Exploring Liquid Resin for 3D Printing Innovations
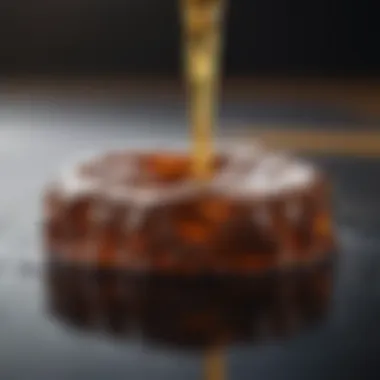
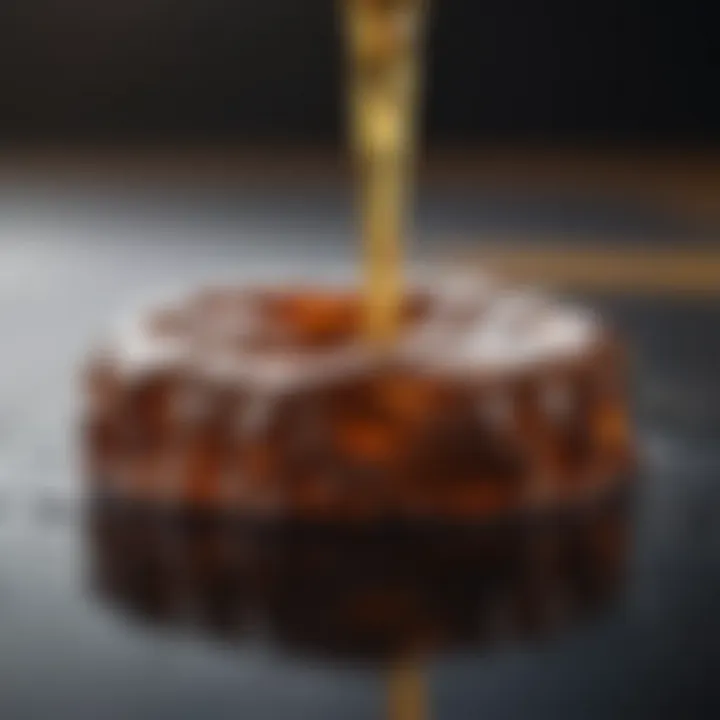
Intro
The evolution of 3D printing has ushered in numerous innovations, among which liquid resin stands out. Liquid resin, also known as photopolymer resin, plays an integral role in the realm of additive manufacturing, enabling the creation of highly detailed and intricate models. This article will systematically dissect the components that make up liquid resin, exploring its fundamental properties, diverse applications across various industries, and notable advancements in technology.
As 3D printing continues to gain traction in research and professional spheres, it's essential for students, researchers, educators, and professionals to comprehend the dynamics of liquid resin. Understanding its chemical formulation and how different printing technologies interact with it can greatly influence the quality and effectiveness of 3D printed products. Moreover, the implications of material selection for specific projects remain critical operatives that determine the success of the printing endeavor.
Discussions surrounding safety considerations, environmental implications, and future trends in resin development will underscore the responsible use of this innovative material. This comprehensive overview aims to serve as a foundational resource, enriching the reader’s understanding and fostering further exploration into the possibilities liquid resin holds for 3D printing.
Foreword to Liquid Resin in 3D Printing
Liquid resin plays a pivotal role in the world of 3D printing, serving as a fundamental material that enables the creation of detailed, intricate models. This section focuses on the significance of liquid resin, understanding its definition, and exploring its historical background. By examining these elements, readers can appreciate how liquid resin has transformed the additive manufacturing landscape, leveraging its potential for various applications.
Definition of Liquid Resin
Liquid resin refers to a photopolymer material that can be solidified by exposure to light, typically via ultraviolet (UV) wavelengths. When subjected to UV light, the liquid resin undergoes a chemical reaction known as polymerization. This process converts the liquid into a hardened plastic structure that retains the shape dictated by a 3D model. Liquid resins are primarily utilized in printing technologies such as Stereolithography (SLA) and Digital Light Processing (DLP).
The composition of liquid resin can vary considerably, including a variety of base formulations tailored for specific applications. Some formulations allow for flexible prints, while others are rigid or possess varying degrees of translucence. This flexibility in properties makes liquid resin an attractive option for numerous industries, from automotive to healthcare.
Historical Context of 3D Printing Resins
The use of resins in 3D printing has a rich history that dates back to the early 1980s when 3D printing technology began to flourish. The first commercial method to utilize liquid resin was Stereolithography, created by Chuck Hull in 1987. This innovation marked a significant turning point as it enabled the production of highly detailed objects that were previously unachievable with traditional manufacturing methods.
Over the years, advancements in chemistry have evolved liquid resins to include a growing range of properties. In the 1990s, the introduction of various photopolymers expanded the capabilities of 3D printing. Fast forward to the present, we see continuous innovation in the formulation and application of liquid resins, leading to developments such as biocompatible resins for medical use and specialized options for jewelry-making.
The evolution of liquid resin technology not only illustrates the strides made in 3D printing but also emphasizes the significance of research and development in this sector. Overall, understanding the historical context of 3D printing resins provides valuable insights into the current landscape of additive manufacturing.
Chemical Composition of Liquid Resins
Understanding the chemical composition of liquid resins is crucial in the context of 3D printing. This knowledge not only affects the performance and properties of the final prints but also influences the selection of appropriate resins for specific applications. Hence, grasping the underlying chemistry becomes essential.
Types of Photopolymers
Liquid resins primarily consist of photopolymers, which are materials that undergo a chemical change when exposed to light, usually ultraviolet (UV) light. There are several types of photopolymers utilized in 3D printing, each providing unique properties:
- Acrylic-based photopolymers: These resins offer good clarity, light sensitivity, and moderate flexibility. They are commonly used for a wide range of applications because of their versatility.
- Epoxy-based photopolymers: Known for their high strength and durability, epoxy resins are favored in applications requiring detailed and solid structures.
- Polyurethane-based photopolymers: These materials provide excellent elasticity and resilience, making them suitable for parts that need to withstand repeated stress.
Each type has advantages and disadvantages, impacting its suitability for different printing needs. Understanding their properties helps in selecting the right resin for specific applications, ranging from medical modeling to artistic projects.
Additives and Their Functions
In addition to base photopolymers, liquid resins often contain various additives. These components improve the resin’s performance and usability. Common additives include:
- Photoinitiators: These substances absorb UV light and initiate the polymerization process, leading to solidification of the resin.
- Colorants: Used to achieve a desired hue, colorants can enhance the aesthetic of the printed object.
- Fillers: These materials can provide additional strength, modify viscosity, or reduce production costs.
- Stabilizers: These additives improve the shelf life of resins by preventing degradation due to exposure to light or heat.
By carefully selecting and balancing these additives, manufacturers can fine-tune the resin properties to meet specific requirements. Each additive plays a pivotal role in determining the overall quality of the 3D printed product.
Properties of Liquid Resin
Understanding the properties of liquid resin is crucial for anyone involved in 3D printing. The characteristics of these resins directly affect how they perform during the printing process and the quality of the final product. This section focuses on two important properties: viscosity and thermal stability. Both play significant roles in determining the resin's usability in various applications within the realm of additive manufacturing.
Viscosity and Its Importance
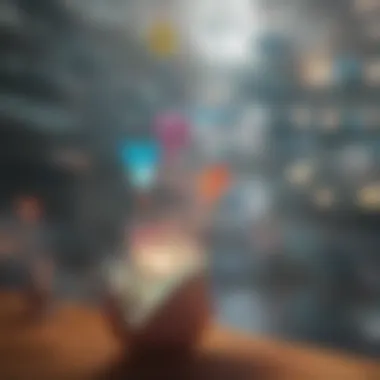
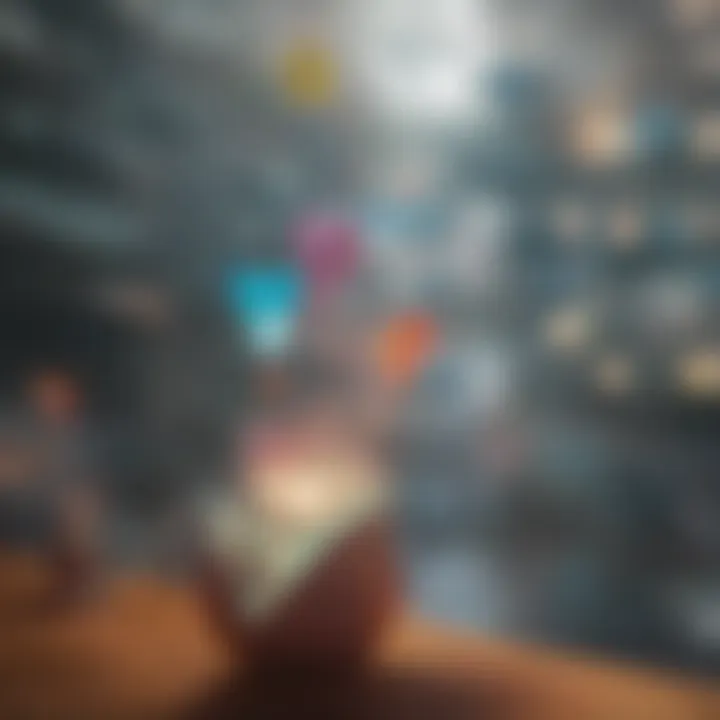
Viscosity refers to a fluid's resistance to flow. In the context of liquid resin, it is a critical factor that impacts the printing process. Lower viscosity resins can flow easier, allowing for finer details and smoother finishes in the printed model. But, if the viscosity is too low, it might lead to issues like sagging or loss of detail during the curing process.
Higher viscosity resins, on the other hand, provide strength but can pose challenges when it comes to detailed layer formation. The balance between these two extremes is paramount. Factors such as temperature and the presence of additives can alter viscosity, affecting the resin's performance.
Key benefits of managing viscosity include:
- Improved print quality
- Enhanced detail retention
- Increased accuracy in producing complex geometries
To ensure consistent results in 3D printing, one must understand how to work with different viscosities. Manufacturers provide data sheets for their products, which include information on viscosity at various temperatures. This makes it easier for practitioners to choose the right resin for their specific printing needs.
Thermal Stability Considerations
Thermal stability refers to how well a material can withstand temperature changes without degrading or losing its intrinsic properties. For liquid resins, thermal stability is vital for both processing and final applications. During the printing process, resins are exposed to UV light to cure and bake into solid forms. If a resin does not possess adequate thermal stability, it may warp or lose structural integrity under varying temperatures.
Additionally, in applications such as automotive parts or medical devices, the end product must withstand heat and stress during use. Therefore, a thorough understanding of a resin's thermal behavior is essential.
Important points regarding thermal stability include:
- Assessment of thermal degradation temperatures
- Compatibility with high-temperature applications
- Resistance to thermal cycling effects
Since thermal stability can be influenced by chemical composition, it is important to select resins that meet the demands of the intended application. Researchers and users must focus on resilience against heat when selecting materials, especially for critical uses that require robust performance.
"The interplay between viscosity and thermal stability is a cornerstone of successful 3D printing with liquid resins."
In summary, the properties of liquid resin, particularly viscosity and thermal stability, are indispensable for achieving excellent results in 3D printing. A deep understanding of these properties enables users to select the right material, optimize their printing processes, and ensure high-quality outcomes.
Applications of Liquid Resin in 3D Printing
The applications of liquid resin in 3D printing are vast and impactful. It showcases the versatility of this material and its capacity to meet the needs of various industries. Liquid resins enable the production of highly detailed and precise models, which is essential for functions ranging from product design to medical applications. This section will examine three prominent applications: rapid prototyping, medical and dental uses, and artistic creation.
Rapid Prototyping
Rapid prototyping stands as one of the primary applications of liquid resin in 3D printing. Businesses, especially in product development, utilize this method to bring ideas to life quickly. Prototyping with liquid resin allows for the creation of functional models that can be tested for form, fit, and function.
The benefits are considerable, including:
- Speed: Liquid resin printers can produce models much faster than traditional methods.
- Detailing: High-resolution prints are achievable, allowing for intricate designs and features.
- Cost-Effective: By rapidly creating prototypes, companies can save time and money in the product development cycle.
Moreover, Stereolithography (SLA) and Digital Light Processing (DLP) technologies excel in rapid prototyping. They provide the necessary precision to produce prototypes that closely resemble final products. This quick turnaround can result in better product designs and faster time-to-market.
Medical and Dental Applications
The medical field benefits significantly from advancements in liquid resin technology. In particular, applications in dental and surgical planning have shown promise. 3D printing with liquid resin in this domain allows for tailored solutions that can enhance patient outcomes.
Some specific uses include:
- Custom Dental Implants: Liquid resin is used to create precise dental molds and implants that fit better and enhance comfort.
- Surgical Models: Surgeons can have a model printed from liquid resin, which helps them prepare better for complex procedures, improving results.
- Prosthetics: Custom prosthetics can be designed and printed using liquid resin, which can reduce lead time and enhance fitting.
Working with biocompatible resins is essential to ensure safety and effectiveness in medical applications. Incorporating these customized solutions can lead to significant benefits for patients and practitioners alike.
Artistic and Pattern Making
Artistic applications of liquid resin are growing in popularity as artists and makers explore this medium. The ability to create intricate and complex shapes aligns well with the needs of creative professionals. Artists can leverage the detailed capabilities of resin printing to enhance their creations.
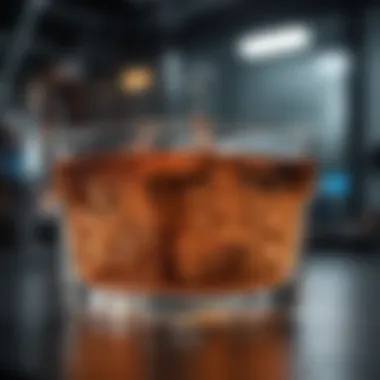
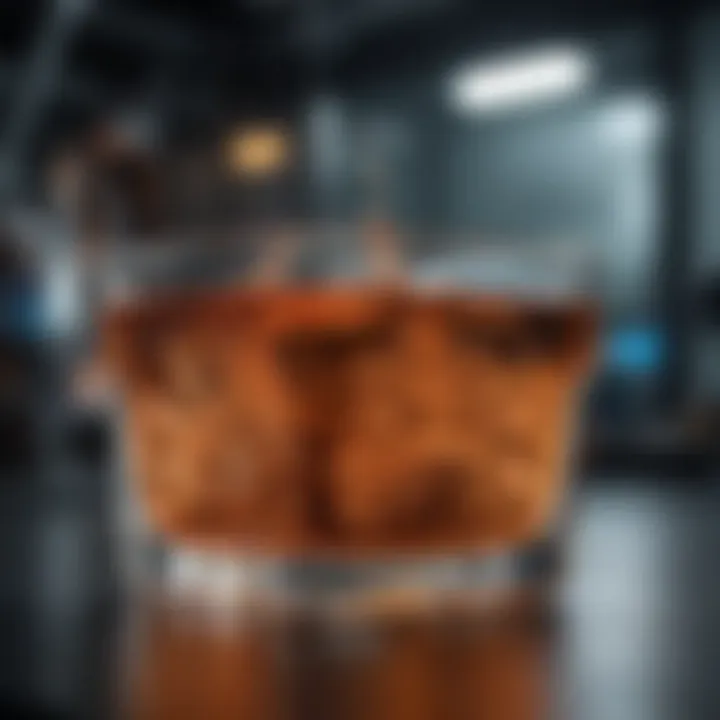
Liquid resin can be used for:
- Sculptures: Artists create stunning sculptures that boast fine details.
- Jewelry Making: Intricate patterns and designs are easily produced, offering unique aesthetic qualities.
- Customized Patterns: Pattern makers utilize liquid resin for unique molds that require precise detail.
In this context, the aesthetic qualities of resin can elevate artistic works. As such, artists have a powerful tool at their disposal. The technology empowers them to turn their visions into tangible reality, transcending traditional boundaries.
Liquid resin bridges the gap between artistic expression and technological precision.
3D Printing Technologies Utilizing Liquid Resin
3D printing technologies that use liquid resin are crucial for the advancement of additive manufacturing. These technologies enable the transformation of digital designs into physical objects with remarkable precision and detail. Understanding these methods is vital for numerous stakeholders, from researchers developing new materials to professionals tasked with creating prototypes and end-use parts. The various resin-based processes not only enhance the capabilities of 3D printing but also open new avenues in diverse fields, such as medical, automotive, and consumer goods.
Stereolithography (SLA)
Stereolithography, often referred to as SLA, is one of the earliest forms of 3D printing using liquid resin. This technology employs a laser to cure liquid resin layer by layer. The laser selectively solidifies the resin based on the computer-aided design file provided. SLA is known for its exceptional accuracy and capability to produce intricate geometries.
The significance of SLA lies in its potential to create high-quality details and smooth surface finishes. Print speeds can be adjustable based on object complexity, making SLA adaptable for various applications. Additionally, SLA resins are available in a range of properties, from flexible to rigid, allowing for extensive customization. Its precision makes it a favored choice in industries where detail is paramount, such as in the production of dental molds, jewelry, and functional prototypes.
Digital Light Processing (DLP)
Digital Light Processing, or DLP, is another method relying on liquid resin. This technology employs a digital light projector to flash an entire layer of resin at once, unlike SLA, which traces each layer with a laser. DLP results in faster print times since it cures layers in whole units rather than sequentially.
DLP technology is particularly beneficial for projects that require a balance between speed and fidelity. It yields high-resolution prints, which is essential for industries like jewelry design, where fine detail is necessary. Moreover, the resin options available for DLP printing often include materials with varied optical and mechanical properties. As a result, DLP supports a wide range of applications, serving both prototyping and production needs in various sectors.
Continuous Liquid Interface Production (CLIP)
Continuous Liquid Interface Production, or CLIP, introduces a novel approach to resin printing. This technology utilizes an oxygen-permeable window, allowing for a continuous flow of resin. Through this mechanism, printing can take place continuously instead of layer by layer. The process is characterized by its speed and efficiency, leading to high-quality outputs with layers that are almost imperceptible.
One of the main advantages of CLIP is its ability to produce finished parts more quickly than traditional methods. As it reduces print times significantly, it enables rapid prototyping and production, which is particularly appealing in markets requiring quick turnaround. CLIP also benefits from a diverse array of resin materials, accommodating specific requirements for strength, flexibility, and appearance.
Post-Processing Techniques for Liquid Resin Outputs
The post-processing phase plays a crucial role in the overall quality and usability of 3D printed objects created with liquid resin. This stage of production not only enhances the aesthetics of the printed pieces but also ensures durability and integrity. Proper techniques can significantly influence the final appearance and functionality of the prints. Thus, understanding the essential post-processing methods is integral for any professional involved in 3D printing.
Cleaning and Removal of Supports
After a resin print is produced, it is typically covered in excess resin and often attached to the build platform with supports. Cleaning is one of the first steps in post-processing. This involves washing the printed part thoroughly to remove any uncured resin.
- Materials and Tools: For effective cleaning, isopropyl alcohol (IPA) is commonly used. The printed item is usually placed in a container filled with IPA, allowing the alcohol to dissolve the uncured resin.
- Ultrasonic Cleaners: Some professionals use ultrasonic cleaners for enhanced cleaning efficiency. These devices generate ultrasonic waves that agitate the liquid, allowing for more thorough removal of excess resin, especially from intricate geometries.
- Support Removal: Once clean, supports can be safely removed. This can be done manually with cutters or pliers. Care must be taken to avoid damaging delicate parts of the print.
- Surface Finishing: After cleaning, surface imperfections may still exist. Sanding or filing can be carried out to achieve a smoother finish. Attention to detail is important in this stage since a well-finished surface enhances the final look and provide better functional outcomes.
Curing Processes Explained
Curing is the next critical step following cleaning. It involves the application of light to the printed part to harden it fully. There are a few methods used for curing, each integral for achieving the best results.
- UV Curing: Ultraviolet light is frequently employed in this process. The print is exposed to UV light for a set duration. This light initiates a chemical reaction, converting the remaining liquid resin into a solid form.
- Curing Stations: Dedicated curing stations are available in the market. They come equipped with UV lights and rotating platforms to ensure an even cure across the surface of the print. These stations can offer improved results compared to simply placing the print in the sunlight.
- Post-Cure Time: The length of time necessary for curing depends on the specific resin being used. Thorough knowledge of the resin’s properties is important for choosing the appropriate curing time.
- Finishing Touches: After curing, the prints can be painted or coated for additional protection or aesthetic appeal.
"Post-processing is not just about refining your object; it’s about unlocking the full potential of your design."
In summary, post-processing techniques are essential for achieving high-quality results when working with liquid resin in 3D printing. From cleaning and removing supports to curing processes, each step requires careful attention and expertise. Understanding and mastering these techniques will substantially improve the final output, benefiting designers, researchers, and practitioners in the field.
Safety Considerations in Working with Liquid Resins
Working with liquid resins in 3D printing presents many benefits, but it also demands serious attention to safety considerations. Resins can pose various health risks, which, if neglected, may lead to unfortunate consequences for users. Understanding these risks is the first step towards effective prevention.
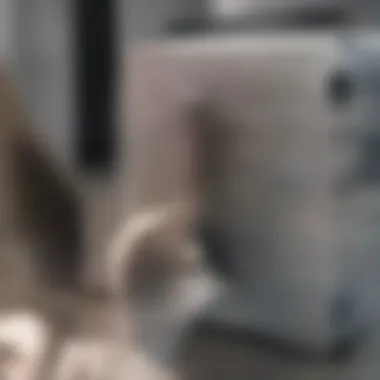
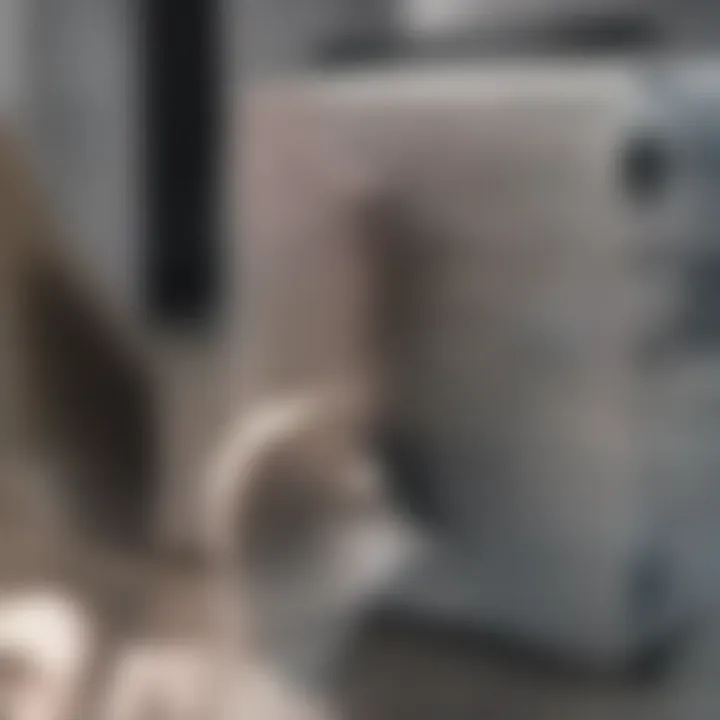
Proper handling and awareness of safety protocols ensure not only the well-being of individuals but also the sustainability of the environment where the materials are used. As 3D printing continues to expand in various sectors, individuals and companies alike must prioritize safety as they explore new applications of liquid resins.
Health Risks and Precautions
Liquid resins often contain chemical compounds that may be hazardous if mishandled. These materials can cause skin irritation, respiratory issues, and allergic reactions. It is crucial for users to understand these potential health risks and take appropriate precautions. Here are some key points to consider:
- Personal Protective Equipment (PPE): Always wear gloves, safety goggles, and masks to minimize direct exposure to resins. PPE acts as the first barrier against harmful substances.
- Ventilation: Use systems that provide adequate air circulation when working with liquid resins. Fumes released during mixing and curing can be toxic. A well-ventilated workspace reduces inhalation risks.
- Safe Handling: Ensure that all containers are sealed when not in use. Avoid spills by regularly checking for leaks in your working area.
- Proper Disposal: Follow your local regulations concerning the disposal of resin waste. Never pour resin down drains. It is important to dispose of uncured and cured resins responsibly.
Proper safety measures not only protect the user but also contribute to maintaining a safe work environment.
Environmental Impact of Resin Use
The environmental implications of liquid resin use cannot be overlooked. While 3D printing offers sustainable alternatives to traditional manufacturing, the choice of materials still raises concerns. Here are aspects to consider about the environmental impact of resin:
- Chemical Composition: Many liquid resins are derived from petroleum, underlining the dependence on fossil fuels. Researchers are working on bio-based alternatives, yet the industry still relies heavily on traditional resins.
- Waste Generation: The production process and post-processing of resin prints can lead to hazardous waste. This waste can accumulate if not managed wisely, leading to significant environmental degradation.
- Pollution from Curing: Some curing methods release volatile organic compounds (VOCs) into the air, contributing to air pollution. Consider alternative curing methods that may be less impactful.
- Recycling: Innovations in the recycling of liquid resin remain limited. Greater emphasis on developing recyclable materials can help alleviate some of the pressure on the environment.
Future Trends in Liquid Resin Development
The field of liquid resin development is constantly evolving, driven by both technological advancements and market demands. Understanding future trends is crucial for comprehending how 3D printing can further expand its applications and improve outcomes. Several factors influence these trends, including innovation in resin chemistry and the increasing relevance of specialty resins.
Innovations in Resin Chemistry
Recent years have seen significant innovations in resin chemistry that promise to enhance the performance of 3D printed objects. Researchers are exploring new formulations that aim to strike a balance between strength and flexibility. For example, the development of hybrid resins combines traditional photopolymers with additives that impart unique properties, such as increased impact resistance.
Additionally, the emphasis on bio-based and sustainable materials is on the rise. These eco-friendly resins aim to reduce the environmental footprint associated with 3D printing. Companies are investing in the research of plant-derived or recyclable materials, which aligns with global sustainability goals. The pursuit of resins that cure faster and with lower energy consumption also represents a significant trend, catering to the need for efficiency in production processes.
The Growing Market for Specialty Resins
The demand for specialty resins is also escalating, fueled by diverse industrial needs. Industries such as medical, automotive, and consumer electronics have specific requirements that standard resins cannot satisfy. For instance, the medical field requires resins that are biocompatible and can endure sterilization processes.
As 3D printing technology matures, the availability of specialty resins ensures that applications can tailor materials for specific tasks. This trend not only expands the utility of 3D printing in various fields but also encourages innovation in resin formulation. Companies that recognize and adapt to these niche requirements stand to gain a competitive edge in the market.
The following aspects summarize the importance of specialty resins:
- Customized Performance: Specialty resins meet unique application requirements.
- Market Expansion: New uses for resin in different industries.
- Innovation Trigger: Creates opportunities for developments in resin chemistry.
Closure and Summary
The conclusion section serves a crucial role in summarizing the extensive discussions presented throughout the article. It consolidates key insights and offers a final perspective on the importance of liquid resin in 3D printing. While the preceding sections dive into specifics regarding chemical compositions, properties, and applications, the conclusion synthesizes these elements, reinforcing their interconnections and implications for future practices.
Understanding liquid resin is no longer just an academic exercise, but a necessary endeavor for anyone involved in the advanced manufacturing landscape. The transformative potential of liquid resin, combined with emerging technologies and innovative formulations, continues to redefine what is possible in additive manufacturing.
This understanding also illuminates the importance of proper safety measures and environmental considerations when working with resins. It is essential to engage with these topics seriously to minimize risks and enhance sustainability. Therefore, the article underscores the significance of ongoing education and resource exploration in this rapidly evolving field.
Recap of Key Insights
- Liquid resin plays an integral role in various 3D printing technologies, delivering fine details and smooth surfaces in prints.
- The chemical composition is diverse, with various photopolymers and additives contributing to performance characteristics.
- Safety risks are involved in handling liquid resins, making it paramount to adhere to best practices in workplace safety.
- The future holds potential for enhanced resin formulations, with a shift towards specialty resins that meet niche requirements in industries ranging from healthcare to creative arts.
Understanding these aspects enhances the ability to make informed decisions about materials and methods, thereby improving outcomes in 3D prints.
Encouragement for Continued Exploration
It is strongly suggested that practitioners, researchers, and educators continue to delve deeper into the evolving landscape of liquid resin technology. The field is rapidly advancing, often characterized by novel approaches and materials that offer improved print quality, efficiency, and safety measures.
Encouraging exploration comes in several forms:
- Stay Informed: Regularly follow academic journals and publications focused on materials science and 3D printing technologies. Websites like Wikipedia and Britannica offer solid foundational information and are good starting points.
- Engage in Communities: Joining forums and groups on platforms like Reddit allows for sharing knowledge, experiences, and best practices among practitioners.
- Experiment with Materials: Hands-on experimentation with different types of liquid resin can provide valuable insights and foster innovation.
As the industry adopts newer technologies, the convergence of different materials and techniques will inevitably unlock additional opportunities for efficiency and creativity. The quest for knowledge in liquid resin use will not only benefit individual projects but will also contribute to the overall advancement of the field.