Concrete Manufacturing: A Comprehensive Exploration
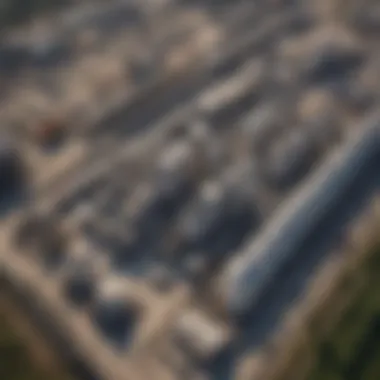
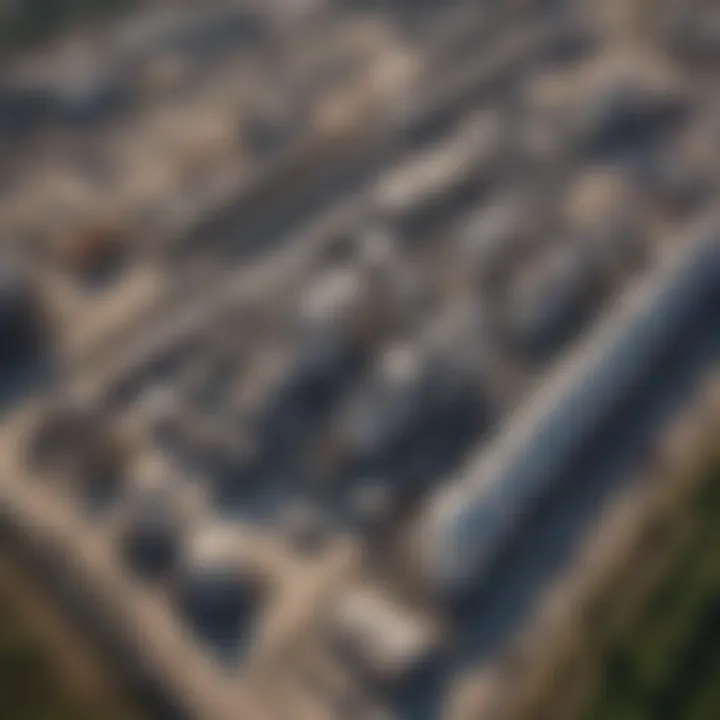
Intro
The evolution of concrete as a construction material is significant in the field of engineering and architecture. Its profound impact on modern infrastructure illustrates its relevance and importance. From the ancient Roman aqueducts to contemporary skyscrapers, concrete has stood the test of time, adapting to various needs and advancements.
Within the sphere of concrete manufacturing, several processes and materials contribute to producing high-quality concrete. Furthermore, the introduction of innovative technologies, such as automated mixing and advanced monitoring systems, enhances efficiency and effectiveness in production. These innovations directly influence the properties of the final product, ensuring that it meets the diverse requirements of modern construction projects.
In recent years, the focus has shifted toward sustainability and environmental considerations in concrete manufacturing. As the industry faces challenges regarding carbon emissions and resource utilization, the exploration of eco-friendly alternatives and practices has become crucial. This aligns with global efforts to mitigate environmental impacts and promote sustainable development in construction.
By understanding the chemistry of concrete, the role of admixtures, and various production techniques, one can grasp both the benefits and challenges associated with concrete manufacturing. This article aims to dissect these components, delivering insights that are both informative and accessible to professionals, students, and researchers alike.
Prelims to Concrete Manufacturing
Concrete plays a vital role in the construction industry. Its versatility, durability, and strength make it a preferred material for various applications, from roads and bridges to buildings and structural components. Understanding concrete manufacturing is not just an academic exercise; it is fundamental for students, researchers, educators, and professionals who aim to grasp the complexities of this essential material. This section aims to lay a solid foundation for the exploration that follows, highlighting key elements such as the processes involved, the types of materials used, and the significance of quality control.
Definition and Importance
Concrete is a composite material made primarily of cement, aggregates, and water. When these components interact, they undergo a chemical process known as hydration, which ultimately results in the hardening of the mixture into a solid mass. This transformation underscores concrete's importance in modern engineering and architecture. The implications of effectively managing concrete production processes extend beyond structural integrity; they influence economic, environmental, and social dimensions of construction. For instance, optimizing concrete mixes can improve not only strength but also reduce waste, aligning with sustainable building practices. Furthermore, quality control in concrete manufacturing assures that the structures built are safe and long-lasting.
Historical Context
The history of concrete dates back to ancient civilizations, with the Romans being notable for their advanced use of the material. Roman concrete, composed of volcanic ash and lime, has withstood the test of time, evident in structures like the Pantheon and aqueducts. The 19th century heralded significant advancements in concrete technology. Joseph Aspdin, an English bricklayer, patented Portland cement in 1824, which became the cornerstone of modern concrete. Today, concrete manufacturing has evolved significantly, incorporating improved materials, technology, and methods, reflecting changes in demands and challenges faced by the construction industry.
Raw Materials in Concrete Production
Raw materials play a critical role in concrete production, as they determine the final characteristics of the concrete mix. The quality and type of these materials directly affect the strength, durability, and workability of concrete. Understanding the raw materials is essential for achieving the desired performance in both structural and aesthetic applications.
Cement Types and Their Characteristics
Cement is a vital binder in concrete. It is responsible for the setting and hardening of the concrete mix. There are several types of cement available, each with its unique properties. The most common types include Ordinary Portland Cement (OPC), Portland Pozzolana Cement (PPC), and Sulfate Resisting Cement (SRC).
Each type serves specific purposes. For instance, OPC is widely used in general construction, while PPC is preferred for its superior resistance to alkali-silica reaction. A significant characteristic of PPC is its reduced heat of hydration, making it suitable for massive structures. Additionally, SRC's resistance to sulfates is vital in environments involving soil interactions rich in sulfates. Understanding these characteristics allows engineers to select the correct cement type for their projects, ensuring the longevity and safety of structures.
Aggregates: The Backbone of Concrete
Aggregates constitute the bulk of concrete. They are divided into coarse and fine varieties. Their primary roles include adding strength, providing resistance to shrinkage and cracking, and improving the overall durability of the concrete mix.
Coarse Aggregates
Coarse aggregates usually range from 4.75 mm to 20 mm in size. Common materials include gravel and crushed stone. The primary characteristic of coarse aggregates is their ability to resist load and transfer stresses efficiently. This feature makes them essential for structural elements, such as beams and slabs.
One unique aspect of coarse aggregates is their interlocking nature, which enhances the strength of concrete by creating a denser structure. On one hand, using high-quality coarse aggregates ensures better concrete compressive strength. On the other hand, the gradation of coarse aggregates can affect the workability of fresh concrete. An imbalance can lead to challenges in placing and finishing, which must be carefully managed during the concrete mix design.
Fine Aggregates
Fine aggregates have smaller sizes, typically passing through a 4.75 mm sieve. Sand is the most common material used in this category. The key characteristic of fine aggregates is their capacity to fill voids between the coarse aggregates, thus improving the density of the concrete mix.
Fine aggregates are crucial for enhancing the workability of the mixture. They provide a smooth texture which aids in the placement and finishing processes. However, if the fine aggregate contains excessive fine particles, it can lead to a reduction in concrete strength. Moreover, the presence of impurities like clay can negatively affect the adhesion between the aggregates and the cement paste.
Water Quality in Concrete Mixes
Water is another essential component in concrete production. Its quality can significantly influence the properties of concrete. Clean water free of contaminants is crucial to avoid detrimental effects on hydration and the final strength of the mix.
Impurities in water, such as oil, organic material, or excessive salts, can lead to complications like delayed setting times or weakened concrete. The water-to-cement ratio is also critical. A lower ratio tends to increase strength, while a higher ratio may lead to lighter but weaker concrete. Understanding water quality is vital for achieving desired material performance and longevity.
Chemical Admixtures: Enhancing Performance
Chemical admixtures are added to concrete mixes to improve specific characteristics. They can alter properties such as setting time, workability, and durability. Common types include water reducers, retarders, accelerators, and air-entraining agents.
Using water reducers, for example, allows for a reduced water-to-cement ratio without sacrificing workability, leading to higher compressive strengths. Retarders are useful in hot weather, preventing rapid setting and providing more working time. Accelerators help in cold conditions, ensuring timely construction progress. Each admixture type serves a different function, and their appropriate use can resolve various practical challenges faced during concrete production.
Understanding and selecting the right raw materials is crucial in concrete manufacturing. Each component brings specific benefits and challenges, and their interplay ultimately defines the performance of the final product. Ensuring quality in these materials leads to stronger, more durable concrete, which is the goal of any construction project.
Concrete Production Process
The concrete production process is a crucial element in the overall manufacturing of concrete. This section delves into the methods and techniques involved, highlighting their significance and benefits. Understanding this process helps ensure quality, efficiency, and sustainability in concrete manufacturing. The production process encompasses batching, mixing, and transportation. Each phase must be executed with precision to maintain the integrity of the final product.
Batching Techniques
Batching is the foundation of concrete production. It involves measuring and combining ingredients accurately to achieve the desired concrete mix. There are two primary batching methods: weight batching and volume batching.
Weight Batching

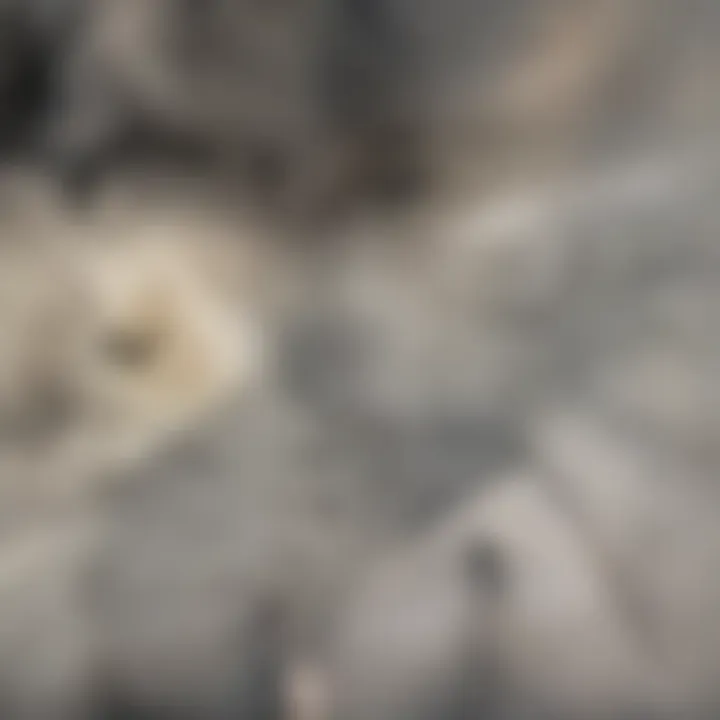
Weight batching is when materials are measured by weight. This method enables precise control over the components of the concrete mix. The primary characteristic of weight batching is its accuracy; it ensures that the correct proportions of sand, aggregates, cement, and water are used. This precision is beneficial for maintaining consistency in concrete quality.
Weight batching is a popular choice due to several factors:
- Accuracy: Minimizes variation in concrete mixes.
- Consistency: Aids in producing uniform results.
- Automation: Facilitates easier integration with automated systems.
Though effective, weight batching can have drawbacks. It often requires specialized equipment, which adds to the initial cost. It also needs careful calibration and regular maintenance to ensure continued accuracy, which can increase operational demands.
Volume Batching
Volume batching involves measuring ingredients by volume rather than weight. This technique relies on standard containers to portion out materials. The key characteristic of volume batching is its simplicity. It is straightforward and does not necessitate complex weighing equipment. Consequently, this method is common in smaller operations or projects with less stringent requirements.
Here are some advantages and disadvantages:
- Advantages:
- Disadvantages:
- Simple to implement and understand.
- Suitable for small-scale projects.
- Less accurate than weight batching, which can lead to inconsistencies.
- Variability in material density can affect results.
Mixing Methods
Mixing is the process where all ingredients blend together to form concrete. This phase is vital to ensure that the mix achieves its targeted properties. Two main mixing methods are commonly used: central mixing and truck mixing.
Central Mixing
Central mixing introduces all materials in a dedicated plant where mixing occurs before transport. The primary characteristic of central mixing is its ability to produce a homogenous mix, which facilitates a more uniform product. This method is particularly advantageous for large projects requiring consistent quality.
Central mixing offers several benefits:
- Uniformity: Ensures consistent quality across batches.
- Efficiency: Allows for larger quantities to be mixed at once.
- Controlled environment: Easier to regulate conditions during mixing.
However, central mixing can require more transportation logistics, which may complicate project management. Additionally, this method often demands a more substantial initial investment in equipment and facilities.
Truck Mixing
Truck mixing involves mixing concrete while en route to the job site. As trucks are equipped with revolving drums, they allow for mixing during transit. This method's key characteristic is convenience, making it suitable for projects requiring rapid delivery.
Truck mixing provides unique features:
- Flexibility: Suitable for remote locations and minimizes logistical challenges.
- Time-saving: Concrete arrives freshly mixed, reducing time on site.
Nevertheless, truck mixing has drawbacks. The mixing quality may vary, and the time from mixing to placement may affect workability. Furthermore, variables such as road conditions can disrupt delivery schedules.
Transport and Placement
Transport and placement are the final steps in the concrete production process. After mixing, concrete must be moved to the work site and placed efficiently. Proper transport methods preserve the concrete's integrity and ensure that it remains workable until placement.
Different methods are available for transport, including:
- Dump trucks: Often used for larger pours.
- Concrete pump trucks: Ideal for hard-to-reach areas.
- Belt conveyors: Useful for continuous placement in large pours.
Placement techniques can involve various tools like chutes, which help guide the mix into position. Ensuring correct handling is essential to avoid segregation and maintain consistency.
Effective transport and placement are critical to the quality and longevity of concrete structures.
Quality Control in Concrete Manufacturing
Quality control in concrete manufacturing is crucial for ensuring the structural integrity and longevity of concrete structures. This encompasses various procedures and tests that confirm concrete meets specified standards before, during, and after production. Quality control plays a pivotal role in preventing failures, enhancing performance, and guaranteeing that the end product aligns with industry specifications.
Concrete is inherently complex due to its varied components, such as cement, aggregates, water, and admixtures. Each of these elements must be precisely controlled. When quality control measures are effectively implemented, they can mitigate issues like shrinkage, cracking, and strength deficiencies. Therefore, investing in rigorous quality control methods is essential for producers aiming to optimize performance and reliability in their concrete products.
Testing Concrete Strength
One of the primary components of quality control in concrete manufacturing is the assessment of concrete strength. This is often measured through compressive strength tests, where concrete samples are evaluated under controlled conditions to determine their load-bearing capacity. Employing standardized testing procedures, such as ASTM C39, helps provide reliable data that can influence project planning and execution.
Regular strength testing is essential to guarantee adherence to structural requirements. For example, inadequate strength can compromise the safety and durability of a building. Through consistent testing, manufacturers can also ensure that their production processes have not deviated and that mix designs remain effective.
Monitoring Fresh Concrete Properties
Monitoring the properties of fresh concrete is another vital facet of quality control. This involves evaluating aspects such as workability, setting time, and temperature. Accurate monitoring ensures that concrete can be efficiently placed and finished without issues.
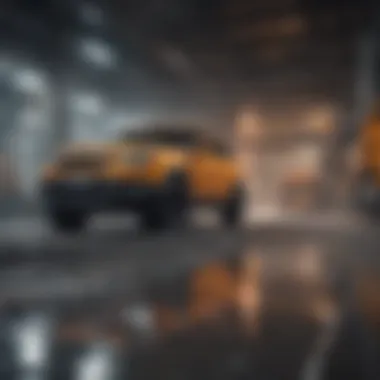
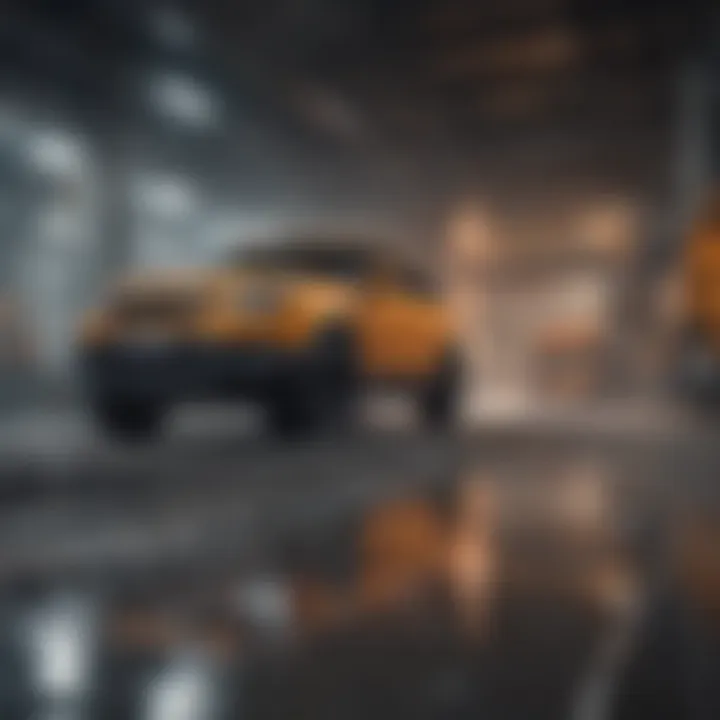
Slump Test
The slump test is a widely used method for assessing the workability of fresh concrete. It involves filling a cone-shaped mold with concrete and measuring the vertical drop, or slump, after the mold is removed. The key characteristic of the slump test is its simplicity and speed, making it a popular choice in the field.
Advantages of the Slump Test:
- Quick Results: It provides immediate feedback on mix consistency.
- Field Application: It can be performed on-site without extensive equipment.
However, the slump test does have its limitations. It primarily assesses workability in terms of flow but does not account for other important factors like cohesion. As such, it should be combined with other tests for a comprehensive evaluation.
Temperature Management
Temperature management is another critical aspect of quality control. The temperature of fresh concrete can significantly influence its strength and durability. Excessive heat can lead to rapid setting and cracking, while low temperatures slow down hydration processes, compromising strength gains. A key characteristic of effective temperature management is maintaining optimal hydration conditions throughout the curing process.
Advantages of Temperature Management:
- Stability: Helps ensure consistent hydration and strength development.
- Prevention of Defects: Reduces risks of thermal cracking and other temperature-related issues.
Managing temperature can involve techniques such as using chilled water or ice, adjusting the timing of placements, or employing insulation. Understanding and implementing effective temperature management can greatly enhance concrete durability over its life cycle.
Long-term Durability Tests
Lastly, conducting long-term durability tests serves as an effective strategy for assessing the lifespan of concrete structures. These tests evaluate how concrete holds up against environmental stresses over time. Factors such as freeze-thaw cycles, chemical exposure, and moisture levels all play a role in the durability of concrete.
Implementing long-term durability testing allows manufacturers to identify weaknesses in their products and make necessary adjustments in their processes or mix designs. This commitment to durability not only strengthens the concrete itself but also improves overall confidence in the materials used in construction projects.
Sustainability in Concrete Manufacturing
Sustainability in concrete manufacturing is a critical aspect of the industry's modern transformation. With increasing concerns over climate change and resource depletion, the push for more sustainable concrete practices is more important than ever. This section explores various elements of sustainability, emphasizing their benefits and the considerations for concrete manufacturers.
Recycled Aggregate Use
Recycled aggregate use represents a key area for enhancing the sustainability of concrete production. This involves reusing materials from demolished or unused concrete structures. By incorporating recycled aggregates, manufacturers can conserve natural resources, reduce landfill waste, and minimize carbon emissions associated with quarrying.
Notably, recycled aggregates can have comparable performance characteristics to their natural counterparts when properly processed. However, it is essential to ensure their quality through appropriate screening and testing. Benefits include lower material costs and a decrease in the environmental footprint of concrete production.
Eco-friendly Admixtures
Eco-friendly admixtures play a significant role in improving the sustainability of concrete mixtures. These substances can enhance the performance of concrete while reducing its environmental impact. For instance, the use of industrial by-products such as fly ash and slag can replace portions of cement, leading to reduced energy consumption and lower greenhouse gas emissions.
Moreover, some admixtures enhance the durability of concrete, further extending its lifespan. This reduces the need for repairs or replacements in the long term, contributing to resource conservation. The integration of eco-friendly admixtures into concrete formulations reflects a proactive approach to sustainability in the industry.
Reducing Carbon Footprint in Production
Reducing the carbon footprint in concrete production is vital for achieving sustainability goals. The cement industry is a significant source of carbon dioxide emissions globally. Strategies to minimize this impact include optimizing production processes, utilizing renewable energy sources, and incorporating alternative materials.
Efforts to enhance energy efficiency in cement kilns and improve logistics can result in considerable emission reductions. Additionally, the adoption of carbon capture technologies offers significant promise to offset emissions from traditional cement production.
Implementing these strategies not only benefits the environment but can also lead to cost savings for manufacturers. The shift towards an eco-friendly production model is increasingly becoming a competitive advantage in today's market.
"Concrete industry must innovate to meet the demands of sustainability while maintaining quality and durability."
In summary, sustainability in concrete manufacturing encompasses a range of practices, from recycling materials to reducing emissions. The continuous evolution of technology and materials in this field offers pathways toward a more sustainable future for construction.
Innovative Trends in Concrete Technology
Innovative trends in concrete technology are reshaping the construction industry. These trends enhance efficiency, durability, and sustainability, allowing concrete to meet the demands of modern infrastructure needs. As the industry evolves, there is a continual push toward integrating new methods and materials that address challenges faced in traditional concrete production.
Embracing innovation in concrete manufacturing enables engineers to develop solutions that minimize risks associated with structural failure, environmental impact, and production costs. The introduction of advanced technologies not only improves the performance characteristics of concrete but also revolutionizes the way structures are designed and built.
Self-healing Concrete
Self-healing concrete represents a significant advancement in building materials. This technology enables concrete to repair its own cracks autonomously, extending the lifespan of structures and reducing maintenance costs. When fractures occur, healing agents embedded in the concrete activate, filling gaps and restoring integrity. This concept relies on specific chemical reactions, often using microorganisms or special polymers, that bond with the surrounding concrete.
Benefits of self-healing concrete include:
- Reduced Maintenance: Less frequent repairs lower overall costs and labor.
- Sustainability: Extending the lifespan of structures conserves resources and minimizes environmental disturbance.
- Improved Safety: Maintaining structural integrity reduces risks associated with failure, improving safety for users.
As more research emerges, scalability and efficiency in production will improve, making self-healing concrete a viable option for widespread application.
3D Printing with Concrete
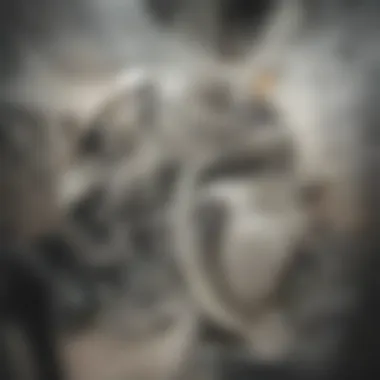
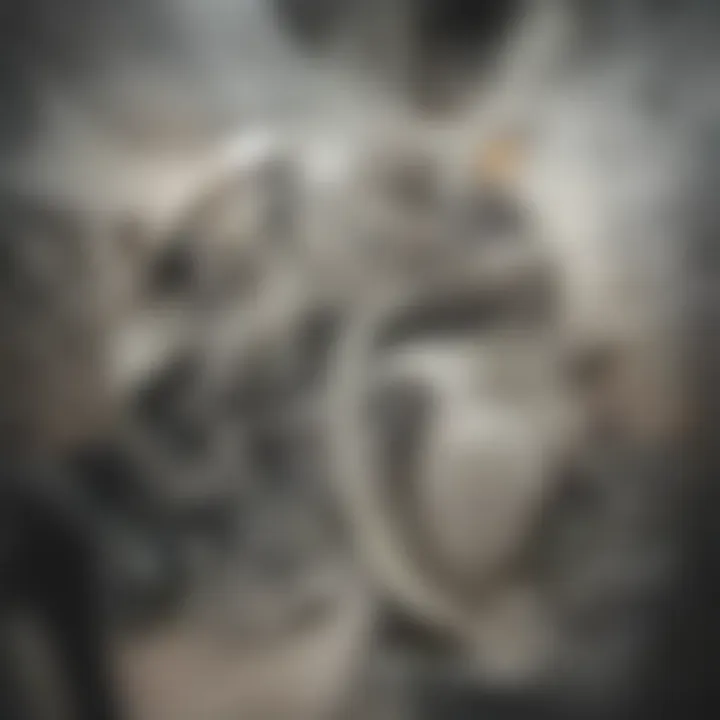
3D printing technology in concrete has gained momentum due to its potential to create complex shapes that traditional methods cannot achieve. This approach allows for rapid construction, reducing labor costs and project timelines. It leverages computer-aided design to produce layers of concrete, which can be customized to suit specific architectural needs.
Positive aspects of 3D printing with concrete include:
- Design Flexibility: Architects can explore innovative shapes and structures without the constraints of standard forms.
- Material Efficiency: Minimizing waste is a crucial aspect, as only the required amount of material is used in the design.
- Faster Construction: Projects can progress significantly faster due to the automated nature of 3D printing.
The potential applications range from housing to intricate public installations, reshaping urban landscapes through efficient design solutions.
Smart Concrete: Integration with Technology
Smart concrete involves the incorporation of sensors and advanced materials to monitor the condition of structures in real-time. This innovative concrete type can detect stress, temperature changes, and pressure, providing crucial data for assessment and maintenance planning.
Key features of smart concrete technology include:
- Real-time Monitoring: Enables timely interventions before issues become critical.
- Data Collection: Informs future construction projects and enhances understanding of material behavior under various conditions.
- Safety Enhancements: Continuous monitoring can prevent accidents by identifying potential structural weaknesses promptly.
As both the technology and data analysis techniques evolve, the integration of smart components into concrete will become commonplace, offering businesses essential tools for efficient operation and risk management.
In an industry that constantly seeks improvement, adopting innovative trends in concrete manufacturing plays a vital role in enhancing resilience and sustainability in civil engineering.
Challenges in Concrete Manufacturing
Understanding the challenges in concrete manufacturing is essential for professionals in the construction and materials industry. These challenges encompass various aspects such as supply chain disruptions, regulatory compliance, and market competition. Addressing these issues is crucial for maintaining a robust and efficient production process, which directly impacts the quality of concrete and, subsequently, the longevity of structures.
Supply Chain Issues
Supply chain issues present a significant challenge in concrete manufacturing. These disruptions can arise from various factors, including raw material shortages and transportation delays. As concrete production heavily relies on specific raw materials like cement, aggregates, and water, any hiccup in their availability can lead to production setbacks.
"The complexity of the supply chain in concrete production can sometimes lead to delays and increased costs, impacting projects significantly."
To mitigate these challenges, manufacturers must establish reliable sources for raw materials and create strategic partnerships with suppliers. Transparency and communication are key in this process. Companies must forecast demand accurately and plan material procurement accordingly. Ensuring a well-established supply chain can enhance the resilience of the manufacturing process against unforeseen events.
Regulatory Compliance and Standards
Regulatory compliance is another essential aspect of concrete manufacturing. The industry is subject to stringent regulations concerning safety, environmental impacts, and quality standards. Adhering to these regulations is not merely about avoiding penalties; it ensures that the products are safe and sustainable.
Manufacturers must stay updated on changes in legislation and industry standards. This requires frequent training for staff and investment in processes that promote compliance. Specifically, understanding the necessary codes and specifications can lead to improved product quality and reduced liability risks. For instance, following guidelines provided by the American Concrete Institute can result in better performance and safer structures.
Market Competition
Market competition in the concrete manufacturing sector is intense. It is vital for businesses to innovate and differentiate their products. This competition often leads to price wars, which can compromise quality if companies cut corners to reduce costs.
In responding to this challenge, manufacturers should focus on enhancing their production techniques and exploring new technologies. Continuous improvement in product offerings, such as introducing eco-friendly options or high-performance concrete solutions, can set a company apart from its competitors.
Key strategies to overcome market competition include:
- Investing in research and development.
- Building brand reputation through quality assurance.
- Offering excellent customer service and engagement.
Future of Concrete Manufacturing
The future of concrete manufacturing is imperative for advancing construction methods and addressing environmental challenges. With increasing urbanization and the pressing need for sustainable practices, innovative solutions are essential. This section explores the emerging trends and areas of research that could redefine concrete as a primary building material.
Emerging Research Areas
Research in concrete technology is evolving rapidly. New materials and methods are being developed to improve performance, durability, and sustainability. Some key areas of focus include:
- Nanotechnology: Enhancing the properties of concrete by incorporating nanoparticles can improve strength and reduce permeability.
- Bio-based materials: Exploring natural fibers alongside traditional aggregates can lead to lighter, more eco-friendly concrete mixtures.
- Smart materials: Research on materials that respond to environmental changes could pave the way for concrete that adapts to varying conditions, improving longevity and safety.
By investing in these research areas, the concrete industry can reinforce its relevance while meeting the demands of future construction projects.
Regenerative and Circular Economies
The transition to regenerative and circular economies is crucial for sustainable development in concrete manufacturing. This approach emphasizes minimizing waste and maximizing resource efficiency. Key principles include:
- Material Reuse: Implementing systems for reclaiming concrete from demolished structures can significantly reduce waste.
- Recycling: Integrating recycled aggregates into new concrete blends conserves natural resources and lowers carbon emissions.
- Life Cycle Assessment (LCA): This evaluates the environmental impacts of concrete production from raw material extraction to disposal, guiding more sustainable practices.
Embracing these principles not only benefits the environment but also enhances the economic viability of concrete projects.
Potential for Urban Applications
Urbanization presents unique challenges and opportunities for concrete manufacturing. As cities grow, the demand for innovative concrete solutions increases. For example:
- High-performance concrete can meet the needs of skyscrapers, offering strength and lightweight characteristics without compromising safety.
- Porous concrete aids in stormwater management by allowing water to permeate, reducing urban flooding.
- Modular construction utilizing precast concrete elements can speed up construction timelines while maintaining high quality.
The ability to adapt concrete applications for diverse urban environments makes it a versatile material for future built environments.
"An integrated approach towards concrete manufacturing can bridge sustainability and functionality, ensuring the industry remains relevant in a changing world."
Investing in these innovative areas is vital for solidifying concrete's role in future construction, creating a resilient infrastructure that aligns with the demands of contemporary society.