: Availability and recyclability of copper offer economic advantages.
While opportunities are abundant, the industry faces challenges, such as fluctuating copper prices and sourcing sustainable materials.
Copper foil remains indispensable across industries, facilitating innovations in technology, sustainability, and efficiency. Its applications highlight the need for ongoing research and development to optimize material performance and adapt to emerging trends.
Future Trends in Copper Foil Development
The significance of understanding future trends in copper foil development cannot be understated. As industries evolve, innovations in technology directly influence the demand and specifications for copper foil. These trends not only impact the manufacturing processes but also have broader implications on efficiency, sustainability, and performance across various applications. In this section, we will delve into market forecasts and explore the acquisition of new materials.
Market Forecasts
Market forecasts indicate a rising demand for copper foil driven by its integral role in electronic devices, automotive applications, and renewable energy sectors. Several factors contribute to this growth:
- Emerging Technologies: The proliferation of electric vehicles and advanced electronics continues to heighten the requirement for high-performance copper foil.
- Consumer Preferences: There is increasing consumer awareness and demand for sustainable products, leading to a preference for materials that minimize environmental impact.
- Globalization: The expanding reach of tech companies into new markets necessitates a reliable and adaptable supply of copper foil.
- Innovation in Product Design: New applications are emerging where improved electrical and mechanical properties are essential, influencing the specifications of copper foil thickness.
In light of these trends, industry players are positioning themselves to capitalize on these shifts. By investing in research and development, companies aim to create enhanced copper foil solutions that meet the specific needs of future technologies.
Acquisition of New Materials
The acquisition of new materials is a critical component in advancing copper foil technology. As industries search for ways to improve performance and reduce costs, the focus often turns to innovative material alternatives. This section discusses key aspects of material acquisition:
- Alternative Alloys: Researchers are exploring alternatives to pure copper, such as copper-nickel or copper-tin alloys, which may offer enhanced properties like corrosion resistance and increased strength.
- Recycled Materials: The shift toward sustainability has prompted interest in sourcing copper from recycled products. This approach not only reduces environmental footprint but can also decrease raw material costs.
- Smart Materials: The emergence of smart materials that can adapt to changing conditions adds a new dimension to copper foil applications, as they may offer improved efficiency in electronic devices.
"The future of copper foil development hinges on our ability to adapt and innovate in sourcing and processing materials."
In summary, the future trends in copper foil development reveal an exciting landscape characterized by growing market demand and evolving material capabilities. As we move forward, keeping an eye on these trends will be essential for stakeholders in the industry.
Summary and Finale
In this article, we explored the complexities of copper foil thickness, revealing its critical role across various technological domains. Understanding this topic is paramount, as copper foil serves as a cornerstone in many applications, from electronics to renewable energy systems. We examined measurement methods, factors influencing thickness, and the implications of these variations on both electrical conductivity and mechanical properties. Such understanding allows industries to optimize their processes for better product performance and durability.
The key benefits of grasping the nuances of copper foil thickness include enhanced design capabilities, improved functionality of electronic components, and the advancement of manufacturing techniques. Additionally, a comprehensive awareness of industry standards helps ensure regulatory compliance and encourages innovation.
As we have analyzed each aspect of copper foil thickness, our aim was to provide relevant and insightful information for students, researchers, educators, and professionals who seek deeper knowledge in this field. Thus, this concluding section will highlight essential takeaways and encourage ongoing research in the area.
Key Takeaways
- Copper foil thickness significantly impacts electrical conductivity and mechanical properties, influencing design choices in electronics and automotive applications.
- Measurement techniques are diverse, ranging from standard methods to advanced techniques like X-ray fluorescence and ultrasonic testing. Each has its specific applications and benefits.
- Variations in manufacturing processes and environmental factors play crucial roles in determining the final copper foil thickness.
- Adhering to industry standards ensures high quality and compliance in copper foil production, benefiting manufacturers and end-users alike.
- Innovations in copper foil production, particularly focusing on sustainability and emerging technologies, are critical for future advancements in multiple sectors.
Call for Further Research
Further exploration into copper foil thickness is necessary to address current challenges and improve methodologies in related industries. Potential areas for research include:
- Advanced Measurement Techniques: Investigating new methods that reduce inaccuracies in measuring copper foil thickness could lead to better consistency in high-precision applications.
- Material Innovations: Researching alternative materials or composite solutions can enhance copper foil characteristics and broaden its applicability in current technologies.
- Sustainability in Production: Investigating environmentally-friendly manufacturing processes can mitigate adverse effects on the ecosystem and lead to advancements in circular economy practices.
- Real-World Applications: Studying the practical impacts of copper foil thickness variations in emerging technologies, such as electric vehicles and solar panels, can provide valuable insights into optimizing designs.
Through continued research in these areas, we can enrich our understanding and application of copper foil thickness, fundamentally contributing to technological progress.