Accounting Insights for Food Manufacturing Sector
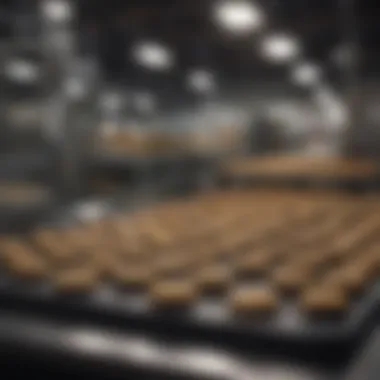
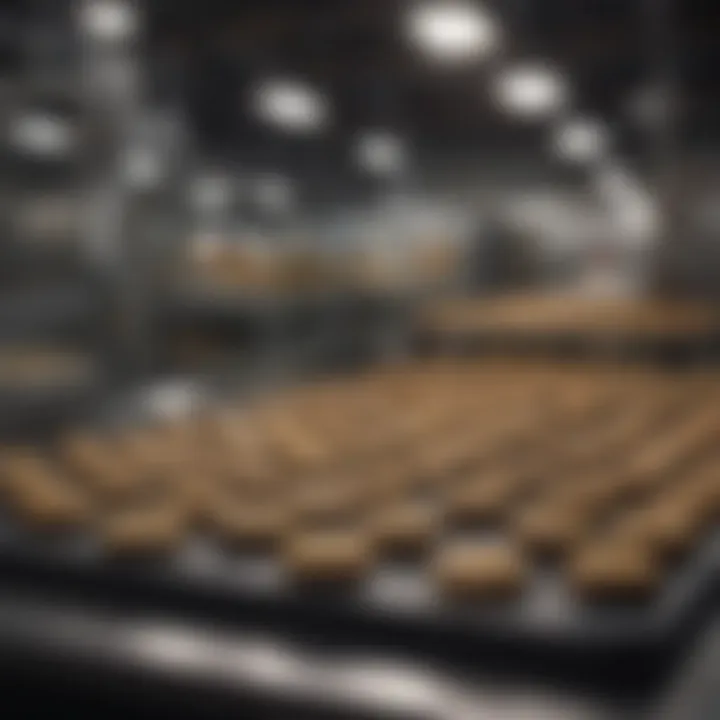
Intro
Accounting for food manufacturing involves a complex interplay of unique challenges and practices. The food sector is characterized by stringent regulatory compliance, fluctuating costs, and the necessity for precise inventory management. These factors make it crucial for professionals in this field to understand the accounting systems that best serve their operations.
This article examines the various aspects that define accounting in food manufacturing. From cost control to compliance with standards, the intricacies of inventory strategies, and the influence of advanced technology, every component plays a vital role. Additionally, the emphasis on sustainability and its role in financial reporting is increasingly relevant.
By blending theoretical insights with practical applications, we aim to equip both new learners and experienced professionals with the tools necessary to navigate this specialized sector. The exploration of this field offers not only essential knowledge but also highlights its significance in ensuring efficient and responsible food production.
Foreword to Accounting in Food Manufacturing
Accounting plays a crucial role in the food manufacturing sector, functioning as the backbone of operational efficiency and financial stability. Understanding the nuances of accounting in this context enables professionals to address unique challenges that arise from inventory management, compliance with regulatory frameworks, and cost control. These factors are fundamental not just for profitability, but also for long-term sustainability and competitiveness in a rapidly evolving market.
A major facet of accounting in food manufacturing is its impact on decision-making. By analyzing financial data, manufacturers can optimize their production processes, manage overhead costs, and establish sound budgeting practices. This analysis can lead to improved resource allocation and reduced waste, which are vital in a sector where margins can be thin. Additionally, the importance of accurate record-keeping cannot be overstated. Precise accounting records help in tracking costs associated with raw materials, labor, and overhead, which are all essential for establishing proper pricing strategies.
Moreover, ethical considerations such as sustainability are becoming increasingly critical. Stakeholders now demand transparency in how food products are sourced and produced. Therefore, robust accounting practices not only fulfill regulatory requirements but also build trust with consumers. Accounting professionals in this sector must be adept at integrating sustainable practices into financial reporting, promoting greater corporate responsibility.
This section sets the stage for a deeper exploration into specific aspects of accounting that directly affect food manufacturing, from historical development to contemporary techniques and trends. By understanding these elements, professionals can better navigate the complexities and demands of the industry.
The Role of Accounting in the Food Industry
Accounting serves as an essential framework for managing the intricate financial needs of food manufacturing. It encompasses a variety of functions including cost accounting, budgeting, and financial reporting. Cost accounting allows manufacturers to determine the actual costs associated with producing their goods, enabling them to set competitive pricing while ensuring profitability.
Financial reporting in this context provides stakeholders with clear insights into the financial health of the business. Reports such as income statements and balance sheets help in assessing performance, guiding investment decisions, and ensuring compliance with accounting standards. Furthermore, the budgeting process is critical for planning future operations, helping managers allocate resources effectively and prepare for unforeseen expenses.
Historical Perspectives on Food Manufacturing Accounting
The evolution of accounting practices in food manufacturing reflects broader changes in economic paradigms and technology. In the earlier decades of industrialization, accounting was primarily focused on basic cost tracking. As operations grew more complex, so too did the need for more sophisticated methods of accounting. The introduction of standardized financial reporting was a response to growing regulations and an increasingly competitive market.
By the mid-20th century, food manufacturing faced new challenges such as global supply chains and increased consumer demand for transparency. This led to the adoption of more refined accounting systems that could track not only costs but also the source of ingredients and their journey through the supply chain. Innovations such as Activity-Based Costing emerged to provide deeper insights into how resources were utilized in production, driving efficiency and cost-effectiveness.
Overall, understanding these historical shifts helps current professionals appreciate the continuous evolution of accounting in this vital sector, shedding light on the underlying principles that govern their practices today.
Key Accounting Principles for Food Manufacturing
Accounting principles in food manufacturing play a crucial role in ensuring financial success and sustainability. This area requires a focus on specific elements like cost management, regulatory compliance, and inventory control. By understanding these principles, food manufacturers can optimize their operations, enhance profitability, and meet the demands of a diverse and dynamic market.
Cost Accounting Fundamentals
Cost accounting is fundamental in food manufacturing. It assists managers in understanding the costs associated with production at a granular level. This involves analyzing direct costs, like raw materials and labor, and indirect costs, such as overhead. By breaking down costs, manufacturers can identify inefficiencies and make informed decisions to improve profitability.
- Tracking Costs: Accurate tracking allows for better pricing strategies.
- Product Costing: Understanding the full cost of producing a product enables manufacturers to price it appropriately.
- Analysis of Variances: Regularly reviewing variances between budgeted and actual costs helps in identifying areas for improvement.
Cost accounting provides valuable insights for decision-making, ultimately leading to greater competitiveness and operational efficiency.
Financial Reporting Standards for Food Manufacturers
Financial reporting standards are essential for food manufacturers to ensure transparency and accountability. Compliance with standards such as Generally Accepted Accounting Principles (GAAP) or International Financial Reporting Standards (IFRS) is critical. These standards guide the preparation of financial statements, ensuring that they accurately reflect the company’s financial health.
- Balance Sheet: Shows the assets and liabilities, offering a clear picture of financial stability.
- Income Statement: Reveals operational performance over a specific period.
- Cash Flow Statement: Highlights cash inflows and outflows, critical for sustaining operations.
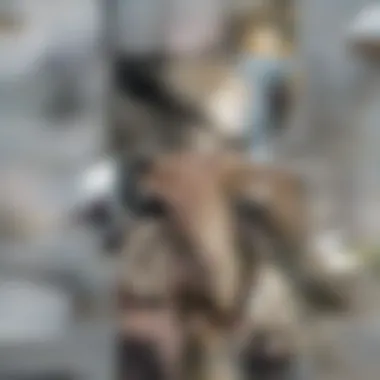
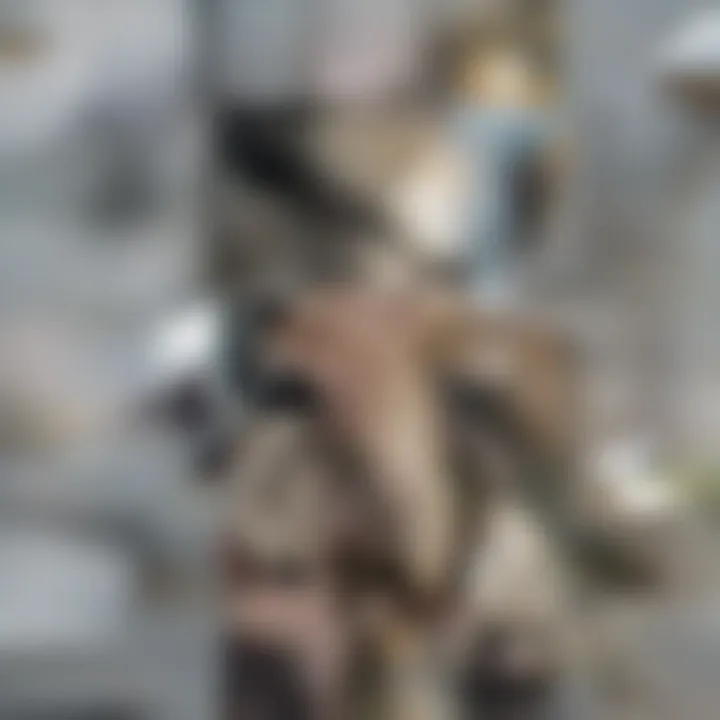
Proper adherence to these standards not only helps in regulatory compliance but also builds trust with stakeholders, including investors and customers.
Budgeting Techniques in Food Manufacturing
Budgeting is an essential element for financial planning in food manufacturing. Effective budgeting techniques allow organizations to allocate resources efficiently, set financial goals, and monitor performance against projections. A well-structured budget accommodates seasonal variations and fluctuating market conditions.
- Operational Budgets: Focus on day-to-day operations and costs.
- Capital Budgets: Plan for long-term investments in equipment or facilities.
- Flexible Budgets: Adjust based on changes in production volume, allowing better real-time assessment.
Utilizing these budgeting techniques can significantly enhance a manufacturer's ability to manage cash flow and operational efficiency.
Key accounting principles not only facilitate effective decision-making, but also support sustainable growth in the food manufacturing industry.
In summary, understanding these key accounting principles is vital for anyone involved in food manufacturing. They provide a framework for managing costs, maintaining compliance, and budgeting effectively, all of which are critical for achieving success in this competitive sector.
Unique Challenges in Food Manufacturing Accounting
The food manufacturing sector operates within a complex framework of regulations, consumer expectations, and economic pressures. Understanding accounting in this environment requires a recognition of several unique challenges that directly impact financial performance and operational efficiency. These challenges include inventory management, regulatory compliance, and supply chain dynamics. Addressing these issues is essential for accurate financial reporting and sustainable business practices.
Every food manufacturer must contend with varying degrees of complexity in tracking costs and ensuring compliance with industry standards. The implications of these challenges affect not just accounting and finance departments, but resonate throughout the entire organization, influencing decisions made at various levels.
Inventory Management and Valuation
Inventory management in food manufacturing involves the diligent tracking of raw materials, work-in-progress, and finished goods. Accurate valuation is crucial, as mismanagement can lead to financial discrepancies and affect cash flow. Food products often have a limited shelf life, necessitating precise accounting practices that account for spoilage and wastage.
- Cost Methodologies: Manufacturers commonly use valuation methods such as FIFO (First In, First Out) or LIFO (Last In, First Out) to determine the cost of goods sold. Choosing the right method greatly impacts profitability and tax obligations.
- Perpetual Inventory System: Implementing a real-time inventory tracking system is beneficial. This approach allows for continuous monitoring and adjustments, minimizing discrepancies.
Inventory data can also influence budgeting and forecasting processes. Regular audits are necessary to confirm that inventory valuation aligns with actual stock on hand, ensuring that financial statements reflect true performance.
Regulatory Compliance Issues
Regulatory compliance is a critical aspect of accounting in food manufacturing. Companies must adhere to a myriad of local, national, and international regulations such as the Food Safety Modernization Act (FSMA) in the United States, which governs food safety practices.
- Documentation: Maintaining detailed records is not only a best practice but a legal requirement. Accurate documentation ensures that a manufacturer can swiftly provide evidence of compliance during inspections or audits.
- Traceability: The ability to trace food products throughout the supply chain enhances accountability. Accounting systems must incorporate features that support traceability from raw materials to final products.
Failure to comply with regulations can result in significant penalties, including fines and loss of licensure. Therefore, food manufacturers must invest in compliance training and robust accounting systems to manage this risk effectively.
Understanding the Supply Chain Dynamics
The food supply chain is intricate, involving multiple stakeholders from growers to distributors. Understanding the financial implications of these relationships is essential for effective accounting.
- Cost Fluctuations: Prices of raw materials can be volatile due to market conditions, impacting overall production costs. This requires sophisticated forecasting to anticipate changes and adjust budgets accordingly.
- Vendor Relationships: Establishing strong relationships with suppliers can enhance negotiating power and supply chain efficiency. Maintaining accurate records of these interactions supports better decision-making and financial planning.
Technological Advancements in Accounting for Food Manufacturing
The realm of accounting for food manufacturing has seen considerable shifts due to technological advancements. The integration of new tools and systems is not just advisable, but critical in ensuring efficient accounting practices. These advancements contribute to higher accuracy, better compliance with regulations, and improved efficiency of processes. In a sector as dynamic as food manufacturing, staying updated with technology is essential.
Role of Accounting Software
Accounting software plays a pivotal role in modern food manufacturing. These tools streamline various processes, from tracking expenses to managing payroll and ensuring regulatory compliance. The benefits of using accounting software are numerous:
- Efficiency: Automation of repetitive tasks saves time and reduces human error.
- Real-time Reporting: Companies can monitor their financial status instantly, which aids in timely decision-making.
- Scalability: As businesses grow, accounting software can adapt to increased complexity without significant additional costs.

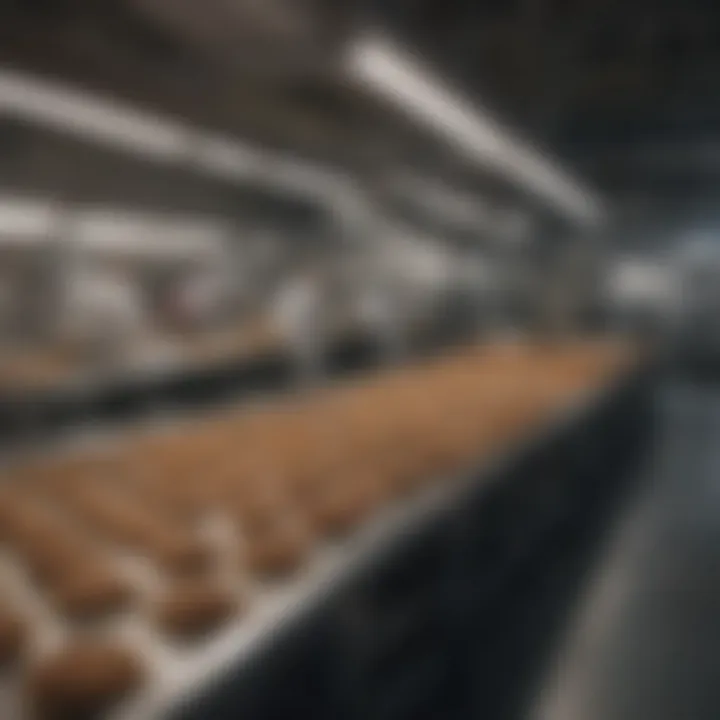
A prominent example of such software is QuickBooks, which is widely used in the industry for managing financial data. Its features help food manufacturers in managing accounts payable and receivable. This allows them to focus on core operations rather than tedious bookkeeping.
Integration of ERP Systems
Enterprise Resource Planning (ERP) systems offer an integrated approach to managing company resources and data. For food manufacturers, integrating accounting with an ERP system can yield substantial benefits:
- Holistic View: ERP systems consolidate data across departments, providing insights into overall business performance.
- Streamlined Processes: From procurement to sales, every function is interconnected, leading to increased productivity.
- Improved Data Accuracy: By limiting data entry points, ERP systems minimize errors that often occur when transferring data between systems.
For example, SAP ERP is often deployed in food manufacturing to unify various business processes, enhancing collaboration and understanding across departments.
Impact of Data Analytics
The role of data analytics in food manufacturing accounting cannot be understated. It allows businesses to harness vast amounts of data collected through various operations. The implications of this are significant:
- Enhanced Decision-Making: By analyzing financial data, manufacturers can identify trends, forecast future sales, and make informed investment choices.
- Cost Reduction: Analytics can highlight areas for cost savings, optimizing resource allocation and minimizing waste.
- Regulatory Compliance: With data analytics, companies can ensure adherence to financial regulations by maintaining accurate records and facilitating audits.
To summarize, the advancements in technology, including accounting software, ERP systems, and data analytics, are revolutionizing how food manufacturers approach their financial management. These innovations provide a framework for accountability and efficiency, which are paramount for success in a highly competitive industry.
Sustainability and Ethical Considerations in Food Manufacturing Accounting
Accounting in food manufacturing must consider sustainability and ethics. These elements are not mere trends; they are essential for long-term viability in this industry. Companies face increasing pressure to demonstrate accountability not just in financial terms but also regarding their environmental and social impact. Incorporating sustainable practices can lead to cost savings, improve brand reputation, and ensure compliance with regulations. Addressing these issues is vital for stakeholders who are progressively more concerned about the ecological footprint of their food sources.
Sustainable Accounting Practices
Sustainable accounting practices focus on aligning financial goals with environmental stewardship. These practices include:
- Life Cycle Assessment (LCA): This evaluates the environmental impact of a product from raw material extraction to end-of-life disposal. It helps companies understand their resource use and waste generation.
- Green Costing: This method accounts for environmental costs associated with production, such as waste management or energy consumption. It encourages firms to reduce resource utilization and swap to more sustainable materials.
- Triple Bottom Line (TBL): Companies employing TBL measures success in three areas: social, environmental, and financial. This integrated approach provides a more comprehensive understanding of an organization’s impact.
Adopting sustainable accounting practices can aid food manufacturers in meeting regulatory requirements and shaping positive consumer perceptions.
Disclosure of Environmental Impacts
Transparency in reporting environmental impacts is becoming crucial in food manufacturing. Businesses ought to disclose their sustainability efforts in a clear and factual manner. This includes reporting on:
- Carbon Emissions: Many governments mandate reporting greenhouse gas emissions. Understanding and reducing carbon footprints can mitigate operational risks.
- Water Use and Management: Water scarcity is a pressing concern. Reporting on water usage policies and practices can demonstrate responsibility and mitigate potential risks.
- Waste Management Strategies: Companies should explain how they handle production waste and recycling initiatives. This can reveal strengths and vulnerabilities within operations.
"Being transparent about environmental impacts shows a commitment to sustainability and can enhance competitive advantage in the market."
This focused disclosure not only fulfills regulatory requirements but can also boost investor confidence and attract environmentally conscious consumers.
The integration of sustainability and ethics into food manufacturing accounting isn't just a compliance measure. It’s a strategic avenue towards building a brand that resonates well with stakeholders. When firms embrace transparency and sustainability, they better equip themselves to navigate the complexities of an ever-evolving market.
Future Trends in Food Manufacturing Accounting
In today's dynamic landscape, accounting in food manufacturing is undergoing significant transformations. As businesses strive for efficiency and adaptability, understanding future trends becomes crucial. This not only enhances financial accuracy but also aligns operations with market demands and regulatory expectations. By examining the developments in this area, stakeholders can anticipate shifts that will shape practices in the coming years.
Adaptation to Changing Regulatory Environments
The regulatory environment for food manufacturing is often complex and subject to rapid change. Compliance with food safety standards, environmental regulations, and financial reporting procedures is critical. Companies must stay informed about these changes to avoid penalties and maintain operational integrity.
Accounting systems must be flexible enough to incorporate new regulations promptly. This adaptability ensures that businesses remain compliant while minimizing the administrative burden on accounting staff.
Key strategies include:
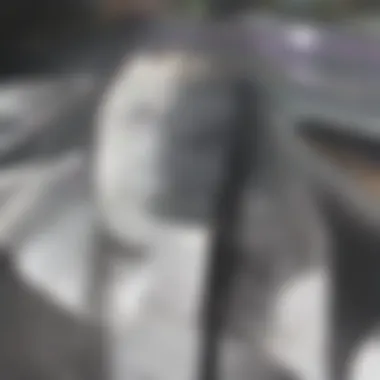
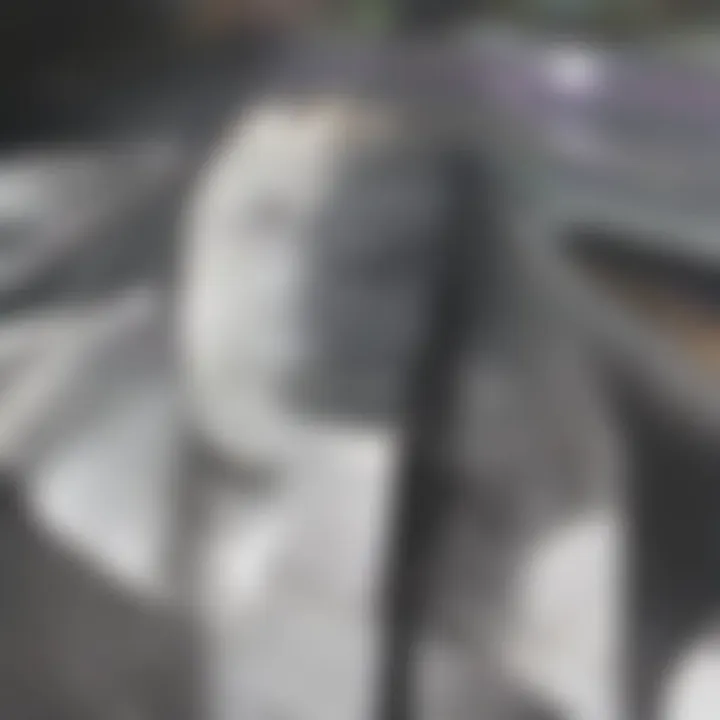
- Regular training for staff on new regulations
- Integrating real-time compliance checks in accounting software
- Analyzing how changes affect cost structures and pricing strategies
Evolving Consumer Expectations and Their Impact
Today’s consumers are more informed and selective. They expect transparency regarding product sourcing, nutritional information, and sustainability practices. This consumer behavior compels food manufacturers to refine their accounting practices.
Tracking and reporting data related to sustainability, for instance, adds complexity to financial statements. Accounting departments need to develop methodologies for quantifying these factors in a numerical format.
Incorporating consumer expectations into financial strategies can lead to significant market advantages. This includes:
- Developing transparent financial reporting related to sourcing practices
- Ensuring consistency in branding and product cost assessments
- Engaging with consumers to gather feedback and adjust offerings accordingly
Emerging Technologies and Their Implications
Technological advancements are fundamentally transforming the landscape of accounting in food manufacturing. Automation, artificial intelligence, and data analytics are at the forefront of this evolution. Tools that streamline processes and enhance data accuracy are becoming indispensable.
For instance, AI can help in predictive analytics, enabling companies to forecast demand and manage inventory more effectively. Additionally, blockchain technology offers a way to enhance traceability for food products, which is increasingly demanded in today’s market.
Key implications of emerging technologies include:
- Enhanced efficiency in data handling and reporting
- Improved accuracy in financial forecasting and risk management
- Greater transparency in supply chain management
"Understanding and adapting to emerging technologies leads to more effective decision-making in food manufacturing accounting."
Each of these aspects highlights the need for food manufacturers to remain agile and informed. By anticipating regulatory changes, understanding consumer demands, and leveraging technology, these organizations can not only survive but thrive in a competitive marketplace.
Case Studies in Food Manufacturing Accounting
Case studies serve as vital tools in understanding practical applications of accounting in food manufacturing. They provide detailed narratives about how specific companies implement accounting systems, strategies, and best practices. By analyzing real-world scenarios, professionals can discern what works effectively and what does not in various contexts. This section will shine a spotlight on two distinctive aspects of case studies: successful implementations of accounting systems and lessons learned from financial mismanagement.
Successful Implementations of Accounting Systems
Examining successful implementations of accounting systems offers insights into best practices that can guide others. Companies that have effectively adopted comprehensive accounting systems often report significant improvements in operational efficiency and data accuracy. For instance, a food manufacturing company may utilize Oracle NetSuite to track real-time inventory levels, sales, and supply chain metrics seamlessly.
- Benefits of Implementation
- Improved accuracy in financial reporting
- Enhanced inventory management
- Streamlined compliance with regulatory requirements
Additionally, successful cases often illustrate the importance of training staff on these new systems. New software can be daunting, but with adequate training, employees can maximize its potential. Engaging employees early in the adoption process fosters a culture of openness and readiness for change.
"Investing in staff training is as crucial as investing in advanced accounting technology."
Furthermore, successful organizations frequently display traits such as adaptability and continuous improvement. They analyze feedback from their accounting systems regularly to refine processes, which ultimately enhances overall business performance.
Lessons Learned from Financial Mismanagement
Learning from mistakes is essential in any field, and food manufacturing is no exception. Several cases illustrate how financial mismanagement can have dire consequences for businesses. One prominent example is a food company that neglected proper inventory valuation, leading to overstated profits.
- Consequences of Financial Mismanagement
- Loss of investor confidence
- Regulatory penalties
- Damage to company reputation
Such scenarios highlight the critical role of inventory management and adherence to accounting standards. Mismanagement generally stems from inadequate systems, lack of training, or insufficient awareness of available resources. By analyzing these failures, companies can develop robust mechanisms to prevent similar occurrences.
Culmination and Final Thoughts
The exploration of accounting within the food manufacturing sector reveals its multifaceted nature. It is essential for industry stakeholders to comprehend the relevance of effective practices in this sphere. The conclusions drawn from previous sections highlight how societies depend on reliable accounting methods to maintain standards in food quality and safety. Each aspect discussed – from cost management to compliance – intertwines to create a robust framework for success in food manufacturing.
The Importance of Evolving Practices
In today's fast-paced market, the importance of evolving practices in accounting cannot be overstated. The food manufacturing landscape is subject to constant changes driven by consumer preferences, technological advancements, and regulatory shifts. Understanding these dynamics enables firms to adapt and stay competitive.
Simply adhering to traditional methods can lead to stagnation. Companies that embrace innovation, such as automated accounting systems and data analytics, can enhance efficiency and accuracy. Evolving practices also foster transparency and accountability, which are crucial in gaining consumer trust and maintaining compliance with regulations. Moreover, adapting to these changes is not just beneficial; it is necessary for long-term sustainability.
Encouraging Continuous Learning in Accounting
Another vital element in the accounting landscape is fostering a culture of continuous learning. The complexities of accounting in food manufacturing necessitate that professionals remain informed about the latest standards and technologies. This ongoing process of education allows individuals to refine their skills and knowledge, equipping them to handle emerging challenges.
Organizations should promote workshops, seminars, and online courses to facilitate growth among their accounting staff. This not only enhances individual capabilities but also strengthens the organization as a whole. Furthermore, encouraging collaboration among professionals can lead to the sharing of best practices and innovative ideas.