Ceramics in Aerospace: Innovations and Applications
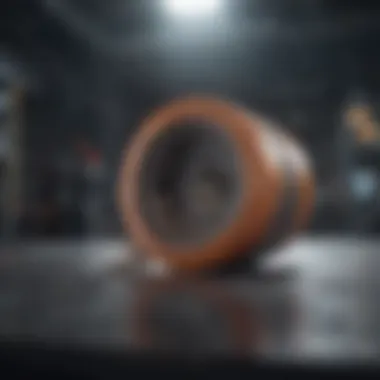
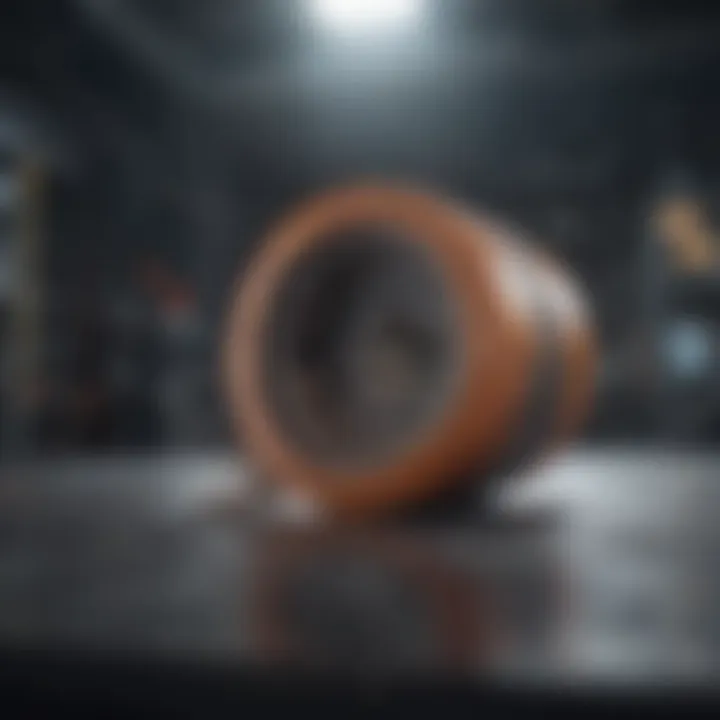
Intro
The realm of aerospace engineering stands at the intersection of tradition and innovation, where the quest for strength, lightweight materials, and heat resistance culminates in groundbreaking advancements. One such advancement is the integration of ceramics, whose exceptional properties address demands of modern aerospace applications. Unlike metals, which have dominated the industry for decades, ceramics bring unique characteristics that merit a closer look.
In the world of flying machines, how do materials behave under extreme conditions? How do they hold up against high stresses or temperature fluctuations? That’s where ceramics come into play. These materials boast extraordinary resistance to thermal and mechanical stresses, fulfilling a role of paramount importance in the field.
But what exactly makes ceramics so appealing? Their inherent low density combined with superior strength opens up avenues for applications in components that were once thought to be limited to metals. In addition, recent innovations in manufacturing processes have made ceramics more accessible and practical for diverse aerospace applications.
As we unravel the extensive narrative around ceramics in aerospace, we're going to navigate through their properties, manufacturing techniques, and applications. We will highlight both the achievements and the challenges encountered in their integration. Turning the pages of advancements in ceramics can reveal a future of possibilities that enhance efficiency, durability, and perhaps even reimagine how we look at aircraft design and functionality.
So, whether you’re a researcher delving into material science or an educator shaping the minds of tomorrow, understanding the contribution of ceramics in the aerospace sector will be pivotal in any discourse surrounding innovation and progress.
Foreword to Ceramics in Aerospace
The aerospace industry constantly pushes the boundaries of technology and materials science. Within this landscape, ceramics have emerged as a game-changer, playing a crucial role in enhancing performance and efficiency. The importance of ceramics is not just a fleeting trend; it is rooted in their exceptional properties, including thermal resistance, mechanical strength, and lightweight characteristics. Understanding ceramics is paramount for anyone involved in aerospace engineering, from students and researchers to seasoned professionals.
As aerospace applications demand materials that withstand extreme conditions—think blistering temperatures during re-entry or high pressures at cruising altitude—ceramics offer unparalleled advantages. They are not only able to endure these harsh scenarios but can also help improve fuel efficiency and reduce greenhouse emissions by facilitating lighter designs. Furthermore, the integration of ceramics can drive advancements in engine performance, safety, and overall durability of aerospace structures.
In this section, we will dive deeper into the specifics of what ceramics are and survey the historical context of their use in aerospace applications.
Understanding Ceramics
Ceramics encompass a broad range of materials made from inorganic compounds, typically involving a combination of metallic and non-metallic elements. The term itself often brings to mind traditional applications such as pottery and tiles, yet in the aerospace context, ceramics take on a more advanced and significant role.
Ceramics can be classified into two main groups: traditional ceramics and advanced ceramics. While traditional ceramics are often used for insulators, tableware, and building materials, advanced ceramics find their place in technological applications. These materials are engineered to exhibit remarkable properties tailored to specific needs, particularly in extreme environments where typical metals would fail.
Key characteristics that distinguish ceramics include:
- High hardness: This makes them excellent for wear resistance.
- Low thermal conductivity: Crucial for thermal insulation in aerospace components.
- Chemical stability: Ensures longevity in the face of harsh chemical environments.
- Electrical insulation: This property is important for several aerospace sensors and components.
Historical Context of Ceramic Materials in Aerospace
The journey of ceramic materials in aerospace engineering isn't just a modern tale. It takes roots back into the early 20th century when engineers began exploring materials that could withstand high temperatures—an essential requirement for aircraft and engine design. In the 1950s, the development of jet engines created a pressing need for materials that could maintain structural integrity under heat and stress, paving the way for the introduction of ceramics.
In the following decades, vast advancements were made, driven by the space race and the quest to create materials that could endure re-entry into the Earth's atmosphere. These early iterations of space shuttles relied heavily on ceramic tile technology, which famously protected crafts from the extreme heat generated during re-entry. Much of the knowledge gained during that era served as a springboard for the innovations we see in ceramics today.
The use of ceramics in modern aerospace design continues to evolve. Research into newer composites and ceramics, such as silicon nitride and zirconium oxide, highlights the ongoing quest to leverage these materials' properties for future aerospace applications. Just like a fine wine that improves over time, the role of ceramics in aerospace is a testament to human ingenuity and the relentless pursuit of perfection in engineering.
Properties of Ceramic Materials
The investigation into the properties of ceramic materials is essential for grasping how these materials function effectively in the complex realm of aerospace engineering. Unlike metals or plastics, ceramics come with their unique characteristics that can be pivotal, yet demanding, in aviation environments. With high mechanical strength, outstanding thermal resistance, and excellent corrosion resistance, ceramics offer an array of benefits that align with the hefty demands of modern aerospace technology. The selection and application of these materials hinge on understanding their properties, which allows engineers to tailor solutions that meet stringent performance requirements.
Mechanical Strength
Mechanical strength is a cornerstone of ceramic properties, establishing ceramics as formidable candidates for load-bearing applications. The tensile and compressive strengths of ceramics not only withstand static loads but can also endure sudden impact forces. For instance, many aerospace structures need to resist significant forces as they encounter airflow and turbulence during flight. Notably, advanced ceramics like silicon carbide are recognized for their robust performance in these aspects. Furthermore, while ceramics can be brittle, their failure can often be predictable and non-catastrophic under controlled conditions, which is vital for maintaining safety standards in aviation.
Thermal Resistance
The ability of ceramics to endure high temperatures without deforming or losing structural integrity is crucial in aerospace applications. The phenomenon of thermal resistance stems from their atomic structure, which allows them to maintain their shape and functionality even in extreme heat environments, such as near jet engine components or during re-entry into the Earth's atmosphere. Materials like zirconium dioxide can tolerate temperatures above 2000 degrees Celsius, making them suitable for thermal protection systems in spacecraft. This capability significantly extends the lifespan of components under thermal stress, ultimately leading to a more reliable aerospace system.
Corrosion Resistance
Ceramics exhibit remarkable corrosion resistance, a property that plays a significant role in extending the operational lifespan of aerospace components. Due to their chemical stability, ceramics can withstand hostile environments filled with oxidative elements or other corrosive agents. For example, alumina ceramics are frequently used in humid or salt-laden atmospheres found at sea, protecting sensitive parts from degradation. Their resistance to wear and chemical attacks ensures lower maintenance and replacement costs, which is a critical consideration in the aerospace industry where reliability is paramount.
Electrical Insulation Properties
The electrical insulation properties of ceramics are invaluable, particularly for components involved in sensor and electronics systems in aerospace applications. Ceramics like barium titanate demonstrate excellent insulating capabilities and can withstand high voltages without breakdown. This makes them suitable for dielectric materials in capacitors or as insulation layers in electronic devices. Moreover, their ability to manage heat generated from electrical paths helps maintain component integrity in various operating conditions, further enhancing their role in modern aircraft and spacecraft.
"Ceramics stand apart in aerospace not just for their strength, but for their resilience against time and harsh conditions, making them a vital element in engineering innovation."
In summary, comprehensively understanding the mechanical strength, thermal resistance, corrosion resistance, and electrical insulation properties of ceramics is crucial for modern aerospace engineering applications. These properties work synergistically to create components that not only withstand the rigors of flight but also enhance the overall efficiency and durability of aircraft and spacecraft.
Types of Ceramics Used in Aerospace Applications
The aerospace industry hinges on precision, safety, and the ability to withstand extreme conditions. Among the myriad materials available, ceramics stand out due to their unique properties and versatile applications. Their significance is evident in various components, offering advantages that other materials may lack. Understanding the types of ceramics utilized in this field is crucial for recognizing how they contribute to aviation advancements and the overall safety and efficiency of aerospace vehicles.
Oxide Ceramics
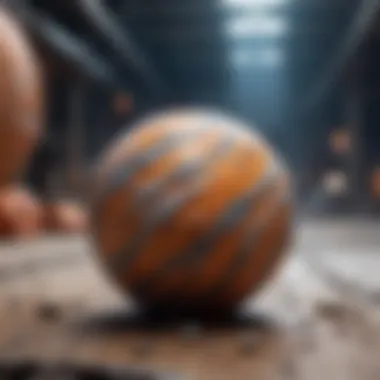
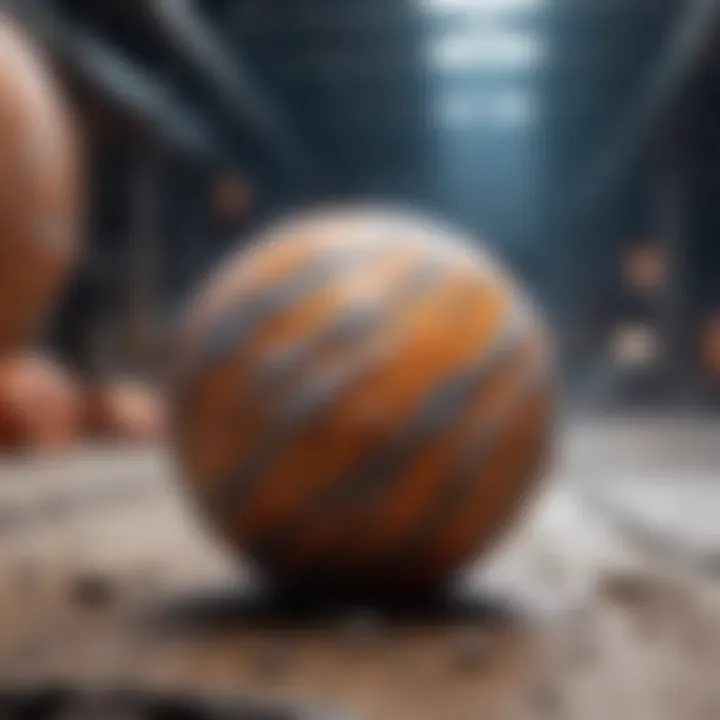
Oxide ceramics are perhaps the most familiar category, renowned for their thermal stability and resistance to harsh environments. Composed primarily of oxides, these materials excel at high temperatures. For instance, alumina and zirconia are commonly used in thermal protection systems due to their ability to maintain performance without degrading. The lightweight nature of these ceramics also helps in reducing the overall mass of aircraft and spacecraft, a critical consideration in aerospace design.
Additionally, oxide ceramics often display excellent electrical insulating properties, which are beneficial in electronic applications within aerospace systems. This combination of heat resistance and insulation makes oxide ceramics invaluable.
"The future of aerospace engineering is not just about flying higher but also smarter, and materials like oxide ceramics pave the way for that evolution."
Non-Oxide Ceramics
When discussing non-oxide ceramics, materials such as silicon carbide and boron carbide come into play. These ceramics are known for their exceptional hardness and wear resistance, making them suitable for engine components, such as heat exchangers or seals. Non-oxide ceramics offer significant advantages in environments subjected to abrasion and wear.
However, one must also consider their brittleness compared to their oxide counterparts. While they perform admirably under certain conditions, their sensitivity to impact and fracture is a factor that engineers must account for during design and testing phases.
In the aerospace context, non-oxide ceramics often serve as armor, providing protection against physical and thermal stresses, thus enhancing the overall safety of aircraft and crew.
Composite Ceramics
Composite ceramics are like the superheroes of the aerospace material world, combining the best features of different types of ceramics. By integrating materials like fibers or particulates, these composites can optimize properties such as strength, thermal resistance, and overall durability. A prime example is the carbon-fiber-reinforced ceramic matrix composites, which are lightweight yet incredibly strong.
These advanced materials are frequently employed in applications where both thermal stability and mechanical integrity are required, such as in thermal protection systems and high-performance turbine components.
Bay sometimes, the complexity of manufacturing these materials can present hurdles. Ensuring the uniformity of composites while maintaining desired properties requires careful consideration and control during production.
In short, the diverse types of ceramics utilized in aerospace applications each offer distinct benefits and considerations. The moving parts of the aerospace industry rely on these materials to ensure that vehicles withstand the test of time and rigorous conditions, keeping safety paramount. Innovations in this field continue to shape the future of flight, highlighting the enduring relevance of ceramics in aerospace.
Manufacturing Processes for Aerospace Ceramics
When it comes to aerospace ceramics, the manufacturing processes are the backbone of innovation and functionality. Understanding these processes is crucial because they directly affect the properties of the final ceramic materials, which in turn influences the reliability and performance of aerospace components. Given the demanding conditions found in aerospace environments, the processes chosen must not only ensure quality but also adhere to strict industry standards.
The significance of effective manufacturing processes cannot be understated; they allow for the precise control of material characteristics such as density, microstructure, and porosity. These features determine a ceramic's ability to withstand extreme temperatures and pressures, making them essential for applications like thermal protection systems and intricate engine components.
Traditional Methods
Traditional methods of manufacturing ceramics have evolved over centuries and are foundational to obtaining high-quality products. Common techniques include:
- Hand Molding: A straightforward approach where artisans shape the ceramic material manually before firing it.
- Slip Casting: This process involves pouring a liquid clay mixture into a mold. It is particularly useful for creating complex shapes with fine details.
- Pressing: Applying mechanical force to compact ceramic powders into a certain shape. This technique is well-suited for producing uniform solid shapes, typically used in structural components.
The simplicity of these techniques can be appealing, especially in terms of cost and accessibility. However, they often fall short in scalability and precision compared to modern methods.
Advanced Techniques
As demand for more sophisticated materials has grown, so too have the manufacturing techniques. Advanced methods enable higher precision and customization. Some notable examples include:
- Sintering: This technique involves heating compacted powders below their melting points to create dense, durable structures. Different atmospheres and temperatures can be used to achieve desired properties.
- Hot Pressing: Combining pressure and heat simultaneously, this method enhances the density and durability of ceramics without generating cracks.
- Spark Plasma Sintering: An innovative technique that uses electrical pulses to heat the material rapidly, allowing for finer control over the material properties while reducing processing time significantly.
These advanced techniques represent the shift toward more controlled and efficient manufacturing that can lead to higher-performing materials, essential for today’s aerospace applications.
Additive Manufacturing of Ceramics
Additive manufacturing, commonly known as 3D printing, is a game changer in the production of ceramics for aerospace. This method involves building structures layer by layer, resulting in highly complex geometries that traditional methods may struggle to achieve. With additive manufacturing, significant advantages include:
- Customization: Tailored designs can be produced without the need for expensive molds, promoting creativity and innovation.
- Material Efficiency: Only the necessary material is used, leading to less waste compared to conventional methods.
- Rapid Prototyping: Speedy production allows for quick iterations in design, enabling engineers to test and modify designs efficiently.
The impact of additive manufacturing on aerospace ceramics is still unfolding, but it holds promise for creating lightweight and multifunctional components that push the limits of what can be achieved.
"The future of aerospace ceramics relies heavily on the ability to adapt manufacturing processes to the specific demands of applications, ultimately shaping the industry’s landscape."
In summation, the manufacturing processes for ceramics in aerospace are paramount not just for quality, but for advancing the capabilities of materials that can withstand extreme conditions. As the field continues to evolve, both traditional and innovative methods will play essential roles in shaping the future of aerospace engineering.
Applications of Ceramics in Aerospace Engineering
Ceramics have carved a niche for themselves in the realm of aerospace engineering, primarily due to their unique set of properties that cater to the demands of modern aviation and space exploration. Their inherent benefits—high strength-to-weight ratios, temperature resilience, and corrosion resistance—play pivotal roles in the creation and maintenance of aerospace components. This section delves into the specific applications of ceramic materials, sheding light on how they enhance operational efficiency and safety while tackling significant engineering challenges.
Thermal Protection Systems
In the aerospace industry, thermal protection is crucial for spacecraft and high-speed aircraft that encounter intense heat during flight, particularly during atmospheric re-entry. Ceramic materials, such as silica tiles and ceramics like silicon carbide, are invaluable in these situations due to their ability to withstand extreme temperatures without melting. These ceramics are often lightweight yet durable enough to endure significant thermal stress.
For instance, the Space Shuttle utilized rigid tiles made from thermal protection ceramics to safeguard its structure during re-entry into Earth's atmosphere. The tiles were designed to dissipate heat effectively, preventing damage and ensuring the shuttle's safely return. This practical application of ceramics not only highlights their efficiency in thermal management but also underlines their importance in advancing aerospace technologies.
Engine Components
Engine performance is a critical aspect of aerospace engineering, where every ounce of weight and every degree of efficiency matters. Ceramics are often found in various engine components, such as turbine blades and combustion chambers, where they can withstand high-pressure environments and extreme heat.
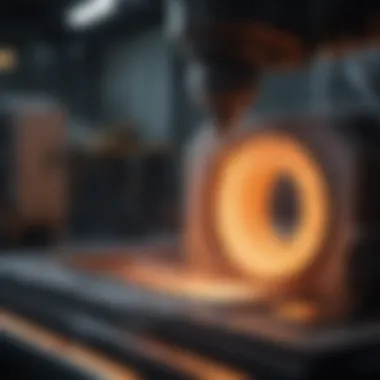
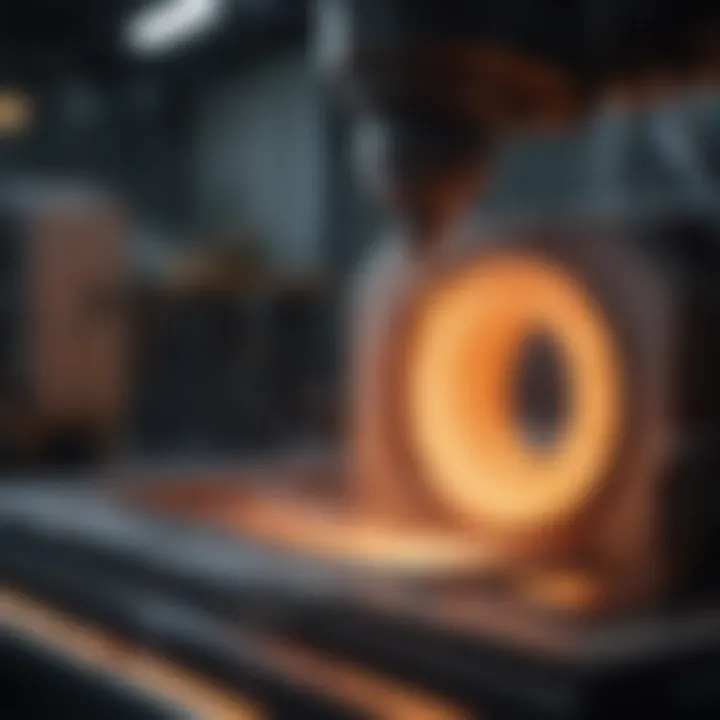
Ceramic matrix composites (CMCs), for example, enhance the durability of engine parts while significantly reducing weight. By incorporating ceramic fibers into a resin, manufacturers can create components that not only resist thermal degradation but also maintain structural integrity at high pressures. This is particularly relevant in jet engines, where efficient fuel consumption translates into reduced operational costs and enhanced performance. The development of ceramics for engine components represents a significant leap in aerospace material science, marrying weight reduction with heat resistance.
Structural Components
The structural integrity of an aircraft is non-negotiable; without it, safety is compromised. Ceramics are increasingly utilized in structural components due to their high strength and lightweight properties.
For instance, structural ceramics are leveraged in the design of airframes, where minimizing weight without sacrificing structural performance is critical. Lightweight ceramics can replace heavier materials, contributing to fuel efficiency and performance enhancements in aircraft design. Moreover, using ceramics in creating aerostructures can also lead to improved resistance to dynamic and static loads, thereby extending the lifespan of the components and minimizing maintenance needs.
Sensors and Electronics
As aerospace technology advances, the role of electronics and sensors becomes ever more vital. Ceramics also play a crucial role in this domain. They possess excellent insulating properties, making them ideal for electrical components in aircraft and spacecraft.
Examples include the use of piezoelectric ceramics in sensors that monitor structural health and performance in real-time. Piezoelectric materials can convert mechanical stress into electrical signals, providing critical data on how aircraft are performing under various conditions. Additionally, ceramic capacitors are instrumental in managing power systems across various aircraft systems. Their reliability under varying temperatures and environmental conditions ensures that electronic systems function optimally even in the harshest settings.
"The use of ceramics in aerospace not only promotes higher performance and reliability but also proves essential in meeting safety regulations for modern aircraft design."
Performance of Ceramics in Extreme Conditions
The role of ceramics in aerospace is fascinating and vital, particularly when we talk about their performance in extreme conditions. Aerospace applications often thrust materials into challenging environments, where factors like temperature, pressure, and aerodynamic forces can cause significant stress. This performance aspect is not merely a side note; instead, it’s absolutely central to their overall utility and reliability in aerospace settings.
Ceramics are known for their remarkable ability to withstand high temperatures, making them suitable for components like thermal protection systems and engine parts. This high-temperature resistance is critical, especially when dealing with re-entry situations where temperatures can soar over a thousand degrees Celsius. Similarly, the capacity to endure high pressures, such as those experienced during flight, is another crucial aspect that defines their application in fuselage and engine components. To cap it off, understanding how ceramics handle aerodynamic forces can influence design choices, optimizing efficiency and safety in aerospace engineering.
High Temperatures
When it comes to high temperatures, ceramics shine brighter than many conventional materials. Their thermal stability enables them to maintain their structural integrity even when exposed to extreme heat. Take, for instance, silicon carbide, often hailed for its exceptional thermal resistance. In aerospace, materials like silicon carbide are used in thermal protection systems due to their ability to withstand rapid thermal fluctuations and resist oxidation.
The significance of high thermal performance cannot be overstated. It allows components to operate in intense environments, such as the atmospheres surrounding rocket engines during launch or satellites re-entering Earth's orbit. By utilizing ceramics that can endure these extreme temperatures, engineers can design safer, more efficient systems that last longer, ultimately leading to cost savings over time.
"The ability of ceramics to resist thermal shock and extreme heat is key; it allows for safer exploration in unpredictable environments."
High Pressure
High pressure poses another challenge in aerospace applications, one where ceramics prove their worth. While metals can often deform under extreme pressure, certain ceramics maintain their stiffness and strength, providing a stable framework for various components. This attribute is particularly crucial in engine components where high pressures are common.
For example, ceramic matrix composites can withstand the kind of intense pressures found in combustion chambers. These materials are engineered to combine the high strength of ceramics with a lightweight structure, significantly enhancing performance. The ability to perform under high-stress conditions can lead to lighter, more efficient designs, offering great advantages in aerospace performance.
In sum, the performance of ceramics under high pressures contributes to greater safety and reliability in aerospace engineering, allowing for more ambitious designs and missions.
Aerodynamic Forces
Lastly, let’s consider how aerodynamic forces affect ceramics. In the high-speed realm of aerospace, planes and rockets experience significant forces that can influence material performance. While metals often bend or warp under strain, ceramics, with their rigid structure, offer a reliable alternative that can stand up to these forces.
Ceramics are also being developed to create aerodynamically efficient shapes. Their lightweight nature is crucial in reducing drag, enhancing fuel efficiency in aircraft, and improving propulsion systems. In wind tunnel testing, ceramic components have exhibited strength without a substantial increase in mass, illustrating their potential in lightweight designs that do not compromise on performance.
In summary, understanding the performance of ceramics in extreme conditions—high temperatures, high pressures, and aerodynamic forces—sheds light on their indispensable role in pushing the boundaries of aerospace engineering. As innovations continue, it’s clear that ceramics will remain a cornerstone material for future advancements.
Challenges in Implementing Ceramics in Aerospace
The adoption of ceramics within aerospace engineering is not without hurdles. While ceramic materials boast impressive properties such as high-temperature resistance and low weight, their implementation in practical applications poses varied challenges. Understanding these challenges is crucial for advancing aerospace technology. From brittleness to manufacturing constraints and cost factors, each aspect plays a significant role in shaping the future of ceramics in this field.
Material Brittleness
One of the foremost concerns surrounding ceramic materials in aerospace is their inherent brittleness. Ceramics generally lack the ductility found in metals; as a result, they are prone to crack under stress. In environments where components must endure extreme forces—like during rapid acceleration or in the rapid decompression of altitude changes—this brittleness can lead to catastrophic failures.
While engineers can design ceramic components to enhance resistance to fracture, it doesn’t eliminate risks completely. For example, advancements in composite ceramics aim to mitigate brittleness by introducing toughening mechanisms. However, achieving the right balance between toughness and lightweight properties remains a nuanced challenge.
"The key to breakthroughs is understanding how different forces interact with ceramic structures in real-world scenarios."
Manufacturing Limitations
The production of ceramic components faces its own set of limitations. Traditional methods such as sintering and pressing can yield exceptional results but often come with significant constraints. For instance, the precision required in creating intricate designs may not always be achievable using conventional manufacturing processes. Advanced techniques like 3D printing are emerging as promising alternatives, yet they still encounter challenges in material compatibility and process reliability.
The uniqueness of ceramic materials can also complicate batch production. Variability in raw materials can affect the final product's performance, leading manufacturers to invest heavily in quality control measures. Consistency in ceramic product quality is paramount, given the high-stakes nature of aerospace applications.
Cost Considerations
When it comes to budgeting, ceramics can be a double-edged sword. While the potential for lightweight and high-performance components often makes them attractive for aerospace companies, the associated costs can be significant. The complexity of manufacturing processes and the prices of specialized materials contribute to these expenses.
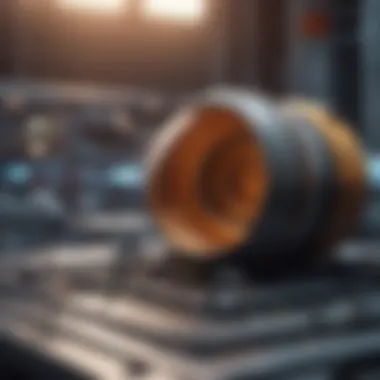
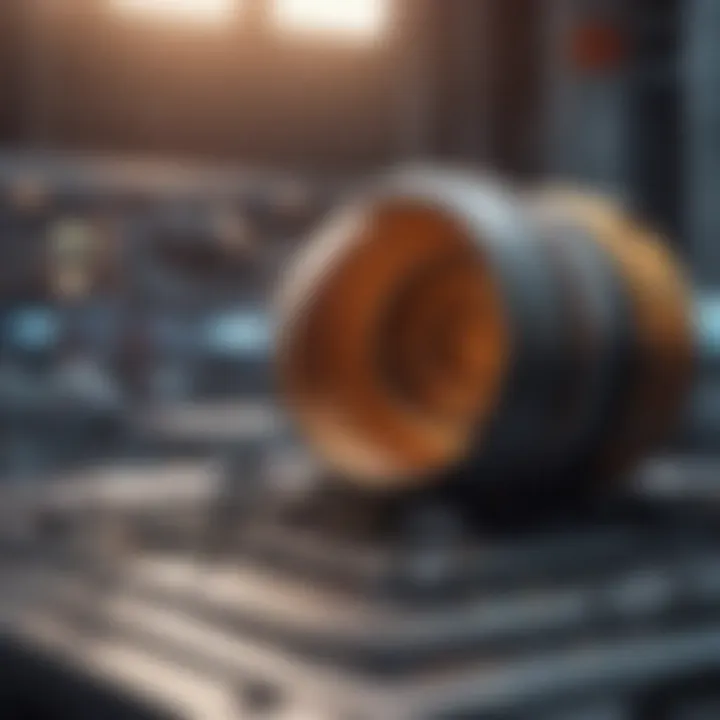
Moreover, investment in research and development to enhance ceramic technology is non-negotiable. As companies strive to innovate, they often find themselves at a crossroads: it’s essential to balance financial feasibility with the pursuit of cutting-edge materials that push the envelope.
This cost dilemma can sometimes stifle the widespread acceptance of ceramics in aerospace, especially compared to traditional materials that are well understood and have established supply chains. Nonetheless, as technology improves and economies of scale are achieved, the financial outlook for ceramics may become more favorable in the long run.
Future Directions in Ceramics Research for Aerospace Applications
In this ever-evolving field of aerospace engineering, ceramic materials are generating considerable excitement. The advancements made in specific areas cater to increasing performance requirements and environmental considerations. Future directions in ceramics research hold promise of unleashing capabilities previously deemed unattainable, pushing manufacturers to reimagine how ceramics can be utilized. Understanding emerging materials, innovative manufacturing techniques, and sustainability considerations is essential for engineers, designers, and researchers alike.
Emerging Materials
When we talk about emerging materials in ceramics, we often refer to a blend of traditional ceramics and novel advancements. One particularly captivating innovation is the application of several layered ceramics, sometimes called functionally graded materials. These involve a gradual transition in composition, thus providing improved mechanical and thermal stability across a range of conditions. For aerospace applications, this can translate into parts that handle thermal stress more efficiently, ultimately boosting their lifespan.
Other noteworthy mentions include silicon nitride and zirconia, which are garnering attention for their lightweight and resistant properties. Researchers continue to explore such materials, seeking ways to integrate their benefits into both structural components and control systems within aircraft.
Innovative Manufacturing Techniques
Now, let's dig deeper into manufacturing processes, which directly impact how ceramics perform in real-world applications. The advancements in techniques like 3D printing have revolutionized the way ceramics are customized for specific needs in aerospace. Unlike traditional manufacturing methods, such as pressing or casting, additive manufacturing allows for intricate designs that minimize material usage while enhancing performance traits.
Moreover, the recent exploration of hybrid manufacturing, which combines traditional and additive methods, offers a promising route. This approach can yield complex geometries, and aircraft designers can tap into more customized shapes that enhance aerodynamics and thermal management. As these technologies mature, they can pave the way for cost-effective and high-performance ceramic components that drastically reduce lead times.
Sustainability in Ceramic Materials
The sustainability factor is rapidly becoming a driving force in materials research. The aerospace sector is no exception; the environmental footprint has raised concerns. Ceramic materials, traditionally viewed as energy-intensive to produce, are now under scrutiny for more eco-friendly processing methods. Researchers are exploring alternative formulations and reducing raw material use without sacrificing quality.
Notably, recycling spent ceramics or remnants from the manufacturing process represents a significant opportunity. The concept of a circular economy is gaining traction, with innovative methods being developed to convert leftover ceramic materials into usable products.
As those involved in aerospace engineering contemplate the future, embracing sustainability not only benefits the environment but also aligns with increasingly rigorous regulations and consumer demands for green technologies.
Case Studies of Ceramics in Current Aerospace Projects
Case studies serve as vital avenues for exploration and understanding in the integration of ceramics within aerospace projects. They not only offer rich insights into real-world applications but also highlight lessons learned throughout each project's lifespan. This knowledge is invaluable for designers, engineers, and researchers who seek innovative solutions to overcome existing hurdles in aerospace materials.
Successful Implementations
In examining successful instances of ceramic material applications in aerospace, specific projects stand out for their exemplary use of ceramic technologies:
- NASA’s Space Shuttle Program: The shuttle famously used reinforced carbon-carbon composites for its nose cone and wing leading edges, showcasing how advanced ceramics can withstand extreme re-entry temperatures. This implementation allowed for improved thermal protection, extending the shuttle's operational capabilities.
- Lockheed Martin’s F-35 Lightning II: The F-35 employs ceramic matrix composites in several components, from thermal protection systems to structural elements. This not only helps to reduce weight but also enhances durability, ensuring that parts can endure the tremendous conditions associated with high-speed flight.
- Airbus A350 XWB: This aircraft utilizes a proprietary blend of ceramic materials for its engine components, allowing for better heat resistance and contributing to overall fuel efficiency. The decision to integrate ceramics stems from a strategic aim to reduce maintenance costs and improve longevity.
These examples underline the tangible rewards of ceramic integration, highlighting enhancements in thermal performance, weight reduction, and overall efficiency. The aerospace industry benefits from such advancements, pushing the limits of engineering capabilities.
Failures and Lessons Learned
Not all projects embrace a smooth journey; several endeavors integrating ceramics have encountered significant setbacks. Understanding these failures can guide future efforts. Some key lessons include:
- The Concorde Program: Early iterations of the Concorde faced severe challenges with ceramic tiles used for thermal protection. Many tiles cracked under pressure, necessitating prolonged testing and redesign. This experience imparted essential knowledge on the resilience required in ceramics to withstand thermal shock during flight.
- RB211 Engine Development: In the development of the Rolls-Royce RB211 engine, issues arose when ceramic components were expected to perform at high stress levels. Some components failed prematurely, leading to a comprehensive reevaluation of material specifications. This situation showed how vital it is to rigorously test ceramics under operational conditions.
- NASA’s X-33 Program: The experimental X-33 faced operational difficulties partly due to inadequate material selection. Several ceramic components did not meet thermal thresholds and exhibited brittleness. This highlighted the need for thorough material vetting processes.
The experience gained from these projects emphasizes that while ceramics hold immense potential, they also present unique challenges that must be carefully navigated. It unveils the importance of instrumented testing and refinement throughout the design and implementation stages.
"The journey of ceramic materials in aerospace isn’t just about successes; it’s about learning, adapting, and evolving. Every failure serves as a stepping stone towards innovation."
In summary, case studies offer a dual lens of light and shadow on the integration of ceramics in aerospace. Successful applications showcase the benefits, such as enhanced durability and optimized performance, while failures illuminate pitfalls and areas for improvement. Understanding both aspects is crucial for stakeholders aiming to harness ceramic technology for future advancements.
Summary and Culmination
Reflecting on the importance of ceramics within aerospace engineering, it becomes clear that this material class is more than just a curiosity; it is pivotal in modern designs. Ceramics, known for their unique properties such as high thermal resistance and lightweight nature, are revolutionizing various components in aerospace applications. As the industry faces ever-growing demands for efficiency, performance, and sustainability, the role of ceramics becomes crucial in navigating these expectations.
The potential benefits of ceramics extend across multiple facets: from their ability to withstand extreme temperatures in thermal protection systems to providing robust solutions for engine components. It is crucial to understand that the innovative use of ceramics not only improves performance but also enhances the durability of aerospace systems while contributing to weight reduction. These attributes are invaluable when discussing fuel efficiency and overall mission success.
However, the journey is not without challenges. As discussed, issues such as material brittleness can impede widespread application, and the costs associated with advanced manufacturing techniques add another layer of complexity. Understanding these challenges does not diminish the relevance of ceramics but rather frames the conversation about their evolution and future applications.
In summary, as this article demonstrates, the marriage of advanced materials like ceramics with cutting-edge aerospace technology is a thrilling frontier. This progressive approach promises to not only foster innovations but also inspire future research that could mitigate existing challenges, ensuring that ceramics remain at the forefront of aerospace engineering.
Recap of Key Points
- Importance of Ceramics: Essential in enhancing performance, durability, and efficiency in aerospace components.
- Properties of Ceramics: Outstanding thermal resistance, mechanical strength, and lightweight characteristics crucial for modern aerospace needs.
- Challenges: Material brittleness and manufacturing complexities are hurdles that must be addressed.
- Future Directions: An emphasis on sustainability and innovative manufacturing techniques could shape the next phase of ceramic applications in aerospace.
The Path Forward for Ceramics in Aerospace
Looking ahead, the path for ceramics in aerospace seems promising yet complex. First and foremost, emerging materials and composites will likely play a significant role in expanding the applications of ceramics. For instance, researchers are exploring bio-inspired ceramic composites that mimic natural structures, paving the way for improved performance under stress.
Moreover, as additive manufacturing of ceramics develops, it offers a unique route to customizing component designs, cutting costs and reducing waste. This technology has the potential to create intricate geometries that were previously thought unattainable in traditional manufacturing, thus pushing the envelope in design possibilities.
Lastly, sustainability must remain a focal point. With a growing emphasis on green technologies, the aerospace industry can benefit significantly by exploring environmentally friendly ceramic materials and manufacturing processes. This aligns well with the global move towards reducing carbon footprints and fostering a sustainable future.