Understanding Shot Peening: Fundamentals and Applications
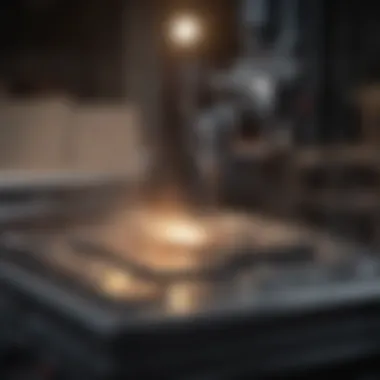
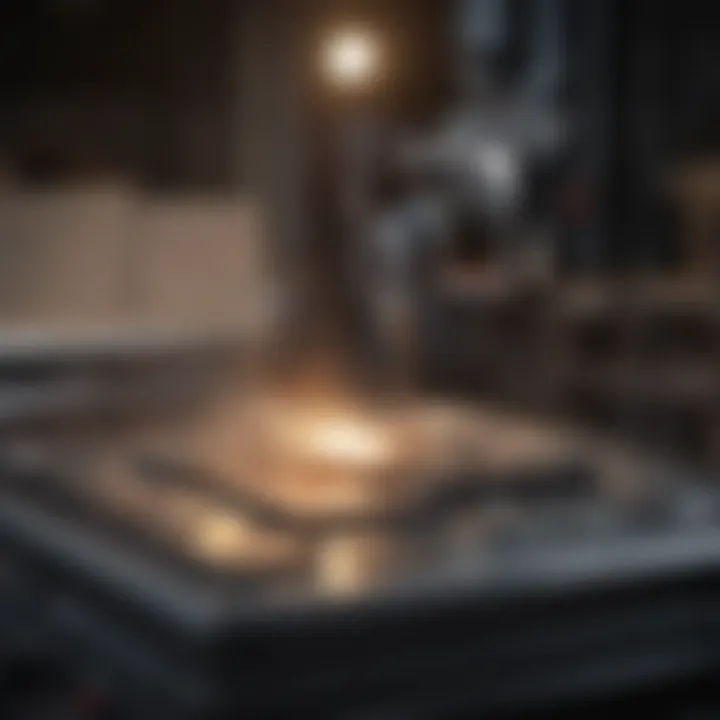
Intro
Shot peening is a mechanical process that plays a crucial role in enhancing the material properties of various substrates. This technique, often used in metal treatment, modifies the surface of materials to increase their resistance to fatigue, enhance durability, and improve overall performance. Knowledge of shot peening is essential for students, researchers, educators, and professionals. Understanding its mechanics, historical context, and applications provides a strong foundation for exploring its significance in modern engineering practices.
The process works by bombarding a surface with small spherical particles, known as shots. This impact creates a compressive residual stress layer on the material's surface, which counteracts tensile stresses that lead to failure. The complexity of shot peening extends beyond its mechanics; it encompasses a variety of factors including shot size, shape, and the intensity of the bombardment. The understanding of these factors not only streamlines current practices but also opens avenues for future research and development.
In this article, we aim to delve deep into the fundamentals and applications of shot peening. We will highlight the key findings, implications of the research, and the potential impact on future innovations in the field.
Intro to Shot Peening
Shot peening is an essential process in material engineering used to enhance the properties of various substrates. This introductory section aims to highlight the significance of shot peening, its critical role in improving material performance, and its implications across multiple sectors. Understanding the fundamentals of shot peening can lead to informed decisions in material selection and treatment processes. The benefits include increased fatigue strength, reduced susceptibility to stress corrosion cracking, and overall extended lifespan of components.
In a world that increasingly demands efficiency and durability in materials, shot peening emerges as a valuable procedure. Industries such as aerospace and automotive rely on this technique for the manufacturing of structural components. By altering the microstructure of materials, shot peening not only enhances fatigue resistance but also improves the overall reliability of products. Knowing its principles allows engineers and material scientists to maximize effectiveness in applications, ultimately leading to safer and more efficient designs.
Definition of Shot Peening
Shot peening is a surface treatment process that involves bombarding parts with small spherical media called shots. The primary goal of this procedure is to induce compressive residual stresses on the material's surface. This treatment can significantly increase the material's fatigue strength and corrosion resistance. The process is typically performed in a controlled environment, ensuring that the angle, speed, and type of shot are optimal for specific applications.
The shots used can be made from various materials such as steel, glass, or ceramic, depending on the requirements of the job. When shot peening is performed correctly, it creates a compressed layer on the surface of the material. This layer works against tension forces during service, thus preventing potential cracks from propagating and significantly enhancing longevity.
Brief History of Shot Peening
The concept of shot peening has a rich history, dating back to the early 20th century. Initially, it was developed as a method to extend the life of military aircraft components. Engineers recognized that bombarding metal surfaces with shots could improve their resistance to fatigue failures, which are crucial in high-stress applications.
Over the decades, technical advancements and deeper understanding prompted the expansion of shot peening into other industries. In the 1950s, the aerospace sector embraced shot peening as a standard practice. Similarly, the automotive industry began to integrate it into their manufacturing processes to ensure durability and performance.
"Shot peening not only represents a mechanical process but serves as a vital step in enhancing the performance and safety of critical components across diverse engineering sectors."
Today, shot peening is recognized worldwide as an essential part of quality control and material enhancement in engineering. Its historical evolution reflects its growing importance in a landscape that prioritizes material reliability and resilience.
Mechanics of Shot Peening
The topic of mechanics of shot peening is a critical element in understanding how this process enhances material properties. Shot peening involves bombarding a surface with small spherical media, referred to as shots. This impact creates compressive residual stresses that can significantly improve fatigue life and resistance to crack propagation in metals and alloys. Furthermore, understanding these mechanical principles is vital for optimizing processes in various industrial applications, ensuring that materials achieve desired performance standards through precise control of shot peening conditions.
Basic Principles Involved
In shot peening, several basic principles govern how the process affects materials. When the shots strike the surface of the workpiece, multiple phenomena occur:
- Kinetic Energy Transfer: The shots possess kinetic energy, which is transferred to the surface upon impact. The energy transfer creates a localized deformation, resulting in the generation of compressive stresses.
- Surface Hardening: The process alters the microstructure at the surface of the material. It leads to a refined grain structure, which increases hardness. This refinement also promotes uniformity in material properties across different sections of the workpiece.
- Elastic and Plastic Deformation: Depending on the intensity of shot peening, a combination of elastic and plastic deformation occurs. The elastic component recovers when the load is removed, while the plastic deformation remains, contributing to the development of residual stresses.
These principles establish the foundation of the shot peening effect. By understanding how energy is transferred, professionals can manipulate parameters like pressure and velocity to optimize the results.
Material Interaction
The interaction between the shots and the material surface is complex and influenced by several factors, including:
- Material Type: Different materials respond uniquely to shot peening. For instance, harder materials may exhibit different microstructural changes compared to softer ones.
- Shot Characteristics: The size, shape, and hardness of the shots play a crucial role in determining the outcome. Spherical shots tend to provide uniform coverage, while angular shots may induce higher localized stresses.
- Peening Intensity: This refers to the energy delivered by the shots. Higher intensity results in deeper penetration and more significant deformation, while lower intensity might lead to shallower changes.
Understanding these interactions allows for effective process control. The objective is to achieve a desirable balance between enhancing material properties and avoiding potential damage that excessive peening might cause.
"Shot peening creates a critical balance between surface hardening and maintaining overall material integrity."
In summary, the mechanics of shot peening encompasses fundamental principles governing energy transfer, deformation, and interactions of shots with various materials. Grasping these components is essential for optimizing applications and ensuring material performance across multiple sectors.
Materials Used in Shot Peening
The selection of materials in shot peening is fundamental to achieving optimal results. Different materials used for shot peening can significantly influence the effectiveness of the process and the resulting improvements in material properties. Understanding the various types of shots and their specific properties helps in determining the most suitable choices for particular applications.
Types of Shots
Shot peening involves the use of small spherical particles, commonly referred to as shots. The types can vary based on their material composition, size, and shape. The most frequently used shots include:
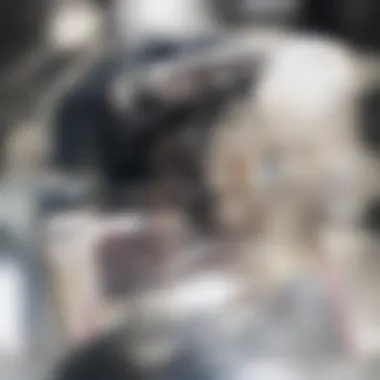
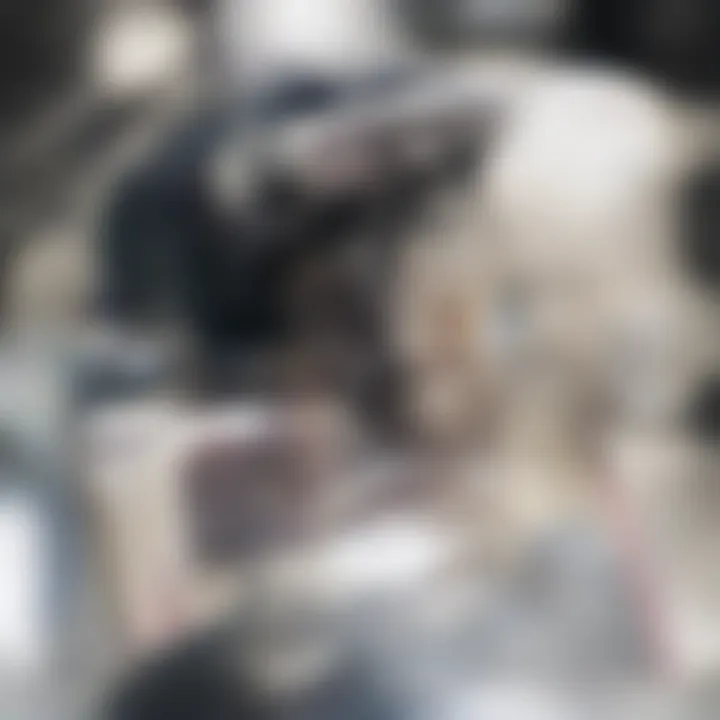
- Steel Shots: These are created from carbon steel and known for their strength and durability. Steel shots are particularly effective for a wide range of applications, providing a consistent surface finish.
- Glass Beads: Being softer, glass beads are typically used for finishing processes where a gentler impact is desired. They offer a unique finish and are ideal for sensitive components where protection from surface damage is crucial.
- Aluminum Shots: Lightweight and less abrasive, aluminum shots are suitable for peening softer materials or delicate parts. Their lower mass results in less intense impacts, making them appropriate for applications requiring a careful approach.
- Ceramic Shots: Ceramic materials introduce hardness and wear resistance. They are often used in applications requiring high durability, like aerospace components. Ceramic shots can produce a specific surface roughness that meets stringent specifications.
Choosing the right type of shot is essential, as it affects not only the efficiency of the process but also the final condition of the peened surface. Different industries may require specific shots to meet their material properties and performance standards.
Material Properties of Shots
The material properties of the shots themselves play a crucial role in the efficacy of the shot peening process. Key considerations include:
- Hardness: The hardness of the shots influences how they impact the substrate material. A harder shot will impart more compressive stresses to the surface, enhancing fatigue life.
- Size: The diameter of the shots should be selected based on the specific application. Larger shots deliver more energy, while smaller ones can be used in fine finishing. A balance must be struck to ensure that the intensity of the peening is suitable for the material being treated.
- Shape: Most commonly, shots are spherical, but variations like angular or irregular shapes can be used to achieve different surface effects. The shape impacts the distribution of impact forces and the resulting surface profile.
- Density: Heavier shots may provide more substantial impacts but can also lead to deeper indentations. The choice of density should align with the desired characteristics of the final product.
The careful consideration of these material properties is vital. Selecting optimal shots will directly impact the outcomes, enhancing not only the mechanical properties of the materials but also ensuring longevity and performance in their respective applications.
Successful shot peening relies fundamentally on the deliberate choice of materials, with both the type of shot and its properties guiding the process towards achieving specific performance goals.
Applications of Shot Peening
The applications of shot peening are vast and critical in enhancing the longevity and performance of many industrial components. This mechanical process serves to not only improve fatigue strength but also alters the surface properties of materials. By generating compressive residual stresses, shot peening effectively reduces the likelihood of crack formation and growth. This section will delve into its applications across various sectors, highlighting the specific benefits and considerations that make shot peening indispensable in today’s engineering landscape.
Aerospace Industry
In the aerospace sector, part reliability and performance are paramount. Components in aircraft experience extreme stress and strain during flight. Shot peening is extensively utilized to enhance the fatigue life of these critical components. High-strength materials, such as titanium and aluminum alloys, benefit significantly from this treatment. The process improves surface hardness and reduces the susceptibility to fatigue failure.
- Key Components: Turbine blades, landing gears, and structural frames are among the most commonly shot peened parts.
- Benefits: Enhanced fatigue resistance leads to increased safety and reduced maintenance costs, both essential in aviation.
The aerospace industry continuously pushes for innovation and efficiency. Thus, shot peening remains a focal point for ongoing research, exploring advanced techniques such as automated and precise peening methods, which can offer even greater improvements in material properties.
Automotive Sector
In the automotive sector, shot peening is vital for enhancing vehicular lifespan and safety. Components like crankshafts, gears, and springs often face cyclic loading during operation. By employing shot peening, manufacturers can significantly extend the fatigue life of these parts.
- Key Components: Gear systems, suspension springs, and transmission parts frequently undergo shot peening.
- Benefits: Improved performance, lower vehicle maintenance requirements, and increased component reliability help manufacturers meet stringent quality standards while enhancing customer satisfaction.
As automotive technologies evolve, especially with the rise of electric vehicles, the role of shot peening is becoming even more pronounced. The demand for lightweight and strong materials makes this process indispensable, ensuring that components can withstand the unique stresses they encounter.
Construction and Heavy Machinery
In the construction and heavy machinery sector, shot peening is applied for structural integrity and durability of machinery components. Equipment such as excavators, cranes, and bulldozers often work under heavy loads. Therefore, improving the fatigue resistance of these components leads to increased operational efficiency and safety.
- Key Components: Load-bearing structures, booms, and hydraulic components are common targets for shot peening.
- Benefits: The enhanced toughness achieved through shot peening decreases the likelihood of sudden failures, which can have catastrophic consequences on job sites. This process also minimizes wear and tear, extending the service life of expensive machinery.
As construction practices evolve, integrating shot peening into maintenance routines can reduce lifecycle costs and enhance productivity, crucial in the competitive construction industry.
Effects of Shot Peening on Materials
The effects of shot peening on materials are significant and warrant in-depth discussion. Shot peening enhances the mechanical properties of materials, especially concerning their fatigue resistance. This section elaborates on two primary aspects: fatigue strength improvement and microstructural changes. Understanding these elements is essential for professionals who aim to optimize materials for various applications, particularly in high-stress environments.
Fatigue Strength Improvement
Fatigue strength improvement is one of the most critical benefits of shot peening. The process induces compressive residual stresses on the surface of materials, which counteracts the tensile stresses that lead to crack formation and fatigue failure. This enhancement is particularly vital in applications within the aerospace and automotive industries, where components are subjected to repeated loading cycles.
Key points regarding fatigue strength improvement include:
- Residual Stress Generation: Shot peening introduces compressive stresses in the surface layer, which can significantly extend the lifespan of components under cyclic loading.
- Crack Delay: The presence of compressive residual stresses can delay the initiation and propagation of cracks, enhancing the overall durability of parts.
- Quantitative Benefits: Testing shows that shot-peened components can achieve improvements in fatigue life by two to six times compared to non-peened counterparts, making this method essential for performance-critical applications.
Overall, the impact of shot peening on fatigue strength cannot be understated. It is a well-established technique for improving the longevity of materials in diverse settings, particularly under dynamic loading conditions.
Microstructural Changes
The microstructural changes induced by shot peening also play a significant role in enhancing material properties. During the process, the impact of the shots causes deformation at the grain level. These alterations can lead to several benefits that improve the material’s properties. It is important for engineers and material scientists to recognize and utilize these changes effectively.
Consider the following aspects of microstructural changes:
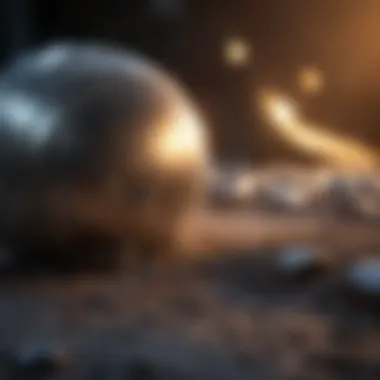
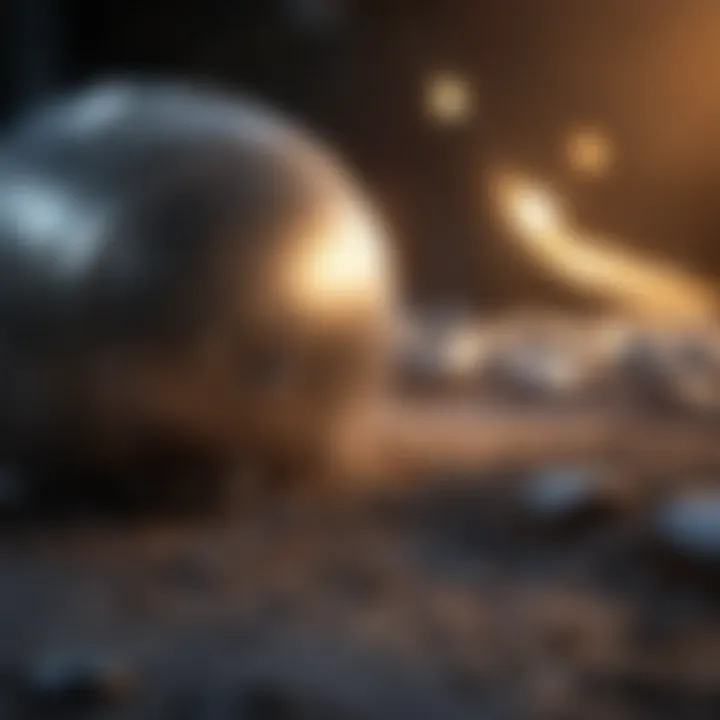
- Grain Refinement: Shot peening typically results in refined microstructures, which can lead to improved strength and toughness. Smaller grains often yield better mechanical performance due to enhanced slip systems.
- Phase Transformations: Depending on the material composition, shot peening can initiate phase transformations that may contribute to advantageous properties like increased hardness and wear resistance.
- Distribution of Inclusions: Changes in the distribution and behavior of inclusions can also occur, which may affect the ductility and toughness of the material.
Understanding microstructural changes helps professionals predict how a material will respond to service conditions after treatment, allowing for better design and application decisions.
"Shot peening is a vital process for optimizing material performance, particularly in high-stress environments where fatigue life is critical."
In summary, the effects of shot peening on fatigue strength and microstructural changes are central to the process's value. These elements not only enhance material performance but also facilitate innovations in design strategies across various industries.
Optimization of Shot Peening Parameters
The optimization of shot peening parameters is a critical element in enhancing the overall effectiveness of this mechanical process. The success of shot peening lies in its ability to induce beneficial compressive stresses within materials, thereby improving fatigue resistance and extending the life of components. This section elucidates the specific elements that play a role in optimizing shot peening parameters, the benefits of proper optimization, and the key considerations to ensure efficient practices in industry.
Pressure and Velocity Considerations
The pressure and velocity at which shots are propelled during the peening process significantly influence the outcomes achieved. Higher pressures tend to result in increased impact energies of the shots, impacting the depth of the induced compressive layer within the material. However, this comes with a caveat; excessively high pressures can lead to undesirable surface damage or insufficient coverage of the peened area.
Notably, the velocity of the shots also is crucial. An optimal shot velocity facilitates better coverage and an even distribution of stress across the surface of the substrate. Striking a balance between pressure and velocity is vital.
"Achieving a fine-tuned setting of both pressure and velocity factors allows manufacturers to optimize the strength properties of materials."
Coverage and Intensity Metrics
Coverage and intensity metrics dictate how well the surface is treated by the shot peening process. Coverage percentage refers to the fraction of the surface area that is impacted by the shots. Generally, a coverage level of 100% is the target, meaning every part of the surface receives adequate treatment. Insufficient coverage can result in weak spots, undermining the benefits of the process.
On the other hand, intensity metrics gauge the force of impact from the shots on the surface. It can be measured in terms of Almen intensity, which quantifies the kinetic energy imparted during peening. Higher intensity can enhance fatigue life but must be balanced against the risk of over-peening, which may lead to microstructural damage in the material.
In summary, optimizing the pressure, velocity, coverage, and intensity metrics is paramount in the shot peening process. These parameters must be researched and validated based on the specific application and material in use, ensuring that components achieve their expected performance while maintaining long-term reliability. Understanding and applying these insights will facilitate better industry practices, ultimately leading to improved product quality.
Technological Advances in Shot Peening
Technological advancements have significantly transformed the field of shot peening, enhancing both efficacy and precision. The integration of modern technology has improved the ability to control the peening process, resulting in better material performance and consistency. Furthermore, technological innovations streamline operations, making shot peening more accessible to a wider range of industries. Companies can gain greater control over parameters such as intensity, coverage, and the distribution of shots. These advances not only lead to improvements in quality but also boost the overall efficiency of production processes.
Automation and Control Systems
Automation in shot peening involves the use of advanced machinery and robotics to perform peening operations with minimal human intervention. This level of mechanization brings various advantages, such as increased productivity and decreased variability in outcomes. Automated systems can monitor parameters in real-time, such as velocity and impact angle, which allows for a more consistent application of shot peening across multiple parts.
Moreover, control systems facilitate data collection and analysis during the peening process. For example, sensors can track key parameters and feed this information into a central database. From there, operators can make adjustments as necessary without interrupting the process. This capacity for continuous monitoring ultimately extends the life of the machinery and improves safety. Benefits of automation include:
- Consistency: Automated systems reduce variance in the peening process, leading to more uniform results.
- Efficiency: Increased speed and repeatability minimizes labor costs and time.
- Data-Driven Decisions: Enhanced analytics allow for informed decision-making based on historical data and patterns.
Directional Peening Techniques
Directional peening techniques involve the strategic application of shots at specific angles to optimize the peening effect on parts. This advancement allows engineers to tailor the shot peening process to meet particular material specifications or design requirements. Employing directional peening can enhance fatigue resistance by creating a beneficial compressive stress profile in the targeted areas.
The benefits of these techniques include:
- Targeted Treatment: Focusing energy on specific areas can lead to improved performance in high-stress zones.
- Versatility: Different materials and shapes can benefit from customizable approaches, aligning the peening process with the part's unique needs.
- Quality Control: By systematically directing the shot flow, it becomes easier to monitor and control results, thus maintaining high quality in the finished products.
The future of shot peening lies in its ability to adapt to evolving material applications and industry demands through technological advancements.
Overall, the technological advancements in shot peening are not merely trends; they represent significant contributions to manufacturing and material science. As industries continue to evolve, both automation and specialized techniques will play vital roles in enhancing shot peening outcomes.
Quality Control in Shot Peening
Quality control in shot peening is crucial as it ensures the effectiveness and consistency of the process. The aim is to maintain high standards, which directly influences the performance and longevity of treated materials. By implementing stringent quality control measures, various industries can mitigate risks associated with material failure, thereby enhancing safety and reliability.
There are several specific elements that need attention when discussing quality control in shot peening. Firstly, monitoring the parameters of the peening process, such as the intensity and coverage, is vital. Parameters directly affect the outcome of the treatment, influencing factors like surface hardness and residual stress patterns in materials. Secondly, ensuring that the shots used are of appropriate material properties is necessary. This includes checking for size, shape, and hardness, all of which can impact the efficiency of the peening process.
Moreover, regular training for personnel involved in shot peening is a key aspect that should not be overlooked. Knowledgeable staff can better control the process, recognize potential issues, and implement corrective actions effectively.
Benefits derived from robust quality control can be numerous. Key benefits include:
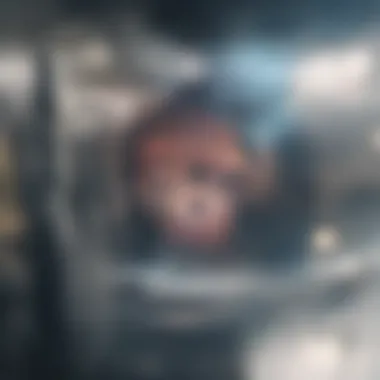
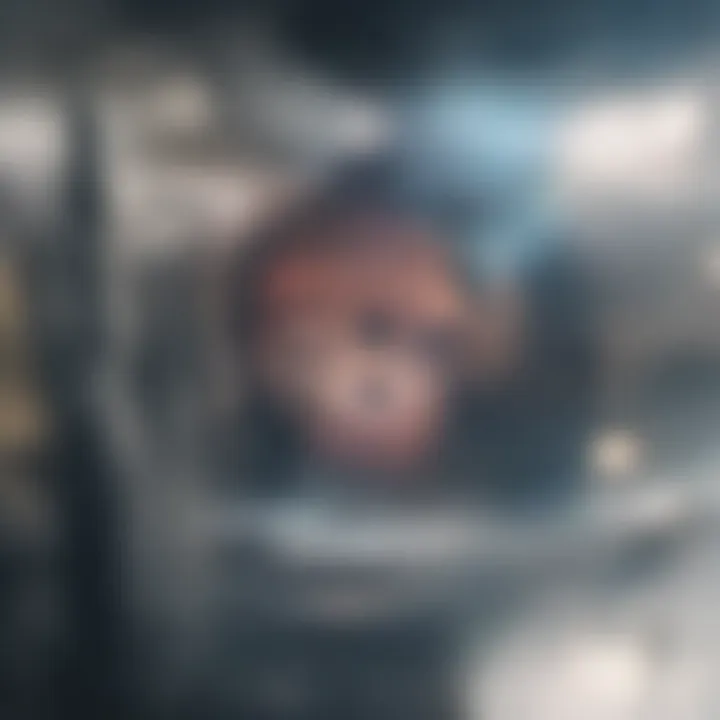
- Increased Material Longevity: Ensuring that the material properties are optimized leads to less frequent failures.
- Cost Effects: Quality assurance reduces the need for rework and replacements, saving costs in the long term.
Inspection Methods
Inspection methods in shot peening play a significant role in the quality assurance process. Various techniques can be applied to evaluate both the process and the results. One commonly used method is visual inspection, where operators assess the surface condition after treatment for any visible defects or inconsistencies. This method is important yet may not capture all nuances, hence often it is supplemented with more advanced techniques.
Additionally, other methods include:
- Optical Microscopy: To examine surface characteristics at a micro-level, optical microscopy can reveal issues that may not be visible to the naked eye.
- Residual Stress Measurement: Measuring residual stress using techniques such as X-ray diffraction or contour method is essential in determining the effectiveness of shot peening.
- Hardness Testing: Conducting hardness tests ensures that the desired material properties have been achieved post-treatment.
Together, these methods create a comprehensive inspection framework that enhances the reliability of shot peening results.
Standardization Practices
Standardization practices are an integral part of maintaining quality control in shot peening. They involve establishing uniform guidelines, which help in ensuring consistency across different processes and applications. Standardization is about creating a common understanding of what performance and quality mean in shot peening, which can also aid in training new personnel.
Some important standardization practices include:
- Development of Specifications: Establishing clear specifications for materials and processes to be used in shot peening helps in maintaining uniformity in results across applications.
- Regular Audits: Implementing routine internal and external audits aids in verifying that procedures are being followed and standards maintained.
- Documentation and Reporting: Keeping detailed records of processes, inspections, and outcomes allows for better accountability and traceability, which is vital for quality assurance.
In addition, aligning with industry-wide standards and certifications is beneficial. Organizations that implement ISO standards related to shot peening demonstrate a commitment to ongoing improvement and reliability. Thus, standardization not only enhances quality but also builds trust with clients and within sectors that rely on this technology.
Regulatory and Safety Considerations
The importance of regulatory and safety considerations in shot peening cannot be overlooked. Understanding the implications of this process helps ensure that practitioners adhere to essential guidelines while promoting the efficiency and safety of operations. These considerations encompass both environmental impacts and worker safety protocols, which are critical for sustainable practices in industries utilizing shot peening.
Environmental Impact
Shot peening generates certain by-products and waste materials that can affect the environment. It is necessary for industries to assess these impacts and comply with applicable regulations.
Key factors include:
- Waste Management: The process may produce spent materials that require proper disposal. Industries must follow local regulations regarding waste management to avoid harming the environment or violating laws.
- Air Quality Control: Techniques like dry peening can produce airborne particles. It's crucial for facilities to implement effective air filtration systems to minimize emissions and adhere to environmental protection standards.
By focusing on these elements, companies can contribute to a cleaner environment and promote responsible practices in shot peening operations.
Worker Safety Protocols
Worker safety is paramount in the shot peening process. Inherent risks, such as exposure to noise, flying projectiles, and hazardous materials, necessitate strict safety protocols.
Some key safety protocols include:
- Personal Protective Equipment (PPE): Operators must wear appropriate PPE, including eye protection, earplugs, and gloves. This mitigates the risk of injury from projectiles or excessive noise.
- Training Programs: Staff must receive training in machine operation and safety protocols. Education on the hazards associated with shot peening contributes significantly to workplace safety.
- Regular Inspections: Ensuring that equipment undergoes regular inspections can prevent malfunctions and accidents. This promotes a safer working environment.
Implementing these safety measures not only protects workers but also enhances operational efficiency within the shot peening domain. By fostering a culture of safety, organizations can minimize risks and promote a responsible work environment.
Future Directions for Shot Peening Research
The future of shot peening research is a critical component of its ongoing evolution. As industries demand higher performance materials, understanding and enhancing the effectiveness of shot peening becomes paramount. This area of research holds significant promise for both practical applications and theoretical advancements. New insights can lead to the development of superior materials and optimized peening processes.
Exploring New Materials
New materials are at the forefront of shot peening research. The investigation of advanced alloys, composites, and surface treatments can provide substantial benefits. For instance, materials with enhanced toughness and fatigue resistance can directly affect the longevity of components in high-stress environments. Understanding how these materials behave during the shot peening process is vital.
- Improved alloys and composites may require different shot materials or sizes.
- The goal is to maximize surface compressive stress while minimizing microstructural damage.
- Analyzing the response of new materials under various peening conditions can lead to tailored processes.
"Innovations in material science open new avenues for shot peening applications, which cannot be overlooked."
As researchers experiment with these materials, they can establish best practices that not only advance efficacy but also contribute to the sustainability of the processes involved. The adaptive nature of shot peening to accommodate new materials will enhance overall performance while potentially reducing costs.
Advanced Analytical Techniques
Another significant area of future research is the integration of advanced analytical techniques into shot peening processes. As technology progresses, tools for analyzing the effects of shot peening on materials also evolve. These techniques can provide deeper insights into microstructural changes and material performance.
- Techniques like X-ray diffraction and electron microscopy can reveal critical data about internal stresses and material structure post-peening.
- Moreover, automated systems can facilitate real-time monitoring and adjustments during the peening process. This ensures that the parameters are optimized for the specific material in use.
- Computational modeling and simulation tools can predict outcomes, allowing for more controlled experiments and efficient design.
Incorporating these advanced analytical techniques can reshape the future of shot peening. It allows researchers to draw more accurate conclusions, leading to innovations in both theory and practical applications. The combination of exploring new materials and employing advanced techniques will define the future landscape of shot peening research.