Ni Foam: Properties, Applications, and Future Insights
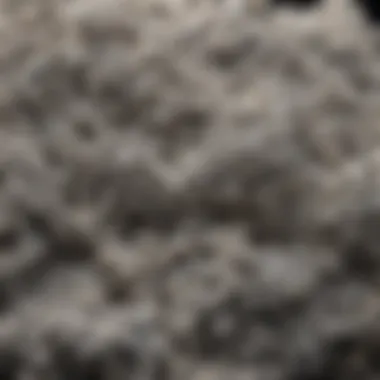

Intro
The material world often holds surprises, and nickel foam stands testament to this notion. Emerging as a promising material in various applications, this lightweight yet robust substance is reshaping our understanding of capabilities in science and technology. From energy storage solutions to innovative filters, the depth and breadth of nickel foam's utility are beginning to gather attention like a snowball rolling down a hill.
Nickel foam, despite being simply a metallic sponge, possesses complex structures and properties that invite thorough examination. Its unique open-cell structure contributes not just to its lightweight nature but also allows for high surface area, making it ideal for numerous energy-related applications. Energy efficiency and sustainability are at the forefront of many scientists' and engineers' agendas today, and ni foam fits right in the mix.
As we engage with the multifaceted aspects of nickel foam, it becomes crucial to understand both its current applications and future potentials. The journey navigates through its production techniques, performance in energy systems, environmental considerations, and its juxtaposition against alternative materials. We’re peeling back the layers, aiming to reveal what makes ni foam a critical player in modern technological advancements.
Prolusion to Ni Foam
Nickel foam, often deemed a marvel in the realm of materials science, holds significant relevance across various fields. This article focuses on the essential characteristics and applications of Ni foam to provide a thorough understanding of its intricacies. The increasing interest in sustainable technology and energy solutions has underscored the need for materials like Ni foam that balance efficacy with environmental considerations.
Definition and Basic Properties
Ni foam is characterized by its unique porous structure, comprised primarily of nickel, which provides several distinct advantages over traditional materials. It exhibits high porosity along with an impressive surface area, making it an excellent candidate for various applications ranging from energy storage to catalysis. The material maintains a remarkable combination of lightweight and strength, equipping it for demanding environments. Typically, the thickness of Ni foam can vary, although a standard range is between one to five millimeters, allowing adaptability to specific uses.
Moreover, Ni foam’s conductive properties are noteworthy, presenting an opportunity for applications in electronic devices and battery technology. This conductivity, coupled with its durability, ensures longevity and effectiveness in performance.
Historical Context and Development
The invention and evolution of nickel foam trace back several decades, reflecting advancements in materials technology. Initially synthesized through metallurgical processes, the development of nickel foam has revolutionized our approach to energy efficiency and storage. The earliest applications were rudimentary, commonly seen in industrial filters and other mechanical components where strength and durability were paramount.
As scientific inquiries into the material expanded, researchers began to recognize the potential of nickel foam in energy applications. For instance, its role in supercapacitor technology started gaining traction in the late 1990s, with studies illustrating its beneficial properties concerning electrode material. This historical context illuminates the transformative journey of nickel foam from simple applications to complex roles in burgeoning technologies like fuel cells and renewable energy sources.
"The evolution of nickel foam is a testament to the human quest for innovation, mirroring our societal needs for efficiency and sustainability in the face of mounting challenges."
Structural Characteristics of Ni Foam
Understanding the structural characteristics of nickel foam (Ni foam) is fundamental to its performance and applications. The structure of this material serves as a backbone, influencing its usability in diverse fields such as energy storage, catalysis, and biomedical engineering.
From its unique interpenetrated framework to its multi-faceted porosity, each of these elements plays a pivotal role in determining how well Ni foam can perform under various conditions. The benefits of exploring these characteristics extend beyond mere academic interest; they can directly impact the efficiency and effectiveness of technologies developed utilizing this material.
Porosity and Surface Area Analysis
Porosity refers to the volume fraction of void spaces within the foam. Ni foam is renowned for its high porosity, which can significantly enhance its surface area. Such a feature is advantageous in applications like supercapacitors and catalysis, wherein high surface area allows maximum interaction with other materials or systems.
- Types of Porosity: Ni foam exhibits both open and closed porosity. Open pores are critical for gas and liquid permeability, whereas closed pores might be utilized in specific applications where insulation or buoyancy is necessary.
- Influence on Performance: A greater surface area allows for more active sites, which translates into higher efficiency in processes such as electrochemical reactions. This property is central to its role in energy storage solutions, where the effective area for charge dissipation and accumulation can directly affect the performance of batteries or supercapacitors.
- Measurement Techniques: Various methods, such as mercury intrusion porosimetry and gas adsorption techniques, are employed for quantifying the porosity of Ni foam. These techniques help in determining the precise structural parameters that can be manipulated during synthesis to optimize performance.
Mechanical Strength and Durability
In addition to porosity, the mechanical strength of Ni foam is equally important and warrants significant attention. Understanding how robust this material is, directly correlates with its practical applications.
Ni foam needs to maintain its integrity under mechanical loads while also being versatile enough for various operational conditions.
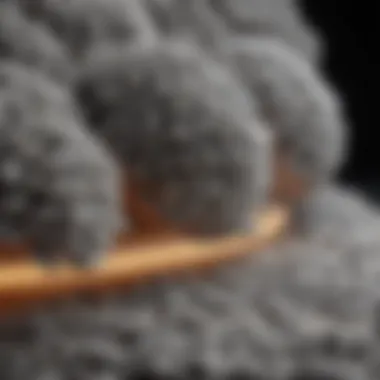
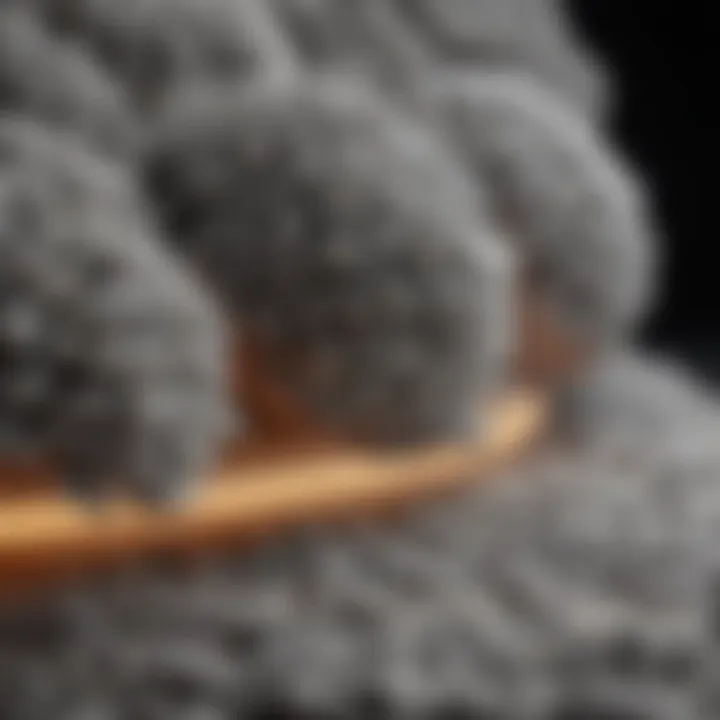
- Young's Modulus and Yield Strength: Nickel foam exhibits a delightful balance between lightweight construction and strength. Its Young's modulus indicates its ability to withstand deformation under stress. Higher yield strength ensures that it can endure considerable pressure without permanent deformation.
- Durability Under Stress: The mechanical properties of Ni foam make it suitable for use in environments subject to fluctuation, such as temperature changes and mechanical shocks. This durability is essential for applications in automotive and aerospace industries, where materials must repeatedly endure cycling loads.
- Fatigue Resistance: The fatigue life of Ni foam under repeated loading conditions determines its long-term use in critical applications. Therefore, considerations for how the structure performs over time will inform future design and application choices.
Understanding these structural characteristics not only helps in tailoring Ni foam for specific applications but also guides future research directions in material science. By focusing on the porosity and mechanical integrity, one can unlock new applications and enhance the existing ones in energy storage, catalysis, and beyond.
Production Methods of Ni Foam
The creation of nickel foam is a critical area of focus because it directly influences the material's properties and its potential applications. Understanding the production methods allows researchers and professionals to optimize processes for specific uses, whether in energy storage or catalytic applications. The choice of fabrication technique not only determines the structural integrity of the foam but also impacts its overall performance metrics, such as electrical conductivity and porosity. Therefore, distinguishing between these methods is more than just a technical necessity; it is essential for driving innovation and improving technology.
Electrochemical Deposition Techniques
Electrochemical deposition is a versatile method widely recognized for producing nickel foam, leveraging the principles of electrochemistry to deposit nickel onto a substrate. The process typically involves immersing a conductive substrate into an electrolyte solution containing nickel ions, with an electrical current applied to facilitate the deposition.
One of the significant advantages of this method is the ability to control the thickness of the foam with precision. This means that by adjusting the current density and deposition time, one can fine-tune the characteristics of the foam, resulting in enhanced mechanical properties and pore structures. Researchers have found that optimal current density leads to a more uniform foam structure, which is crucial for applications like supercapacitors and fuel cells.
"Electrochemical methods allow for the creation of tailored nickel foam with specific properties, paving the way for advances in energy storage and catalysis."
Additionally, this method is cost-effective compared to other techniques, making it appealing for large-scale production. However, certain challenges remain, such as the need for thorough post-treatment processes to ensure surface uniformity and electrochemical stability. The development of innovative electrolytes and methodologies is an ongoing research avenue aimed at overcoming these hurdles.
Chemical Vapor Deposition Processes
Chemical Vapor Deposition (CVD) provides another effective route for producing nickel foam. This method involves the chemical reaction of gaseous precursors that decompose on a heated substrate, forming a solid deposit. CVD is particularly advantageous because it can produce dense and homogenous layers of nickel foam, which possess high surface area.
What sets CVD apart are the options it provides to create complex 3D structures, making it especially useful for advanced applications that require intricate designs. The uniformity achieved through CVD often outmatches that of electrochemical deposition, which is critical for performances in fields like catalysis, where surface area and active sites are paramount.
Nonetheless, CVD comes with its own set of challenges. The process often requires high temperatures and controlled environments, which can lead to increased production costs and complexity in maintaining reactors. Researchers need to navigate these challenges while exploring innovative pathway to streamline the process.
Comparison of Fabrication Techniques
When comparing electrochemical deposition and chemical vapor deposition, several factors come into play. Electrochemical deposition shines in its cost-effectiveness and the ease of manipulation of various parameters to adjust the foam characteristics. It's particularly favorable for academic environments or smaller startups that may not have extensive resources.
On the other hand, CVD excels in creating high-quality, uniform structures, which can be crucial for high-stakes applications like hydrogen storage or advanced catalysis. The choice between these methods often boils down to the specific requirements of the intended application.
- Electrochemical Deposition:
- Chemical Vapor Deposition:
- Cost-effective
- Highly controllable
- May require post-treatment
- Produces dense, uniform layers
- Suitable for complex designs
- Higher cost and complexity
Ultimately, as research continues and technology evolves, new methods and hybrid techniques may emerge, potentially blending the benefits of these traditional methods while mitigating their drawbacks.
Applications of Ni Foam
Nickel foam has carved out a significant niche in various cutting-edge applications, attributable to its exceptional properties. In modern technological contexts, understanding the scope of these applications is crucial. The multifaceted advantages of Ni foam extend not only to energy storage but also to catalytic processes and medical utilization. Its lightweight structure, high surface area, and excellent electrical conductivity make it a key player in several domains.
Energy Storage Systems
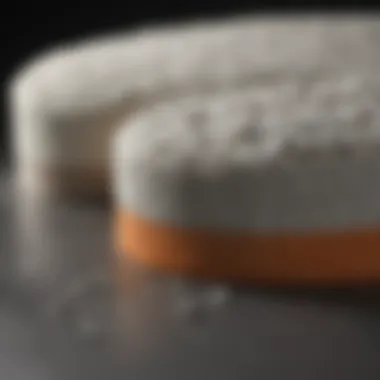
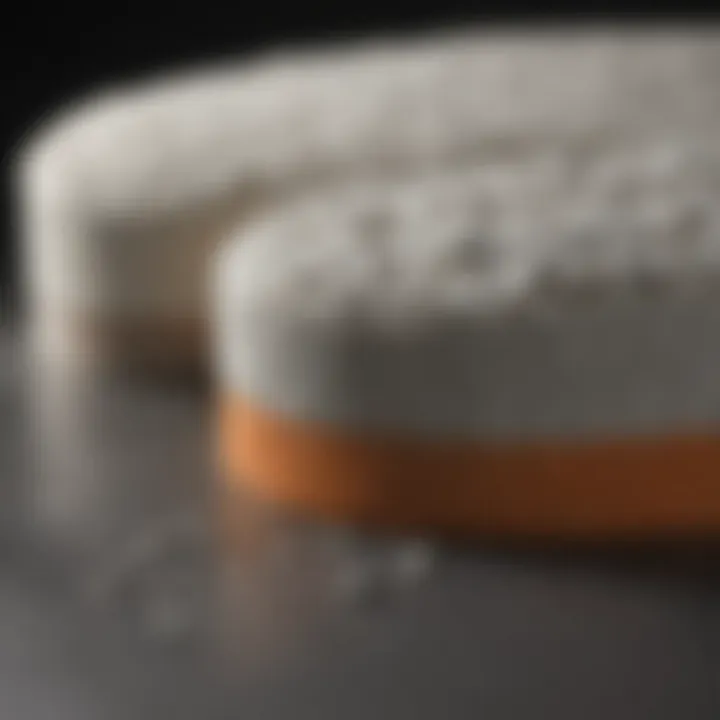
Supercapacitors
Supercapacitors have emerged as a vital technology for energy storage, offering a bridge between traditional capacitors and batteries. What sets supercapacitors apart is their ability to deliver quick bursts of power, making them incredibly useful for applications needing rapid charge-discharge cycles. Nickel foam plays a pivotal role here due to its high surface area, which optimizes the electrochemical interfaces. The specific characteristic of Ni foam enhances the performance of supercapacitors significantly, providing not only high capacitance but also excellent cycle stability.
However, while these components are highly beneficial, they come with limitations such as lower energy density compared to conventional batteries. This trade-off between power density and energy density is something that researchers continue to navigate, seeking to harness the best of both worlds.
Fuel Cells
Fuel cells represent a promising avenue in the pursuit of sustainable energy solutions. Notably, nickel foam contributes to the efficiency of fuel cells, particularly in hydrogen fuel cells, where it serves as an effective catalyst support. The key characteristic that makes Ni foam desirable here is its superior conductivity, which can significantly lower the resistance in the fuel cell setup.
Its unique feature lies in its structured porosity, which not only increases the surface area for reactions but also facilitates better gas diffusion. While fuel cells employing Ni foam can provide significant advantages like enhanced performance and durability, the costs associated with materials and production are notable disadvantages that need careful consideration.
Catalysis and Chemical Reactions
Beyond energy applications, nickel foam has faultlessly entered the realm of catalysis. Its high surface area and tunable microstructure foster an environment that can accelerate a variety of chemical processes. For instance, it has shown promise in hydrogenation reactions and CO2 reduction, offering notable performance improvements. In comparison to traditional catalyst supports, Ni foam is appreciated for its resistance to deactivation, owing to its mechanical strength and thermal stability. Its deployment in catalytic systems can not only optimize reaction rates but also simplify reactor designs.
The flexibility of using Ni foam can have substantial implications for green chemistry, where using fewer and less toxic materials is desired.
Biomedical Applications
In the biomedical field, nickel foam is gaining traction. Its biocompatibility, combined with unique porous structures, makes it a favorable candidate for scaffolds in tissue engineering. Such characteristics allow for enhanced nutrient transport and cellular adhesion, fostering environments conducive to cell growth. The applications extend to drug delivery mechanisms, where tailored nickel foam structures can aid in controlling the release rates of therapeutic agents.
However, the biocompatibility and long-term stability of Ni foam in biological environments remain subjects of ongoing research. Addressing these concerns is critical for broader acceptance and application in clinical settings.
In summary, the applications of nickel foam range from energy storage to catalysis and biomedicine, showcasing its versatility across disciplines. As urban scenarios evolve and the quest for efficient materials continues, the significance of nickel foam is only expected to grow.
Comparison with Other Materials
The examination of nickel foam against other materials plays a crucial role in understanding its unique properties and applications. By placing nickel foam side by side with its rivals, researchers and industry experts can better appreciate its advantages and limitations. This comparison not only highlights the strengths of nickel foam but also informs potential applications and areas of improvement. Through rigorous evaluation, stakeholders can make informed decisions regarding material selection for various technological implementations.
Nickel Foam vs. Carbon Foam
When comparing nickel foam and carbon foam, several key differences emerge. Nickel foam is primarily composed of nickel metal, granting it notable conductivity and strength, while carbon foam is based on carbon, which lends it excellent thermal and chemical stability. Here are some points of distinction:
- Conductivity: Nickel foam boasts superior electrical conductivity due to the metal composition, making it suitable for applications like batteries and fuel cells.
- Weight: Carbon foam is significantly lighter than nickel foam, a critical consideration in industries where weight is a factor, such as aerospace.
- Durability: Nickel foam tends to exhibit greater durability, especially under mechanical stress, which can be advantageous in environments where materials endure harsh conditions.
- Chemical Resistance: Although nickel foam is quite resistant, carbon foam can better withstand highly corrosive environments due to its inert nature.
Ultimately, the choice between nickel foam and carbon foam largely depends on the specific requirements of the intended application. For example, energy-related applications may favor nickel foam for its conductivity, whereas construction materials may benefit from the lightweight properties of carbon foam.
Performance Differences in Energy Applications
Energy applications provide a fertile ground for assessing the performance differences of nickel foam compared to other materials such as carbon foam and metal foams. In energy storage systems, for instance, nickel foam demonstrates remarkable resilience and efficiency. Its high surface area facilitates rapid charge and discharge cycles, proving beneficial in supercapacitors and fuel cells alike.
- Supercapacitors: Nickel foam serves as an excellent current collector, enhancing the energy density while also improving the power density. This dual benefit is vital for applications requiring quick bursts of power.
- Fuel Cells: The catalytic properties of nickel foam create an advantageous environment for reactions, leading to improved performance and longevity in fuel cells compared to substitutes primarily composed of carbon.
"Nickel foam's unique attributes make it indispensable, especially in energy-related technologies where performance is paramount."
Environmental Considerations
The growing focus on sustainable materials in recent years has put Ni foam into the spotlight. While discussing its applications and properties, it is equally crucial to address the environmental aspects linked to its production and utility. Understanding the ecological impacts of nickel foam not only helps in improving manufacturing processes but also in aligning with global sustainability goals. This section delves into two significant elements: sustainability in production and recyclability of nickel foam, highlighting the benefits these aspects bring.
Sustainability in Production
Sustainability in the context of Ni foam production has become a pressing issue, particularly when the world is striving for more eco-friendly practices. The conventional methods of producing nickel foam often involve energy-intensive processes that can lead to significant carbon emissions. However, recent advancements are leaning towards more sustainable practices.
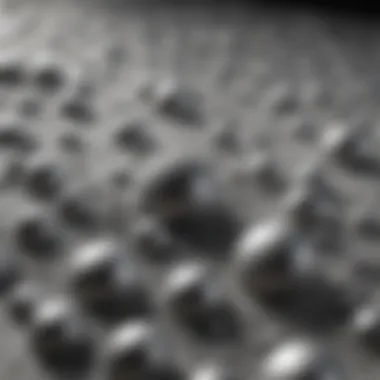
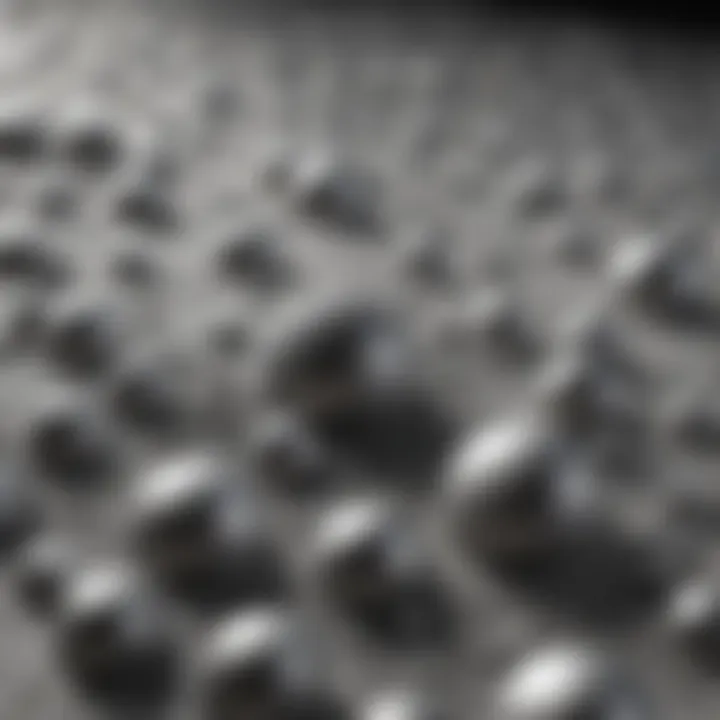
- Use of Renewable Energy: Some manufacturers are exploring renewable energy sources that power the production lines, drastically lowering dependence on fossil fuels. This shift not only reduces the carbon footprint of Ni foam but also contributes positively to the overall environmental health.
- Eco-Friendly Chemicals: Switching from harsh chemicals to more environmentally friendly alternatives in the electrochemical deposition process is gaining traction. This evolution not only safeguards human health but significantly lessens the pollution load on ecosystems.
- Optimized Resource Use: Developing processes that maximize resource efficiency—like reducing waste during fabrication—ensures that less raw material is needed. This careful utilization means less nickel is extracted from the earth, lessening the overall impact of mining operations on the environment.
By prioritizing sustainability in its production, Ni foam not only aligns itself with modern demands for ecologically responsible materials but also stands to gain a larger market footprint as industries move toward greener solutions.
Recyclability and Waste Management
Recyclability is another crucial environmental consideration while exploring materials like nickel foam. It has characteristics that make it notably easier to recycle compared to many other materials. This circle of reuse can help mitigate waste and foster a more sustainable approach throughout its lifecycle.
- Closed-Loop Recycling: Ni foam can often be reclaimed and reprocessed without losing its structural integrity. This presents an ability to create a closed-loop system where waste material can be reintegrated into production cycles. Rather than ending up in landfills, spent Ni foam can be re-used, which closes the resource loop efficiently.
- Reduced Waste Generation: During recycling, the waste materials generated are significantly lower when compared to producing new nickel foam from mined resources. This means a smaller environmental impact and less strain on landfill sites.
- Economic Benefits: Besides the ecological advantages, recycling Ni foam presents economic benefits. Businesses can save on raw material costs and potentially receive incentives from governments encouraging recycling efforts.
"Embracing the principles of recycling and sustainability not only supports the planet, but could also be a boon to innovation within the industry."
Future Research Directions
Research into nickel foam has come a long way, but the road ahead is just as promising. This section will focus on the potential future directions in this dynamic field, with an emphasis on two pivotal areas: enhancements in fabrication techniques and the exploration of hybrid materials. The title of this section might seem rather technical, but it's crucial for students, researchers, educators, and professionals who stand at the forefront of innovation in materials science.
Advancements in Fabrication Techniques
As researchers continue to push the boundaries of what’s possible with Ni foam, innovative fabrication methods are coming to the forefront. The advent of new technologies has broadened the horizon for production techniques, making it possible to customize properties to suit specific applications. Some key points to consider include:
- 3D Printing Innovations: Utilizing additive manufacturing can lead to more intricate designs which can enhance the performance characteristics of Ni foam, such as porosity and surface area.
- Self-Assembly Methods: Leveraging self-assembly can potentially reduce costs while improving scalability, ensuring that production meets industrial demand.
- Nano-Coating Techniques: Applying nano-coatings can modify the chemical and physical properties significantly, potentially leading to further enhancements in energy storage systems.
"The engagements of diverse fabrication methods can transit Ni foam from a niche material to a staple in a variety of industries."
The benefits of these advancements don’t just lie in improved performance but also in sustainability and efficiency. Future research needs to delve deeper into how these methods can be optimized not just for performance but also for environmental impact. A holistic approach to innovation will play a key role in determining the fate of Ni foam in future applications.
Potential for Hybrid Materials
The pursuit of hybrid materials represents an exciting frontier within the realm of Ni foam research. Combining nickel foam with other materials can yield synergistic effects, enhancing the overall properties while expanding its applications.
- Composite Systems: Integrating Ni foam with polymers could lead to lightweight yet strong materials, suitable for aerospace applications or automotive components. The combination can provide unique mechanical properties and thermal stability.
- Graphene and Other Nanomaterials: Merging nickel foam with graphene can substantially improve its conductivity and catalytic activity. Research into such hybrids could unveil breakthroughs in energy storage technologies.
- Biocompatible Materials: The potential for combining Ni foam with biocompatible substances opens doors for medical applications, ranging from implants to tissue engineering.
Given the increasing interest in sustainable practices, hybrid materials can leverage both functionality and eco-friendliness. The road forward requires continuous collaboration across disciplines and sectors, with scientists, engineers, and industry experts pooling their knowledge to lay the groundwork for innovations that are not only useful but also environmentally responsible.
Ending
In the realm of material science, the exploration of nickel foam, or Ni foam, underscores its growing significance in a variety of applications. As this article has emphasized, Ni foam is not just a passing trend; its versatile properties make it a cornerstone in energy storage, catalysis, and even biomedical fields. The conclusion synthesizes these insights and illustrates the broader implications of its use.
When considering the advancements Ni foam has brought about, it is evident how it bridges theoretical research with practical application. The unique characteristics, such as its high porosity and surface area, give it distinct advantages over more traditional materials. This does not merely enhance performance but also opens avenues for innovative applications that were once thought impractical.
Crucially, the dialogue surrounding Ni foam cannot be complete without acknowledging its environmental aspects. The discussion on sustainability during production and how recyclable the material is, reflects a pressing need for balance between technological advancement and ecological responsibility.
Summary of Key Points
- Nickel foam displays remarkable porosity and surface area, making it effective for various energy applications.
- Its strength and durability make it suitable for long-term use across multiple sectors.
- Various production methods contribute to the unique properties of Ni foam, with each technique having its own advantages and drawbacks.
- The material has a definitive role in energy storage systems, particularly within supercapacitors and fuel cells.
- Environmental impact and sustainability considerations are integral to its development, encouraging a focus on responsible innovation.
- Future research directions highlight the promise of hybrid materials and improved fabrication techniques.
The Future of Ni Foam in Scientific Advancements
Looking ahead, the future of nickel foam in scientific advancements appears bright and robust. There’s ongoing interest in refining the methods of producing Ni foam to enhance its properties further. For instance, improvements in electrochemical deposition could yield foams with tailored characteristics, thus expanding its functional repertoire.
Moreover, the potential for hybrid materials suggests exciting applications. Imagine integrating Ni foam with graphene or other substances to create composites that significantly outperform current technologies. This kind of innovation can propel varied fields, from renewable energy to biomedicine, into unprecedented realms.