Exploring 3D Printed Production Parts Innovations
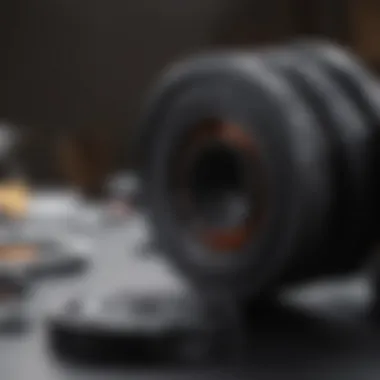
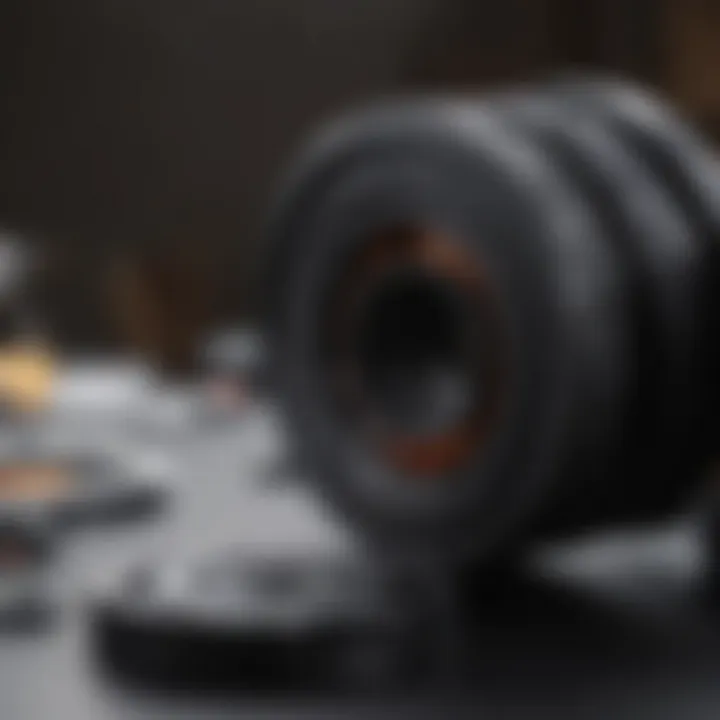
Intro
The field of 3D printing has seen rapid developments over the last decade, significantly changing the landscape of production parts. Today, additive manufacturing opens new pathways for designing and fabricating components across several industries. With its ability to create complex geometries that traditional manufacturing methods cannot, 3D printing has gained traction in sectors such as aerospace, automotive, and healthcare.
As we delve into this article, it will explore the evolution of 3D printed production parts and how they integrate with established manufacturing processes. The advancement of materials and technological capabilities plays a critical role in fostering these changes. Understanding the balance between the advantages presented by additive manufacturing and the hurdles it faces will offer insights valuable to students, educators, and professionals alike.
Key Findings
Summary of the main results
The research reveals several vital findings about 3D printed production parts. First, the adaptation of 3D printing technology has resulted in a significant reduction in lead times for product development. By utilizing digital files, companies can move quickly from design to prototype, and eventually to finished product. Second, the use of advanced materials such as polymers, metals, and composites has expanded the functionality and performance of printed components.
Moreover, case studies demonstrate that sectors like aerospace have adopted 3D printing to produce lightweight parts, which enhance fuel efficiency and overall performance. Companies in the automotive sector are leveraging this technology to create custom parts, reducing waste and costs. The healthcare industry has also seen advancements, particularly in creating customized implants and prosthetics tailored to individual patient needs.
Significance of findings within the scientific community
The implications of these findings are far-reaching. The scientific community acknowledges the role of 3D printing in pushing boundaries. Researchers are exploring new materials and printing techniques, thereby contributing to both academia and industry. The shift towards additive manufacturing signifies a change in how products are designed, highlighting sustainability and efficiency in production.
3D printing is not just a trend. It represents a fundamental shift in manufacturing paradigms, influencing both design thinking and production efficiency.
Implications of the Research
Applications of findings in real-world scenarios
The findings discussed above carry considerable applications in real-world scenarios. In aerospace, for instance, 3D printing allows the creation of parts that are both lightweight and strong. This capability promotes energy savings and enhances performance. The automotive industry benefits similarly through the production of complex parts that were once unfeasible to manufacture using traditional methods.
In healthcare, with the growing demand for personalized medicine, 3D printed guides and patient-specific implants enable tailored surgical procedures. This customization can lead to quicker recovery times and improved patient outcomes.
Potential impact on future research directions
Future research in this domain could focus on the development of biocompatible materials, addressing regulatory challenges, and exploring the potential integration of artificial intelligence in the design process. These directions could further enhance the capabilities of additive manufacturing and its applicability across other sectors as technology continues to progress.
Preamble to 3D Printing
3D printing, also known as additive manufacturing, represents a transformative shift in the way products are designed and produced. It enables the creation of complex parts through a layer-by-layer process, offering benefits not seen with traditional manufacturing methods. Understanding this technology is crucial as it lays the foundation for advancements in producing parts across various fields.
In this article, we will delve into the significance of 3D printing, emphasizing its impact on the production of parts. It highlights advantages like cost efficiency, customization, and the ability to create intricate geometries which are often difficult to achieve with conventional processes. As industries become more competitive, the demand for innovative manufacturing solutions increases. 3D printing stands out as a viable option, warranting comprehensive discussion.
Definition and Overview
3D printing refers to manufacturing techniques that produce three-dimensional objects from a digital file. This process involves adding material layer by layer, as opposed to subtractive methods, which typically involve cutting away material from a solid block. Various technologies including Fused Deposition Modeling (FDM), Stereolithography (SLA), and Selective Laser Sintering (SLS) are common within the realm of 3D printing.
The process begins with a digital model, often created using Computer-Aided Design (CAD) software. This model is then sliced into thin horizontal layers using slicing software, leading to the production file sent to the printer. The printer then builds the object according to the file's specifications.
Historical Context
The roots of 3D printing can be traced back to the 1980s. The initial concept emerged from the mind of Chuck Hull, who invented Stereolithography in 1983. This seminal development opened doors to what would become a burgeoning field of additive manufacturing.
Manufacturing technology evolved rapidly. By the 1990s, other processes like FDM and SLS gained traction, paving the way for diverse applications across several industries. Early on, 3D printing primarily served prototyping purposes. However, as technology advanced, its applications shifted toward actual production parts, fostering growth and innovation.
Today, 3D printing stands at the frontier of manufacturing, illustrating how additive technologies can redefine traditional production pathways. This evolution invites a thorough exploration of the characteristics, requirements, and benefits of producing parts via 3D printing.
Understanding Production Parts
Understanding production parts is a critical aspect in the discussion of 3D printing technology. As industries evolve, the need for efficient, high-quality production becomes paramount. The advent of 3D printing has changed the expectations and the realities of how production parts are conceptualized, designed, and manufactured.
In the realm of manufacturing, production parts refer to the components that are created for end-use in various applications across multiple sectors. These parts optimize performance, durability, and utility, making them integral to the functionality of larger systems, like in automobiles, airplane assemblies, and medical devices. The significance of production parts enhances as they can be customized or modified to suit specific needs or requirements based on consumer demands.
There are several key elements that define production parts:
- Material Selection: The choice of materials impacts strength, weight, and performance which affects the overall quality of the final product.
- Precision and Accuracy: The capability to achieve high levels of detail through 3D printing is essential for the effectiveness of the part within its intended environment.
- Cost-Effectiveness: Efficient production parts can lead to reduced costs, particularly when produced in small batches or during prototyping phases.
This necessity of comprehending production parts encourages professionals to engage deeply with the design and manufacturing processes. As the industry faces an increasing demand for customization and rapid production, understanding production parts leads to improved strategies in product development and customer satisfaction.
Characteristics of Production Parts
Production parts are defined by distinctive characteristics that set them apart from prototypes or less demanding designs. These characteristics include:
- Robustness: Unlike prototypes that may be for testing purposes, production parts must exhibit durability to withstand operational stresses.
- Standardization: Consistency in dimensions and properties is required for parts that are used interchangeably within a production line.
- Functionality: Each part must fulfill a specific function reliably; any failure in performance can lead to significant downtime in industrial applications.
Overall, these characteristics ensure that production parts contribute effectively to operational efficiency and productivity in manufacturing environments.
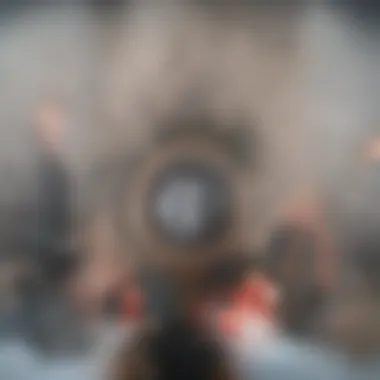
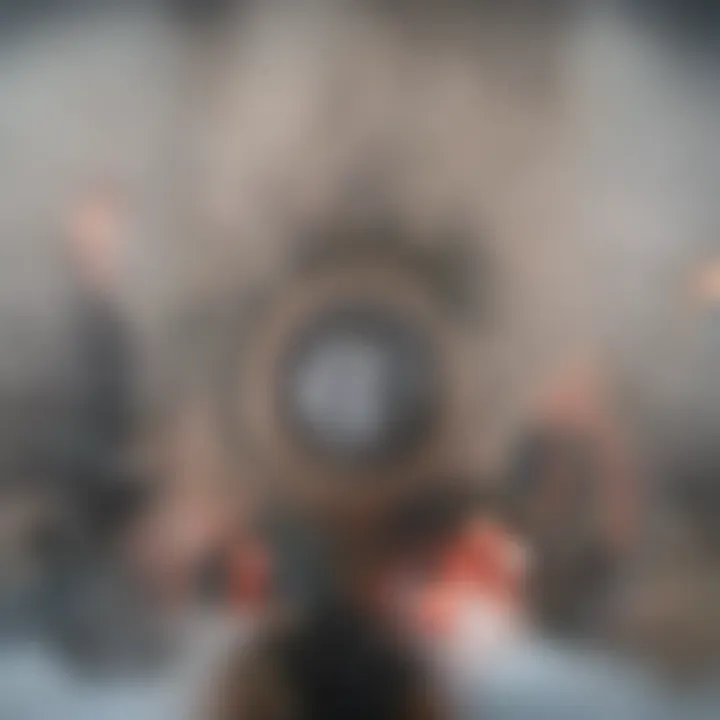
Requirements for Quality and Performance
Quality and performance are paramount in the realm of production parts. Various factors contribute to these elements, ensuring that end products meet industry standards and customer expectations.
- Testing and Validation: Production parts should undergo a rigorous testing process to assess their structural integrity, dimensional accuracy, and compatibility with other parts.
- Certification: Regulatory requirements often dictate that certain parts must meet specific certifications, especially in sectors like aerospace and healthcare.
- Traceability: It is crucial to maintain records of the materials and processes used in the production of parts for accountability and quality assurance.
These requirements can be challenging yet necessary for the successful integration of 3D printed production parts into mainstream industries. Achieving a high standard in these areas often differentiates successful companies from their competitors.
"Quality is never an accident; it is always the result of intelligent effort."
- John Ruskin
The Additive Manufacturing Process
The additive manufacturing process, commonly known as 3D printing, plays a crucial role in the fabrication of production parts. This method offers distinct advantages over traditional manufacturing techniques, such as subtractive manufacturing. The relevance of this process extends beyond mere fabrication. It encapsulates flexibility in design, efficient material utilization, and the ability to create complex geometries that are difficult or impossible to achieve otherwise.
Techniques for 3D Printing
Fused Deposition Modeling (FDM)
Fused Deposition Modeling is a widely used 3D printing technique that builds parts layer by layer using thermoplastic materials. This methods ease of use and cost-effectiveness have made it a popular choice in many industries. FDM operates by melting a filament, which is then extruded through a nozzle to form a desired shape.
The key characteristic of FDM is its accessibility. Many educational institutions and small enterprises utilize FDM for prototyping and production because it requires relatively low investment in equipment. A unique feature of FDM is its ability to use a variety of materials, allowing diverse applications from simple prototypes to functional parts.
Advantages of FDM include low operational costs and a wide range of compatible materials. However, it has limitations; the layer adhesion can sometimes be weaker compared to other methods, and the resolution may not meet the requirements for high-precision applications.
Stereolithography (SLA)
Stereolithography is another prominent 3D printing technique known for its high precision and ability to produce intricate details. SLA uses a UV light source to cure liquid resin into hardened plastic. This method is often chosen for applications requiring detailed and smooth finishes, making it suitable for various industries including jewelry and dental.
The key characteristic of SLA is its exceptional accuracy. It can create parts with fine features and intricate designs due to its layer-by-layer curing process. This benefit makes SLA a favored technique for industries that demand high-quality prototypes and production parts.
A unique feature of SLA is its ability to produce highly complex geometries with smooth surface finishes, ideal for aesthetic components. One disadvantage is its relatively slower printing speed compared to other methods like FDM, which might limit production volume.
Selective Laser Sintering (SLS)
Selective Laser Sintering employs a laser to fuse powdered materials into solid forms. This technique is advantageous for creating functional parts with complex geometries and a wide range of material availability, including plastics and metals.
The key characteristic of SLS is its versatility. It allows the production of parts without the need for support structures since the unsintered powder supports overhangs. This capability is particularly beneficial in producing detailed parts for aerospace or automotive applications.
A unique feature of SLS is its ability to use materials that are difficult to process with other methods. The main disadvantage lies in the higher costs associated with the equipment and materials used, which may present barriers for smaller companies or startups.
Software and Design Methodologies
Computer-Aided Design (CAD)
Computer-Aided Design is an essential component of the additive manufacturing process. CAD software allows designers and engineers to create detailed 3D models of parts before they are printed. This digital design process facilitates visualization and modifications, streamlining the workflow.
A significant characteristic of CAD is its ability to enhance precision and efficiency in design. It enables simulations and makes it easier to alter designs based on performance requirements or manufacturing constraints. A unique feature of CAD is its integration with printers, which can directly translate designs into machine instructions.
The advantages include improved design accuracy and the capability to optimize designs for manufacturability. Nevertheless, the initial learning curve for CAD software can be challenging for new users, impacting its widespread adoption.
Simulation and Optimization Tools
Simulation and optimization tools play a vital role in preparing designs for 3D printing. These tools help predict the performance of printed parts under various conditions. They can also assist in identifying potential issues in the design phase, minimizing material waste, and enhancing overall production efficiency.
A key characteristic of these tools is their analytical capabilities. They allow for testing models virtually, leading to better-informed decisions about design adjustments or material selections. Moreover, optimization can reduce weight in parts while maintaining strength, which is vital in industries like aerospace.
The unique feature of simulation tools is their ability to enhance reliability in production by providing insight into how parts will behave during use. One of the challenges is the cost associated with advanced simulation software, which may be a barrier for smaller enterprises.
Materials Used in 3D Printing
The choice of materials in 3D printing is a pivotal element in the production of effective and high-quality parts. These materials determine not only the feasibility of creating specific designs but also the end performance of the produced components. As various industries explore the advantages of additive manufacturing, an understanding of the materials involved can provide insight into their capabilities and limitations.
Commonly Used Materials
Plastics
Plastics form the backbone of 3D printing materials. They are versatile, lightweight, and relatively inexpensive, making them a beneficial choice across multiple applications. One key characteristic of plastics is their ability to be easily manipulated, allowing for complex designs that would be difficult or impossible with traditional manufacturing methods.
Among the unique features of plastics, the availability of different types such as ABS (Acrylonitrile Butadiene Styrene) and PLA (Polylactic Acid) is notable. These materials have distinct thermal and mechanical properties. For example, while PLA is biodegradable and has a low melting temperature, ABS is known for its strength and durability. However, using plastics presents some disadvantages such as susceptibility to warping and lesser structural strength compared to metals.
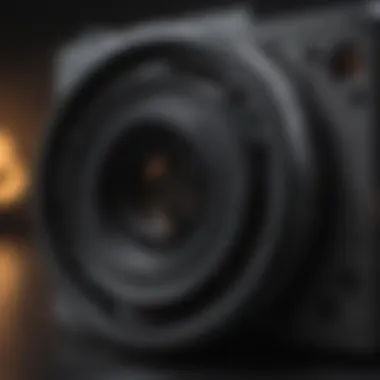
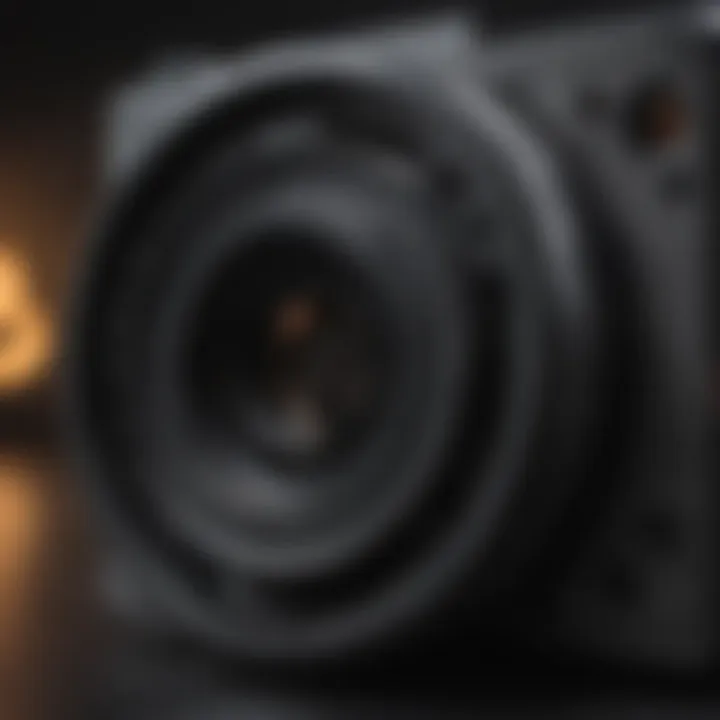
Metals
Metals are increasingly being used in 3D printing due to their strength and ability to withstand harsh environments, particularly in the aerospace and automotive industries. The use of metals allows for the production of parts that require exceptional durability and heat resistance. One of the key characteristics of metals in 3D printing is their high tensile strength.
Metals such as titanium and aluminum are popular choices. Their unique feature includes high melting points and excellent mechanical properties. However, the challenges with metals are often related to cost and the complexity of the printing process, which may lead to longer production times.
Composites
Composite materials are another significant category in 3D printing. These materials combine plastics with fibers or other additives to enhance performance. The key characteristic of composites is their ability to offer improved properties such as increased stiffness and reduced weight.
One major advantage of composite materials is their tailorability, meaning properties can be modified based on specific application needs. For instance, reinforced composites can exhibit greater tensile strength than standard plastics. However, the complexity of printing with composites can introduce challenges, including the need for specialized equipment and potential issues with consistency.
Emerging Material Technologies
Biosourced Materials
Biosourced materials, often derived from renewable resources, represent a significant advancement in 3D printing technology. They are gaining attention for their role in promoting sustainable practices. A key aspect is their renewable origin, which can lead to lower carbon footprints.
One of the unique features of biosourced materials is their biodegradability. This attribute makes them a compelling option for companies focused on sustainability. However, challenges remain regarding their performance in comparison to traditional materials. They may lack the same mechanical properties, limiting their applications in demanding environments.
Smart Materials
Smart materials are at the forefront of 3D printing advancements, as they can react to environmental changes or stimuli. Such materials include shape-memory alloys and temperature-responsive polymers. The key characteristic of smart materials is their ability to adapt, which allows for innovation in various applications, from healthcare to aerospace.
Their unique feature is the capacity to change properties under certain conditions, providing dynamic solutions for engineers and designers. Nevertheless, integrating smart materials into existing manufacturing processes can be complex and may require additional research and development to optimize performance.
Overall, the future of 3D printing in production parts will depend heavily on the ongoing innovation in materials technology, balancing performance with sustainability.
Applications of 3D Printed Production Parts
The significance of 3D printed production parts spans across various industries, offering innovative solutions to traditional manufacturing challenges. The ability to create complex geometries with relative ease and customize components for specific applications highlights the advantages of additive manufacturing. This section explores how different sectors utilize 3D printing, emphasizing its role in pushing boundaries of design, enhancing efficiency, and reducing time to market.
Aerospace Industry
The aerospace industry is among the early adopters of 3D printing technologies. This field requires high precision and durability in components. With the demand for lightweight and strong materials, 3D printing emerges as a suitable solution. For example, components for engines and airframes can be produced with complex internal structures that reduce weight without sacrificing strength.
Notably, companies like Boeing and Airbus are investing significantly in additive manufacturing. They aim to streamline production processes while ensuring safety and performance standards are met. 3D printing allows for rapid prototyping and testing, enabling engineers to iterate designs faster compared to conventional methods.
Automotive Sector
The automotive sector has also experienced a transformation due to 3D printed production parts. The technology allows for quick tailoring of designs to meet specific vehicle requirements. This customization ranges from exterior parts to intricate components within the engine. With the introduction of lightweight materials, manufacturers can improve fuel efficiency and overall vehicle performance.
Automakers such as Ford and General Motors are using 3D printing for rapid prototyping in the design phase. The ease of modifying designs based on performance feedback presents a significant advantage over traditional production techniques. Additionally, spare parts can be printed on demand, reducing inventory costs and minimizing downtime.
Healthcare Innovations
Prosthetics and Implants
Prosthetics and implants represent a key area where 3D printing significantly enhances patient outcomes. With the ability to create custom-fitted prosthetics, patients experience improved comfort and mobility. These devices can accommodate individual anatomical differences, contributing to greater ease of use.
One hallmark of 3D printed prosthetics is their relatively low cost when compared to traditional prosthetic devices. Moreover, materials used in 3D printing, like thermoplastics and biocompatible materials, are advantageous for patients. They offer customization that caters to specific medical needs, leading to uniformly satisfactory results.
Bioprinting Applications
Bioprinting has emerged as a groundbreaking development in healthcare, focusing on the production of organic tissues and organs. The unique characteristic of bioprinting is its ability to layer living cells, creating structures that mimic natural tissues. This innovation promises to alleviate organ shortages and is gaining traction in tissue engineering.
While the prospects are promising, bioprinting faces notable challenges, such as scalability and regulatory hurdles. However, its potential to revolutionize transplants and regenerative medicine makes it an important topic in discussions surrounding 3D printed production parts.
"3D printing in healthcare not only seeks to produce parts but aims to change lives through individualized medical solutions."
In summary, the applications of 3D printed production parts in aerospace, automotive, and healthcare are profound. They highlight the flexibility and potential of additive manufacturing across diverse fields. As technologies evolve and methodologies improve, the trajectory of 3D printing is likely to expand, revealing new opportunities in production and design.
Benefits of 3D Printed Production Parts
The benefits of 3D printed production parts are significant, particularly as industries strive for greater efficiency and responsiveness to market needs. 3D printing offers advantages that traditional manufacturing methods often struggle to match. Among these are cost efficiency and customization, both of which play crucial roles in enhancing production capabilities. Each benefit serves a unique purpose, aligning with various industry requirements, thus reinforcing the viability of 3D printing in production.
Cost Efficiency
Cost efficiency is a primary advantage of using 3D printing for production parts. Traditional manufacturing processes often involve high setup costs, especially for low-volume production runs. In contrast, 3D printing allows for the direct production of parts from digital models, eliminating the need for expensive molds and tooling. This not only reduces initial costs but also minimizes waste.
Moreover, the ability to produce parts on-demand leads to lower inventory costs. Companies can manufacture parts only as needed, effectively reducing the need to warehouse excess products. This strategy is particularly beneficial in industries where parts may have long lead times, thus allowing businesses to respond to customer demands more rapidly.
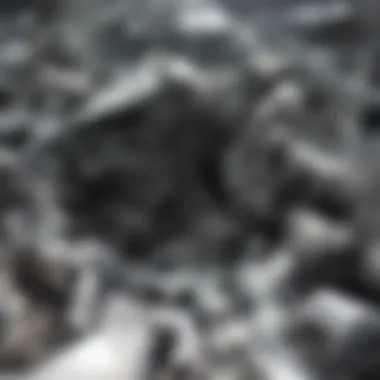
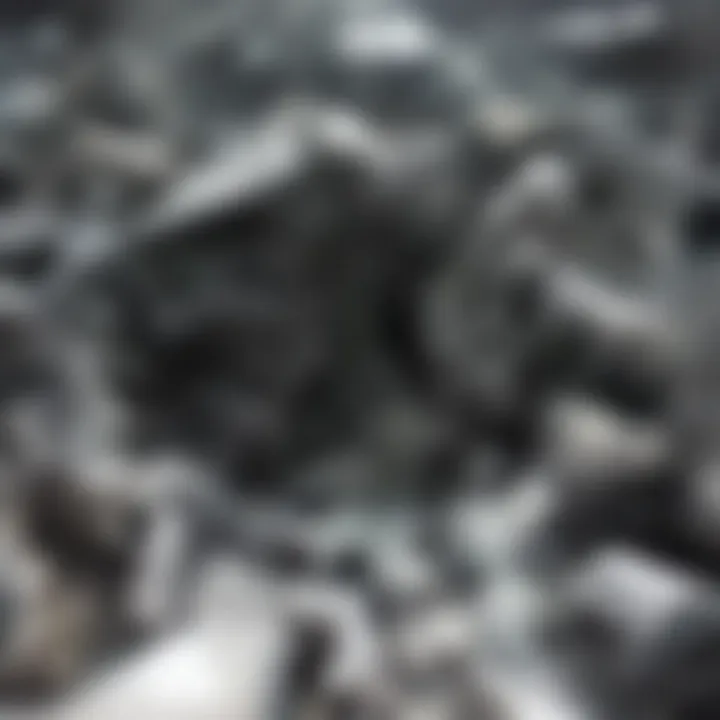
"By eliminating the need for extensive tooling, 3D printing can fundamentally change the economic landscape of manufacturing."
In addition, advancements in printing technologies and materials continue to make production processes more efficient. As a result, the total cost per part can decrease as businesses scale their operations. Investment in 3D printers can yield significant returns, especially when considering the potential for rapid prototyping, where companies can test and iterate designs swiftly without incurring heavy expenses.
Customization and Design Flexibility
Customization and design flexibility are critical features of 3D printing that have opened new avenues for product development. Companies can create production parts tailored to specific requirements, enhancing product performance and user satisfaction. This contrasts sharply with traditional methods, where modifying designs often demands expensive retooling.
With 3D printing, designs can be adjusted at a moment's notice based on customer feedback or changing market trends. This speed of innovation allows businesses to stay ahead of their competitors. For instance, in the automotive sector, manufacturers utilize 3D printing to produce customized parts that cater to individual client needs, optimizing vehicles for specific applications.
Additionally, the design possibilities with 3D printing allow for complex geometries that traditional methods cannot achieve. Designers can introduce lightweight structures and intricate features that improve functionality. This flexibility is especially important in sectors such as aerospace, where weight savings can translate directly to better fuel efficiency.
In summary, the benefits of 3D printed production parts are substantial. Cost efficiency reduces financial burdens, while customization enhances relevance to market demands. As these technologies continue to advance, their implications for manufacturing will only grow more profound.
Challenges in Adopting 3D Printing for Production Parts
Adopting 3D printing for production parts presents various challenges that must be carefully considered. While the technology offers significant potential advantages, there are several hurdles that can impede its widespread acceptance in manufacturing. Understanding these challenges is crucial for industries looking to integrate 3D printing into their processes. Assessing the constraints can help in recognizing potential solutions that maximize the benefits of this technology.
Material Limitations
Material selection is one of the most prominent challenges in 3D printing. Not all materials are suitable for every application. Current 3D printing technologies mainly utilize polymers, metals, and composites. However, the range of functional materials is still limited. This can affect the performance and durability of the parts produced. For instance, certain high-strength applications like aerospace components may require materials that are not easily achievable with current 3D printing processes.
Another concern is the mechanical properties of 3D printed materials. Parts often struggle to meet the same specifications as those produced by traditional manufacturing. Factors such as layer adhesion, porosity, and surface finish can significantly impact the final product. Developing newer materials and enhancing existing ones will be essential to overcome these limitations and enable more reliable production.
Regulatory and Certification Issues
Regulatory compliance poses another significant challenge. Many industries, such as healthcare and aerospace, are heavily regulated. They require rigorous testing and certification processes for any components used in their applications. The current landscape for 3D printed parts lacks standardized guidelines, making it difficult for businesses to obtain necessary certifications. Each part may require individual assessment, which can be time-consuming and costly.
Establishing universally recognized standards and certification methods is necessary for enhancing trust among industries that wish to use 3D printed components. Without a robust regulatory framework, the shift to 3D printing will likely face resistance due to fears about safety and reliability.
Production Speed and Scale
Production speed is a critical factor for any manufacturing operation. Although 3D printing can produce complex geometries more easily than traditional methods, scaling production remains a major issue. Additive manufacturing technologies can be slower than subtractive methods when it comes to high-volume production. As such, industries that rely on quick turnaround times might hesitate to switch to 3D printing.
Moreover, the setup times, post-processing requirements, and equipment investment can create bottlenecks in the production workflow. The up-front costs associated with 3D printing machinery can also be a barrier for smaller manufacturers. To fully exploit the advantages of 3D printing, advancements in production speed and scalability need to be made.
"3D printing offers incredible promise, but realizing its full potential in production parts requires addressing these key challenges."
Future Trends in 3D Printing
The domain of 3D printing is rapidly evolving. Understanding the future trends in this technology provides valuable insights into where the industry is heading. As companies seek innovative solutions, the importance of advancements in additive manufacturing cannot be overstated. Emerging trends not only improve efficiency but also enhance sustainability. This section explores key elements and benefits of future developments in 3D printing.
Technological Innovations
Technological innovations are at the forefront of 3D printing advancements. With emerging technologies, 3D printing is becoming faster and more precise. Here are some specific innovations that are shaping the landscape:
- Multi-material printing allows for the creation of complex components with varying properties in a single print. This is particularly useful in sectors like aerospace, where different material properties are essential for performance.
- Large-scale 3D printing has begun to revolutionize construction. Structures once built using traditional methods can now be printed, significantly reducing time and labor costs.
- 4D printing, which incorporates the dimension of time into 3D printing, is gaining attention. This technology can produce objects that change their shape or function in response to external stimuli, opening new possibilities for robotics and medical devices.
These innovations enhance production capabilities. They allow companies to manufacture parts that were previously too complex or costly to produce.
Sustainable Manufacturing Practices
Sustainable practices are becoming critical in the manufacturing landscape. 3D printing presents several opportunities for greener production methods. Here are important aspects to consider:
- Reduced material waste: Traditional manufacturing often results in significant waste, particularly in subtractive processes. 3D printing, being an additive process, builds parts layer by layer, which minimizes excess material usage.
- Energy efficiency: Advances in print technology often lead to lower energy consumption. More efficient machines will ensure that 3D printing can play a pivotal role in reducing the carbon footprint of manufacturing.
- Recyclable and bio-based materials are becoming more available. Utilizing these materials not only reduces reliance on virgin resources but also promotes circular economy principles.
"The intersection of sustainability and technology in 3D printing could redefine modern manufacturing on an environmental level."
Epilogue
The conclusion of this article serves as a pivotal section, bringing together the numerous strands of knowledge presented throughout the text. It highlights the significance of 3D printed production parts, emphasizing their transformative role in modern manufacturing. The advancements in this technology have consistently challenged traditional methods, introducing new levels of efficiency, customization, and design innovation. Understanding the implications of these advancements is crucial not only for industry stakeholders but also for academics and students looking to explore the future of manufacturing.
Recap of Key Points
In the preceding sections, several key points have been discussed that encapsulate the essence of 3D printed production parts:
- Technological Innovations: The evolution of 3D printing techniques such as Fused Deposition Modeling, Stereolithography, and Selective Laser Sintering has pushed boundaries in production efficiency and part design.
- Material Diversity: The availability of various materials, including plastics, metals, and emerging options like biosourced materials, indicates a shift towards meeting the nuanced demands of different industries.
- Applications Across Industries: From the aerospace sector's need for lightweight yet sturdy components to the automotive industry's quest for rapid prototyping, 3D printing applications showcase its versatility.
- Challenges Identified: Despite its benefits, challenges such as material limitations, regulatory hurdles, and production speed still hinder the widespread adoption of 3D printing technologies.
These points remind us of the dynamic nature of 3D printing and its potential to reshape production methodologies across sectors.
Looking Ahead at the Industry
Looking towards the future, the landscape of 3D printing in production parts is poised for expansive growth. Key trends suggest a movement toward:
- Continued Technological Advancements: Innovations in software and printing techniques will likely enhance the quality and scope of 3D printed parts.
- Integration of Sustainable Practices: As industries increasingly prioritize sustainability, the development of eco-friendly materials and processes will become more significant.
- Increased Collaboration: Cross-industry partnerships may emerge, promoting knowledge sharing and the acceleration of advancements in 3D printed technologies.
In summary, the future of 3D printed production parts is promising and demands attention from all interested in the evolution of manufacturing. Understanding these trends will prepare students, educators, researchers, and professionals to navigate and exploit this rapidly changing landscape.