Surface Roughness Measurement: Techniques and Implications
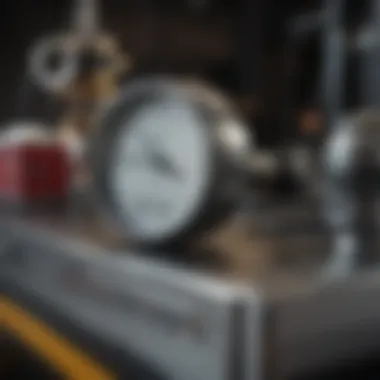
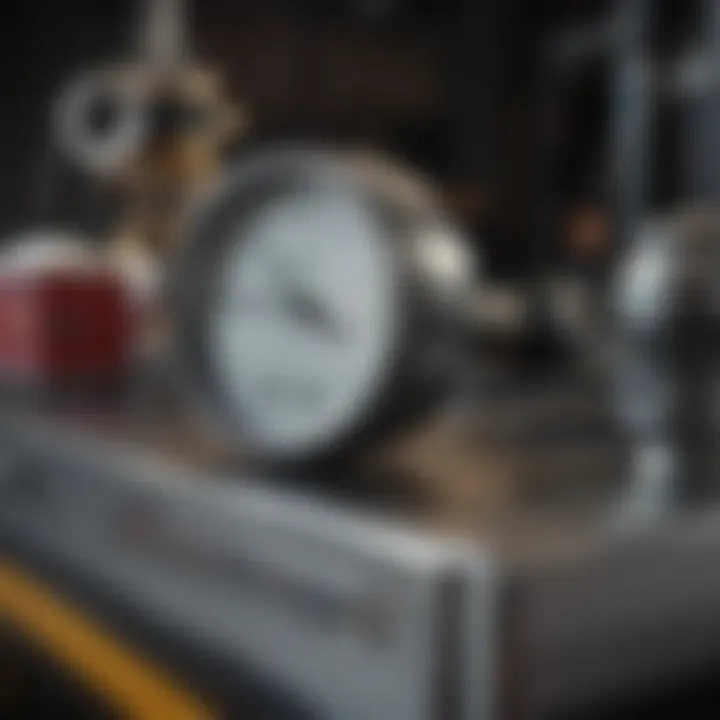
Intro
Surface roughness measurement plays a crucial role in a wide range of scientific and industrial fields. It serves as a key factor influencing material performance, durability, and overall functionality. From precision engineering to materials science, understanding the intricacies of surface texture shapes many decisions in production processes and quality control.
Though it may seem like a niche topic, the implications of surface roughness extend far and wide. This section takes a closer look at the various techniques that help measure this parameter, emphasizing the critical findings and the repercussions that arise from them.
Prelims to Surface Roughness
The measurement of surface roughness plays a pivotal role in a myriad of industries. It serves as a crucial determinant of how products will function, feel, and even wear over time. Understanding surface roughness is not just a checkmark on a technical specification sheet; it influences everything from product durability to manufacturing efficiency.
Defining Surface Roughness
Surface roughness refers to the irregularities or deviations in the texture of a surface. These variations may be small, yet they can significantly impact a material's performance. A smoother surface often means lower friction, which may enhance the lifespan of components that face regular wear, like gears or engine parts. On the other hand, some applications might require rough surfaces—like those used in adhesives—where increased texture aids in adhesion.
To put it simply, surface roughness is a measurement of deviation from the ideal geometry. It can be quantified in multiple ways, often using parameters like average roughness (Ra), root mean square roughness (Rq), and maximum peak height (Rz). These metrics allow engineers and material scientists to communicate the quality of a surface in a clear and quantifiable manner.
Importance in Various Fields
Manufacturing
In the manufacturing realm, surface roughness is non-negotiable. It affects the efficiency of machining processes as well as the functionality of finished products. For example, developing a cutting tool requires understanding the interplay between tool roughness and the material being cut. If the tool is too smooth, it may not grip the material properly, leading to slippage. Conversely, excessive roughness can create undesirable friction, harming tool longevity.
The key characteristic of manufacturing in relation to surface roughness is precision. When manufacturers measure surface texture accurately, it can optimize processes to ensure that parts fit together as intended, which reduces waste and increases quality control. Nevertheless, it’s a balancing act; manufacturing techniques can gear towards finer finishes, yet these often come with higher costs and longer lead times.
Metrology
Metrology, or the science of measurement, encompasses surface roughness evaluation as a vital aspect of ensuring quality and compliance in various sectors. Accurate measurement tools and methodologies are essential to quantify surface characteristics reliably.
The key aspect here is reliability. Metrology standards dictate how measurements should be conducted and what tolerances are acceptable. In this way, discrepancies in measurements can reveal underlying issues in manufacturing. For instance, if one batch of components consistently shows higher roughness than the previous ones, it could signal a mechanical fault in the production line.
However, marking its unique feature, metrology often utilizes sophisticated equipment that can be costly to maintain and operate. This can be a hurdle for smaller firms looking to meet high standards without shoulderig a heavy financial burden.
Material Science
Surface roughness is undeniably linked to material science, as it directly influences how materials interact with their environment. Be it determining how coatings adhere to a surface or assessing the corrosion resistance of a material, surface roughness offers critical insights.
The characteristic that marks the relationship between material science and surface roughness is functionality. Materials like metals may require different roughness parameters compared to plastics, all depending on the intended use.
For example, a roughened surface on a medical implant might help in tissue integration, whereas a smoother surface may be required in automotive applications to reduce friction. Yet, a drawback is that the roughness might also lead to issues such as stress concentrations, potentially impacting durability if not carefully managed.
In sum, understanding surface roughness is integral to enhancing material performance, ensuring product reliability, and optimizing manufacturing processes across various fields.
Through a comprehensive grasp of these just-discussed elements, it becomes apparent how pivotal the measurement of surface roughness is in shaping industry standards and application efficacy.
Fundamentals of Surface Texture
Understanding surface texture is crucial in comprehending surface roughness measurement. Different factors come into play, impacting how surfaces interact with one another—be it in machinery, electronics, or even everyday items. Surfaces that appear smooth at a glance might have deep grooves and microscopic vibrations that can affect performance in significant ways. The nuances of texture define how surfaces behave regarding friction, adhesion, and wear, which can immensely influence material longevity and reliability.
Characterizing Surface Textures
Characterizing the various facets of surface textures allows for a better grasp of how they affect surface performance. The most critical aspects include roughness, waviness, and lay, each playing a significant role in the overall assessment.
Roughness
Roughness refers to the fine irregularities in a surface. It's primarily defined by the random deviations from the nominal surface. The distinctive characteristic of roughness is its scale; it typically involves small, closely spaced variations. This aspect makes roughness a vital focus since it contributes directly to frictional resistance. A rough surface can increase friction, which might be beneficial in some applications, like tire treads, but could spell disaster in precision components like bearings.
On the other hand, rough surfaces can also attract dirt and debris, leading to wear and premature failure. These are some of the disadvantages of high roughness, but understanding and measuring it enables industries to tailor surface finishes for specific applications.
Waviness
Waviness indicates the more pronounced and longer waves that occur on a surface—think of it as the broader, rippled characteristics compared to the minute details of roughness. Waviness is critical because it can affect the performance of interfaces in dynamic applications, such as seals or gaskets.
The advantage of considering waviness is that it can highlight systematic issues during manufacturing processes, like machine vibrations that could be corrected for better quality assurance. However, it might also represent an added complexity, as distinguishing between waviness and roughness requires precise measuring techniques and tools.
Lay
Lay describes the direction of the predominant surface pattern, often organized from the machining process (like grinding or milling). Understanding lay is essential in applications where fluid flow is a consideration. The direction in which a fluid flows can be highly influenced by the surface structure, thus impacting friction and erosion.
The unique aspect of lay lies in its ability to provide insights into the manufacturing processes used, thus serving as an indirect indicator of surface quality. While important, its consideration adds yet another layer to the already complex nature of surface roughness measurements.
The Role of Scale
Another fundamental aspect of understanding surface texture involves the scale of measurement. The scales are typically categorized into micro-scale and macro-scale, each presenting their own set of complexities and benefits in surface roughness assessment.
Micro-scale
Focusing on micro-scale measurements allows for an in-depth analysis of surface features ranging from sub-micrometer to several micrometers in height and width. This precision is beneficial for understanding phenomena like coating adhesion or the performance of micro-electromechanical systems (MEMS). The key characteristic here is the ability to evaluate fine details essential in high-tech industries.
However, measuring at a micro-scale also presents challenges, such as the limitations of various measurement methods that might not be able to capture the intricate features accurately. A thorough understanding of the tools and techniques is required to minimize errors in measurement and ensure reliable data.
Macro-scale
On the other hand, macro-scale evaluations look at larger surface features, often noticeable to the naked eye or measurable with standard tools. Macro-scale measurements can display broad trends in surface texture, which can be useful for quick assessments. It's often used in quality control processes or field applications.
However, while easier to conduct, macro-scale assessments can miss important details that might be critical for certain applications. Balancing the two scales can yield a thorough understanding of surface characteristics, guiding effective decision-making in various engineering or material science fields.
To summarize, grasping the fundamentals of surface texture—namely roughness, waviness, and lay, alongside understanding the role of micro and macro-scale measurements—forms the backbone of effective surface roughness assessments. Each aspect presents unique advantages and challenges that, when understood and utilized, can vastly improve material performance and product durability.
Measurement Techniques
In the realm of surface roughness measurement, the techniques employed play a pivotal role in defining the effectiveness of the assessment and the resulting implications for material performance. Understanding the specific methods can help practitioners choose the right approach depending on their needs. Measurement techniques can primarily be divided into contact and non-contact methods. Each has its own pros and cons, dictated by the nature of the material being measured, the precision required, and the environmental conditions present.
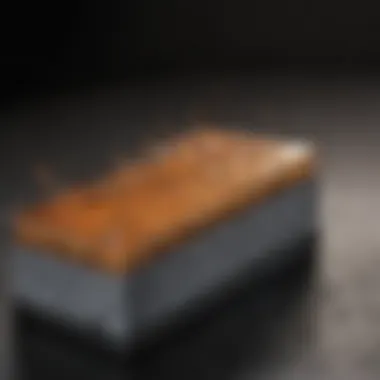
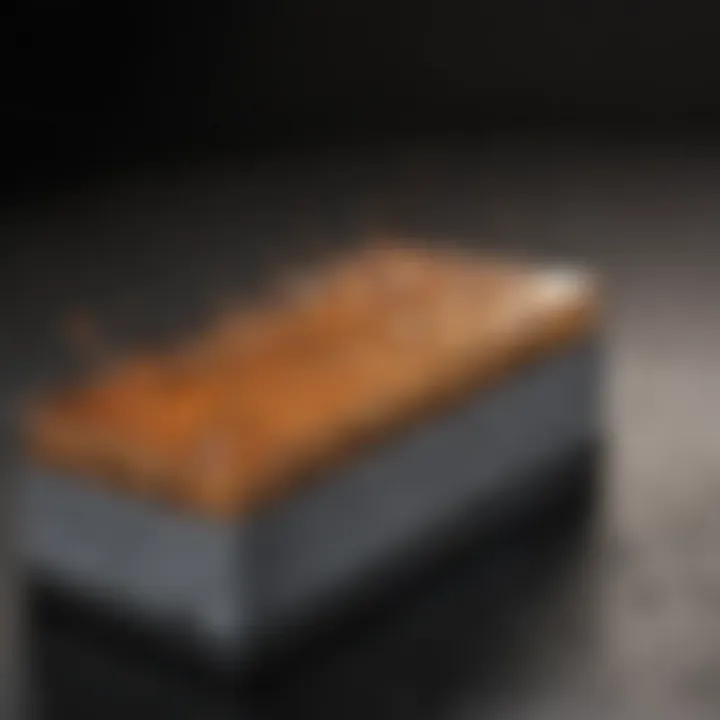
Contact Methods
Stylus Profilometry
Stylus profilometry is one of the cornerstone techniques in measuring surface roughness. This method involves dragging a fine stylus across the surface of a material and recording the vertical displacements as it moves. A key characteristic of stylus profilometry is its capability to deliver detailed surface profiles. This resolution enables analysts to obtain accurate readings of surface features, making it a favored choice for applications where minute details matter.
The unique feature of stylus profilometry lies in its simplicity and the wealth of data it can provide. It's not overly complex to set up, and the resulting data is generally straightforward to interpret. However, it's worth noting that this method can potentially damage softer materials, especially if the stylus pressure is not calibrated correctly. Consequently, while it provides excellent depth of information, practitioners must exercise caution regarding the type of materials they subject to this method.
Scanning Tunneling Microscopy
Scanning tunneling microscopy (STM) marks a significant advance in surface measurement techniques. This method shines in its ability to provide atomic-scale imaging of surfaces. The primary appeal of STM is its ability to visualize surfaces at an extremely high resolution, thus revealing not just roughness, but also electronic properties that are related to surface characteristics.
A standout feature of STM is that it does not require a physical contact with the surface, reducing the risk of damage significantly. Yet, this sophisticated technique comes with its challenges. STM is typically limited to conductive materials, which can restrict its applicability. Furthermore, the complexity of the setup and interpretation of the images can pose a hurdle for newcomers learning this technique.
Non-Contact Methods
Optical Techniques
Optical techniques have revolutionized surface roughness measurement by allowing the evaluation of surfaces without any physical contact. Utilizing laser beams or light to illuminate the surface, this approach captures reflections and determines roughness based on the light's behavior. A main benefit of optical methods is that they can assess larger areas quickly, making them ideal for production environments where speed is crucial.
The ability to minimize contact-related damage to the specimen adds to the appeal. However, challenges exist. Surface coatings, transparency, and reflectivity play significant roles in the accuracy of optical measurements, which necessitates careful consideration of the surface material being analyzed.
Laser Interferometry
Laser interferometry is yet another powerful non-contact method that relies on the interference patterns of light waves. By comparing the path length of multiple light beams, it can deduce very precise surface measurements. The high level of accuracy this technique offers makes it especially appealing for research facilities and quality control settings.
Interferometry's unique feature lies in its ability to achieve nanometer resolution, but the complexity of the equipment and the environment must be stable to achieve these results. External vibrations and air disturbances can disrupt the measurements significantly, making laser interferometry somewhat sensitive to its operational context.
Emerging Technologies
Atomic Force Microscopy
Atomic force microscopy (AFM) has carved its niche in the field of surface analysis by providing topographical maps at atomic resolution. AFM operates by scanning a sharp tip over the surface while measuring the forces between the tip and the sample. Its ability to measure a wide array of materials, including insulators, conductors, and biological samples, makes it immensely versatile.
A defining characteristic of AFM is its multifunctionality; different modes can be applied to measure specific properties such as magnetic or electric forces. However, like many high-end techniques, AFM requires a level of expertise and can be time-consuming due to the detailed imaging process.
3D Microscopy
3D microscopy methods, which allow for capturing and analyzing three-dimensional images of surface topographies, represent some of the most advanced measurement techniques available today. These methods help in visualizing and quantifying surfaces in a way that traditional 2D methods cannot. The ability to navigate through the layer of the surface opens doors for insights into complex surface structures.
Yet, the uniqueness of 3D microscopy comes at a cost. The systems often require significant investment and skill, limiting accessibility to larger laboratories or specialized research units. Furthermore, data management can be challenging due to the immense volume of information that 3D images can produce.
"Each method of surface roughness measurement carries its own strengths and limitations, thus presenting a rich tapestry of choices for professionals in various fields."
In sum, the exploration of measurement techniques underscores their essential roles in material characterization. Choice of method can significantly impact not only the data gathered but also the resulting actions taken in manufacturing, quality control, and research endeavors.
Analysis of Surface Roughness Data
In the realm of surface roughness measurement, data analysis serves as the backbone that transforms raw measurements into meaningful insights. Understanding this data is critical for delivering accurate evaluations of surface properties, which in turn influences the performance of materials in various applications. The data analysis process doesn't just compile statistics; it makes sense of the textures and irregularities that define how a material interacts with its environment.
Parameters for Measurement
The heart of surface roughness data analysis lies in its parameters—key metrics that quantitatively assess the texture of surfaces. Three pivotal parameters are Ra, Rz, and Rq. Each brings its own flavor to the table and reflects different aspects of surface profiles.
Ra
Ra, or Arithmetic Average Roughness, is perhaps the most well-known metric. It gauges the average deviation of the surface profile from its mean line over a specified length. This characteristic makes Ra an intuitive choice for many applications where general surface quality is assessed.
One unique feature of Ra is its simplicity. Even though it is popular, its limitations can be significant in certain contexts. For instance, it does not account for peak heights and valley depths distinctly, which can skew interpretations in cases where profiles display considerable height variations. Thus, its effectiveness depends largely on the nature of the material and the specific use case.
Rz
Rz, or Mean Roughness Depth, delves deeper into the texture by quantifying the average maximum peak-to-valley height within a sampling length. This parameter stands out for its sensitivity to extreme surface variations, making it beneficial when evaluating surfaces that must withstand high stress or wear.
The inclusion of Rz can be particularly advantageous when assessing surfaces meant for contact applications, as it provides a clearer picture of how surface features interact under load. However, like Ra, Rz also has its shortcomings. For complex surface geometries, relying solely on Rz could misguide engineers as it does not capture the subtle profiles that might be crucial to the surface's performance.
Rq
Rq, or Root Mean Square Roughness, rounds out the trio of primary parameters. It calculates the square root of the average of the squares of the deviations. This method gives greater weight to larger deviations, encapsulating surfaces that are not just rough but also those with notable peaks and troughs.
As such, Rq is particularly useful in advanced engineering applications, where microstructures play a pivotal role in determining material behavior. However, its complexity may pose a challenge for teams that prioritize straightforward interpretations, possibly making it less popular compared to Ra and Rz in broader discussions.
Statistical Methods
Data analysis wouldn’t be complete with statistical methods. Techniques like Histogram Analysis and Fourier Transform methods allow for a thorough understanding of the surface profile distributions, shaping how engineers approach material design and processing.
Histogram Analysis
Histogram analysis evaluates the distribution of surface roughness measurements, presenting the data in a graphical format. This portrayal assists in recognizing patterns or anomalies that might affect functionality. Key characteristics of this method include its intuitive visual outputs, which make it easy to identify ranges where roughness falls outside of expected values. This way, quick adjustments can be made in line with manufacturing specifications.
Although histogram analysis can be an effective tool, it can also fall short if the sample size is too small. A limited dataset may not accurately depict the surface attributes, leading to misleading conclusions about overall texture performance.
Fourier Transform Techniques
Fourier Transform Techniques come in handy for those looking to analyze surface profiles in a more detailed manner. This method transforms the surface data from the spatial domain to the frequency domain, allowing for a different kind of insight into the texture characteristics. In essence, it reveals how many different types of "textures" are present in a surface, influencing both how materials can perform and how they might wear over time.
The tremendous versatility of Fourier Transform methods lies in their ability to analyze complex surfaces and identify specific patterns or frequencies that might be critical for advanced material applications. However, the precision and depth of analysis comes at the cost of complexity. It demands a strong understanding of both the surface being measured and the mathematical underpinnings of the derived data—potentially a hurdle for some operators.
In summary, weaving through the analysis of surface roughness data isn’t merely about crunching numbers; rather, it’s about piecing together a comprehensive picture that can predict performance and inform design decisions. By understanding parameters such as Ra, Rz, and Rq, alongside robust statistical methods, professionals can elevate their surfaces to meet the demanding standards of modern applications.
Impact of Surface Roughness
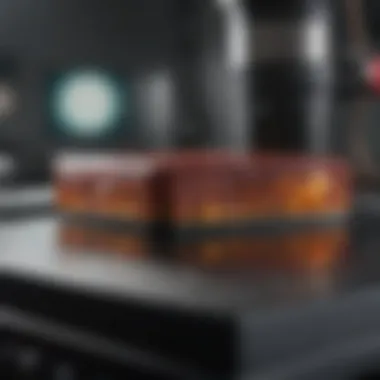
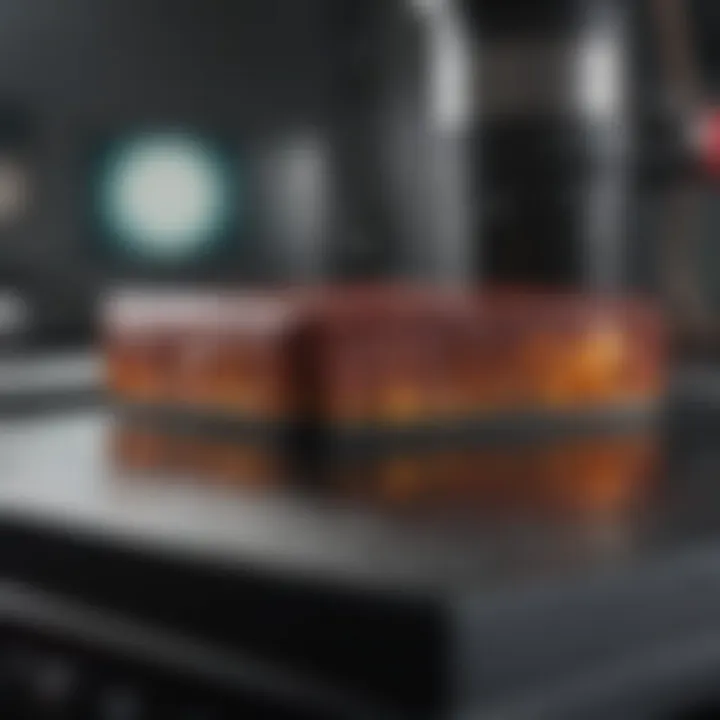
Understanding the impact of surface roughness is vital across various applications, especially in engineering and material sciences. Surface roughness significantly affects the physical properties of materials, as well as their performance in different contexts. Rough surfaces can enhance friction, while also affecting adhesion in coatings or bonding processes. In essence, even minute alterations in roughness can lead to substantial changes in how materials behave under stress or wear. This section will highlight the implications that surface roughness has on material properties and performance, paving the way for better design and application strategies.
Influence on Material Properties
Friction
Friction plays a major role in defining how materials interact. The roughness of a surface can lead to increased friction as the tiny peaks and valleys create more contact points between two surfaces. This characteristic is essential when considering applications like flooring materials or brakes, where greater friction can ensure safety and stability. However, while high friction can be advantageous, it can also lead to increased wear over time.
Key Feature: The heightened contact area at the microscopic level
Advantages: Enhanced grip and braking efficiency; beneficial in situations where more control is necessary.
Disadvantages: Greater wear and heat generation may lead to premature failure of components.
Wear Resistance
Wear resistance refers to a material’s ability to resist being worn away, often through mechanical action. Rough surfaces can sometimes enhance wear resistance due to their ability to redistribute load and minimize wear by engaging multiple surface points. This can be particularly crucial in industries such as automotive or aerospace, where performance and longevity of components are paramount.
Key Feature: Distribution of load over a larger area reduces localized wear.
Advantages: Can lead to longer-lasting components, which reduces maintenance costs and extends service life.
Disadvantages: In some applications, excessive roughness may compromise the smooth operation of moving parts, leading to inefficiencies.
Effects on Performance
Adhesion
Adhesion is another critical aspect influenced by surface roughness. For coatings or adhesives to bond effectively, the underlying surface must be appropriately rough. A certain level of roughness increases the contact area, aiding better mechanical bonding. In construction or manufacturing, this concept becomes invaluable when applying paints or epoxies, where adhesion can determine the success of the application.
Key Feature: Increased surface area for bonding enhances adhesive properties.
Advantages: Leads to stronger bonds and improves the durability of applied coatings.
Disadvantages: Too much roughness may lead to incomplete coverage or increased likelihood of surface defects.
Coating Applications
In coating applications, the roughness of the substrate can impact not only adhesion but also the overall effectiveness of the coating. A moderate roughness can provide optimal conditions for creating a strong and uniform coating. In industries that rely heavily on coatings—like automotive or electronics—this factor is vital for ensuring both protection and aesthetics.
Key Feature: Proper roughness enhances coating adherence and uniformity.
Advantages: Results in better durability and corrosion resistance of coatings, contributing to longer lifespans.
Disadvantages: Measuring the ideal roughness level can be challenging, making it necessary to employ precise measurement techniques.
"Surface roughness serves as a double-edged sword; it can facilitate improved performance or lead to unwarranted failure, making it essential to strike the right balance."
By recognizing the impacts and distinguishing features of surface roughness on material properties, we can better tailor applications ranging from manufacturing to material selection.
Standardization of Measurements
Standardization of measurements plays a pivotal role in ensuring consistency, accuracy, and reliability in surface roughness measurements. It creates a framework within which researchers and industry professionals can compare results, share knowledge, and address various challenges in the field of material characterization. Without standardized methods, it would be like comparing apples to oranges; results would vary widely based on the measuring techniques or instruments used. This not only impacts quality control and product performance, but also hinders advancement in scientific research regarding material behavior and characteristics.
International Standards
ISO Guidelines
The International Organization for Standardization (ISO) has established a comprehensive set of guidelines addressing surface roughness measurement. One significant aspect of the ISO guidelines is their global applicability, which permits universal comprehension among international practitioners. By adhering to these standards, it becomes easier to harmonize results, as everyone is operating under the same conditions and terminologies.
A key characteristic of ISO guidelines is their structured approach. The guidelines categorize various roughness parameters, which helps users in selecting the most suitable method for their particular applications. This categorization is a beneficial feature when preparing to report and analyze roughness data.
However, there's a unique aspect, or perhaps a drawback, of ISO guidelines—they may sometimes seem overly rigid. In certain situations, flexibility in measurement approaches may be needed, but this cannot be accommodated within the confines of strict standards. This limitation can be challenging, especially in rapidly advancing technology and material science areas.
ASTM Standards
Another prominent body setting standards in this area is the American Society for Testing and Materials (ASTM). ASTM standards also focus on ensuring credible and repeatable measurements across various industries. A notable aspect of ASTM standards is their expansive coverage; they address a wider variety of materials and applications than ISO.
One standout feature of ASTM standards is their adaptability. These standards frequently undergo revisions to align with technological advancements and emerging materials. This makes them a popular choice among professionals who seek the latest best practices in surface roughness measurement.
Nonetheless, a drawback to ASTM standards could be the frequency of updates, which might require constant re-evaluation of measurement techniques. For some, keeping up with these changes might be daunting. Despite this, their commitment to improvement serves to enhance measurement practices and, ultimately, material performance across applications.
Best Practices
Adopting best practices in surface roughness measurement is crucial for obtaining reliable and repeatable results. These practices incorporate various processes and techniques designed to mitigate errors and enhance measurement accuracy.
Calibration Procedures
Calibration procedures are an integral part of best practices for surface roughness measurement. The main goal here is to ensure that measuring instruments accurately reflect the true geometrical characteristics of surfaces being analyzed. A key trait of calibration is its preventive nature; it allows potential discrepancies in measurement to be identified and corrected before they lead to erroneous conclusions or product failures.
The unique aspect of calibration is that it inherently builds confidence among users. Knowing that their equipment is calibrated and operating within defined parameters reassures practitioners about the validity of their data. However, it demands time and resources, which smaller enterprises may find challenging to allocate. Regardless, adequate calibration practices are vital for preserving the integrity of measurements.
Environmental Considerations
Environmental considerations are increasingly recognized as essential for effective surface roughness measurement. Factors such as temperature, humidity, and even the cleanliness of the environment can dramatically affect measurement outcomes. A key characteristic of incorporating environmental considerations is the recognition that measurements are not conducted in a vacuum; the surrounding conditions can have profound effects on results.
This attention to environmental conditions enables practitioners to fine-tune their measurements. For instance, by controlling the room temperature or ensuring instruments are free of contaminants, better accuracy and precision can be achieved. However, this diligence may introduce complexities, such as increased operational costs or logistical challenges in maintaining controlled settings. Nevertheless, factoring in environmental conditions fosters more reliable and meaningful surface roughness assessments.
Challenges in Surface Roughness Measurement
Surface roughness measurement presents a unique set of challenges that are critical to address to ensure the quality and reliability of measurement outcomes. Recognizing and overcoming these challenges is essential for producing accurate surface evaluations in a range of applications, from manufacturing to material science. These challenges revolve around two main themes: measurement uncertainty and material considerations.
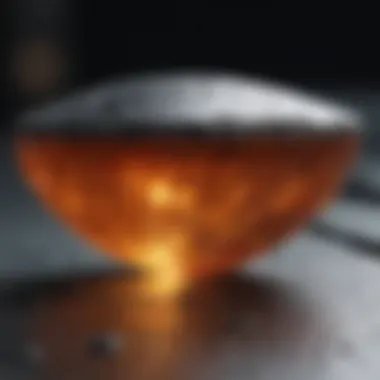
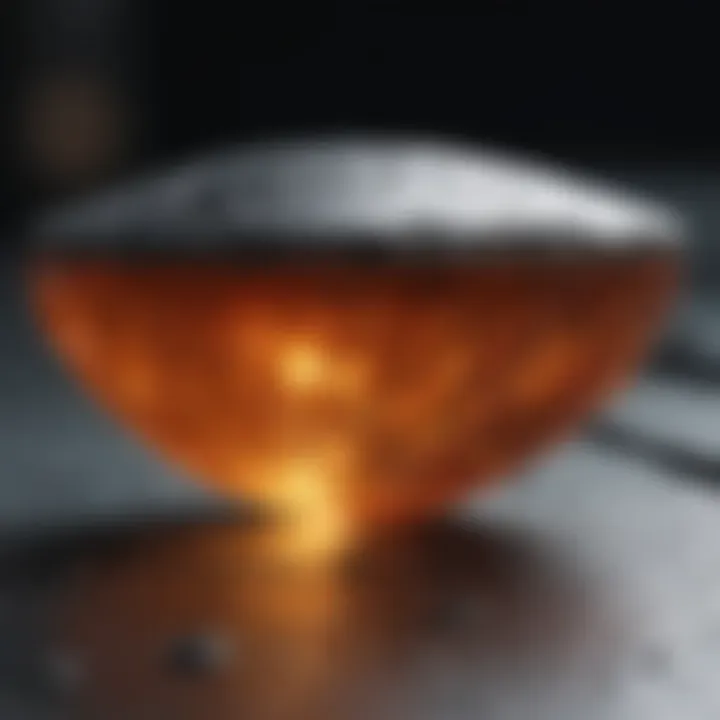
Measurement Uncertainty
Measurement uncertainty plays a pivotal role in how effective surface roughness assessments can be. Determining surface characteristics is not as straightforward as one might think. There are several factors that can lead to inaccuracies, but understanding these sources allows professionals to implement better measurement strategies and ultimately produce more reliable data.
Sources of Error
One prominent aspect of sources of error relates to the equipment and environment used during measurements. Many types of instruments, such as stylus profilometers or laser systems, can yield different results based on their calibration, sensitivity, and operating conditions. For instance, slight vibrations in the environment or incorrect calibration could skew results. The key characteristic here is the inherent nature of instruments to have limitations, which makes understanding their operational quirks a necessity. These errors, although not often entirely avoidable, can significantly impact the analysis if not properly considered. This aspect of sources of error underlines the need for detailed scrutiny when utilizing measuring devices for surface roughness evaluation.
Despite these challenges, there remain crucial advantages in examining sources of error. This understanding can lead to better training on equipment, more effective use of resources, and enhancements in technology development.
Minimizing Errors
Minimizing errors is a vital approach to handles the uncertainties inherent in measuring surface roughness. This can be achieved through several strategies, such as routine calibration and consistent methodology in data collection. Employing trained personnel to conduct the measurements can also lessen variability and enhance accuracy.
One of the key characteristics of minimizing errors is the establishment of strict protocols. This adherence to methodology ensures that any measurement is reproducible, which can support reliable data interpretation. Unique to this point is the understanding that while some errors may be unavoidable, having an established routine for minimizing them can help create a more robust measurement outcome. The advantages of minimizing errors include increased confidence in results and a greater understanding of the surface characteristics being analyzed.
Material Considerations
In addition to measurement uncertainty, material considerations must also be taken into account when evaluating surface roughness. Various materials can exhibit different behaviors in terms of surface properties, which can complicate measurement efforts. Understanding these material characteristics is essential to generate meaningful data.
Surface Treatments
The role of surface treatments is often underestimated in the context of surface roughness measurement. Treatments such as coatings, polishing, or plating can drastically alter surface characteristics. Highlighting surface treatments showcases how variations in roughness can arise before measurements even take place. It's beneficial to consider these treatments because they can enhance or detract from the material's performance, ultimately impacting how it fits into intended applications.
Unique to these treatments is their ability to disguise or exaggerate roughness. For example, a polished surface may appear smoother at first glance, but underlying irregularities can still exist. This complexity presents a double-edged sword—while surface treatments can optimize performance, they also introduce additional variables that must be carefully monitored during measurement activities.
Material Heterogeneity
Material heterogeneity refers to the inconsistency in a material's structure and composition, which can profoundly affect surface roughness readings. This can be particularly pertinent in composite materials, where the interface between components may cause differing surface textures. Acknowledging this factor is critical for deriving accurate data.
The key characteristic of material heterogeneity is its complexity, which introduces additional layers of difficulty in measurement consistency. It emphasizes the importance of thorough sample assessment before measurement, ensuring that data reflects true surface characteristics rather than misleading artifacts from inherent material variations.
Moreover, understanding the benefits of considering material heterogeneity allows for better customization of measurement techniques. Certain materials may require specific types of measurement methods or conditions to acquire accurate readings. This tailored approach can lead to improved outcomes and a greater depth of analysis.
Accurate measurement of surface roughness is not just about utilizing advanced equipment; it also involves understanding the nuances of the material and method used.
Future Trends in Surface Roughness Measurement
As we peer into the future of surface roughness measurement, it becomes clear that the evolution of technology will play a fundamental role in shaping this field. The rise of advanced measurement techniques not only enhances our ability to accurately characterize surfaces but also influences multiple industrial applications. By embracing innovative methodologies, we can significantly improve the efficiency and precision of these measurements. This section explores the notable advancements and the new frontiers that lie ahead, emphasizing how they may transform the understanding and application of surface roughness in various industries.
Advancements in Technology
Integration of AI
The integration of artificial intelligence (AI) in surface roughness measurement systems is emerging as a game-changer. One notable aspect is the ability for AI algorithms to analyze vast data sets quickly and provide insights based on historical patterns. This characteristic makes AI a highly effective tool for predicting surface performance under multiple conditions. For instance, AI can be used to refine measurement techniques by suggesting optimal parameters based on learned experiences from previous assessments.
The unique feature of AI integration lies in its capacity to continuously learn and adapt from new data, which is immensely advantageous. However, it does pose some disadvantages as well, particularly concerning the complexity in understanding how these AI algorithms interpret data, which may lead to skepticism among traditionalists in the field.
Automation in Measurements
Automation is steadily making its mark in surface roughness measurement, streamlining processes that were once labor-intensive. By automating measurements, industries can enhance productivity and minimize human error—one of the significant pitfalls in manual assessments. A key characteristic of automation is its ability to maintain consistent measurement environments, which is crucial for reproducibility in data collection.
This shift to more automated systems enables on-demand assessments, catering specifically to the fast-paced nature of modern manufacturing. While automation offers advantages such as efficiency, it can also be accompanied by challenges. The initial investment costs can be substantial, and there may be a steeper learning curve for personnel in operating sophisticated measurement systems.
Expanding Applications
Nanotechnology
The realm of nanotechnology is expanding rapidly, making it a pivotal topic within surface roughness measurement. As we venture into the nanoscale, the specific aspect of accurately measuring surfaces becomes crucial due to the implications for material properties at such a minuscule scale. This precision serves to enhance functionalities in fields like electronics and medicine, where even the slightest surface irregularities can lead to significant performance differences.
What makes nanotechnology particularly relevant in this discussion is its ability to tailor material properties through precise surface engineering. The downside, however, is that this also increases the complexity of the measurement processes, requiring highly sophisticated equipment and methodologies.
Biocompatible Materials
Biocompatible materials are increasingly important in medical applications, where the surface roughness can play a vital role in cellular interaction. Understanding this specific aspect helps researchers develop materials that minimize rejection and enhance integration into biological systems.
A striking characteristic of biocompatible materials is their wide array of applications, from implants to drug delivery systems. These materials must be finely tuned to optimize their surface roughness, as it directly influences how cells adhere and grow.
On the flip side, there's a challenge in this area, too. The specificity required in the roughness and the variability in how materials respond to biological environments demand constant innovation and testing.
"The future of surface roughness measurement lies in our ability to innovate and adapt to emerging technologies that influence not just the materials but also industries at large."
In summary, the future trends in surface roughness measurement present a landscape filled with potential. Advancements in technology, particularly the integration of AI and automation, create pathways for increased accuracy and efficiency. Meanwhile, the expanding applications in nanotechnology and biocompatible materials underline the critical need for precision in measurement to influence performance outcomes across diverse fields.
Culmination
In wrapping up our discussion on surface roughness measurement, it’s important to recognize that this topic holds significant weight in various domains of science and industry. The implications of understanding surface roughness extend far beyond academic curiosity; they touch upon practical challenges faced by professionals operating in sectors such as manufacturing, material science, and engineering.
One can't overstate the value of accurate surface roughness measurements. They play a pivotal role in determining how a material will behave under different conditions, such as friction, wear, or bonding with different substances. When precision in measurement is achieved, it leads to enhanced material performance, longer lifespans, and reduced operational costs. This ultimately translates into improved efficiency and reliability in products and processes.
Summary of Key Points
To emphasize the crucial points discussed throughout the article, here’s a concise summary:
- Understanding surface roughness is vital for material characterization in multiple fields.
- Various measurement techniques, including contact and non-contact methods, provide different insights into surface texture.
- Parameters such as Ra, Rz, and Rq are essential for quantifying surface roughness accurately.
- The implications of roughness on performance factors like friction and adhesion cannot be ignored.
- Standardization efforts help reduce measurement variability, making data more reliable.
- Challenges still exist, such as measurement uncertainty and material variances that need ongoing attention.
The Importance of Continued Research
The landscape of surface roughness measurement is always evolving. With advancements in technology and an increasing need for precision, ongoing research is essential. New materials and applications arise consistently, prompting the need for more refined measurement methods and better comprehension of their implications.
Furthermore, the integration of artificial intelligence in measurement systems promises to revolutionize how we assess and interpret surface texture. Such developments could lead to far more accurate readings in real-time, minimizing errors that arise from manual interpretations.
In short, further exploration into surface roughness measurement is not merely beneficial; it is an imperative in keeping pace with advancements in technology and material science. Researchers, engineers, and educators alike should advocate for increased focus in this domain to ensure that innovations continue to support and enhance performance across various industries.
"The only way to do great work is to love what you do."
— Steve Jobs
Each stride toward a deeper understanding of surface roughness will ultimately contribute to significant advancements in performance and efficiency. By investing in this knowledge, we're paving the way for a future where materials perform their best under myriad conditions.