In-Depth Insights on Thermal Evaporation Techniques
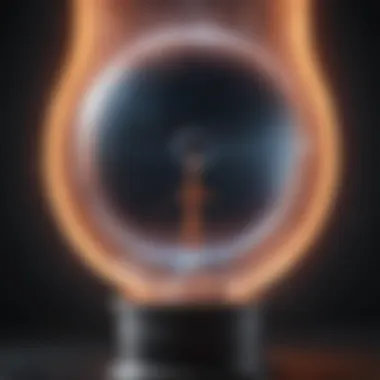
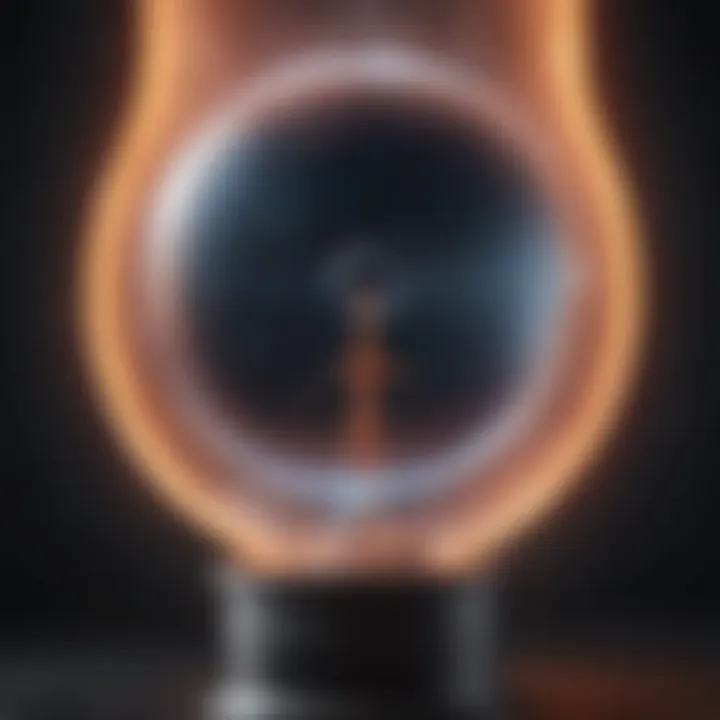
Intro
Thermal evaporation is a fundamental physical process employed in the deposition of thin films on various substrates. This method leverages heat to vaporize a solid material, subsequently allowing vapors to condense onto surfaces, thus forming uniform layers. The significance of thermal evaporation extends across multiple sectors, such as electronics, optics, and nanotechnology, making it crucial for advancements in material science. As professionals in the field explore innovations and applications, understanding this technique is paramount.
In this article, we will dissect the principles of thermal evaporation, examine its applications, and highlight the latest innovations shaping its future. We will also examine the challenges encountered by researchers and industries employing this technique. This composition serves as both an informative resource and a backdrop for discourse among students, educators, and specialists.
Intro to Thermal Evaporation
Thermal evaporation is a significant process within material science. This technique plays an essential role in various fields such as electronics, optics, and energy production. The core of thermal evaporation lies in its ability to produce thin films that are critical in modern technology. These films serve multiple functionalities, from simple protective coatings to complex layers used in semiconductors. Individuals involved in research and development often rely on this method to refine materials for specific applications.
The importance of understanding thermal evaporation cannot be overstated. Comprehending the fundamental principles and mechanisms behind this process allows professionals and researchers to leverage it effectively for innovative solutions. Recognizing the limitations and advantages of different methods is equally crucial for optimizing the performance of thermal evaporation-based designs.
Definition and Core Concepts
Thermal evaporation refers to the process of transforming a solid or liquid material into vapor through thermal energy. This vapor then condenses onto a substrate, forming a thin film. Key concepts in thermal evaporation include:
- Evaporation Rate: This is the measure of how much material transforms into vapor per unit time. It is influenced by temperature, pressure, and surface area.
- Substrate: The surface onto which the vapor condenses, which can be of various materials, such as glass or silicon.
- Heat Sources: Different heating methods, like resistive heating or electron beam heating, are used to achieve the necessary temperature for evaporation.
Understanding these concepts enhances one’s grasp on how to control deposition rates and film quality.
Historical Development
The journey of thermal evaporation dates back to the early 20th century. The method has evolved significantly since its inception. Initially, thermal evaporation was a rudimentary process, with limited control over the deposition parameters. Early applications included coatings for optical elements, where precise thin films were necessary.
As the demand for advanced materials grew, researchers developed more sophisticated equipment, enhancing the process's efficiency and precision. By the mid-20th century, thermal evaporation found vital applications in electronics, particularly in the fabrication of semiconductors. The introduction of tools such as vacuum chambers allowed for a controlled environment, improving the quality of the evaporated films.
Today, thermal evaporation remains integral to technology. Continuous advancements and research focus on improving throughput and sustainability, ensuring its relevance in a rapidly changing industrial landscape.
"Understanding the historical context of thermal evaporation allows for greater appreciation of its current innovations and future potential."
The Physical Principles of Thermal Evaporation
Understanding the physical principles of thermal evaporation is essential to grasp how this technique operates and its implications across various applications. Thermal evaporation relies on the fundamental laws of thermodynamics and kinetic theory. This section discusses key concepts that elucidate the mechanics behind the process such as thermodynamics, the kinetics involved, and factors affecting evaporation rates.
Thermodynamic Foundations
The thermodynamic framework underpinning thermal evaporation begins with the concept of phase transitions. When a material is heated to a point where its molecules gain sufficient energy, they transition from a solid or liquid phase to a gaseous state. This phase change is crucial as it dictates the behavior of the material when subjected to heat.
In thermal evaporation, energy is added primarily through heat applied by resistive heating or electron beams. The heat increases the kinetic energy of the atoms or molecules, allowing them to escape from the surface. The critical point here is that the material must reach its evaporation temperature, where the vapor pressure is significant enough to allow molecules to transition into gas.
The efficiency of this process is further influenced by the laws of thermodynamics, specifically the ideal gas law, which relates pressure, volume, and temperature in gas behavior. Understanding these principles helps researchers in optimizing conditions for desired outcomes in various applications.
Kinetics of Evaporation
Kinetics plays a vital role in thermal evaporation. The rate at which a substance evaporates is not constant and is influenced by several factors including the temperature of the substrate and the characteristics of the material itself. The molecular speed of the evaporating particles, along with their mean free path in the vapor phase, collectively determine the overall kinetics of evaporation.
An important aspect of kinetics is the concept of the sticking coefficient. This coefficient quantifies the likelihood that an evaporated atom or molecule will adhere to the substrate once it reaches the vapor surface. A higher sticking coefficient correlates with better film quality and uniformity, which is often a primary goal in applications like thin-film deposition.
Factors Influencing Evaporation Rate
Multiple external and internal factors influence the evaporation rate, shaping the outcomes of thermal evaporation. Here, we emphasize the three main factors: temperature, pressure, and surface area.
Temperature
Temperature is arguably the most significant factor in the evaporation process. Higher temperatures increase the kinetic energy of molecules, which accelerates evaporation. The character of the material also affects how temperature influences its evaporation rate. Higher temperatures tend to enhance the vapor pressure of the material significantly, leading to a rapid increase in the rate of evaporation. However, if the temperature exceeds the material’s thermal stability limit, it can lead to unwanted degradation, emphasizing the need for careful temperature management in processes.
Pressure
Pressure reciprocally impacts evaporation rates. In a vacuum setting, lower pressure enables molecules to escape more easily from the surface since the opposing pressure from surrounding molecules is minimal. The relationship between pressure and evaporation plays a critical role in many applications, especially in environments like microelectronics where precise deposition is required. But boosting pressure can also condense vapor back to liquid, reducing overall efficiency.
Surface Area
Surface area directly correlates with the rate of evaporation. Increased surface area provides more opportunity for molecules to escape into the vapor phase. For instance, materials deposited in thin films have a larger effective surface area compared to bulk materials, which promotes a more rapid evaporation rate. Using substrates engineered for optimal surface area can lead to better thin film characteristics and faster manufacturing processes.
In summary, comprehending these principles not only aids in enhancing the practical applications of thermal evaporation but also encourages innovation in various scientific fields where precise material manipulation is necessary.
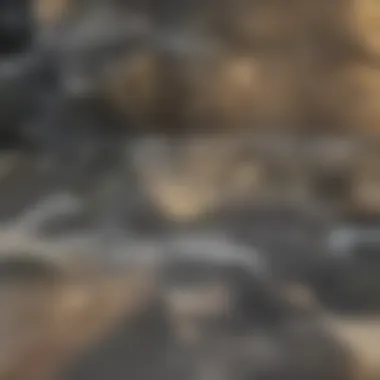
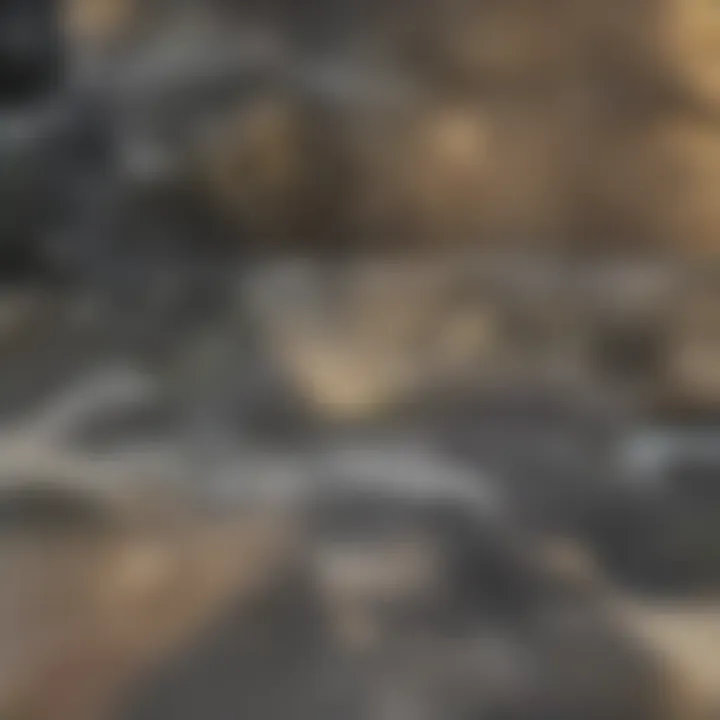
Methods for Implementing Thermal Evaporation
Understanding the methods used for implementing thermal evaporation is crucial for professionals and researchers. This section emphasizes the intricacies of the setup and equipment involved, as well as the actual evaporation process. Both elements are integral for achieving the desired outcomes in various applications. The methodologies dictate performance, efficiency, and scalability.
Equipment and Setup
The equipment for thermal evaporation typically consists of several key components. At the core, there is the evaporation chamber, where the materials are heated until they vaporize. This chamber is designed to create a controlled environment, minimizing contamination and allowing for precise depositions. The subsequent layers then condense onto substrates positioned at a specific distance, which is critical for ensuring uniform thickness.
Additionally, there are various supporting systems like vacuum pumps. Pumps are essential for maintaining the required low pressure within the chamber, enhancing the mean free path of the atoms or molecules involved in the deposition process. A good setup reduces scattering, leading to smoother films. Some systems are equipped with electronic control systems that enhance monitoring and accuracy.
The Evaporation Process
The process of thermal evaporation involves several stages, each contributing to the overall effectiveness.
Heating Sources
Heating sources are fundamental to the thermal evaporation process. Commonly used options include resistive heating, electron beam heating, and laser heating. Each method has distinct characteristics that influence efficiency and material compatibility.
Resistive heating involves passing an electric current through a metal filament or boat, causing it to heat up and subsequently vaporize materials placed above it. This method is notably beneficial for materials that require high temperatures, typically found in making thin films. However, it can be less effective for materials that are highly reflective.
Electron beam heating, on the other hand, generates high-energy electrons focused on a target material. This technique provides rapid heating and better control over the evaporation rate, suitable for high-purity applications. But, it also requires more complex equipment, which can add to overall costs.
The unique feature of laser heating is its precision; it allows for localized heating, minimizing thermal damage to surrounding materials. Nonetheless, the requirement for sophisticated gear can limit its widespread use.
Material Choices
Materials selected for thermal evaporation must fulfill certain criteria to ensure successful deposition. Commonly evaporated materials include metals like aluminum, gold, and silver, as well as some oxides. The key characteristic here is the material's ability to vaporize at the processing temperatures without decomposing.
Choosing materials with high reflectivity can pose challenges since they can lead to uneven deposition. Conversely, more absorbent materials provide uniform layers but may need careful handling due to their volatility.
A noteworthy feature of specific material choices is the potential for alloying. Options like titanium and tungsten are often combined to enhance certain properties, such as hardness or corrosion resistance. The choice of materials directly affects the performance of the final products, which is why careful consideration is necessary in the planning phase.
In summary, methods for implementing thermal evaporation play a definitive role in the success of any related application. Understanding the intricacies of equipment, the nuances of the evaporation process, and the implications of material choices are essential for optimizing outcomes.
Applications of Thermal Evaporation
The applications of thermal evaporation are vast and play a significant role in various scientific and industrial fields. This method's ability to produce thin films of materials is fundamental in areas like electronics, optics, and renewable energy. Each application exhibits unique characteristics and requirements, which dictate the materials used and the conditions under which deposition occurs. Understanding these applications helps to appreciate the complexities and efficiencies of thermal evaporation as a technique.
Thin Film Deposition
Thin film deposition is perhaps the most recognized application of thermal evaporation. In this process, a material is vaporized in a vacuum and then condenses onto a substrate, thus forming a thin film. These films are crucial in semiconductor industries where layers of materials must be precise and uniform for device functionality. The thin films can vary in thickness, composition, and properties depending on the material used and the conditions under which the evaporation occurred.
- Key Benefits:
- Allows precise control over thickness, enabling fine-tuning of electrical, optical, and mechanical properties.
- Enables the production of complex layered structures essential for modern microelectronics.
Microelectronic Fabrication
In microelectronics, thermal evaporation is vital for creating various components such as integrated circuits and sensors. The deposition of metals like aluminum, gold, and silver forms the interconnects essential for chip functionality. Thermal evaporation is favored for its capability to create high purity layers, which is crucial for the performance of electronic components.
- Considerations:
- Substrate materials must withstand the temperature during deposition without degrading.
- Uniformity in deposition is crucial to avoid defects in electronic devices.
Solar Cell Technologies
Solar technology increasingly relies on thermal evaporation for producing photovoltaic cells, particularly thin-film solar cells. Materials like cadmium telluride can be deposited efficiently using thermal evaporation techniques. This application helps in reducing material usage while maintaining efficiency, which is essential to the sustainability of solar technology.
- Significance:
- Contributes to the reduction of manufacturing costs in solar cells.
- Enhances the performance of solar panels through the creation of effective light-absorbing layers.
Optical Coatings
Another important application of thermal evaporation is in the production of optical coatings. This includes anti-reflective coatings, reflective mirrors, and filters. By carefully controlling the evaporation process, layers can be engineered to achieve specific optical characteristics, such as reflectance and transmittance, tailored for various applications ranging from glasses to high-end optical instruments.
- Advantages:
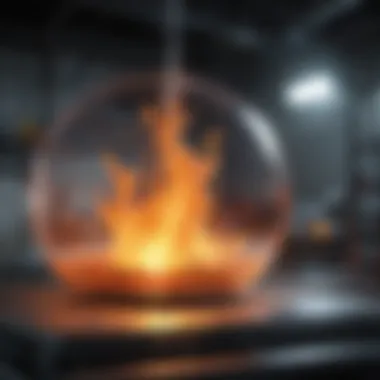
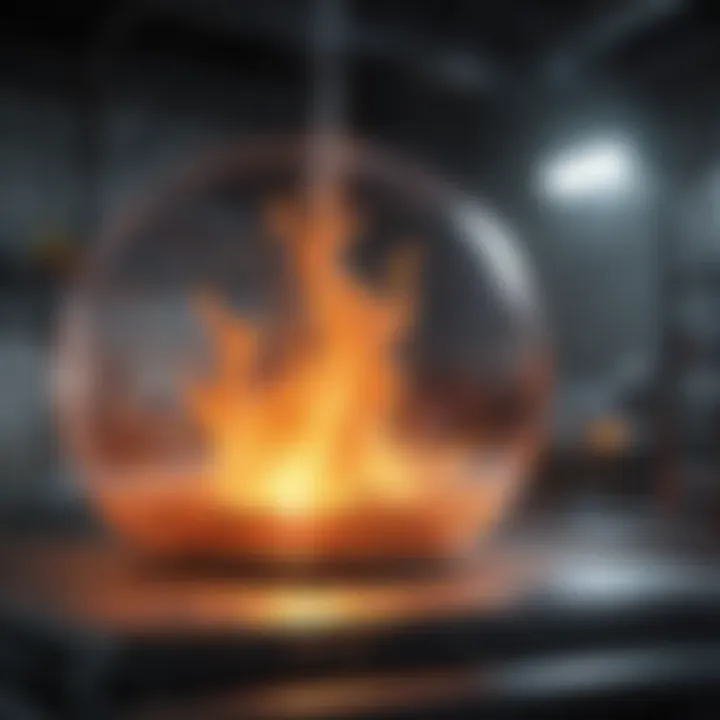
- Produces highly uniform and consistent coatings which are critical in optical performance.
- Adaptable to a variety of substrate materials and shapes, offering flexibility in design.
Thermal evaporation serves not just in manufacturing but enhances technological advancements across numerous disciplines, underscoring its versatility and relevance in modern materials science.
Comparative Techniques in Evaporation
Comparative techniques in evaporation are vital for understanding different methodologies and their suitability for various applications. In the realm of thin film technologies, the choice of technique can significantly affect the properties of the finished product. This section highlights two prominent methods: Physical Vapor Deposition (PVD) and Chemical Vapor Deposition (CVD). Both techniques have unique characteristics that meet specific requirements in material science and technology.
Physical Vapor Deposition (PVD)
Physical Vapor Deposition involves the physical transformation of a material into vapor, which then condenses on a substrate to form a thin film. This process typically uses sources such as thermal evaporation or sputtering. The thickness and quality of the deposited films are influenced by the control over deposition parameters, such as temperature and vapor pressure.
PVD is particularly valued for its versatility and effectiveness in producing high-purity films with good adhesion. Industries widely adopt it for applications like semiconductor manufacturing, optics, and decorative coatings. Key benefits of PVD include:
- Material Efficiency: PVD techniques often have higher deposition rates compared to other methods. Less waste is generated, making them more sustainable.
- Control Over Film Properties: The ability to adjust parameters allows for tuning of film properties such as refractive index, hardness, and conductivity.
- Environmentally Friendly: Many PVD processes avoid using hazardous chemicals, making them safer for operators and the environment.
Despite its advantages, PVD does have limitations. It usually requires vacuum conditions, which can complicate the setup. Additionally, for certain materials, achieving uniform thickness can be challenging.
Chemical Vapor Deposition ()
Chemical Vapor Deposition is a gas-phase process where chemical reactions occur on or near the substrate surface. Gaseous reactants are transported to the substrate, where they react, forming a solid thin film. This method can produce high-quality films with excellent uniformity and conformality over complex topographies.
CVD is extensively used in the production of semiconductor devices, solar cells, and in the creation of advanced coatings. Some notable benefits include:
- Uniform Coatings: CVD processes are particularly effective for depositing uniform films over intricate surfaces, which is crucial for microelectronics and advanced optical systems.
- High Film Quality: The films deposited via CVD often exhibit superior structural and electronic properties, making them desirable for high-performance applications.
- Scalability: CVD techniques can be scaled for production, allowing for high throughput in industrial settings.
However, CVD also comes with drawbacks. The process can involve toxic, corrosive, or expensive precursors. Controlling the deposition rate may require sophisticated equipment. Additionally, the heat generated during the process can limit the materials that can be used.
"Understanding the differences between PVD and CVD is crucial for selecting the appropriate method for specific applications. Each technique offers distinct advantages and hurdles that must be considered."
Challenges in Thermal Evaporation
Understanding the challenges in thermal evaporation is crucial for advancing research and application in this field. It encompasses various elements that can significantly affect the efficiency and effectiveness of the evaporation process. This section will delve into material limitations, uniformity, thickness control, and the associated costs, providing insights that can aid in refining techniques and optimizing results.
Material Limitations
Material limitations present a significant hurdle in thermal evaporation. Each material has unique properties, such as melting point and vapor pressure, that influence its suitability for evaporation. For instance, high melting point materials may not evaporate efficiently under typical thermal conditions. Additionally, some materials are prone to degradation when subjected to high temperatures, limiting their application in thin film technologies. Researchers must conduct thorough thermodynamic assessments of materials to determine their viability.
"Choosing the right material is as critical as the evaporation method itself."
To address these material challenges, a growing emphasis is placed on developing new composites that can withstand the conditions required for thermal evaporation. Innovations in material science aim to produce alloys and compounds that maintain integrity while achieving desired evaporation rates.
Uniformity and Thickness Control
Achieving uniform thickness in deposited layers is another challenge inherent in thermal evaporation. Non-uniform deposits can lead to performance inconsistencies, especially in applications like coatings for optics or microelectronics fabrication. Factors such as source geometry, substrate positioning, and evaporation rate can all influence the uniformity of the deposited layer. In many cases, monitoring systems are essential to ensure consistency.
- Key techniques for ensuring uniform thickness:
- Implementing rotating substrates.
- Utilizing multiple source configurations.
- Employing in-situ measurement tools to gauge thickness continuously.
The technology around thickness monitoring has advanced, enabling more precise control over these critical factors.
Costs and Equipment Maintenance
The financial implications of thermal evaporation cannot be overlooked. Initial setup costs for high-quality evaporation equipment can be substantial, and ongoing maintenance further adds to the expense. Therefore, understanding the operational costs associated with thermal evaporation is vital for institutions and companies.
- Primary cost considerations:
- Equipment purchase and installation costs.
- Regular maintenance and potential downtime.
- Necessity of specialized operating personnel.
Minimizing costs requires balancing performance and longevity. Regular maintenance schedules and training for personnel can reduce unplanned downtime and ensure smooth operations. Institutions must also evaluate the cost-benefit ratio of using durable, high-end equipment versus relying on less costly alternatives that may need frequent replacement.
Each challenge in thermal evaporation calls for ongoing research and innovation. By recognizing and addressing these issues, practitioners can harness thermal evaporation more effectively, pushing the boundaries of what is achievable in material science and related fields.
Recent Innovations in Thermal Evaporation
Recent developments in thermal evaporation have revolutionized the landscapes of material science and engineering. Innovations in this space play a vital role in enhancing the efficiency, precision, and sustainability of coating processes. As industries seek to improve product performance while minimizing environmental impact, the evolution of thermal evaporation techniques proves to be indispensable.
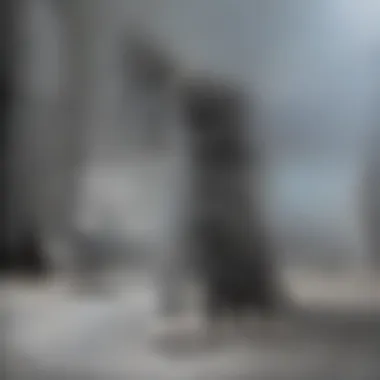
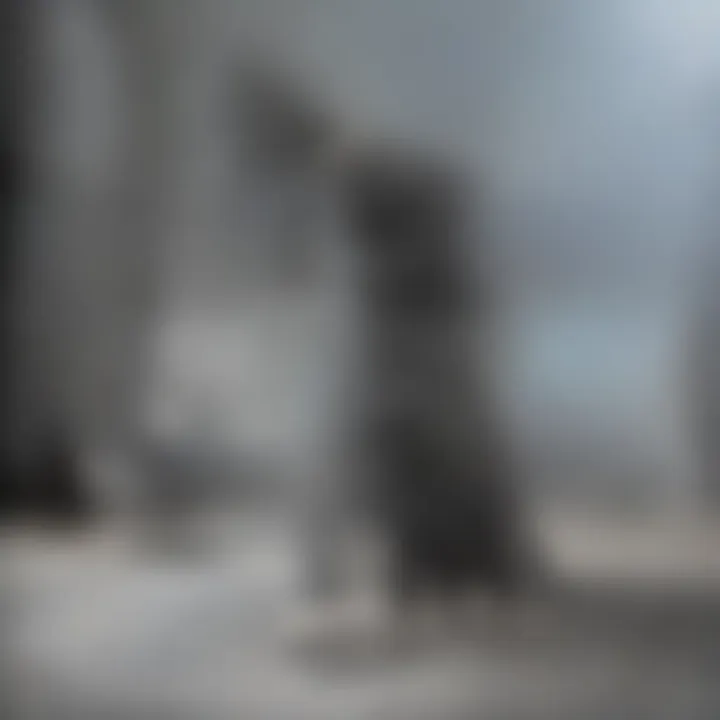
Automation and Control Systems
The integration of automation into thermal evaporation processes has profoundly increased production efficiency and quality control. Automated systems facilitate precise monitoring and regulation of deposition parameters, such as temperature and pressure. This precision ensures a more uniform coating across various substrates. Moreover, automation minimizes human error and allows for real-time adjustments during production. An example is the implementation of programmable logic controllers (PLCs) that streamline operations, enhancing both productivity and reproducibility.
Some critical benefits of automation include:
- Increased deposition rate consistency
- Reduction in labor costs
- Enhanced data collection for future improvements
Automation in thermal evaporation also helps companies adapt to rapid production changes, an increasingly important factor in competitive markets.
Nanomaterials and Coating Techniques
The rise of nanotechnology has led to innovative coating techniques that leverage the properties of nanomaterials. Nanostructured thin films exhibit unique characteristics, including increased strength, enhanced electrical conductivity, and improved optical properties. Thermal evaporation techniques are adapted to handle these materials, providing adequate control over film thickness and layering.
For instance, the ability to layer various nanomaterials leads to multifunctional coatings which can be utilized in various applications ranging from electronics to medicine. These advancements position thermal evaporation at the forefront of nanotechnology, driving research and development in diverse fields.
Notable developments include:
- Development of new precursors for improved evaporation
- Techniques for layering different nanomaterials to enhance performance
- Increased research in biocompatible coatings for medical devices
This innovation not only fosters advancements in existing technologies but also opens new avenues of research across multiple disciplines.
Sustainable Practices
Sustainability is a pressing concern across industries, and thermal evaporation is no exception. Recent innovations focus on reducing energy consumption and waste materials in the evaporation process. Efforts include the development of eco-friendly materials and the optimization of thermal evaporation setups for better energy efficiency.
Specific sustainable practices include:
- Utilizing renewable energy sources to power evaporation systems
- Recycling and repurposing materials to limit waste
- Employing materials that exhibit lower environmental impact
The shift towards sustainable practices aligns with global initiatives to reduce carbon footprints. Implementing these innovations can lead to cost savings in the long run while contributing positively to environmental health.
"The advancements in thermal evaporation not only pave the way for better product performance but also address critical environmental challenges."
Future Directions of Thermal Evaporation Research
The topic of future directions in thermal evaporation research is of paramount importance. As the need for advanced materials and precise fabrication techniques intensifies, the methodologies surrounding thermal evaporation are evolving. The integration of novel materials, automation advancements, and sustainable practices will define the next phase of this field.
Emerging Trends in Applications
The applications of thermal evaporation are rapidly expanding as technology progresses. Current trends include the development of multifunctional coatings that enhance performance in diverse environments. Researchers explore coatings applicable in biomedical devices, where biocompatibility is crucial. Additionally, flexible electronics have emerged as a significant trend. With the rise of wearable technology, thermal evaporation is being adapted to create thin, flexible layers that can conform to various shapes.
Other trends focus on the use of nanomaterials. As researchers investigate the properties of nanostructured materials, the demand for fabrication techniques like thermal evaporation only increases.
- Key trends in applications include:
- Development of biomedical coatings
- Advancements in flexible electronics
- Exploration of nanomaterials for unique properties
Integration with Other Technologies
Integration with other technologies provides a new horizon for thermal evaporation. For instance, combining thermal evaporation with additive manufacturing opens avenues for producing complex structures that were previously unattainable. This hybrid approach can create intricate designs while leveraging the high-quality deposition benefits of thermal evaporation.
Additionally, advancements in machine learning and artificial intelligence are paving the way for optimized process control. These technologies can analyze data in real-time, thereby improving efficiency and quality in material deposition. Such integration will ultimately enhance the accuracy and repeatability of thermal evaporation processes.
"The intersection of thermal evaporation with other modern technological advancements could revolutionize material science."
In summary, the future of thermal evaporation research is intertwined with emerging application trends and integrations that embrace technological innovations. As fields continue to blend, the impacts of thermal evaporation will undoubtedly expand, solidifying its role in cutting-edge research and applications.
Culmination
The conclusion underscores the essential role of thermal evaporation in modern science and engineering. It encapsulates the key insights presented throughout the article, thereby reinforcing the significance of this technique in numerous applications. Thermal evaporation has established itself not only as a fundamental process in material science but also as a critical facilitator in areas such as electronics, optics, and renewable energy.
Summary of Key Insights
In this article, we explored the principles and methods of thermal evaporation. Here are some of the major highlights:
- Definition and Core Concepts: Thermal evaporation is a process where materials transition from a solid-state to a vapor, then condense onto a substrate to form thin films. This is governed by established thermodynamic principles.
- Applications: The versatility of thermal evaporation is exhibited across various fields, such as thin film deposition, microelectronics, solar technology, and optical coatings. Each application demonstrates how this technique can be applied creatively and effectively.
- Innovations: Recent advancements focus on automation, the use of nanomaterials, and the adoption of sustainable practices, indicating a robust future for thermal evaporation techniques.
- Challenges: Despite its advantages, challenges such as material limitations, uniformity issues, and equipment costs must be addressed to enhance efficiency and applicability.
“Understanding thermal evaporation is crucial for both researchers and practitioners who strive to remain at the forefront of technology development.”
Final Thoughts on Thermal Evaporation's Role
Thermal evaporation is poised to continue playing a significant role in both academia and industry. As technology advances, the need for precision and efficiency in producing thin films will only increase. Understanding the underlying principles and staying abreast of innovations will enable professionals to tackle the challenges inherent in this process. Moreover, integrating thermal evaporation with other technologies can lead to groundbreaking developments in various domains.